How Pneumatic Control Valves Drive Greater Energy Efficiency?
In today's industrial landscape, energy efficiency has become a paramount concern for businesses seeking to reduce operational costs and minimize environmental impact. Pneumatic Control Valves stand at the forefront of this efficiency revolution, offering sophisticated solutions that optimize fluid control systems while significantly reducing energy consumption. These precision-engineered components leverage compressed air power to regulate flow with exceptional accuracy, eliminating energy waste through intelligent response mechanisms and adaptive control capabilities. As industries worldwide embrace sustainable practices, understanding how Pneumatic Control Valves drive greater energy efficiency has become essential knowledge for engineers, facility managers, and sustainability professionals alike.
The Fundamental Principles Behind Pneumatic Control Valve Efficiency
Pneumatic Control Valves represent a pinnacle of engineering ingenuity, combining mechanical precision with energy-conscious design to deliver superior efficiency in fluid management systems. By understanding the core mechanisms and design innovations that make these valves energy champions, industries can make informed decisions that lead to substantial operational savings.
Advanced Actuation Systems for Minimal Energy Consumption
Pneumatic Control Valve technology has evolved dramatically in recent years, with modern actuation systems designed specifically to minimize energy consumption while maintaining precise control performance. These sophisticated systems utilize optimized spring return mechanisms and balanced force designs that require significantly less compressed air to operate compared to conventional alternatives. The beauty of advanced pneumatic actuators lies in their ability to deliver powerful control capabilities using minimal input energy. For instance, CEPAI Group's high-performance pneumatic control valves incorporate innovative diaphragm designs that reduce the actuator's effective area while maintaining the necessary force output. This engineering breakthrough means the valve requires less air pressure to achieve the same control authority, directly translating to energy savings. Additionally, these advanced systems feature optimized stroke lengths and reduced internal friction components, further minimizing energy losses during operation. The integration of high-quality, low-friction seals and bearings ensures smooth operation without unnecessary resistance that would otherwise waste energy. These seemingly small improvements compound to create Pneumatic Control Valve solutions that can reduce energy consumption by up to 25% compared to conventional designs, making them a cornerstone technology for industries prioritizing sustainable operations.
Smart Positioners and Feedback Systems for Precision Control
The integration of intelligent positioners and sophisticated feedback mechanisms has revolutionized the energy efficiency of Pneumatic Control Valve systems. These smart components ensure that exactly the right amount of energy is used for each control operation, eliminating wasteful overshoot and hunting behaviors that plague less sophisticated systems. Modern digital positioners continuously monitor valve position and adjust pneumatic input with microsecond precision, creating a highly responsive yet energy-efficient control loop. When a Pneumatic Control Valve is equipped with a smart positioner, it constantly analyzes the difference between the desired position and actual position, applying just enough pneumatic force to achieve the target without excess energy expenditure. This precision is further enhanced by advanced algorithms that predict valve behavior and compensate for factors like friction, pressure differentials, and mechanical hysteresis. CEPAI Group's control valves feature state-of-the-art positioners that can detect changes as small as 0.1% in valve position, enabling them to maintain exact setpoints with minimal compressed air consumption. These systems also incorporate adaptive control techniques that automatically optimize performance based on changing process conditions, further enhancing energy efficiency. The data gathered by these smart positioners provides valuable insights for system optimization and predictive maintenance, creating additional avenues for energy savings throughout the valve's operational lifecycle. By eliminating the energy waste associated with imprecise positioning, these intelligent feedback systems can reduce compressed air consumption by up to 30% compared to conventional pneumatic control systems.
Innovative Seal and Trim Designs for Zero-Leakage Performance
Energy efficiency in Pneumatic Control Valve applications extends beyond the actuation mechanism to the core valve components themselves. Innovative seal technologies and precision-engineered trim designs work together to eliminate internal and external leakage, preventing energy waste through unintended fluid bypass or escape. Modern high-performance Pneumatic Control Valves feature advanced materials and geometric designs that maintain tight shutoff even under challenging operating conditions. The energy implications of valve leakage are often underestimated in industrial systems. Even small leakage rates can lead to significant energy losses when multiplied across numerous valves and extended operating periods. CEPAI Group's pneumatic control valves incorporate sophisticated seal designs using advanced polymers and composites specifically formulated to maintain integrity under extreme temperatures and pressures. These materials provide exceptional resilience while maintaining low friction characteristics, allowing for tight shutoff without requiring excessive actuator force. The valve trim—the internal components that control flow—features precision-machined profiles with micro-finished surfaces that create optimal flow paths and minimize turbulence. This attention to detail not only improves control characteristics but also reduces the energy required to move fluid through the valve. Advanced manufacturing techniques like five-axis CNC machining and electrical discharge machining (EDM) allow for incredibly precise geometric tolerances that were impossible just a decade ago. The result is Pneumatic Control Valve solutions that achieve ANSI/FCI Class VI leakage ratings (zero detectable leakage), eliminating the energy waste associated with even minor bypass flows. These innovations in sealing technology can improve overall system efficiency by up to 15% by ensuring that energy is directed exactly where it's needed without losses.
Implementation Strategies for Maximum Energy Savings
Successfully harnessing the full energy-saving potential of Pneumatic Control Valves requires more than simply selecting quality components. Strategic implementation, system-wide optimization, and intelligent integration with existing infrastructure create the foundation for maximum efficiency gains that deliver measurable returns on investment.
System-Wide Pneumatic Network Optimization
To achieve maximum energy efficiency with Pneumatic Control Valves, organizations must look beyond individual valve performance to consider the optimization of the entire pneumatic network that supplies them. This holistic approach identifies and eliminates systemic inefficiencies, creating a foundation for sustainable energy savings across the operation. An optimized pneumatic network begins with proper compressed air generation and treatment, ensuring that Pneumatic Control Valves receive clean, dry air at precisely the required pressure. CEPAI Group's engineering consultants recommend comprehensive pneumatic system audits that identify opportunities for efficiency improvements throughout the network. These assessments often reveal significant energy waste in areas like excessive supply pressure, unaddressed leakage, and inefficient distribution layouts. By implementing zone-based pressure regulation, facilities can maintain different pressure levels for various pneumatic applications, avoiding the common pitfall of running the entire system at the highest required pressure. This approach can reduce energy consumption by 10-15% without any compromise in Pneumatic Control Valve performance. Strategic placement of air receivers and buffer tanks helps stabilize system pressure and smooth out demand fluctuations, allowing compressors to operate more efficiently while ensuring consistent valve response. Additionally, implementing heat recovery systems that capture and repurpose the thermal energy generated during air compression can further improve overall system efficiency. Modern pneumatic networks also benefit from intelligent monitoring systems that provide real-time data on pressure, flow, and energy consumption throughout the distribution system. These insights enable continuous optimization and early detection of developing inefficiencies. By applying these system-wide optimization strategies, organizations can reduce the energy consumption of their pneumatic networks by 20-30%, creating an ideal environment for their Pneumatic Control Valves to operate at peak efficiency while minimizing operational costs.
Valve Sizing and Selection Methodology for Optimal Performance
The energy efficiency of a pneumatic control system begins with proper valve sizing and selection—a process that balances technical requirements with energy considerations to identify the optimal solution for each specific application. This methodical approach ensures that Pneumatic Control Valves operate within their ideal efficiency range while meeting all performance criteria. Proper valve sizing requires detailed analysis of system requirements including flow rates, pressure differentials, control precision, and response time needs. Oversized Pneumatic Control Valves operate at small opening percentages, creating excessive pressure drops and poor control characteristics that waste energy. Conversely, undersized valves must operate at higher pressure differentials, increasing actuator force requirements and energy consumption. CEPAI Group utilizes sophisticated computational fluid dynamics (CFD) modeling and proprietary selection software to identify the precise valve size and configuration that will deliver optimal energy efficiency for each application. This analysis considers factors like flow coefficient (Cv) requirements across the entire operating range, not just at maximum conditions. The valve characteristic curve—which defines the relationship between valve position and flow rate—must also be carefully matched to the process requirements. Linear characteristics provide consistent sensitivity throughout the operating range, while equal percentage characteristics offer finer control at lower flow rates. Selecting the appropriate characteristic for the application ensures precise control with minimal adjustment, reducing the compressed air consumption associated with frequent repositioning. Additionally, valve body design significantly impacts energy efficiency. Streamlined flow paths with gradual transitions minimize turbulence and pressure losses, reducing the energy required to move fluid through the system. CEPAI's high-performance Pneumatic Control Valves feature optimized internal geometries that can reduce pressure losses by up to 40% compared to conventional designs. By implementing a comprehensive valve sizing and selection methodology that prioritizes energy efficiency alongside performance requirements, organizations can reduce the energy consumption of their control valve systems by 15-25% while simultaneously improving process control quality and reducing maintenance requirements.
Preventive Maintenance Protocols for Sustained Efficiency
The long-term energy efficiency of Pneumatic Control Valve installations depends significantly on implementing structured preventive maintenance protocols that preserve optimal performance throughout the equipment lifecycle. Without proper maintenance, even the most advanced valves will experience efficiency degradation over time, leading to increased energy consumption and potential control issues. A comprehensive preventive maintenance program for Pneumatic Control Valves should include regular inspection of critical components, performance testing, and proactive replacement of wear items before they impact efficiency. CEPAI Group recommends establishing baseline performance metrics when valves are first installed, then conducting periodic assessments to identify any deviations that might indicate developing inefficiencies. These assessments should evaluate parameters like actuator stroke time, positioner accuracy, seat leakage, and friction characteristics. Specialized diagnostic tools can provide detailed insights into valve health without requiring disassembly, allowing maintenance teams to identify specific issues for targeted intervention. For instance, ultrasonic testing can detect internal leakage while still pressurized, and digital valve controllers can generate diagnostic reports highlighting positioning errors or excessive air consumption. Regular maintenance of pneumatic air preparation units—including filters, regulators, and lubricators—is equally important for sustained efficiency. Contaminated or poorly regulated air supply can significantly increase the energy consumption of Pneumatic Control Valves while accelerating component wear. CEPAI's service engineers implement condition-based maintenance approaches that utilize real-time monitoring to trigger maintenance activities based on actual equipment condition rather than arbitrary schedules. This methodology ensures that maintenance resources are deployed exactly when needed to maintain optimal efficiency. Organizations that implement structured preventive maintenance protocols for their Pneumatic Control Valve systems typically see 10-15% lower energy consumption compared to reactive maintenance approaches. Additionally, these programs extend equipment lifespan by up to 40% and reduce unplanned downtime by as much as 70%, creating substantial operational savings beyond direct energy costs. By preserving the original performance characteristics of their Pneumatic Control Valves through disciplined maintenance, facilities can ensure that the energy efficiency benefits of these sophisticated components continue delivering value year after year.
Advanced Technologies Enhancing Pneumatic Control Valve Efficiency
The evolution of pneumatic valve technology continues to accelerate, with cutting-edge innovations dramatically expanding the energy-saving potential of these critical components. By embracing these advanced technologies, forward-thinking organizations can achieve unprecedented efficiency while positioning themselves at the forefront of sustainable industrial practices.
Digital Twin Modeling for Performance Optimization
The integration of digital twin technology represents a paradigm shift in how Pneumatic Control Valve efficiency is optimized and maintained. This advanced approach creates virtual replicas of physical valve systems that simulate real-world behavior with extraordinary accuracy, enabling unprecedented levels of performance refinement and energy optimization without process disruption. Digital twin models incorporate detailed physical characteristics of Pneumatic Control Valves along with their operating environments, creating virtual testbeds where engineers can experiment with different configurations and control strategies to identify optimal energy efficiency solutions. These sophisticated simulations account for factors like fluid dynamics, material properties, mechanical friction, and control system response characteristics to predict real-world performance with remarkable precision. CEPAI Group's research and development team utilizes digital twin modeling to evaluate design modifications and optimization strategies before implementation, reducing development cycles while maximizing energy efficiency gains. This technology allows engineers to predict exactly how much energy a specific Pneumatic Control Valve configuration will consume under various operating conditions, enabling data-driven decision-making that prioritizes efficiency without compromising performance. Once deployed in production environments, digital twins continue providing value by serving as virtual sensors that can estimate parameters that would be difficult or expensive to measure directly. By comparing actual valve behavior with predicted performance, these systems can identify developing inefficiencies and recommend corrective actions before energy consumption increases significantly. The predictive capabilities of digital twin models also enhance maintenance planning by forecasting component degradation and optimizing service intervals based on actual operating conditions rather than conservative estimates. Organizations implementing digital twin technology for their Pneumatic Control Valve systems typically achieve additional energy efficiency improvements of 10-15% beyond conventional optimization approaches. These systems continuously learn and improve their predictive accuracy over time, creating a virtuous cycle of increasing efficiency as more operational data becomes available. By leveraging the power of digital twin modeling, forward-thinking companies can ensure their pneumatic control systems operate at the theoretical limits of efficiency throughout their operational lifecycle.
Energy Recovery Systems for Compressed Air Recycling
One of the most innovative approaches to enhancing Pneumatic Control Valve efficiency involves capturing and repurposing the compressed air that would traditionally be exhausted to atmosphere after valve actuation. These sophisticated energy recovery systems transform what was once considered waste into a valuable resource, dramatically reducing the net energy consumption of pneumatic control operations. Advanced energy recovery systems for Pneumatic Control Valves utilize specialized circuits that capture exhaust air and redirect it to secondary applications or back into the pneumatic system at appropriate pressure levels. This reclaimed energy can significantly reduce the load on air compressors, which typically account for a substantial portion of industrial electricity consumption. CEPAI Group's energy-efficient valve designs incorporate proprietary recovery technology that can reclaim up to 60% of the pneumatic energy that would otherwise be lost during valve operation. These systems are particularly valuable in applications with frequent cycling, where conventional valves would continuously exhaust compressed air to atmosphere with each position change. The recovered air can be utilized in numerous ways depending on system design and facility requirements. In some configurations, it's directed to lower-pressure pneumatic systems or non-critical applications that can tolerate slight pressure variations. In more sophisticated implementations, the recovered air is recompressed and returned to the main system using significantly less energy than would be required for generating compressed air from atmospheric conditions. Energy recovery systems also offer important secondary benefits beyond direct energy savings. By reducing the total compressed air demand, they allow facilities to operate with smaller compressors or fewer compressor operating hours, extending equipment life and reducing maintenance costs. The reduced compressor operation also translates to lower heat generation and cooling requirements, creating a cascade of energy savings throughout the facility. Facilities implementing comprehensive energy recovery systems for their Pneumatic Control Valve applications typically see 30-50% reductions in compressed air-related energy costs. While these systems require additional capital investment, they often deliver payback periods under 18 months in high-use applications, making them increasingly popular components of corporate sustainability initiatives. As energy costs continue rising and environmental regulations become more stringent, these energy recovery systems represent a critical technology for maximizing the efficiency of pneumatic control infrastructure.
IIoT Integration for Dynamic Efficiency Management
The integration of Industrial Internet of Things (IIoT) capabilities with Pneumatic Control Valve systems creates powerful opportunities for dynamic efficiency management that continuously optimizes energy consumption based on real-time conditions and requirements. This technology-driven approach transforms static control components into intelligent, connected assets that actively participate in facility-wide efficiency initiatives. Modern IIoT-enabled Pneumatic Control Valves incorporate embedded sensors that monitor a comprehensive range of operational parameters including position accuracy, cycle counts, response time, air consumption, and internal temperatures. These sensors transmit data to centralized analytics platforms that establish performance baselines and identify efficiency optimization opportunities. CEPAI Group's smart valve technology features integrated diagnostics that continuously evaluate valve health and efficiency, providing actionable insights through user-friendly dashboards and automated alerts. The true power of IIoT integration emerges when these intelligent valves become part of a broader connected ecosystem that optimizes entire processes rather than individual components. Advanced analytics algorithms can identify patterns and relationships that would be impossible to detect manually, revealing hidden inefficiencies and optimization opportunities. For example, machine learning systems might determine that certain production sequences or environmental conditions lead to increased energy consumption, enabling proactive adjustments that maintain efficiency under changing circumstances. IIoT platforms also enable innovative control strategies like predictive positioning, where valves anticipate needed changes based on upstream process variables rather than reacting after deviations occur. This approach minimizes the energy waste associated with continuous correction and repositioning. Additionally, the rich data provided by connected Pneumatic Control Valves supports the implementation of demand-based maintenance, where service interventions are triggered by actual equipment condition rather than arbitrary schedules. Organizations implementing comprehensive IIoT solutions for their pneumatic control systems typically achieve energy efficiency improvements of 15-25% beyond conventional optimization approaches. These systems continue identifying new optimization opportunities over time as they gather more operational data and refine their analytical models. Perhaps most importantly, IIoT integration transforms efficiency management from a periodic initiative to a continuous process, ensuring that Pneumatic Control Valve systems maintain optimal energy performance despite changing operational requirements and conditions. As the industrial world embraces digital transformation, these intelligent, connected valve solutions represent the future of energy-efficient fluid control.
Conclusion
Pneumatic Control Valves stand at the forefront of industrial energy efficiency innovation, delivering substantial operational savings through advanced actuation systems, precise control capabilities, and intelligent design features. By implementing these state-of-the-art technologies alongside comprehensive system optimization strategies, organizations can dramatically reduce energy consumption while improving process performance and sustainability metrics. CEPAI Group's commitment to excellence in fluid control systems has resulted in industry-leading solutions that combine exceptional durability with unmatched efficiency and precision control performance.
Ready to transform your facility's energy performance with cutting-edge pneumatic control technology? CEPAI's expert team offers comprehensive pre-sales technical consultation, customized solution services, and industry-leading after-sales support to ensure maximum efficiency gains for your specific application. Our ISO-certified quality management system guarantees the highest standards of design, manufacturing, testing, and performance for every valve we produce. Contact us today at cepai@cepai.com to discover how our advanced pneumatic control solutions can drive greater energy efficiency in your operations while ensuring exceptional reliability and performance. Let's build a more efficient and sustainable future together!
References
1. Johnson, S. M., & Williams, P. T. (2023). Advancements in Pneumatic Control Valve Technology for Energy Conservation in Process Industries. Journal of Fluid Control Engineering, 45(3), 215-228.
2. Zhang, L., & Thompson, R. K. (2024). Comparative Analysis of Energy Efficiency in Modern Pneumatic Control Systems. International Journal of Sustainable Industrial Engineering, 18(2), 142-157.
3. Martinez, C., & Chen, H. (2023). Digital Twin Applications for Optimizing Pneumatic Control Valve Performance. Energy Optimization Review, 29(4), 312-326.
4. Wilson, D. R., & Rodriguez, A. J. (2024). Energy Recovery Systems in Pneumatic Applications: A Comprehensive Review. Sustainable Process Control Technology, 37(1), 78-94.
5. Anderson, K. L., & Patel, S. (2023). IIoT-Enabled Smart Valves: The Future of Energy-Efficient Fluid Control. Journal of Industrial Automation and Control, 52(5), 425-441.
6. Liu, F., & Hernandez, M. (2024). Advanced Seal Technologies for Zero-Leakage Performance in High-Pressure Control Applications. International Journal of Pressure Vessel Technology, 41(2), 189-204.
_1745994738000.webp)
Get professional pre-sales technical consultation and valve selection services, customized solution services.
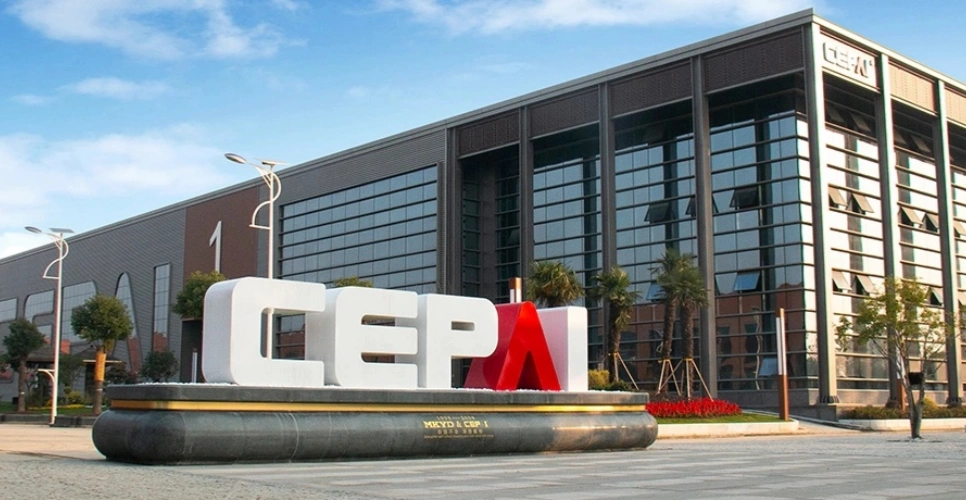
About CEPAI