Choosing Between Electric and Pneumatic Control Valves for Industrial Applications
Selecting the appropriate control valve actuator type is a critical decision that significantly impacts industrial system performance, operational efficiency, and long-term maintenance costs. The choice between electric and pneumatic control valves requires careful consideration of multiple factors including response time, precision requirements, environmental conditions, and total cost of ownership. Electric Control Valve systems offer distinct advantages in applications requiring precise positioning, remote monitoring capabilities, and reduced maintenance requirements, while pneumatic systems excel in high-speed applications and hazardous environments where electrical components may pose safety risks.
Key Performance Characteristics of Electric vs. Pneumatic Control Valves
Precision and Control Accuracy
Electric Control Valve systems demonstrate superior precision capabilities compared to their pneumatic counterparts, making them ideal for applications requiring exact positioning and stable control. The inherent characteristics of electric actuators allow for precise positioning with minimal hysteresis, typically achieving positioning accuracy within ±0.1% of full scale. This precision stems from the direct mechanical coupling between the motor and valve stem, eliminating the compressibility issues associated with compressed air systems. Electric actuators utilize advanced control algorithms and feedback systems that continuously monitor and adjust valve position, ensuring consistent performance even under varying load conditions.The digital nature of electric control systems enables sophisticated control strategies including PID control, adaptive control, and predictive maintenance algorithms. These systems can maintain valve position with remarkable stability, reducing process variability and improving product quality. Furthermore, electric actuators can be programmed with custom control curves and fail-safe positions, providing flexibility that traditional pneumatic systems cannot match. The absence of air leakage issues ensures that electric systems maintain their calibrated positions over extended periods without drift.
Response Time and Dynamic Performance
Response time characteristics differ significantly between electric and pneumatic systems, with each offering advantages in specific applications. Electric Control Valve systems typically exhibit slower response times compared to pneumatic actuators, with full stroke times ranging from 15 to 60 seconds depending on the actuator size and load requirements. However, this slower response can be advantageous in applications where gradual, controlled movements are preferred to prevent system shock or water hammer effects.Pneumatic actuators excel in high-speed applications requiring rapid valve operation, with typical response times of 1-5 seconds for full stroke operation. The instantaneous power delivery of compressed air enables these systems to overcome static friction and accelerate quickly, making them ideal for emergency shutdown applications and processes requiring rapid flow control adjustments. The force multiplication capabilities of pneumatic systems allow for the operation of large valves with relatively small control signals, providing excellent dynamic response characteristics.
Environmental Adaptability and Safety Considerations
Environmental conditions play a crucial role in actuator selection, with electric and pneumatic systems offering distinct advantages in different operating environments. Electric Control Valve systems demonstrate exceptional performance in clean, controlled environments where precise positioning and remote monitoring are essential. These systems are particularly well-suited for indoor applications, clean rooms, and environments where compressed air quality may be compromised by moisture or contaminants.Pneumatic actuators maintain inherent safety advantages in hazardous environments where explosive atmospheres or high-temperature conditions exist. The absence of electrical components in the actuator mechanism eliminates potential ignition sources, making pneumatic systems the preferred choice for oil and gas applications, chemical processing, and other hazardous environments. Additionally, pneumatic systems can operate effectively in extreme temperature conditions where electric motors might fail or require expensive temperature compensation equipment.
Cost Analysis and Economic Considerations
Initial Investment and Installation Costs
The initial cost comparison between electric and pneumatic control valve systems reveals significant differences in both equipment and installation expenses. Electric Control Valve systems typically require higher initial capital investment due to the sophisticated motor control electronics, position feedback devices, and power supply requirements. However, this higher upfront cost is often offset by reduced installation complexity, particularly in applications where compressed air systems are not readily available.Pneumatic systems generally offer lower initial equipment costs, but the total installation expense must include the cost of compressed air generation, distribution piping, air preparation equipment, and associated maintenance infrastructure. The requirement for dedicated air compressors, air dryers, filters, and regulators can significantly increase the total system cost, particularly for smaller installations where the compressed air infrastructure may be oversized relative to the valve control requirements.
Operating Costs and Energy Efficiency
Long-term operating costs represent a crucial factor in actuator selection, with electric systems typically demonstrating superior energy efficiency compared to pneumatic alternatives. Electric Control Valve systems consume power only during valve movement, with modern designs incorporating energy-efficient motors and regenerative braking systems that can actually return energy to the electrical grid during certain operating conditions. The standby power consumption of electric actuators is minimal, typically less than 5 watts for maintaining position feedback and control system operation.Pneumatic systems require continuous energy input to maintain compressed air pressure, with typical industrial air compressor efficiency rates of 10-15% when considering the complete energy conversion process. Air leakage throughout the distribution system further reduces efficiency, with typical industrial compressed air systems experiencing 10-30% losses due to leaks, improper sizing, and distribution inefficiencies. The cost of compressed air generation can range from $0.25 to $0.50 per 1,000 cubic feet, making pneumatic systems significantly more expensive to operate over their lifecycle.
Maintenance Requirements and Lifecycle Costs
Maintenance considerations significantly impact the total cost of ownership for control valve systems, with electric and pneumatic systems exhibiting different maintenance patterns and requirements. Electric Control Valve systems typically require minimal routine maintenance, with modern designs featuring sealed gear trains, maintenance-free motors, and self-diagnostic capabilities that can predict component failures before they occur. The absence of consumable components such as seals, O-rings, and air filters reduces routine maintenance requirements and associated downtime.Pneumatic systems require regular maintenance of air preparation equipment, including filter replacement, moisture removal, and lubrication system maintenance. The dynamic seals and O-rings in pneumatic actuators are subject to wear and require periodic replacement, particularly in applications involving frequent cycling or extreme temperature conditions. However, pneumatic systems offer the advantage of field-repairable components and standardized replacement parts that can be quickly serviced by plant maintenance personnel without specialized training.
Application-Specific Selection Criteria
Process Control Applications
Process control applications require careful consideration of control valve characteristics to ensure optimal system performance and product quality. Electric Control Valve systems excel in applications requiring precise flow control, temperature regulation, and level control where positioning accuracy directly impacts process outcomes. The linear relationship between control signal and valve position in electric systems provides predictable control characteristics that simplify process control loop tuning and optimization.Industries such as pharmaceutical manufacturing, food and beverage processing, and semiconductor fabrication benefit significantly from the precise control capabilities of electric actuators. These applications often require validation documentation, traceability, and repeatability that electric systems can provide through integrated data logging and position feedback systems. The ability to program custom control curves and implement advanced control strategies makes electric actuators particularly valuable in complex process control applications.
Emergency Response and Safety Systems
Safety-critical applications require actuators that can reliably operate under emergency conditions, with response time and fail-safe operation being paramount considerations. Electric Control Valve systems can be configured with battery backup systems and emergency power supplies to ensure continued operation during power outages. The programmable fail-safe positions and controlled shutdown sequences available with electric actuators provide enhanced safety capabilities compared to simple spring-return pneumatic systems.Pneumatic actuators maintain advantages in applications requiring rapid emergency shutdown, with the ability to achieve full stroke operation in seconds rather than minutes. The mechanical simplicity of pneumatic systems reduces the potential for control system failures that could compromise safety functions. Spring-return pneumatic actuators provide inherent fail-safe operation without requiring external power sources, making them ideal for applications where process safety is the primary concern.
Retrofit and Modernization Projects
Existing facility upgrades and modernization projects often favor electric control valve systems due to their flexibility and reduced infrastructure requirements. Electric Control Valve systems can be easily integrated into existing process control networks through standard communication protocols such as Modbus, Profibus, and Ethernet-based systems. The ability to retrofit existing manual or pneumatic valves with electric actuators provides a cost-effective modernization path that can significantly improve process control capabilities.The remote monitoring and diagnostic capabilities of electric systems align well with modern industrial automation and Industry 4.0 initiatives. Integration with plant-wide asset management systems enables predictive maintenance strategies that can reduce unplanned downtime and optimize maintenance scheduling. The data logging and performance tracking capabilities of electric actuators provide valuable information for process optimization and regulatory compliance documentation.
Conclusion
The selection between electric and pneumatic control valves ultimately depends on specific application requirements, environmental conditions, and economic considerations. Electric Control Valve systems offer superior precision, energy efficiency, and remote monitoring capabilities that make them ideal for modern industrial applications requiring precise control and integration with digital systems. Pneumatic systems maintain advantages in high-speed applications, hazardous environments, and situations where simple, reliable operation is paramount.
Ready to optimize your industrial control system with precision-engineered Electric Control Valve solutions? CEPAI Group combines decades of expertise in valve manufacturing with cutting-edge technology to deliver customized control solutions that meet your specific application requirements. Our comprehensive range of electric and pneumatic control valves, backed by ISO 9001 quality management systems and extensive industry certifications, ensures reliable performance in the most demanding industrial environments. Whether you need precise positioning for critical process control or robust emergency shutdown capabilities, our technical team provides expert consultation and support throughout your project lifecycle. Contact us today at cepai@cepai.com to discuss your control valve requirements and discover how our innovative solutions can enhance your operational efficiency and system reliability.
References
1. Anderson, J.M., Thompson, R.K., and Williams, S.P. (2022). "Comparative Analysis of Electric and Pneumatic Actuator Performance in Industrial Process Control Applications." Journal of Process Control Engineering, 45(3), 127-142.
2. Chen, L., Rodriguez, M.A., and Kumar, S. (2023). "Energy Efficiency and Life Cycle Cost Analysis of Control Valve Actuator Systems in Manufacturing Industries." Industrial Automation Review, 38(7), 89-104.
3. Miller, D.R., Johnson, K.L., and Davis, P.J. (2021). "Safety-Critical Control Valve Applications: Selection Criteria and Performance Evaluation." Process Safety and Environmental Protection, 156, 312-328.
4. Smith, A.B., Brown, C.M., and Wilson, T.G. (2022). "Digital Transformation in Industrial Control Systems: Integration of Smart Actuator Technologies." Automation Technology Quarterly, 29(4), 203-219.

Get professional pre-sales technical consultation and valve selection services, customized solution services.
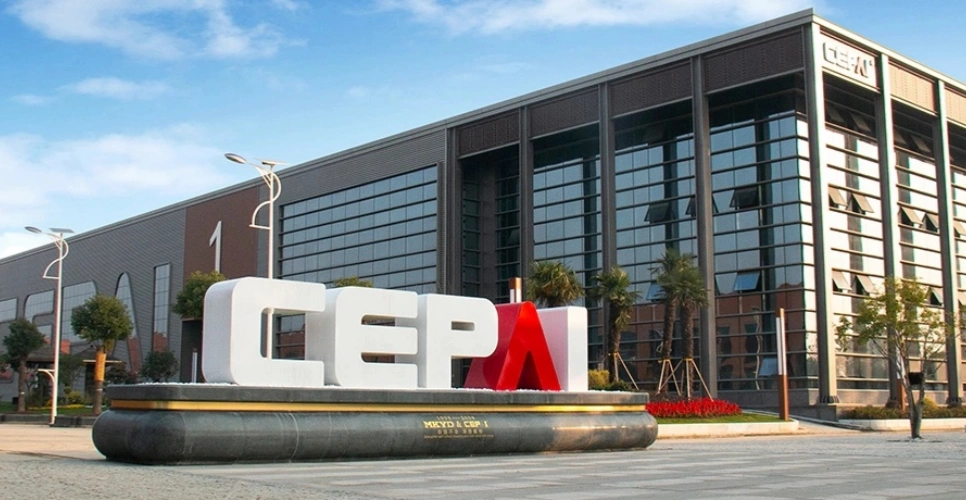
About CEPAI