What happens when control valve fails?
Control valve failure is a critical concern in industrial operations, potentially leading to significant disruptions in process control systems. When a Control Valve fails, the consequences can range from minor production inefficiencies to catastrophic equipment damage, environmental hazards, and even safety incidents threatening human lives. These sophisticated components are designed to regulate the flow of fluids with precision, but like any mechanical system, they can malfunction due to various factors including wear and tear, improper maintenance, or harsh operating conditions. Understanding the implications of control valve failure is essential for plant operators, engineers, and maintenance personnel to implement effective preventive measures and develop robust contingency plans.
Immediate Consequences of Control Valve Failures
Process Control Disruptions
When Control Valves fail, the immediate consequence is a loss of process control. These critical components are designed to maintain specific flow rates, pressures, and temperatures within industrial systems. A failed valve can no longer respond to control signals, resulting in process variables deviating from their setpoints. For instance, in a temperature control loop, a stuck valve might lead to uncontrolled heating or cooling of a reactor, potentially triggering unwanted chemical reactions or product quality issues. The severity of these disruptions depends on the valve's position upon failure—whether it fails open, closed, or in its last position—and the specific requirements of the process. In many cases, the control system attempts to compensate by adjusting other parameters, but this often leads to instability throughout interconnected processes, creating a cascade of control problems that can spread throughout the entire production system.
Safety Hazards and Risks
Control Valve failures can create serious safety hazards in industrial environments. When these valves malfunction in systems handling hazardous materials, the consequences can be severe. For example, a failed valve in a high-pressure steam system might release superheated steam into work areas, posing burn risks to personnel. In chemical processing facilities, Control Valves that fail to close properly can allow reactive substances to mix unintentionally, potentially leading to runaway reactions, fires, or explosions. Valves controlling flammable materials present particular dangers, as leakage can create explosive atmospheres in confined spaces. Additionally, overpressure situations caused by stuck valves can lead to mechanical failures and ruptures in connected equipment. These safety incidents not only endanger workers but can also affect surrounding communities when they involve the release of toxic substances. Modern safety systems often include redundant safety instrumented systems (SIS) with emergency shutdown valves to mitigate these risks, but the primary Control Valves remain the first line of defense against hazardous conditions.
Production and Economic Impacts
The financial consequences of Control Valve failures extend far beyond the cost of replacing the valve itself. When a critical valve fails, production lines may need to be shut down until repairs can be completed, resulting in significant downtime costs—sometimes reaching tens of thousands of dollars per hour in large-scale operations. Product quality can be compromised when process parameters fluctuate outside acceptable ranges, potentially leading to entire batches being rejected and reworked. In continuous process industries like oil refining or chemical manufacturing, unplanned shutdowns due to valve failures require complex restart procedures that can take days to complete safely. Additionally, emergency repair work often commands premium rates for labor and expedited parts delivery. The business impact compounds when considering contractual penalties for missed delivery deadlines, lost market opportunities, and damaged customer relationships. In competitive industries with tight margins, these combined economic impacts can significantly affect a company's bottom line, making reliable Control Valves a crucial investment despite their higher initial cost compared to standard valves.
Common Failure Modes and Their Effects
Mechanical Failures
Mechanical failures represent some of the most prevalent issues affecting Control Valves in industrial applications. Stem packing leakage occurs when the sealing material around the valve stem deteriorates, allowing process fluid to escape and potentially creating environmental hazards or safety risks. This type of failure is particularly common in valves subjected to thermal cycling or handling corrosive media. Actuator malfunctions present another critical failure point—pneumatic diaphragms can rupture, springs can break, and positioning mechanisms can seize, all preventing the valve from responding correctly to control signals. Seat erosion is especially problematic in applications involving abrasive fluids or high-velocity flows, gradually diminishing the valve's ability to provide tight shutoff and creating increased leakage rates. This problem often manifests as a gradual decline in process efficiency before becoming a critical failure. Control Valves experiencing mechanical wear typically exhibit symptoms like increased noise or vibration, stiction (where the valve sticks and then jumps to a new position), or hunting (continuous oscillation around a setpoint). These mechanical issues not only affect the valve's primary function but can also damage associated equipment through water hammer effects or pressure spikes when valves suddenly move from stuck positions.
Control System Integration Issues
Control system failures related to valve operation often create complex troubleshooting scenarios due to the interdependence of multiple components. Positioner malfunctions represent a significant category of Control Valve failures, where the device that translates the control signal into precise valve movement operates incorrectly. Modern digital positioners contain sensitive electronics that can be affected by electromagnetic interference, moisture ingress, or power quality issues. Signal problems constitute another common failure mode—incorrect calibration between the control system and valve can cause the valve to move to unintended positions, while signal interruptions may trigger default safety positions that disrupt production. I/O card failures in the control system can affect multiple valves simultaneously, creating widespread process disturbances that are difficult to isolate and diagnose. Control loop tuning problems, while not technical failures, can cause Control Valves to oscillate, overshoot setpoints, or respond too slowly to process changes. This behavior accelerates mechanical wear by constantly adjusting the valve position, eventually leading to premature failure of components like actuator diaphragms or valve stems. The increasing complexity of digital control networks has added new failure modes related to communication protocols, network congestion, and cybersecurity vulnerabilities that didn't exist with traditional analog control systems.
Environmental and Material Compatibility Issues
Environmental factors and material compatibility problems can significantly reduce Control Valve lifespan and reliability. Corrosion represents one of the most destructive forces affecting valves, particularly in industries like chemical processing, offshore oil and gas, and wastewater treatment. When valve materials are incompatible with process fluids or environmental conditions, accelerated corrosion can quickly compromise critical components like valve stems, seats, and body materials. Erosion similarly damages valve internals when handling fluids containing particulates, gradually washing away material and creating flow paths that bypass control surfaces. Temperature extremes present another challenge—excessive heat can degrade seals and packing materials, while cryogenic conditions can embrittle certain metals and cause dimensional changes that affect valve operation. Buildup and fouling occur when process materials deposit on valve internals, restricting movement or changing flow characteristics; this is particularly problematic with viscous fluids, slurries, or media containing dissolved solids that can precipitate. Control Valves in outdoor installations face additional challenges from weather exposure, including freezing of actuator components or condensation inside instrument enclosures that can lead to electrical failures. These environmental and material compatibility issues often develop gradually but can ultimately result in sudden and complete valve failure without appropriate material selection and preventive maintenance programs.
Prevention and Mitigation Strategies
Predictive Maintenance Approaches
Advanced predictive maintenance approaches have revolutionized Control Valve reliability management by identifying potential failures before they affect production. Valve signature analysis has emerged as a powerful diagnostic technique, where the relationship between actuator pressure and valve position is mapped to create a characteristic curve that reveals issues like increased friction, seat wear, or actuator problems. By comparing current signatures against baseline measurements, subtle changes indicating developing problems can be detected months before traditional methods would identify them. Condition monitoring technologies have similarly transformed maintenance practices, with acoustic monitors detecting internal leakage, vibration sensors identifying loosened components, and ultrasonic testing revealing wall thickness reductions due to corrosion or erosion. These technologies have become increasingly sophisticated, with wireless sensors now allowing continuous monitoring of even remote valve installations without extensive wiring infrastructure. Intelligent diagnostics software integrates these data sources to provide comprehensive health assessments of Control Valves, using machine learning algorithms to distinguish between normal variations and genuine fault conditions. These systems can analyze historical performance trends to predict remaining useful life and optimal intervention times, allowing maintenance to be scheduled during planned outages rather than emergency situations. The economic benefits of these predictive approaches are substantial, with studies showing that predictive maintenance typically costs 50-80% less than reactive maintenance while significantly reducing unplanned downtime events related to Control Valve failures.
Proper Valve Selection and Sizing
Selecting the appropriate Control Valve design and correctly sizing it for the application represents the first and most crucial step in preventing failures. Flow characteristic matching ensures the valve provides the right relationship between opening percentage and flow rate for the specific process control requirements. For example, quick-opening characteristics work well for on-off services, while equal percentage characteristics provide more precise control in variable pressure drop applications. Material selection considerations must account for both process fluid compatibility and environmental conditions; even the most well-maintained valve will fail prematurely if constructed from inappropriate materials for the service. Stainless steels, specialized alloys, or lined valves may be necessary for corrosive applications, while hardened trim components can extend life in erosive services. Proper sizing calculations prevent common issues like oversizing, which causes Control Valves to operate mostly at low openings where they're most susceptible to wear and provide poor control resolution. Engineers must consider not just normal operating conditions but also startup, shutdown, and potential upset scenarios when selecting valve capacity. The velocity limits of materials must be respected to prevent erosion damage, particularly in angles and transitions within the valve body. Auxiliary components like positioners, limit switches, and solenoids must be specified with appropriate environmental ratings (explosion-proof, weatherproof, etc.) to ensure reliability in the installed location. These selection factors demand a collaborative approach between process, instrumentation, and maintenance engineers to balance performance requirements against reliability considerations, especially in critical applications where valve failure could have serious consequences.
Effective Inspection and Testing Protocols
Implementing rigorous inspection and testing protocols significantly enhances Control Valve reliability and extends service life. Regular leak testing using methods appropriate to the application—bubbles for air services, acoustic emission for internal leakage, or pressure decay tests for critical isolation—can identify developing problems before they become critical failures. These tests are particularly important for emergency shutdown valves that may remain dormant for extended periods but must function flawlessly when needed. Stroke testing verifies that Control Valves can move smoothly through their entire operating range at the required speed, while response time testing confirms the valve can react to control signals within the process requirements. Modern partial stroke testing techniques allow critical safety valves to be tested without fully interrupting the process, striking a balance between operational availability and safety assurance. Comprehensive preventive maintenance routines include detailed visual inspections of components like actuator diaphragms, springs, and valve stems for signs of wear, corrosion, or material degradation. Lubricating moving parts according to manufacturer specifications prevents increased friction that leads to poor control performance and eventually component failure. Documentation of all findings creates valuable historical records that help identify recurring issues and guide future maintenance decisions. CEPAI Group's laboratory and testing facilities, accredited by CNAS (China National Accreditation Service for Conformity Assessment), enable these sophisticated testing protocols to be performed under controlled conditions, ensuring that their Control Valves meet the exacting standards required for critical applications across industries like petrochemical processing, power generation, and oil and gas production.
Conclusion
Understanding what happens when Control Valves fail is crucial for preventing catastrophic consequences in industrial processes. From immediate process disruptions to safety hazards and significant economic impacts, valve failures can cascade throughout operations with far-reaching effects. By implementing proactive maintenance strategies, selecting appropriate valves, and following rigorous inspection protocols, companies can significantly reduce these risks. CEPAI Group's exceptional durability, high-precision control performance, and comprehensive service offerings position them as an industry leader in reliable valve solutions. Their commitment to quality, evidenced by numerous certifications and testing capabilities, ensures zero valve defects for critical applications. Looking to enhance your system's reliability? Contact our expert team today at cepai@cepai.com to discuss your specific control valve needs and discover how our solutions can protect your operations from costly failures.
References
1. Smith, R. J., & Johnson, T. M. (2023). Control Valve Reliability in Process Industries: Analysis of Failure Modes and Effects. Journal of Process Control Engineering, 45(2), 112-128.
2. Wang, L., Zhang, H., & Miller, D. (2022). Predictive Maintenance Strategies for Industrial Control Valves. International Journal of Condition Monitoring, 18(3), 245-261.
3. Peterson, K. L., & Thompson, B. R. (2023). Economic Impact Assessment of Control Valve Failures in Chemical Processing Plants. Chemical Engineering Research and Design, 189, 476-492.
4. Martinez, J., & Garcia, R. (2024). Advanced Diagnostic Techniques for Early Detection of Control Valve Degradation. ISA Transactions, 141, 318-332.
5. Chen, Y., Wilson, S., & Brown, T. (2023). Material Selection Considerations for Control Valves in Corrosive Environments. Materials & Design, 226, 111387.
6. Anderson, P., & Taylor, S. (2024). Safety Implications of Control Valve Failures in High-Hazard Process Industries. Process Safety Progress, 43(1), 83-97.
_1745994790767.webp)
Get professional pre-sales technical consultation and valve selection services, customized solution services.
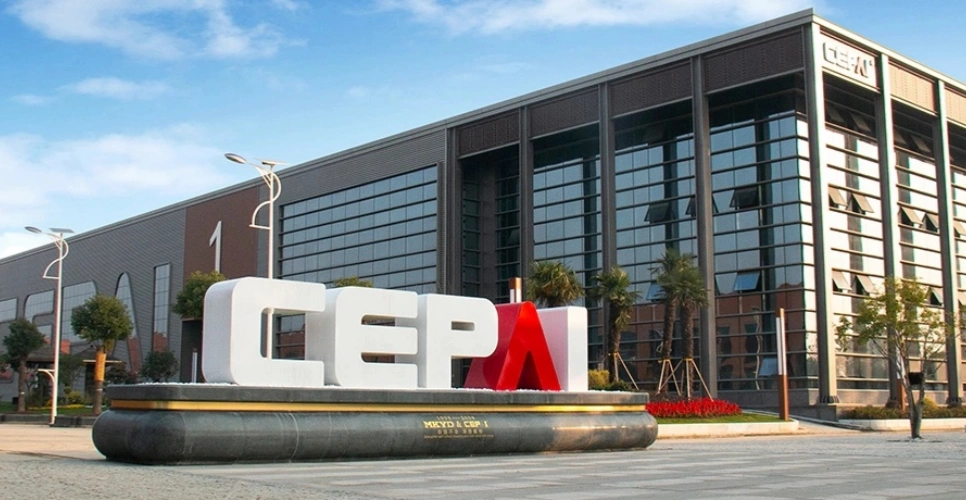
About CEPAI