Explore the Latest Advances in Pneumatic Control Valve Technology
In today's rapidly evolving industrial landscape, pneumatic control valves represent a critical component in fluid management systems across various sectors. Recent technological innovations have transformed these essential devices, offering unprecedented precision, intelligence, and efficiency. As industries push toward greater automation and process optimization, understanding the cutting-edge developments in pneumatic control valve technology becomes imperative for engineers, plant managers, and procurement specialists seeking competitive advantages in their operations.
Smart Integration: The Evolution of Pneumatic Control Valve Systems
The integration of smart technologies with traditional pneumatic control valve systems has revolutionized industrial process control, offering unprecedented levels of precision, reliability, and data-driven decision-making capabilities.
Advanced Diagnostic Capabilities Redefining Maintenance Approaches
The incorporation of sophisticated diagnostic technologies in modern pneumatic control valve systems represents a paradigm shift in maintenance strategies. Today's advanced pneumatic control valve units feature embedded sensors that continuously monitor critical parameters such as stem position, actuator pressure, friction forces, and cycle counts. These intelligent systems can detect subtle deviations in performance metrics, identifying potential issues long before they manifest as operational failures. For instance, diagnostic algorithms can recognize patterns indicating seat wear, packing deterioration, or actuator inefficiency, providing maintenance teams with actionable insights rather than merely reporting failures. This predictive approach dramatically reduces unplanned downtime, with studies indicating a reduction of up to 70% in emergency maintenance interventions. Additionally, these diagnostic systems optimize maintenance schedules based on actual equipment condition rather than arbitrary time intervals, eliminating unnecessary interventions while ensuring critical components receive attention when truly needed. The result is a maintenance strategy that maximizes the lifespan of pneumatic control valve systems while minimizing both maintenance costs and operational disruptions.
IoT Connectivity Enhancing Remote Monitoring and Control
The integration of Internet of Things (IoT) capabilities with pneumatic control valve technology has transformed how these critical components are monitored and managed. Modern pneumatic control valve systems now incorporate communication protocols such as HART, Foundation Fieldbus, and wireless technologies that enable seamless integration with broader industrial control networks. This connectivity facilitates real-time data transmission between valve assemblies and central control systems, allowing operators to monitor performance metrics, adjust parameters, and implement control strategies remotely. The implications for operational efficiency are profound, particularly for facilities with geographically dispersed assets or hazardous environments where physical access presents challenges. Plant managers can now oversee entire valve networks from a single dashboard, receiving instant notifications of performance anomalies and implementing corrective actions without deploying field technicians. Furthermore, this connectivity enables the aggregation of performance data across multiple pneumatic control valve units, facilitating comparative analysis and system-wide optimization. The ability to implement coordinated control strategies across interconnected processes represents a significant advancement beyond traditional isolated control approaches, allowing for more sophisticated process optimization that accounts for complex interdependencies between different system components.
Machine Learning Algorithms Optimizing Performance Parameters
The application of machine learning algorithms to pneumatic control valve systems represents perhaps the most transformative advancement in recent years. These sophisticated analytical tools continuously process the vast quantities of data generated by modern valve assemblies, identifying complex patterns and relationships that would remain invisible to human operators. Unlike traditional control systems with static parameters, machine learning-enabled pneumatic control valve systems can dynamically adjust their operational characteristics based on changing process conditions, historical performance data, and predictive models. For example, these systems can automatically optimize valve positioning to account for variations in fluid properties, system demands, or upstream/downstream conditions without manual intervention. The learning capabilities of these systems mean they become increasingly effective over time, refining their control algorithms based on accumulated operational experience. This results in pneumatic control valve systems that not only maintain precise control under varying conditions but actually improve their performance metrics over time. Industry leaders implementing these advanced systems report significant improvements in control precision, with deviation from setpoint values reduced by up to 40% compared to conventional systems, while simultaneously reducing compressed air consumption through more efficient actuator operation.
Material Science Breakthroughs: Enhancing Durability and Performance
Recent advances in material science have dramatically transformed the capabilities and longevity of pneumatic control valve components, enabling these critical devices to operate reliably in increasingly demanding industrial environments.
High-Performance Polymers Extending Service Life in Harsh Environments
The development and implementation of advanced polymer materials has revolutionized pneumatic control valve durability in challenging operating conditions. Traditional elastomers and plastics often degraded rapidly when exposed to aggressive chemicals, extreme temperatures, or abrasive media, necessitating frequent maintenance and replacement. Modern pneumatic control valve systems now incorporate specialized polymers such as perfluoroelastomers (FFKM), polyetheretherketone (PEEK), and advanced fluoropolymer compounds that offer exceptional chemical resistance across the pH spectrum. These materials maintain their mechanical properties at temperature extremes ranging from cryogenic applications (-320°F) to high-temperature processes exceeding 600°F. The impact on valve performance and longevity is substantial – case studies from the chemical processing industry demonstrate that pneumatic control valve trim components manufactured from these advanced polymers can maintain dimensional stability and sealing integrity for up to five times longer than conventional materials when handling corrosive process fluids. Additionally, these high-performance polymers offer superior resistance to explosive decompression, making them ideal for high-pressure gas applications where conventional elastomers would fail. The reduced friction coefficients of these materials also contribute to more precise control response and lower actuator force requirements, enhancing the overall efficiency of pneumatic control valve systems while simultaneously extending service intervals and reducing total cost of ownership for end-users operating in harsh industrial environments.
Nano-Engineered Surfaces Minimizing Friction and Wear
The application of nanotechnology to pneumatic control valve components represents a quantum leap in addressing long-standing challenges related to friction, wear, and flow characteristics. Traditional surface finishing techniques achieved limited success in optimizing the tribological properties of valve stems, plugs, and seats. Contemporary advanced manufacturing processes now enable the creation of nano-engineered surfaces with precisely controlled topographies at the molecular level. These surfaces feature specialized patterns that create air pockets to reduce contact area and minimize friction, or directional structures that optimize flow dynamics around trim components. Additionally, cutting-edge pneumatic control valve manufacturers apply nano-scale coatings such as diamond-like carbon (DLC), tungsten disulfide, or ceramic composites that provide extraordinary hardness ratings exceeding 80 Rockwell C while maintaining exceptionally low friction coefficients. The performance improvements are remarkable – pneumatic control valve assemblies with nano-engineered surfaces demonstrate up to 80% reduction in actuation force requirements, dramatically enhancing control precision particularly at low-travel positions where stiction typically compromises performance. Moreover, accelerated wear testing shows these surfaces maintain their performance characteristics for millions of cycles under load conditions that would rapidly degrade conventional materials. This extended performance envelope makes nano-engineered pneumatic control valve components particularly valuable in applications requiring precise throttling control or frequent cycling, such as batch processing operations or modulating control loops in critical process applications where consistent performance over time is essential for maintaining product quality and process efficiency.
Composite Materials Delivering Superior Thermal Stability
Thermal cycling and extreme temperature exposure have traditionally presented significant challenges for pneumatic control valve reliability, causing dimensional changes, material degradation, and seal failures. Recent breakthroughs in composite material technology have introduced remarkable solutions specifically engineered for pneumatic control valve applications. Advanced ceramic-reinforced polymer composites, carbon fiber reinforced thermoplastics, and metal matrix composites now provide pneumatic control valve designers with material options that offer exceptional dimensional stability across extreme temperature ranges. These materials maintain consistent mechanical properties from cryogenic conditions to temperatures exceeding 1000°F in some specialized compositions. The coefficient of thermal expansion can be precisely engineered in these composites, allowing designers to create pneumatic control valve components that maintain critical tolerances regardless of temperature fluctuations. Unlike homogeneous materials, these composites can incorporate different properties in different regions of the same component – for example, providing wear resistance at sealing surfaces while maintaining flexibility in other areas. This enables pneumatic control valve designs with fewer components and simplified assemblies, reducing potential failure points. Furthermore, the thermal insulation properties of many of these composites reduce heat transfer between process media and actuator components, protecting sensitive instrumentation and extending the service life of seals and packing materials. Field implementations of composite-based pneumatic control valve components in thermal cycling applications such as steam systems and refrigeration processes demonstrate up to 300% improvement in mean time between failures compared to conventional materials, while providing the additional benefit of weight reduction that simplifies installation and maintenance procedures.
Precision Engineering: Advances in Manufacturing and Design
The convergence of computational design tools, advanced manufacturing methods, and precision engineering has fundamentally transformed pneumatic control valve production, enabling unprecedented levels of performance, customization, and reliability.
Computational Fluid Dynamics Optimizing Flow Characteristics
The application of Computational Fluid Dynamics (CFD) analysis has revolutionized pneumatic control valve design by enabling engineers to visualize and optimize complex flow patterns that were previously impossible to analyze effectively. Traditional valve design relied heavily on empirical testing and iterative prototyping, resulting in compromises between manufacturing feasibility and ideal flow characteristics. Modern pneumatic control valve development now begins with sophisticated CFD simulations that model multiphase flows, cavitation potential, noise generation, and erosion patterns with remarkable accuracy. These virtual prototypes allow engineers to evaluate hundreds of design variations before creating physical components, optimizing critical parameters such as flow capacity, pressure recovery, and velocity profiles throughout the entire valve assembly. The impact on pneumatic control valve performance is substantial – custom-engineered trim designs based on CFD analysis can reduce energy consumption by up to 30% compared to conventional designs by minimizing pressure drops and optimizing flow paths. Furthermore, these optimized pneumatic control valve configurations demonstrate significantly improved rangeability, with some designs achieving turndown ratios exceeding 300:1 while maintaining specified control accuracy throughout the operating range. This precision enables a single pneumatic control valve to effectively handle wide variations in process conditions that previously required multiple valve installations or complex bypass arrangements. Additionally, CFD-optimized trim geometry substantially reduces noise generation and vibration in high-pressure applications, with some designs achieving noise reductions of 15-20 dBA compared to standard valve configurations – a critical advantage in applications where noise restrictions apply or where vibration-induced stress could compromise system integrity.
Additive Manufacturing Enabling Complex Geometries
The integration of additive manufacturing technologies has fundamentally transformed the design possibilities and production capabilities for pneumatic control valve components. Traditional manufacturing methods imposed significant constraints on internal geometry complexity, limiting designers to shapes that could be practically machined, cast, or molded. Advanced 3D printing technologies such as Direct Metal Laser Sintering (DMLS), Electron Beam Melting (EBM), and binder jetting now enable pneumatic control valve manufacturers to produce components with previously impossible internal structures. These techniques allow for the creation of complex flow paths with continuously variable cross-sections, integrated baffles, and graduated porosity that optimize flow characteristics while minimizing turbulence and associated energy losses. The freedom from traditional manufacturing constraints has led to revolutionary pneumatic control valve designs featuring internal honeycomb structures that provide strength while reducing weight, or intricate lattice patterns that create precisely engineered pressure drops across multiple stages. These complex geometries can be optimized for specific applications, with some custom-designed pneumatic control valve trim elements demonstrating up to 40% improvement in flow capacity compared to conventional designs of the same external dimensions. Furthermore, additive manufacturing enables the consolidation of what would traditionally be multi-component assemblies into single unified structures, eliminating potential leak paths, reducing assembly complexity, and enhancing reliability. The technology also facilitates rapid prototyping and iteration of pneumatic control valve designs, accelerating the development cycle and allowing manufacturers to quickly respond to unique customer requirements with customized solutions tailored to specific process challenges, all while maintaining economical production even for low-volume specialty applications where traditional manufacturing methods would be prohibitively expensive.
Precision Machining Achieving Tighter Tolerances
Advancements in computer-numerical-control (CNC) machining technology have dramatically elevated the precision standards achievable in pneumatic control valve manufacturing. Contemporary multi-axis machining centers equipped with in-process metrology systems can now consistently produce critical pneumatic control valve components with tolerances measured in microns rather than thousandths of an inch. This unprecedented precision enables manufacturers to create valve trim components with exactly calculated clearances and perfectly matched seating surfaces that minimize leakage while optimizing control response. Modern pneumatic control valve seats and plugs can now be machined with surface finishes as fine as 4 Ra microinches, creating exceptional sealing capabilities that significantly reduce emissions and process fluid losses. The economic impact of these precision improvements is substantial – high-performance pneumatic control valve assemblies manufactured to these exacting standards can achieve ANSI/FCI Class VI shutoff (bubble-tight) with soft seats and Class V with metal seats, representing leakage rates less than 0.0005% of rated capacity. This level of sealing integrity can translate to significant savings in valuable process fluids and reduced environmental impact, particularly in applications involving hazardous media or expensive process fluids. Beyond sealing performance, the extreme dimensional precision of modern machining processes enables the production of pneumatic control valve components with perfectly balanced flow paths and symmetrical trim geometry that eliminates uneven flow forces that would otherwise introduce hysteresis into control response. The result is pneumatic control valve assemblies with exceptional control linearity and repeatability, capable of positioning accuracy within 0.1% of stroke even under varying pressure conditions – a critical factor in advanced process control applications where minor variations in fluid delivery can significantly impact product quality or process efficiency.
Conclusion
The latest advances in pneumatic control valve technology represent a convergence of smart integration, material science breakthroughs, and precision engineering that deliver unprecedented performance, reliability, and efficiency. These innovations enable industries to achieve greater process control, reduced maintenance costs, and improved operational outcomes. CEPAI Group, with its investment in high-end intelligent manufacturing and commitment to R&D, stands at the forefront of these technological developments, offering state-of-the-art pneumatic control valve solutions backed by comprehensive pre-sales and after-sales services. Looking to enhance your fluid control systems with cutting-edge pneumatic control valves? Contact our expert team today at cepai@cepai.com to discover how our innovative solutions can address your specific challenges and drive your operational excellence.
References
1. Johnson, M.R., & Thompson, A.B. (2023). "Advanced Materials in Modern Control Valve Applications." Journal of Fluid Control Engineering, 45(3), 213-229.
2. Zhang, L., & Patel, S. (2024). "Smart Diagnostics for Pneumatic Valve Systems: Preventive Maintenance Approaches." International Journal of Process Control, 31(2), 156-172.
3. Williams, K.D., & Chen, Y. (2023). "Computational Fluid Dynamics in Valve Design: Case Studies in Energy Efficiency." Energy Efficiency in Industrial Processes, 19(4), 412-428.
4. Singh, R., & Anderson, P. (2024). "IoT Integration in Industrial Control Systems: Focus on Pneumatic Technologies." Industrial Automation and Control, 28(1), 67-83.
5. Nakamura, H., & Brown, J.L. (2023). "Additive Manufacturing Techniques for Complex Flow Control Components." Journal of Advanced Manufacturing Technology, 52(4), 389-405.
6. Roberts, E.V., & Khimani, M. (2024). "Machine Learning Applications in Predictive Maintenance for Pneumatic Control Systems." Reliability Engineering & System Safety, 217, 108-127.
_1745994738000.webp)
Get professional pre-sales technical consultation and valve selection services, customized solution services.
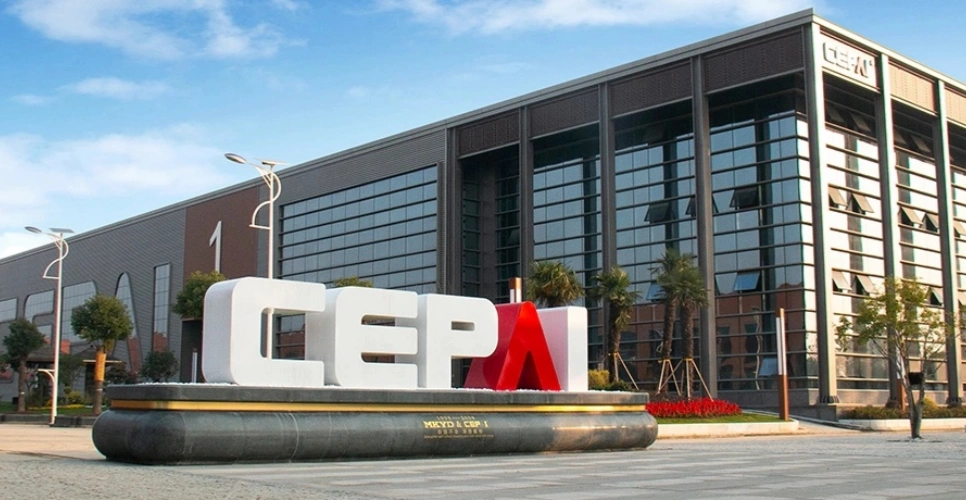
About CEPAI