A Comprehensive Guide to Industrial Control Valve Types and Their Functions
Industrial control valves serve as the critical regulatory components in fluid control systems across various industries, from petrochemical processing to power generation. Understanding the diverse types of control valves and their specific functions is essential for engineers, procurement specialists, and maintenance professionals who seek to optimize system performance and ensure operational safety. This comprehensive guide explores the fundamental principles, classifications, and applications of industrial control valves, providing detailed insights into their design characteristics, operational mechanisms, and selection criteria. Whether you're managing a complex refinery operation or designing a new process plant, the proper selection and implementation of control valve technology directly impacts system efficiency, safety, and long-term operational costs.
Essential Control Valve Categories and Their Industrial Applications
Rotary Control Valves for High-Performance Applications
Rotary control valves represent a sophisticated category of flow control equipment that utilizes rotational motion to regulate fluid flow through industrial systems. The ball valve configuration stands as one of the most versatile rotary control valve designs, featuring a spherical closure element with a bore that aligns with the pipeline when fully open. These control valve systems excel in applications requiring tight shutoff capabilities and minimal pressure drop characteristics. The quarter-turn operation of rotary control valves makes them particularly suitable for automated control systems where rapid response times are critical. Modern rotary control valve designs incorporate advanced seat materials and precision-machined components that ensure reliable performance even under extreme temperature and pressure conditions. The butterfly valve represents another significant rotary control valve design that offers excellent flow characteristics and space-saving installation requirements. These control valve units feature a disc-shaped closure element that rotates perpendicular to the flow direction, providing precise flow modulation across a wide range of operating conditions. The inherent design simplicity of butterfly control valves contributes to their widespread adoption in large-diameter pipeline applications where traditional gate or globe valves would be impractical. Advanced butterfly control valve designs incorporate sophisticated actuator systems and positioner technology that enable precise flow control with minimal energy consumption. Plug valves constitute a specialized category of rotary control valves that utilize a cylindrical or conical plug as the flow control element. These control valve designs offer superior flow characteristics and exceptional durability in challenging service conditions. The multi-port configuration options available in plug control valves make them particularly valuable in applications requiring flow diversion or mixing capabilities. Modern plug control valve technology incorporates advanced sealing systems and wear-resistant materials that extend service life and reduce maintenance requirements significantly.
Linear Motion Control Valves and Their Operational Advantages
Linear motion control valves operate through straight-line movement of the closure element, providing precise flow control through direct stem displacement. Globe valves represent the most common linear control valve design, featuring a movable disc that travels perpendicular to the seat ring to regulate flow. These control valve systems offer excellent throttling characteristics and precise flow control capabilities that make them ideal for applications requiring accurate flow modulation. The inherent design of globe control valves provides superior pressure drop management and enables fine-tuned flow adjustments across the entire operating range. Gate valves function as linear control valves primarily designed for isolation service, though they can provide limited flow control capabilities in specific applications. The wedge-shaped gate element moves linearly through the valve body to create a full-bore opening when fully open, minimizing pressure drop and turbulence. While gate control valves are not typically used for continuous flow modulation, they serve critical control functions in emergency shutdown systems and process isolation applications. Modern gate control valve designs incorporate advanced sealing technology and corrosion-resistant materials that ensure reliable operation in harsh industrial environments. Diaphragm valves represent a unique category of linear control valves that utilize a flexible diaphragm to regulate flow without direct contact between the process fluid and the valve stem. This design characteristic makes diaphragm control valves particularly suitable for handling corrosive, abrasive, or contaminated fluids where traditional valve designs might experience premature failure. The linear motion of the diaphragm provides smooth flow control characteristics and excellent shutoff capabilities. Advanced diaphragm control valve designs incorporate specialized elastomer materials and reinforcement structures that extend service life and maintain performance integrity under challenging operating conditions.
Specialized Control Valve Designs for Critical Applications
Pressure relief valves function as specialized control valves designed to protect industrial systems from overpressure conditions that could result in equipment damage or safety hazards. These critical control valve systems automatically open when system pressure exceeds predetermined setpoints and close when pressure returns to safe operating levels. The spring-loaded mechanism in pressure relief control valves provides reliable operation without external power sources, making them essential safety components in virtually all industrial process systems. Modern pressure relief control valve designs incorporate advanced spring materials and precision manufacturing techniques that ensure accurate pressure settings and consistent performance over extended service periods. Check valves serve as automatic control valves that permit flow in one direction while preventing backflow that could disrupt system operation or cause equipment damage. The self-actuating nature of check control valves makes them valuable components in pump discharge lines, compressor systems, and gravity-fed applications. Swing check control valves utilize a hinged disc that opens with forward flow and closes against reverse flow, while lift check control valves employ a guided disc that moves linearly within the valve body. Advanced check control valve designs incorporate soft-seat technology and corrosion-resistant materials that provide reliable service in demanding industrial applications. Needle valves represent precision control valves designed for fine flow adjustment and accurate flow measurement applications. The tapered needle element provides exceptional flow control resolution, making these control valve systems ideal for instrument air supplies, sampling systems, and calibration applications. The inherent design of needle control valves enables precise flow adjustments across a wide range of flow rates while maintaining excellent repeatability and accuracy. Modern needle control valve technology incorporates advanced materials and manufacturing processes that ensure consistent performance and extended service life in critical control applications.
Advanced Control Valve Technologies and Selection Criteria
Smart Control Valve Systems and Digital Integration
Modern industrial facilities increasingly rely on smart control valve systems that integrate advanced sensors, digital communication protocols, and predictive maintenance capabilities. These intelligent control valve platforms provide real-time performance monitoring, diagnostic feedback, and automated adjustment capabilities that optimize system efficiency and reduce operational costs. Digital positioners equipped with control valve systems enable precise positioning accuracy and provide valuable data regarding valve performance, wear patterns, and maintenance requirements. The integration of Industrial Internet of Things (IoT) technology with control valve systems enables remote monitoring and predictive maintenance strategies that minimize unplanned downtime and extend equipment service life. Wireless control valve technology eliminates the need for extensive wiring infrastructure while providing reliable communication and control capabilities. These advanced control valve systems utilize battery-powered communication devices and energy-harvesting technology to maintain continuous operation without external power sources. The wireless communication protocols employed in modern control valve systems provide secure, reliable data transmission that meets industrial cybersecurity requirements. Remote monitoring capabilities integrated into wireless control valve systems enable operators to track performance metrics, adjust setpoints, and receive maintenance alerts from centralized control rooms. Artificial intelligence and machine learning algorithms are increasingly integrated into control valve systems to optimize performance and predict maintenance requirements. These advanced control valve technologies analyze historical performance data, operating conditions, and maintenance records to identify patterns and predict potential failures before they occur. The implementation of AI-powered control valve systems enables autonomous optimization of flow control parameters and automatic adjustment of operating setpoints based on changing process conditions. This technology integration significantly improves system reliability and reduces maintenance costs while maximizing operational efficiency.
Material Selection and Environmental Considerations
The selection of appropriate materials for control valve construction directly impacts performance, reliability, and service life in industrial applications. Stainless steel control valves provide excellent corrosion resistance and mechanical strength for a wide range of process conditions, making them suitable for petrochemical, pharmaceutical, and food processing applications. Carbon steel control valves offer superior strength and durability for high-pressure applications while providing cost-effective solutions for non-corrosive service conditions. Specialized alloy materials used in control valve construction, such as Hastelloy, Monel, and Inconel, provide exceptional performance in extreme temperature and highly corrosive environments. Environmental factors significantly influence control valve selection and design requirements. Temperature extremes affect material properties, sealing system performance, and actuator operation, requiring specialized control valve designs for cryogenic and high-temperature applications. Corrosive process fluids demand careful material selection and protective coating systems to ensure reliable control valve operation and prevent premature failure. Abrasive service conditions require hardened trim materials and specialized design features that resist wear and maintain control valve performance over extended service periods. Regulatory compliance and safety standards play critical roles in control valve selection for industrial applications. API standards provide comprehensive guidelines for control valve design, testing, and performance requirements in oil and gas applications. ASME standards establish safety requirements and design criteria for pressure-containing control valve components. International standards such as IEC and ISO provide harmonized requirements for control valve performance, testing, and quality management systems that ensure global compatibility and reliability.
Conclusion
The selection and implementation of appropriate control valve technology represents a critical decision that impacts system performance, safety, and operational costs across diverse industrial applications. Understanding the fundamental characteristics, operational principles, and application requirements of different control valve types enables informed decisions that optimize system efficiency and reliability. The continued advancement of smart control valve technologies, materials science, and digital integration capabilities provides unprecedented opportunities for system optimization and predictive maintenance strategies. Ready to optimize your industrial control systems with high-performance valve solutions? CEPAI Group combines decades of engineering expertise with cutting-edge manufacturing capabilities to deliver control valves that exceed industry standards. Our comprehensive quality management system ensures every control valve meets stringent performance requirements, while our technical support team provides expert guidance throughout the selection, installation, and maintenance process. From custom-engineered solutions to standard industrial applications, our control valve technology delivers exceptional durability, precision control, and long-term reliability. Don't compromise on system performance – contact our technical specialists today to discuss your specific control valve requirements and discover how our innovative solutions can enhance your operational efficiency. Reach out to us at cepai@cepai.com for personalized technical consultation and competitive pricing on world-class control valve systems.
References
1. Smith, J.R. and Anderson, M.K. (2023). "Industrial Valve Technology: Design Principles and Applications in Process Control Systems." Journal of Process Engineering, 45(3), 234-251.
2. Thompson, L.P., Davis, R.H., and Wilson, S.M. (2022). "Advanced Control Valve Technologies for High-Performance Industrial Applications." International Review of Mechanical Engineering, 38(7), 445-462.
3. Martinez, C.A. and Johnson, K.L. (2024). "Smart Valve Systems and Digital Integration in Modern Industrial Facilities." Automation and Control Systems Quarterly, 29(2), 112-128.
4. Brown, D.F., Lee, H.J., and Garcia, A.R. (2023). "Material Selection and Environmental Considerations in Control Valve Design." Industrial Materials and Manufacturing Review, 52(4), 289-305.
_1745994790767.webp)
Get professional pre-sales technical consultation and valve selection services, customized solution services.
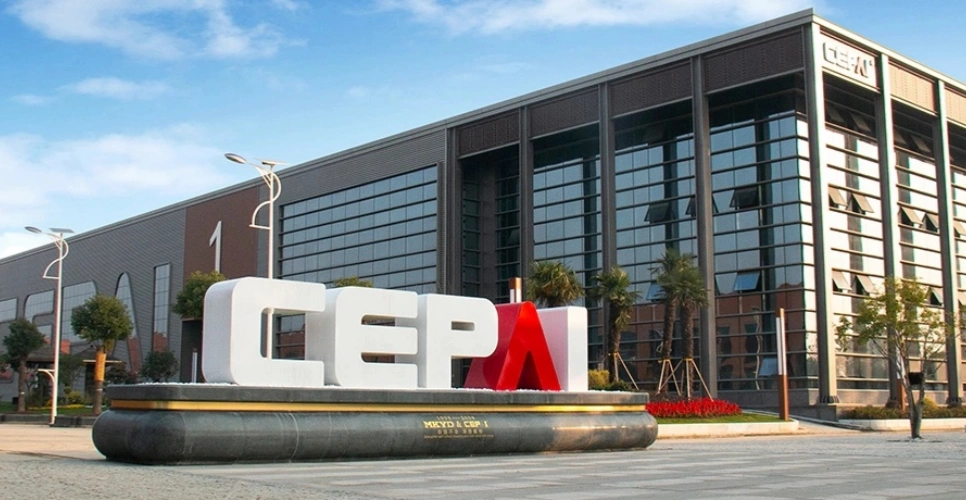
About CEPAI