Essential Standards and Certifications for Pneumatic Control Valves
In today's demanding industrial environments, pneumatic control valves serve as critical components that regulate fluid flow with precision and reliability. To ensure these valves meet stringent safety, performance, and quality requirements, adherence to international standards and certifications is non-negotiable. The complex nature of pneumatic control valve applications—spanning petrochemical, power generation, metallurgy, and water treatment industries—necessitates comprehensive certification frameworks that validate their functionality, durability, and safety protocols under various operating conditions.
Global Standards Governing Pneumatic Control Valve Manufacturing
The manufacturing of high-quality pneumatic control valves is governed by stringent international standards that ensure reliability, safety, and performance across diverse industrial applications.
ISO 9001 Quality Management System
The ISO 9001 certification stands as the fundamental quality management standard that pneumatic control valve manufacturers must implement to ensure consistent product quality. This certification verifies that a company has established systematic quality management processes throughout its operations. For pneumatic control valve production, ISO 9001 certification ensures that every manufacturing step—from design conception to final testing—adheres to documented procedures that guarantee consistent quality. This standard requires manufacturers to implement effective quality control checkpoints, maintain comprehensive documentation, conduct regular internal audits, and pursue continuous improvement initiatives. Companies like CEPAI Group that have obtained ISO 9001 certification demonstrate their commitment to meeting customer expectations by delivering pneumatic control valves that consistently perform according to specifications. The certification also ensures traceability throughout the production process, allowing for quick identification and resolution of any quality issues that might arise during manufacturing or after installation of pneumatic control valves.
API Standards Compliance
API (American Petroleum Institute) standards play a pivotal role in the oil and gas industry, where pneumatic control valves face some of their most demanding applications. API 6D specifically addresses pipeline valves, establishing rigorous requirements for design, manufacturing, testing, and documentation. For manufacturers of pneumatic control valves intended for pipeline service, compliance with API 6D ensures their products can withstand the high pressures and challenging environmental conditions typical in oil and gas transmission. Similarly, API 6A certification is crucial for pneumatic control valves used in wellhead applications, where they must function reliably under extreme pressure and temperature conditions. The API 16C standard focuses on choke and kill equipment, including pneumatic control valves used in these critical safety systems. Manufacturers must subject their pneumatic control valves to extensive pressure testing, material verification, and functional evaluations to achieve these certifications. These standards require stringent quality control measures, including detailed material traceability, comprehensive testing protocols, and thorough documentation, ensuring that pneumatic control valves certified to API standards deliver exceptional reliability in high-stakes applications where failure is not an option.
European Pressure Equipment Directive (PED)
The European Pressure Equipment Directive (PED) establishes essential safety requirements for pressure equipment and assemblies, including pneumatic control valves, with operating pressures exceeding 0.5 bar. Compliance with PED is mandatory for pneumatic control valve manufacturers seeking to sell their products in the European Economic Area. The directive categorizes equipment based on potential hazard levels, determining the appropriate conformity assessment procedures. For pneumatic control valves, this often includes design examination, type approval, and production quality assurance verification. The CE marking on a pneumatic control valve signifies that it meets all applicable PED requirements, confirming its safety for use in pressure applications within the European market. This certification process involves rigorous testing and documentation, including pressure testing, material certification, and risk assessments. The comprehensive nature of PED certification ensures that pneumatic control valves meet the highest safety standards, providing customers with confidence in their reliability and durability when used in critical pressure applications across various industrial sectors, from chemical processing to power generation.
Safety Integrity Level (SIL) Certifications for Pneumatic Control Valves
Safety Integrity Level certifications represent a critical framework for evaluating the reliability of pneumatic control valves in safety-critical applications, providing quantitative measures of risk reduction capabilities.
Understanding SIL Classification Systems
Safety Integrity Level (SIL) classifications provide a systematic framework for assessing and verifying the reliability of pneumatic control valves in safety-critical applications. The SIL system, defined by international standards IEC 61508 and IEC 61511, categorizes safety instrumented systems into four levels (SIL 1 to SIL 4), with higher numbers indicating greater risk reduction capabilities. For pneumatic control valves, SIL certification quantifies their probability of failure on demand (PFD) and safe failure fraction (SFF), critical metrics that determine their suitability for various safety functions. This classification system enables engineers to select the appropriate pneumatic control valve for specific risk mitigation requirements. The certification process involves rigorous failure mode and effects analysis (FMEA), reliability calculations, and testing under simulated fault conditions. Manufacturers must demonstrate that their pneumatic control valves can perform their safety functions consistently throughout their operational lifecycle, with documented evidence of design verification, validation testing, and production quality control measures. By understanding SIL classifications, system designers can properly match pneumatic control valve capabilities to application safety requirements, ensuring that critical processes remain protected against potential hazards without overengineering solutions.
SIL Certification Process for Valve Manufacturers
The SIL certification process for pneumatic control valve manufacturers requires extensive documentation, testing, and third-party verification to validate safety performance claims. Initially, manufacturers must conduct a comprehensive failure modes, effects, and diagnostic analysis (FMEDA) that identifies all potential failure modes of their pneumatic control valves and calculates key reliability parameters. This analysis examines component reliability data, potential failure mechanisms, and diagnostic coverage capabilities. The manufacturer must then implement design features that enhance the pneumatic control valve's safety integrity, such as redundant components, self-diagnostic capabilities, and fail-safe mechanisms. Throughout the development process, extensive testing validates the pneumatic control valve's reliability claims, including accelerated life testing, environmental stress screening, and fault injection testing. An accredited certification body then performs a rigorous assessment of the design documentation, manufacturing processes, and test results to verify compliance with IEC 61508 requirements. This independent validation ensures that pneumatic control valves meet the claimed SIL level and can be trusted in safety-critical applications. CEPAI Group's achievement of SIL certification for their control valves, ball valves, and butterfly valves demonstrates their commitment to providing pneumatic control valves with verified safety performance, giving customers confidence in their reliability when used in safety instrumented systems.
SIL Implementation in Industrial Applications
The implementation of SIL-certified pneumatic control valves in industrial applications provides significant safety and operational benefits across various sectors. In petrochemical facilities, SIL-certified pneumatic control valves serve as critical components in emergency shutdown systems, where their verified reliability ensures proper process isolation during hazardous conditions. Power generation plants utilize these valves in boiler protection systems and turbine trip mechanisms, where their predictable failure modes and documented reliability contribute to overall plant safety. Process industries implement SIL-certified pneumatic control valves in overpressure protection systems, ensuring reliable pressure relief when needed. The integration of these valves into safety instrumented systems requires careful consideration of numerous factors, including valve response time, actuator sizing, and compatible control systems. Proper implementation involves detailed engineering analysis, including safety requirement specifications, cause and effect matrices, and proof test procedures. Regular proof testing of pneumatic control valves verifies their continued ability to perform their safety functions as designed, with test intervals determined by SIL requirements and reliability calculations. By implementing SIL-certified pneumatic control valves, facilities can demonstrate regulatory compliance, reduce insurance costs, and most importantly, protect personnel, equipment, and the environment from potential process hazards. CEPAI Group's comprehensive range of SIL-certified pneumatic control valves enables customers to implement robust safety systems tailored to their specific application requirements.
Material and Testing Standards for Quality Assurance
Ensuring the quality and reliability of pneumatic control valves requires adherence to rigorous material selection criteria and comprehensive testing protocols throughout the manufacturing process.
Material Selection and Certification Requirements
The performance and longevity of pneumatic control valves heavily depend on appropriate material selection based on specific application requirements. International standards such as ASTM, ASME, and EN establish clear guidelines for material properties, composition, and testing methodologies. For pneumatic control valve body and trim components, manufacturers must obtain certified material test reports (CMTRs) that verify chemical composition, mechanical properties, and heat treatment processes. These certifications ensure material traceability from the foundry to the final product, a critical requirement for applications in nuclear, petrochemical, and other high-hazard industries. Material selection for pneumatic control valves must consider various factors, including pressure ratings, temperature extremes, corrosive media compatibility, and erosion resistance. In critical applications, supplementary requirements may include positive material identification (PMI), non-destructive examination (NDE), and special heat treatment certifications. Materials commonly used in pneumatic control valve construction include various grades of stainless steel, carbon steel, alloy steels, and specialty alloys like Hastelloy and Monel for extreme environments. The correct material certification ensures that pneumatic control valves will perform reliably throughout their intended service life without premature failure due to corrosion, erosion, or mechanical stress. CEPAI Group's commitment to material quality is evident in their comprehensive material certification program and sophisticated testing capabilities, including their CNAS nationally recognized laboratory that ensures all materials used in their pneumatic control valves meet or exceed industry standards.
Non-Destructive Testing (NDT) Methods
Non-destructive testing (NDT) plays a vital role in verifying the structural integrity of pneumatic control valves without compromising their functionality. Various NDT methods are employed throughout the manufacturing process to detect potential defects that could lead to valve failure during operation. Radiographic testing (RT) utilizes X-rays or gamma rays to detect internal defects in pneumatic control valve castings, such as porosity, inclusions, or cracks that might compromise pressure-containing capabilities. Ultrasonic testing (UT) employs high-frequency sound waves to identify subsurface flaws in forgings and welds, particularly important for thick-walled pneumatic control valves designed for high-pressure applications. Magnetic particle inspection (MPI) reveals surface and near-surface defects in ferromagnetic materials commonly used in pneumatic control valve components. Liquid penetrant testing (PT) identifies surface defects in non-magnetic materials, ensuring the surface integrity of critical sealing components in pneumatic control valves. Advanced methods like positive material identification (PMI) verify that the correct alloys are used in pneumatic control valve construction, preventing material mix-ups that could lead to premature failure. Each NDT method is governed by specific standards that define acceptance criteria, ensuring consistent quality evaluation across the industry. CEPAI Group's advanced NDT capabilities include all standard methods and specialized techniques optimized for pneumatic control valve inspection, with certified technicians performing these tests in accordance with international standards like ASME B16.34 and API 598. The comprehensive NDT program ensures that every pneumatic control valve leaving their facility meets the highest quality standards, providing customers with confidence in the integrity of their critical flow control equipment.
Pressure and Performance Testing Standards
Rigorous pressure and performance testing serves as the final validation of pneumatic control valve quality before delivery to customers. International standards establish comprehensive protocols for these tests, ensuring valves perform according to specifications under various operating conditions. Hydrostatic testing, conducted in accordance with standards like API 598 and API 6D, verifies the pressure-containing capability of pneumatic control valve bodies by subjecting them to pressures significantly higher than their rated working pressure. Pneumatic seat leakage testing evaluates the sealing performance of pneumatic control valves, with allowable leakage rates specified by standards like ANSI/FCI 70-2 or IEC 60534-4, categorizing valves into different leakage classes based on their sealing capability. Functional testing confirms that pneumatic control valves operate correctly throughout their full stroke range, assessing parameters like opening and closing times, actuator thrust, and control stability. For control applications, flow characteristic testing validates that pneumatic control valves deliver the specified flow behavior (equal percentage, linear, or quick-opening) across their operating range. Environmental qualification testing subjects pneumatic control valves to extreme conditions, including temperature cycling, vibration, and seismic simulation, ensuring reliable operation in challenging industrial environments. These comprehensive testing protocols are documented in detailed test reports that accompany each pneumatic control valve, providing customers with verification of performance capabilities. CEPAI Group's state-of-the-art testing facilities, including their CNAS nationally recognized laboratory, enable them to perform all required tests in-house with exceptional accuracy and thoroughness, ensuring that every pneumatic control valve meets or exceeds the performance expectations of their customers across diverse applications.
Conclusion
The essential standards and certifications for pneumatic control valves represent far more than regulatory compliance—they embody a commitment to excellence in design, manufacturing, and performance reliability. As industries increasingly demand higher safety margins and operational efficiency, partnering with manufacturers like CEPAI Group who have invested in comprehensive certifications becomes a strategic advantage. With exceptional durability, high-precision control performance, and robust R&D capabilities, CEPAI stands ready to meet your pneumatic control valve needs with pre-sales technical consultation, customized solutions, and industry-leading after-sales support. Experience the difference of working with an ISO-certified manufacturer dedicated to zero valve defects. Contact our team today at cepai@cepai.com to discuss how our certified pneumatic control valves can optimize your operations.
References
1. International Organization for Standardization. (2023). ISO 9001:2015 - Quality management systems - Requirements. Geneva, Switzerland: ISO.
2. American Petroleum Institute. (2024). API 6D: Specification for Pipeline and Piping Valves. Washington, DC: API Publishing Services.
3. European Committee for Standardization. (2022). EN 12516: Industrial valves - Shell design strength. Brussels, Belgium: CEN.
4. International Electrotechnical Commission. (2023). IEC 61508: Functional Safety of Electrical/Electronic/Programmable Electronic Safety-related Systems. Geneva, Switzerland: IEC.
5. American Society of Mechanical Engineers. (2023). ASME B16.34: Valves - Flanged, Threaded, and Welding End. New York, NY: ASME.
6. Valve Manufacturers Association. (2024). Control Valve Technical Handbook (5th ed.). Washington, DC: VMA Publications.
_1745994738000.webp)
Get professional pre-sales technical consultation and valve selection services, customized solution services.
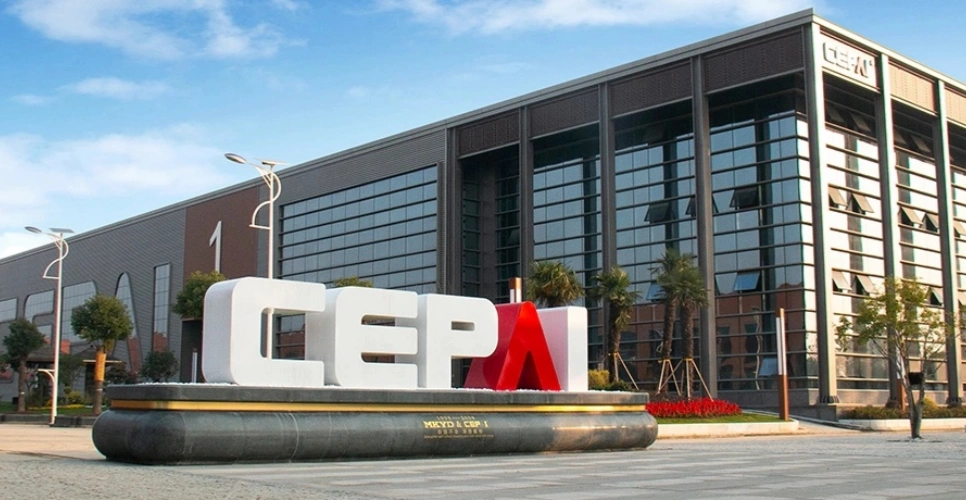
About CEPAI