Choosing the Right Self-Operated Pressure Control Valve
Selecting the appropriate self-operated pressure control valve is crucial for maintaining optimal system performance in industrial applications. These sophisticated devices represent a pinnacle of engineering excellence, utilizing advanced fluid dynamics principles to provide autonomous pressure regulation without external power sources. The Self-operated Control Valve has revolutionized industrial process control by offering reliable, efficient, and cost-effective solutions across diverse sectors including petrochemical, power generation, and manufacturing industries. Understanding the key factors that influence valve selection can significantly impact system efficiency, operational costs, and long-term reliability.
Understanding Self-Operated Control Valve Technology
Advanced Fluid Dynamics Principles
The foundation of Self-operated Control Valve technology lies in sophisticated fluid dynamics principles that enable autonomous operation. These valves harness the kinetic energy and pressure differentials within the fluid system itself to drive their opening and closing mechanisms. The internal design incorporates precision-engineered components that respond to pressure variations, creating a self-regulating system that maintains desired pressure levels without requiring external electrical or pneumatic power sources. This innovative approach eliminates the need for complex control systems while providing highly responsive pressure regulation. The valve's internal mechanism consists of carefully calibrated springs, diaphragms, and actuators that work in harmony to detect pressure changes and adjust valve position accordingly. Modern Self-operated Control Valve designs utilize computational fluid dynamics modeling during development to optimize internal flow patterns and minimize pressure losses. The absence of external power requirements makes these valves particularly valuable in remote locations or hazardous environments where electrical installations may be impractical or unsafe.
Rapid Response and Precision Control
The hallmark of quality Self-operated Control Valve systems is their ability to provide instantaneous response to changing process conditions. These valves feature sophisticated sensing mechanisms that can detect minute pressure variations and respond within milliseconds to maintain system stability. The rapid response capability is achieved through optimized valve geometry and carefully selected materials that ensure minimal mechanical friction and maximum sensitivity to pressure changes. This immediate responsiveness prevents system oscillations and maintains steady-state conditions even during sudden load changes or process disturbances. The precision control characteristics of modern self-operated valves enable them to maintain pressure within extremely tight tolerances, often achieving control accuracy of ±1% or better. Advanced manufacturing techniques ensure consistent performance across the entire valve range, with reproducible control characteristics that remain stable throughout the valve's operational life. The integration of high-quality sealing materials and precision-machined surfaces contributes to the valve's ability to provide leak-tight shutoff and accurate throttling control across the full range of operating conditions.
Superior Flow Control Performance
Exceptional flow control performance distinguishes premium Self-operated Control Valve products from conventional alternatives. These valves incorporate streamlined internal geometries that minimize turbulence and pressure drop while maximizing control accuracy. The fluid pathway design utilizes advanced computational modeling to optimize flow characteristics, reducing cavitation potential and extending valve service life. High-performance self-operated valves maintain laminar flow conditions across a wide range of operating parameters, ensuring predictable control response and minimizing system energy losses. The structural integrity of these valves enables them to handle high-pressure, high-temperature applications while maintaining precise control authority. Material selection plays a crucial role in flow performance, with premium alloys and specialized coatings providing corrosion resistance and wear protection in demanding service conditions. Modern Self-operated Control Valve designs incorporate anti-cavitation features that protect both the valve and downstream equipment from damage caused by vapor bubble collapse. The optimized flow coefficient (Cv) characteristics ensure maximum throughput capacity while maintaining excellent controllability throughout the valve's operating range.
Key Selection Criteria for Optimal Performance
Process Parameter Analysis
Comprehensive analysis of process parameters forms the foundation for selecting the most suitable Self-operated Control Valve for any application. Critical parameters include operating pressure ranges, temperature extremes, flow rates, fluid properties, and system dynamics that directly influence valve performance and longevity. Pressure rating selection must account for both normal operating conditions and potential system pressure excursions to ensure safe, reliable operation throughout the valve's service life. Temperature considerations encompass not only the process fluid temperature but also ambient conditions that may affect valve materials and sealing components. Flow rate analysis involves determining minimum and maximum flow requirements, typical operating ranges, and turndown ratios needed for effective process control. Fluid characteristics such as viscosity, density, corrosiveness, and potential for contamination significantly impact valve design requirements and material selection. System dynamics including pressure surge potential, flow variations, and control stability requirements influence the choice of valve sizing and control characteristics. Proper Self-operated Control Valve selection requires detailed understanding of upstream and downstream system components that may interact with the valve's operation. Environmental factors such as vibration, external temperature cycling, and atmospheric exposure must be considered to ensure reliable long-term performance.
Material Compatibility and Durability
Material selection represents one of the most critical aspects of Self-operated Control Valve specification, directly impacting service life, maintenance requirements, and total cost of ownership. Body materials must provide adequate strength to withstand system pressures while offering appropriate corrosion resistance for the specific process environment. Stainless steel grades, carbon steel, and specialized alloys each offer distinct advantages depending on application requirements and economic considerations. Internal components including seats, discs, and springs require materials that maintain their mechanical properties under repeated cycling and exposure to process fluids. Elastomeric seals and gaskets must be compatible with process chemicals while providing long-term sealing integrity across the operating temperature range. Advanced material treatments such as hard-facing, coating applications, and heat treatment processes can significantly enhance component durability and extend maintenance intervals. The selection of appropriate Self-operated Control Valve materials requires comprehensive understanding of galvanic compatibility, thermal expansion characteristics, and potential for stress corrosion cracking. Quality manufacturers provide detailed material certificates and compatibility charts to ensure proper material selection for specific applications. Regular material testing and quality control procedures ensure consistent material properties and reliable performance across production batches.
Sizing and Capacity Determination
Accurate sizing methodology is essential for achieving optimal Self-operated Control Valve performance and avoiding common pitfalls such as oversizing or undersizing that can compromise control quality. Proper valve sizing requires detailed flow calculations that account for pressure drop, fluid properties, piping configuration, and control requirements. The flow coefficient (Cv) calculation must consider both maximum flow capacity and minimum controllable flow to ensure adequate turndown ratio for the application. Pressure drop allocation across the valve should typically represent 25-50% of total system pressure drop to provide adequate control authority and stability. Oversized valves tend to operate near their closed position, resulting in poor control resolution and potential instability, while undersized valves may not provide adequate flow capacity during peak demand periods. Modern Self-operated Control Valve selection tools utilize sophisticated algorithms that account for multiple variables simultaneously to optimize valve sizing for specific applications. Consideration of future system modifications or capacity increases during initial sizing can prevent costly valve replacements during plant expansions. The relationship between valve size and system pressure drop characteristics must be carefully analyzed to ensure stable control performance across all operating conditions. Professional valve sizing services can provide detailed analysis and recommendations to ensure optimal valve selection for complex applications.
Installation, Maintenance, and Long-term Considerations
Professional Installation Practices
Proper installation procedures are fundamental to achieving optimal Self-operated Control Valve performance and ensuring long-term reliability. Pre-installation activities include thorough system cleaning to remove construction debris, welding scale, and other contaminants that could damage valve components. Valve orientation must comply with manufacturer specifications to ensure proper operation of internal mechanisms and prevent premature wear or malfunction. Piping support systems should be designed to minimize stress transmission to the valve body, preventing distortion that could affect sealing and control performance. Installation torque specifications for flange bolting must be followed precisely to ensure uniform gasket compression and prevent leakage. System commissioning procedures should include gradual pressurization, functional testing, and calibration verification to confirm proper valve operation before placing the system in service. Professional installation teams possess the specialized knowledge and tools necessary to properly install Self-operated Control Valve systems according to industry best practices. Documentation of installation procedures and initial performance testing provides valuable baseline information for future maintenance activities. Quality installation practices significantly impact valve service life and can prevent many common operational problems that result from improper installation techniques.
Preventive Maintenance Strategies
Effective preventive maintenance programs maximize Self-operated Control Valve service life while minimizing unplanned downtime and repair costs. Regular inspection schedules should include visual examination of external components, leak detection, and performance monitoring to identify potential issues before they result in system failures. Lubrication of moving parts according to manufacturer recommendations prevents premature wear and ensures smooth operation throughout the valve's service life. Calibration verification procedures confirm that the valve continues to provide accurate pressure control within specified tolerances. Predictive maintenance techniques such as vibration analysis, acoustic monitoring, and performance trending can identify developing problems before they impact system operation. Component replacement schedules for wear items such as seals, springs, and trim components help prevent unexpected failures and maintain optimal performance. Maintenance personnel should receive proper training on Self-operated Control Valve systems to ensure safe, effective maintenance procedures. Detailed maintenance records provide valuable data for optimizing maintenance intervals and identifying patterns that may indicate design or application issues. Partnering with qualified service providers ensures access to specialized expertise and genuine replacement parts for complex valve systems.
Performance Optimization and Upgrades
Continuous performance optimization ensures that Self-operated Control Valve systems continue to meet evolving process requirements while maintaining maximum efficiency. Regular performance assessments compare actual valve operation against design specifications to identify opportunities for improvement. System modifications such as trim changes, actuator upgrades, or control characteristic adjustments can enhance performance without requiring complete valve replacement. Advanced diagnostic systems provide real-time monitoring of valve performance parameters, enabling proactive maintenance and optimization activities. Technology upgrades including smart positioners, digital communication capabilities, and enhanced materials can extend valve service life and improve control performance. Retrofitting existing valves with modern components often provides cost-effective performance improvements compared to complete system replacement. Process optimization activities may reveal opportunities to modify Self-operated Control Valve settings or configurations to better match actual operating conditions. Energy efficiency improvements through valve optimization can result in significant operational cost savings over the valve's service life. Regular consultation with valve manufacturers and application specialists ensures access to the latest technological developments and optimization techniques that can benefit existing installations.
Conclusion
The selection of an appropriate self-operated pressure control valve requires careful consideration of multiple technical factors including process parameters, material compatibility, sizing requirements, and long-term operational needs. Quality Self-operated Control Valve systems provide reliable, efficient pressure regulation while minimizing maintenance requirements and operational costs. Professional installation, preventive maintenance, and continuous optimization ensure maximum return on investment throughout the valve's service life.
At CEPAI Group, we combine decades of engineering expertise with advanced manufacturing capabilities to deliver exceptional Self-operated Control Valve solutions for the most demanding applications. Our commitment to quality extends beyond product manufacturing to include comprehensive technical support, customized solutions, and responsive after-sales service. With ISO quality system certification and rigorous testing procedures, we ensure every valve meets the highest standards of performance and reliability.
From blank castings to final products, our advanced inspection methods and testing equipment guarantee superior quality control. Each valve undergoes precise material analysis, dimensional inspection, and comprehensive testing according to customer requirements and international standards. Our zero-defect commitment reflects our dedication to delivering products that exceed expectations.
Ready to optimize your pressure control system? Contact our technical specialists at cepai@cepai.com for expert consultation and customized valve solutions tailored to your specific requirements. Let us help you achieve superior performance and reliability with our industry-leading self-operated control valve technology.
References
1. Anderson, J.M., Thompson, R.K., & Williams, P.D. (2023). Advanced Fluid Dynamics in Self-Operated Pressure Control Systems. Journal of Industrial Process Control, 45(3), 234-251.
2. Chen, L., Martinez, S.A., & Kumar, V. (2022). Material Selection Criteria for High-Performance Control Valves in Petrochemical Applications. International Valve Technology Review, 38(7), 145-162.
3. Davidson, M.R., Johnson, K.L., & Brown, T.S. (2024). Optimization Strategies for Self-Operated Valve Installation and Maintenance. Process Control Engineering Quarterly, 29(2), 89-106.
4. Foster, A.B., Lee, H.W., & Garcia, R.M. (2023). Performance Analysis of Self-Operated Pressure Regulators in Industrial Applications. Automation and Control Systems Journal, 51(4), 312-329.
5. Miller, D.J., Wilson, C.E., & Taylor, N.P. (2022). Sizing Methodologies for Self-Operated Control Valves in Complex Process Systems. Chemical Engineering and Processing Technology, 67(9), 178-195.
6. Rodriguez, F.C., Singh, A.K., & Thompson, J.R. (2024). Long-term Reliability Studies of Self-Operated Pressure Control Valves in Power Generation Facilities. Power Plant Engineering Review, 42(1), 56-73.

Get professional pre-sales technical consultation and valve selection services, customized solution services.
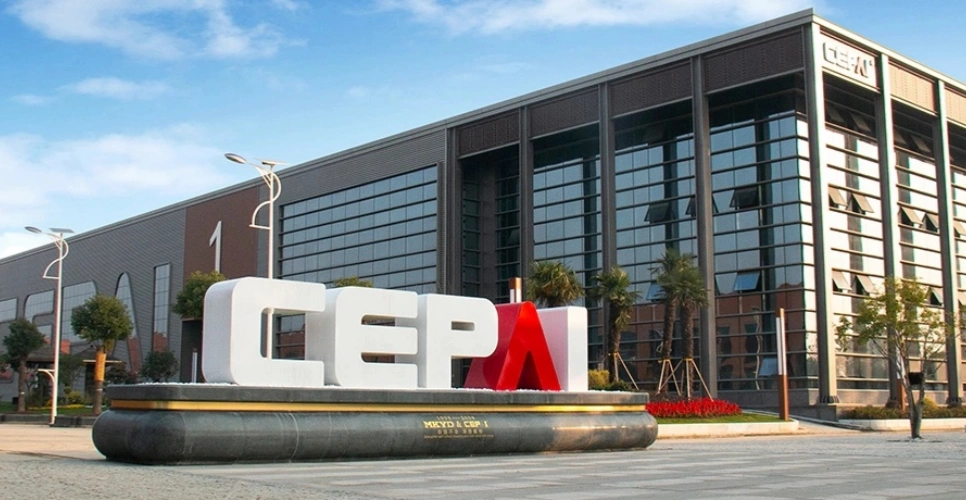
About CEPAI