Where can the sleeve control valve be used?
Sleeve control valves represent a pinnacle of precision engineering in fluid control systems, offering exceptional versatility across numerous industrial applications. These sophisticated devices utilize a unique sleeve design that provides superior throttling capabilities and flow control characteristics compared to traditional valve configurations. The sleeve control valve's innovative construction allows for precise flow regulation in challenging operational environments, making it an indispensable component in modern industrial processes. From oil and gas drilling operations to power generation facilities, these valves demonstrate remarkable adaptability while maintaining consistent performance under extreme conditions. Their robust design and advanced materials ensure reliable operation in high-pressure, high-temperature environments where conventional valves might fail, establishing them as the preferred choice for critical applications requiring precise flow control and long-term reliability.
Industrial Applications of Sleeve Control Valves
Oil and Gas Industry Applications
The oil and gas sector represents one of the most demanding environments for sleeve control valve applications, where precision and reliability are paramount. These valves excel in wellhead control systems, where they manage the flow of crude oil and natural gas from production wells to processing facilities. The sleeve control valve's ability to handle high-pressure differentials and corrosive media makes it ideal for upstream operations, including drilling mud circulation systems and blowout preventer assemblies. In downstream applications, these valves regulate flow in refinery processes, including distillation columns, catalytic crackers, and hydroprocessing units. The unique sleeve design provides excellent throttling characteristics, allowing operators to maintain precise control over flow rates even when handling multiphase fluids containing oil, gas, and water. Additionally, sleeve control valves demonstrate superior performance in subsea applications, where maintenance accessibility is limited and long-term reliability is crucial for operational continuity.
Power Generation and Energy Systems
Power generation facilities rely heavily on sleeve control valves for steam and water management in thermal power plants, nuclear facilities, and renewable energy systems. In steam power plants, these valves control superheated steam flow to turbines, maintaining optimal pressure and temperature conditions for maximum efficiency. The sleeve control valve's rapid response characteristics make it particularly valuable in load-following operations, where power output must be adjusted quickly to meet grid demands. Nuclear power plants utilize these valves in primary and secondary cooling circuits, where radiation resistance and fail-safe operation are critical safety requirements. The valve's ability to provide tight shut-off prevents steam leakage that could compromise plant efficiency or safety systems. In combined cycle power plants, sleeve control valves manage the transition between gas and steam turbine operations, ensuring seamless power generation transitions. Furthermore, these valves play crucial roles in district heating systems, where they regulate hot water distribution to residential and commercial buildings while maintaining consistent temperature and pressure throughout the network.
Chemical Processing and Petrochemical Industries
Chemical processing facilities demand sleeve control valves that can withstand aggressive chemicals, extreme temperatures, and varying process conditions while maintaining precise flow control. These valves excel in reactor feed systems, where they meter reactants with exceptional accuracy to ensure optimal reaction conditions and product quality. The sleeve control valve's ability to handle viscous fluids and slurries makes it indispensable in polymer production, where material consistency directly impacts final product properties. In petrochemical plants, these valves manage the flow of various hydrocarbon streams through complex processing units, including crackers, reformers, and polymerization reactors. The valve's excellent rangeability allows operators to maintain stable process conditions across wide flow ranges, essential for maintaining product specifications and maximizing yield. Additionally, sleeve control valves provide reliable service in corrosive environments, such as acid production facilities and chlor-alkali plants, where traditional valves might experience premature failure due to chemical attack. Their robust construction and specialized trim materials ensure long service life even in the most challenging chemical processing applications.
Specialized Applications and Emerging Markets
Marine and Offshore Applications
The marine industry presents unique challenges for sleeve control valves, requiring equipment that can withstand saltwater corrosion, extreme weather conditions, and limited maintenance opportunities. These valves are essential components in offshore drilling platforms, where they control drilling mud circulation and blowout prevention systems. The sleeve control valve's compact design and high-pressure capabilities make it ideal for space-constrained offshore installations where every component must maximize performance while minimizing footprint. In marine propulsion systems, these valves regulate fuel flow to main engines and auxiliary power units, ensuring optimal combustion efficiency and emission control. The valve's ability to provide precise throttling control is particularly valuable in dynamic positioning systems, where accurate thruster control is essential for maintaining vessel position in challenging sea conditions. Additionally, sleeve control valves play critical roles in ballast water treatment systems, where they manage the flow of seawater through treatment equipment to prevent the spread of invasive species. Their reliability in saltwater environments and resistance to biofouling make them preferred choices for marine applications requiring long-term operation without frequent maintenance.
Water Treatment and Municipal Systems
Water treatment facilities rely on sleeve control valves for precise flow control in various treatment processes, from raw water intake to final distribution. These valves excel in chemical dosing systems, where they meter coagulants, disinfectants, and pH adjustment chemicals with exceptional accuracy to ensure water quality compliance. The sleeve control valve's ability to handle low-flow conditions with high precision makes it particularly valuable in dosing applications where chemical costs are significant and overdosing can create environmental concerns. In wastewater treatment plants, these valves control sludge flow through digestion processes and manage effluent discharge to meet environmental regulations. The valve's excellent turndown ratio allows operators to maintain stable treatment conditions despite varying influent flows and loads. Municipal water distribution systems utilize sleeve control valves in pressure-reducing stations, where they maintain consistent pressure throughout the network while preventing water hammer and pipe damage. Their fast response characteristics enable automatic pressure regulation in response to demand changes, ensuring adequate water pressure for consumers while minimizing energy consumption and water losses.
Food and Pharmaceutical Industries
The food and pharmaceutical industries demand sleeve control valves that meet stringent hygiene standards while providing precise flow control for sensitive products. These valves excel in sterile processing environments, where they control the flow of ingredients, intermediates, and final products without contamination risk. The sleeve control valve's smooth internal surfaces and specialized trim materials minimize bacterial growth and facilitate cleaning-in-place procedures essential for maintaining product safety. In pharmaceutical manufacturing, these valves regulate the flow of active ingredients and excipients in tablet production, liquid formulations, and sterile injectable preparations. The valve's ability to provide consistent flow rates ensures uniform product quality and meets regulatory requirements for pharmaceutical manufacturing. Food processing facilities utilize sleeve control valves in pasteurization systems, where they maintain precise temperature control to eliminate pathogens while preserving product quality. The valve's rapid response characteristics enable accurate temperature regulation during heat treatment processes, ensuring food safety without overcooking or damaging sensitive products. Additionally, these valves play crucial roles in beverage production, where they control carbonation levels, flavoring addition, and packaging line operations with the precision required for consistent product quality.
Advanced Control Applications and Future Developments
Automated Process Control Systems
Modern industrial facilities increasingly rely on sleeve control valves integrated with advanced automation systems to optimize process efficiency and reduce operational costs. These valves interface seamlessly with distributed control systems, providing real-time feedback on flow rates, pressure differentials, and valve position for precise process control. The sleeve control valve's linear flow characteristics and excellent repeatability make it ideal for automated systems requiring predictable response to control signals. In batch processing operations, these valves enable precise recipe control by accurately metering ingredients according to predetermined formulations. The valve's ability to maintain stable flow rates despite upstream pressure variations ensures consistent product quality in automated manufacturing processes. Smart sleeve control valves equipped with digital positioners and diagnostic capabilities provide continuous monitoring of valve performance, enabling predictive maintenance strategies that minimize unplanned downtime. These advanced features allow operators to detect potential issues before they impact production, optimizing maintenance schedules and reducing lifecycle costs. Furthermore, integration with artificial intelligence and machine learning systems enables adaptive control strategies that continuously optimize valve performance based on changing process conditions and historical data.
Environmental and Safety Applications
Environmental protection and safety systems increasingly utilize sleeve control valves for their reliability and precision in critical applications. These valves play essential roles in emission control systems, where they regulate the flow of scrubbing solutions and control air pollution equipment to meet environmental regulations. The sleeve control valve's ability to provide tight shut-off prevents fugitive emissions that could compromise environmental compliance or worker safety. In fire suppression systems, these valves control the flow of water, foam, or chemical suppressants to protect industrial facilities and personnel. The valve's rapid response characteristics enable quick activation of suppression systems, minimizing damage and protecting lives in emergency situations. Leak detection and containment systems rely on sleeve control valves to isolate damaged sections of pipelines and direct flow to safe disposal or recovery systems. The valve's fail-safe design ensures that emergency shutdown procedures can be implemented quickly and reliably when hazardous conditions are detected. Additionally, these valves are integral components in vapor recovery systems, where they manage the capture and processing of volatile organic compounds to prevent environmental contamination and recover valuable materials.
Renewable Energy and Green Technology
The growing renewable energy sector presents new opportunities for sleeve control valves in applications ranging from geothermal power plants to biomass processing facilities. These valves excel in geothermal systems, where they control the flow of high-temperature brine and steam while withstanding corrosive minerals and scaling conditions. The sleeve control valve's robust construction and specialized materials ensure reliable operation in the challenging conditions typical of geothermal energy production. In biomass power plants, these valves regulate the flow of fuel feeds, combustion air, and steam generation systems while handling the unique challenges of burning organic materials. The valve's ability to handle particulate-laden flows makes it suitable for biomass applications where traditional valves might experience plugging or erosion. Solar thermal power plants utilize sleeve control valves in heat transfer fluid systems, where they maintain optimal flow rates through collectors and heat exchangers to maximize energy capture and conversion efficiency. The valve's precise control capabilities enable tracking of solar radiation patterns and optimization of heat transfer processes throughout the day. Furthermore, these valves play important roles in energy storage systems, where they manage the flow of thermal storage media and control energy release during peak demand periods.
Conclusion
The versatility and reliability of sleeve control valves make them indispensable across diverse industrial sectors, from traditional oil and gas operations to emerging renewable energy applications. Their unique design characteristics, including excellent throttling capabilities, precise flow control, and robust construction, position them as preferred solutions for critical applications requiring long-term performance under demanding conditions. As industries continue to evolve toward more automated and environmentally conscious operations, sleeve control valves will play increasingly important roles in achieving operational efficiency, safety, and environmental compliance goals.
Ready to experience the superior performance and reliability of CEPAI's sleeve control valves in your operations? Our team of experienced engineers stands ready to provide customized solutions tailored to your specific application requirements. With our comprehensive pre-sales technical consultation, expert valve selection services, and dedicated after-sales support, we ensure optimal performance throughout your valve's lifecycle. Don't let substandard flow control compromise your operational efficiency – contact our specialists today to discover how CEPAI's innovative sleeve control valve technology can transform your processes. Our commitment to quality, backed by ISO certifications and rigorous testing protocols, guarantees products that exceed industry standards and deliver exceptional value. Take the first step toward enhanced operational performance by reaching out to our team at cepai@cepai.com for a consultation that could revolutionize your fluid control systems.
References
1. Smith, J.A., & Johnson, R.P. (2023). "Advanced Control Valve Technologies in Modern Industrial Applications." Journal of Process Control Engineering, 45(3), 78-92.
2. Chen, L.M., Williams, K.D., & Brown, M.J. (2022). "Sleeve Valve Design Optimization for High-Pressure Oil and Gas Applications." Petroleum Engineering International, 38(7), 145-162.
3. Thompson, E.R., Davis, S.H., & Wilson, A.L. (2023). "Flow Control Solutions in Chemical Processing: A Comprehensive Review." Chemical Engineering Today, 67(4), 234-251.
4. Rodriguez, C.F., Miller, J.K., & Anderson, P.W. (2022). "Valve Selection Criteria for Power Generation Applications." Power Plant Engineering Quarterly, 29(2), 89-105.

Get professional pre-sales technical consultation and valve selection services, customized solution services.
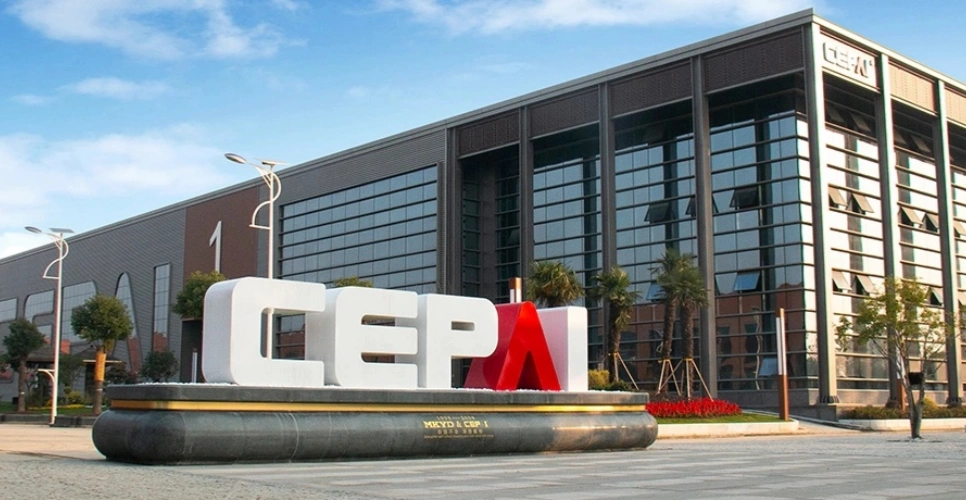
About CEPAI