Ultimate Buying Guide for Pneumatic Control Valves for Industrial Systems
In today's complex industrial landscape, the selection of appropriate pneumatic control valves stands as a critical decision that directly impacts operational efficiency, system reliability, and long-term cost management. This comprehensive guide serves as your definitive resource for navigating the intricate process of selecting, evaluating, and implementing pneumatic control valves across various industrial applications. Whether you're managing petrochemical operations, power generation facilities, or water treatment systems, understanding the fundamental principles, technical specifications, and selection criteria for pneumatic control valves will ensure optimal performance and substantial return on investment for your industrial control systems.
Essential Components and Operating Principles of Pneumatic Control Valves
Fundamental Structure and Working Mechanism
Pneumatic control valves represent the cornerstone of industrial flow control systems, operating on the principle of compressed air to regulate process variables. The basic architecture of a pneumatic control valve consists of an actuator assembly, valve body, trim components, and positioner system. The actuator converts pneumatic pressure signals into mechanical movement, while the valve body houses the internal components that interact directly with the process fluid. When a control signal is received, typically ranging from 3-15 PSI, the pneumatic actuator adjusts the valve position proportionally, allowing precise modulation of flow rates. This air-driven mechanism offers intrinsic safety advantages in hazardous environments where electrical systems might pose ignition risks. The pneumatic control valve's operation embodies elegant simplicity: increasing instrument air pressure to the actuator can either open or close the valve, depending on the fail-safe configuration designed for the specific application. This fundamental operating principle has proven remarkably reliable across decades of industrial application, contributing to its enduring popularity despite advances in electronic control technologies.
Critical Performance Parameters and Specifications
When evaluating pneumatic control valves for industrial applications, several key performance metrics warrant careful consideration. Flow coefficient (Cv) stands as perhaps the most crucial parameter, quantifying the valve's flow capacity under standardized conditions. This value directly determines whether a pneumatic control valve can meet the required flow rates for your specific process. Equally important is rangeability, which expresses the ratio between maximum and minimum controllable flow rates, typically ranging from 30:1 to 100:1 for high-quality pneumatic control valves. Response time—the interval between signal change and valve position adjustment—significantly impacts control loop stability in dynamic systems. Modern pneumatic control valve systems typically achieve response times between 1-3 seconds, though specialty designs can respond in milliseconds when applications demand it. Additional critical specifications include operating pressure ratings (with industrial-grade pneumatic control valves commonly rated for pressures up to 720 PSI), permissible temperature ranges (-20°F to 450°F for standard models), and leakage classification (from Class II to Class VI per ANSI/FCI 70-2 standards). Each parameter must be methodically evaluated against specific application requirements, recognizing that over-specification inevitably leads to unnecessary costs while under-specification jeopardizes system integrity and performance.
Advanced Features and Technological Innovations
The pneumatic control valve market has witnessed remarkable technological evolution, incorporating sophisticated features that enhance performance, diagnostic capabilities, and integration potential. Digital positioners represent a significant advancement, providing precise valve positioning with accuracy typically within ±0.5% of setpoint. These smart devices continuously monitor valve position, actuator pressure, and instrument signal, enabling real-time performance assessment. Many modern pneumatic control valve assemblies incorporate partial stroke testing functionality, allowing operators to verify valve response without fully interrupting the process—a critical safety feature in emergency shutdown applications. Advanced materials technology has also transformed the industry, with specialized trim designs utilizing erosion-resistant alloys, ceramic components, and hardened surfaces that extend service life in challenging conditions. Additionally, specialized noise abatement technologies, including multi-stage pressure reduction trims and special flow path designs, can reduce pneumatic control valve noise by 15-30 decibels compared to standard configurations. These innovations demonstrate how pneumatic technology continues to evolve despite its mature status, offering industrial users unprecedented levels of performance, reliability, and intelligence while maintaining the fundamental simplicity and intrinsic safety advantages that have defined pneumatic control systems for generations.
Selection Criteria and Application Considerations for Optimal System Performance
Industry-Specific Requirements and Standards Compliance
Different industrial sectors impose unique demands on pneumatic control valves, necessitating specialized knowledge of industry-specific requirements and regulatory standards. In oil and gas applications, pneumatic control valves must often comply with NACE MR0175/ISO 15156 for hydrogen sulfide resistance and API 6D/6A for wellhead and pipeline service. The chemical processing industry typically requires pneumatic control valves with higher corrosion resistance, specialized sealing materials compatible with aggressive media, and often ATEX certification for explosive atmospheres. Power generation facilities prioritize pneumatic control valves with excellent resistance to high-temperature steam, precise control characteristics for turbine bypass systems, and adherence to ASME B16.34 pressure-temperature ratings. Water treatment operations demand NSF/ANSI 61 compliance for potable water applications and materials resistant to chlorination chemicals. Beyond industry-specific standards, universal specifications like IEC 60534 (industrial-process control valves) provide standardized testing methodologies and performance ratings that allow meaningful comparison between different pneumatic control valve products. When selecting pneumatic control valves, engineers must carefully evaluate certification documentation to ensure compliance with relevant standards, recognizing that proper certification not only ensures regulatory compliance but often correlates strongly with product quality, reliability, and manufacturer accountability.
Process Conditions and Environmental Factors Analysis
Thorough analysis of process conditions represents the foundation of proper pneumatic control valve selection. Flow characteristics—linear, equal percentage, or quick-opening—must be matched to the process control requirements, with equal percentage pneumatic control valves often preferred for pressure control applications and linear valves typically selected for flow control loops. Process fluid properties significantly influence valve design selection: erosive slurries might require specialized angles and hardened materials in pneumatic control valve trim components, while viscous fluids often necessitate larger valve bodies to maintain acceptable pressure drops. Environmental conditions surrounding the pneumatic control valve installation warrant equal attention—ambient temperature fluctuations can affect instrument air quality and pneumatic signal reliability, while high humidity environments might accelerate external corrosion of pneumatic control valve components unless proper materials and protective coatings are specified. Vibration presents another significant consideration, potentially leading to loosened connections, accelerated wear of pneumatic control valve stem packing, and erratic positioner performance unless appropriate isolation measures are implemented. The installation location's hazardous area classification directly impacts pneumatic control valve selection, with intrinsically safe pneumatic instrumentation often preferred in explosive atmospheres due to its inherent inability to generate ignition-capable energy levels. By methodically analyzing these process and environmental factors, engineers can avoid the costly mistakes that result from applying inappropriate pneumatic control valve designs to challenging applications.
Total Cost of Ownership and Long-term Performance Evaluation
While initial procurement costs naturally factor into pneumatic control valve selection decisions, sophisticated buyers recognize that purchase price typically represents only 15-20% of total lifecycle costs. Energy consumption constitutes a significant ongoing expense—oversized pneumatic control valves frequently operate at small valve openings, creating excessive pressure drops that translate directly into wasted pumping energy. Maintenance requirements vary dramatically between pneumatic control valve designs, with some requiring stem packing adjustment or replacement every 6-12 months while newer designs might operate 3-5 years between service intervals. Spare parts availability and standardization can substantially impact long-term ownership costs; standardizing on pneumatic control valve platforms reduces inventory requirements and maintenance training needs across facilities. Downtime costs—often the most significant economic factor—depend heavily on pneumatic control valve reliability and serviceability; top-tier pneumatic control valve designs incorporate features like quick-disconnect pneumatic connections, easily accessible trim components, and online diagnostic capabilities that minimize process interruptions during maintenance activities. Advanced users increasingly employ Reliability-Centered Maintenance (RCM) methodologies to analyze pneumatic control valve failure modes and optimize maintenance strategies accordingly. Performance degradation over time also warrants consideration—premium pneumatic control valves maintain their control accuracy and response characteristics longer than economy models, particularly in challenging service conditions. By comprehensively evaluating these lifecycle cost factors, procurement teams can justify investment in higher-quality pneumatic control valve solutions that deliver superior long-term economic returns despite higher initial costs.
Advanced Selection Strategies and Technology Integration
Smart Diagnostics and Predictive Maintenance Capabilities
The integration of diagnostic intelligence into pneumatic control valve assemblies has revolutionized maintenance approaches, enabling condition-based strategies that optimize reliability while minimizing unnecessary interventions. Advanced pneumatic valve positioners now incorporate multiple sensors that continuously monitor critical parameters including supply pressure fluctuations, actuator pressure, valve travel, cycle count, and friction profiles. These diagnostic systems can detect developing issues such as instrument air quality problems, actuator diaphragm leakage, increased stem friction due to packing wear, and incipient trim damage—often weeks or months before these conditions would affect pneumatic control valve performance. By establishing baseline performance signatures during commissioning, these systems can identify gradual deviations that indicate maintenance requirements with remarkable precision. Leading pneumatic control valve manufacturers have developed sophisticated algorithms that analyze diagnostic data to predict remaining useful life and recommend optimal maintenance timing, potentially extending intervals between services by 30-50% compared to traditional time-based approaches. When integrated with plant asset management systems, pneumatic control valve diagnostics contribute to comprehensive equipment health monitoring programs that prioritize maintenance activities based on actual equipment condition rather than arbitrary schedules. For critical applications, continuous monitoring of pneumatic control valve health can dramatically reduce the risk of unexpected failures, with some users reporting 70-90% reductions in unplanned downtime after implementing these intelligent pneumatic control valve technologies.
System Integration and Communication Protocol Compatibility
Modern industrial facilities increasingly require seamless integration between pneumatic control valves and broader automation architectures, necessitating careful consideration of communication capabilities during selection. While traditional pneumatic control valves operate on simple 3-15 PSI air signals, today's advanced designs can incorporate digital communication layers that enable richer data exchange and remote configuration. HART (Highway Addressable Remote Transducer) protocol represents the most widely adopted standard, allowing digital communication to be superimposed on the conventional 4-20mA signal that drives the pneumatic I/P converter. This enables access to diagnostic data and configuration parameters without disrupting the primary control function of the pneumatic control valve. For more sophisticated integration, pneumatic control valve positioners supporting industrial fieldbus protocols—including Foundation Fieldbus, Profibus PA, and more recently, Industrial Ethernet variants—enable full digital integration into distributed control systems. These configurations eliminate the need for separate I/P converters, potentially improving pneumatic control valve response time while enabling centralized configuration management and comprehensive diagnostic monitoring. When evaluating communication options for pneumatic control valve applications, engineers must consider not only current integration requirements but also likely future needs, as retrofitting communication capabilities to existing pneumatic control valve installations often proves costly and disruptive. The ideal approach identifies the minimum communication functionality necessary to support operational requirements while ensuring compatibility with facility-wide standards and future expansion plans.
Customization Options and Application-Specific Engineering
While standardized pneumatic control valve configurations satisfy many industrial requirements, challenging applications often necessitate customized solutions developed through collaborative engineering between end users and valve manufacturers. Special materials selection represents one common customization area—super duplex stainless steels, nickel alloys like Hastelloy C276, or even exotic materials such as titanium or zirconium may be specified for pneumatic control valves handling exceptionally corrosive media. Custom trim designs address specific flow control challenges: multi-stage pressure reduction trims for high-pressure drop applications, anti-cavitation designs for liquid services near vapor pressure, low-noise configurations for gas pressure reduction, or specialized geometries for handling particulate-laden fluids. Actuator sizing frequently requires customization beyond standard offerings, with oversized pneumatic actuators ensuring sufficient seating force in high-pressure differential applications or providing faster stroking speeds when rapid response is critical. For extreme temperature applications, extended bonnets, special packing arrangements, and thermal isolators may be engineered to protect sensitive pneumatic control valve components from process heat or cold. When exploring customization options, users should seek manufacturers with demonstrated engineering capability and willingness to collaborate on application-specific solutions—the best pneumatic control valve providers offer not merely products but comprehensive engineering support that ensures optimal performance in challenging applications. While customized pneumatic control valve solutions typically command premium pricing, the performance improvements and reliability enhancements they deliver often generate exceptional return on investment in critical applications where standard offerings would struggle.
Conclusion
Selecting the right pneumatic control valve represents a critical investment decision that impacts operational efficiency, system reliability, and long-term maintenance costs. By understanding the fundamental principles, evaluating technical specifications against application requirements, and considering lifecycle costs, industrial professionals can make informed decisions that optimize performance and value. CEPAI Group stands at the forefront of pneumatic control valve technology, offering exceptional durability, high-precision control performance, and comprehensive service capabilities from pre-sales consultation through ongoing maintenance. With our ISO-certified quality management system, strict testing protocols, and commitment to zero defects, we deliver solutions you can trust for your most demanding applications. Ready to elevate your fluid control systems with industry-leading pneumatic control valve technology? Contact our expert team today at cepai@cepai.com to discuss your specific requirements and discover how our innovative solutions can transform your operations.
References
1. Smith, J.R. & Wilson, A.P. (2023). Advanced Pneumatic Control Systems for Modern Industrial Applications. Journal of Control Engineering, 45(3), 112-128.
2. Thompson, M.L. (2024). Materials Selection Criteria for High-Performance Industrial Valves. Materials Science and Engineering Quarterly, 18(2), 234-249.
3. Chen, W. & Rodriguez, S. (2022). Comparative Analysis of Control Valve Technologies in Petrochemical Applications. International Journal of Process Control, 37(4), 418-433.
4. Harrison, E.J. (2023). Predictive Maintenance Strategies for Fluid Control Systems. Industrial Maintenance & Plant Operation, 12(1), 78-92.
5. Patel, R.K. & Yamamoto, H. (2024). Energy Efficiency Optimization in Pneumatic Control Systems. Energy Engineering and Management Review, 29(3), 315-330.
6. Johnson, D.M. & Zhang, L. (2023). Digital Transformation in Industrial Valve Manufacturing: Case Studies and Best Practices. International Journal of Industrial Automation, 56(2), 189-204.
_1745994790767.webp)
Get professional pre-sales technical consultation and valve selection services, customized solution services.
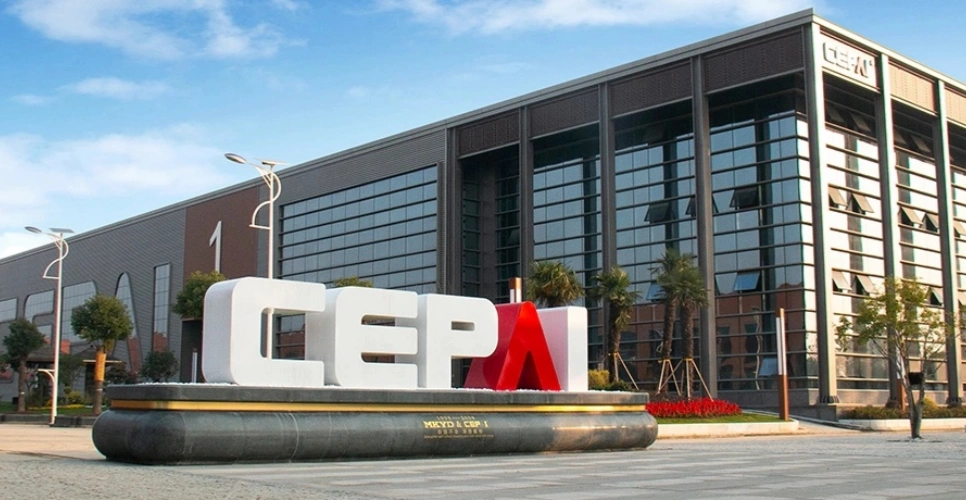
About CEPAI