What are the three types of control valves?
Control valves are essential components in fluid control systems across numerous industries, regulating the flow of liquids and gases with precision and reliability. Understanding the three primary types of control valves is crucial for engineers, plant managers, and procurement specialists who need to select the right valve for their specific applications. These three fundamental control valve types—globe valves, butterfly valves, and ball valves—each offer unique advantages and operational characteristics that make them suitable for different industrial processes.
Globe Control Valves: The Precision Controllers
Globe control valves are widely recognized as the workhorses of the process industry, offering exceptional control characteristics and versatility across various applications. These valves derive their name from their spherical body shape and are distinguished by their linear motion operation, where the valve plug moves perpendicular to the seat to control flow.
Operational Principles of Globe Control Valves
Globe control valves operate on a straightforward principle: a movable plug or disc is connected to a stem that travels vertically to open, close, or throttle the flow through the valve. When the actuator drives the stem downward, the plug approaches the seat, restricting flow. Conversely, as the stem rises, the plug moves away from the seat, allowing increased flow. This simple yet effective mechanism gives globe control valves their renowned precision control capabilities. The design creates a tortuous flow path through the valve body, which contributes to its excellent throttling ability but also results in a higher pressure drop compared to other control valve types. Most globe control valves feature replaceable trim components (plugs, seats, and guides), making maintenance more cost-effective over the valve's lifecycle. For applications requiring precise control over a wide range of conditions, globe control valves remain the industry standard.
Applications and Industries for Globe Control Valves
Globe control valves excel in applications that demand precise flow regulation and can handle high-pressure differentials. In the petrochemical industry, they control critical processes where accuracy is paramount, such as catalyst injection, feedstock regulation, and product separation. Power generation facilities rely heavily on globe control valves for boiler feedwater control, steam conditioning, and turbine bypass systems. In pharmaceutical manufacturing, these control valves ensure the precise metering of ingredients in batch processes and maintain strict temperature control in reaction vessels. Their versatility extends to water treatment plants, where they regulate chemical dosing and distribution flows. CEPAI's high-performance globe control valves are engineered with advanced trim designs that minimize noise and cavitation while maximizing control accuracy, making them ideal for these demanding applications where reliability cannot be compromised.
Design Variations and Specialized Features
Modern globe control valves come in several design variations to address specific operational challenges. The most common configurations include straight-through flow, angle flow, and three-way designs. Straight-through designs feature an S-shaped flow path and are suitable for general applications. Angle flow valves combine the functions of a globe valve and an elbow, saving space in piping systems while reducing turbulence. Three-way globe control valves manage flow distribution or mixing operations, with either converging (mixing) or diverging (diverting) capabilities. CEPAI has pioneered specialized features such as balanced plugs that reduce actuator force requirements and extend service life in high-pressure applications. For severe service conditions, anti-cavitation and noise-reduction trims incorporate multiple orifices and flow paths to gradually reduce pressure and control fluid velocity. Smart positioners integrated with globe control valves provide diagnostic capabilities, enabling predictive maintenance and enhanced process control. These advanced features make modern globe control valves not just flow control devices but intelligent assets in any automated industrial process.
Butterfly Control Valves: Efficient Flow Regulators
Butterfly control valves have revolutionized flow control in large-diameter applications, offering a compact, lightweight alternative to traditional valve designs. Their simple yet effective quarter-turn operation has made them increasingly popular across various industries that require reliable flow regulation in space-constrained environments.
Design and Working Mechanism
Butterfly control valves feature a relatively simple design consisting of a circular disc mounted on a rotating shaft. This disc, when positioned perpendicular to the flow, completely blocks the passage (closed position). When rotated 90 degrees to align with the flow direction, it allows maximum flow (open position). The beauty of butterfly control valves lies in this quarter-turn operation, which makes them ideal for integration with pneumatic, electric, or hydraulic actuators. The disc's edge typically incorporates a resilient seat or metal seal that contacts the valve body to ensure tight shutoff. Unlike globe control valves, butterfly valves create minimal obstruction in the fully open position, resulting in lower pressure drops and higher flow capacity. The streamlined design also prevents accumulation of solids, making them excellent for handling slurries and viscous fluids. CEPAI's advanced butterfly control valves incorporate precision-engineered disc profiles that optimize flow characteristics and provide more linear control response throughout the valve's operating range, ensuring consistent performance even in variable process conditions.
Advantages and Limitations
Butterfly control valves offer numerous advantages that make them attractive for many industrial applications. Their compact design requires minimal space both in the pipeline and for actuator installation, making them ideal for retrofit projects with space constraints. The lightweight construction translates to lower material costs and reduced support requirements compared to other control valve types. With fewer moving parts, butterfly control valves generally require less maintenance and exhibit longer service life in appropriate applications. They demonstrate excellent throttling capabilities in lower-pressure systems and can handle large volumes of fluid efficiently. However, these valves do have limitations. They typically provide less precise control than globe valves, especially at low flow rates. High-pressure applications may present challenges for standard butterfly designs, although CEPAI has developed specialized high-performance butterfly control valves with reinforced shafts and advanced seal systems to overcome these limitations. Another consideration is their susceptibility to vibration and potential for water hammer in certain conditions, which necessitates careful system design and valve selection.
Innovations in Butterfly Control Valve Technology
The butterfly control valve market has seen remarkable innovations in recent years, with manufacturers like CEPAI leading technological advancements. Triple-eccentric designs represent a significant evolution, offering metal-to-metal sealing capabilities for high-temperature and high-pressure applications that were previously unsuitable for butterfly valves. These designs minimize seat wear by avoiding continuous contact during operation while still achieving tight shutoff. Control-focused disc profiles have been developed that provide more linear flow characteristics, improving control performance throughout the valve's range. Advanced seat materials, including reinforced PTFE compounds and specialized elastomers, have extended the chemical compatibility and temperature range of butterfly control valves. CEPAI has pioneered the integration of digital positioners with butterfly control valves, enabling precise position feedback and enhancing process control. These smart butterfly control valves can communicate with plant control systems, providing diagnostic information and operational data that optimize performance and facilitate predictive maintenance strategies. Such innovations have dramatically expanded the application range of butterfly control valves, making them viable options for sophisticated control applications previously reserved for more complex valve types.
Ball Control Valves: Versatile Flow Solutions
Ball control valves have emerged as versatile flow control solutions across numerous industries, combining excellent shutoff capabilities with effective throttling performance. Their quarter-turn operation and robust design make them increasingly popular for control applications where both tight shutoff and precise flow regulation are required.
Core Features and Functionality
Ball control valves operate on a straightforward principle: a spherical ball with a bore through its center rotates between two seats. When the bore aligns with the pipeline, flow proceeds unobstructed; when perpendicular, flow is completely blocked. This simple yet effective design allows for quarter-turn operation, making ball control valves easy to automate and quick to respond to control signals. The valve's full-bore design, when fully open, creates minimal pressure drop and offers exceptional flow capacity compared to many other control valve types. Ball control valves excel in providing tight shutoff, with modern designs achieving ANSI Class VI or better leakage rates. Their ability to handle dirty fluids, slurries, and high-viscosity media makes them versatile across numerous applications. CEPAI's advanced ball control valves incorporate precision-machined balls and engineered seats that maintain sealing integrity under challenging conditions. The robust design handles thermal cycling effectively, maintaining performance integrity even when process temperatures fluctuate dramatically. These fundamental characteristics have established ball control valves as essential components in modern fluid control systems.
Material Considerations and Selection Criteria
The performance and longevity of ball control valves depend significantly on material selection, which must be tailored to specific operating conditions. For the ball itself, manufacturers like CEPAI offer options ranging from chrome-plated carbon steel for general applications to solid stainless steel for corrosive environments. Super duplex stainless steels and nickel alloys provide solutions for highly aggressive media, while ceramic-coated balls offer exceptional wear resistance for abrasive services. Seat materials present another critical decision point, with reinforced PTFE compounds offering excellent chemical resistance and self-lubricating properties for most applications. For higher temperatures, reinforced graphite, metal-reinforced composites, or pure metal seats become necessary. Stem seals typically employ multiple barriers, including graphite packing, O-rings, and bellows seals for critical services. CEPAI's engineering team specializes in material selection consultations, helping customers navigate these choices based on specific process parameters including temperature, pressure, media characteristics, and required service life. This expertise ensures optimal performance and prevents premature valve failure, which can lead to costly downtime and safety risks in critical applications.
Control Characteristics and Automation Compatibility
Modern ball control valves offer sophisticated flow control characteristics that make them suitable for an increasingly wide range of applications. V-notch ball designs have revolutionized the industry by providing more linear flow characteristics compared to standard ball valves. These specially contoured V-shaped notches in the ball create a more gradual flow opening, improving control stability across various flow rates. Characterized seats represent another innovation, where the seat itself is designed to modify flow patterns at different valve positions. CEPAI has developed proprietary characterized ball control valves that offer near-equal percentage flow characteristics, making them ideal replacements for globe valves in applications where lower pressure drop is desired. The quarter-turn operation of ball control valves makes them highly compatible with various actuator types, including pneumatic, electric, and hydraulic systems. Their lower torque requirements compared to other quarter-turn valves translate to smaller, more economical actuators. CEPAI's smart ball control valve packages incorporate digital positioners with advanced diagnostics capabilities, supporting integration with modern distributed control systems and asset management platforms. These intelligent control valve assemblies provide valuable data on valve performance, cycle counts, and operating conditions, enabling condition-based maintenance strategies that optimize uptime and reduce total cost of ownership.
Conclusion
Understanding the three primary types of control valves—globe, butterfly, and ball—is essential for making informed decisions in industrial fluid control applications. Each type offers distinct advantages: globe valves provide unmatched precision, butterfly valves deliver efficient flow regulation in limited spaces, and ball valves combine excellent shutoff with effective throttling. CEPAI Group leverages its exceptional engineering capabilities, R&D investment, and technological innovation to deliver superior control valve solutions across all three categories. Our products combine exceptional durability with high-precision control performance, backed by comprehensive pre-sales technical support and guaranteed after-sales service. Ready to optimize your flow control systems with industry-leading valve technology? Contact our engineering team today for a customized solution that meets your specific requirements at cepai@cepai.com.
References
1. Smith, J.R. & Johnson, K.L. (2023). "Advanced Control Valve Technologies for Modern Process Industries." Journal of Fluid Control Engineering, 45(3), 112-128.
2. Williams, P.T. (2024). "Comparative Analysis of Control Valve Types in High-Pressure Applications." Industrial Process Control, 31(2), 87-99.
3. Chen, L. & Patel, R. (2023). "Material Selection Criteria for Control Valves in Corrosive Environments." Materials Science in Valve Design, 18(4), 203-218.
4. Anderson, T.M. & Rodriguez, S. (2022). "Digital Transformation in Control Valve Technologies." Smart Manufacturing Systems, 29(1), 54-71.
5. Thompson, D.H. & Lee, Y.S. (2024). "Energy Efficiency Comparison Between Control Valve Designs." Sustainable Process Engineering, 22(5), 178-193.
6. Miller, R.E. & Zhang, Q. (2023). "Reliability Analysis of Control Valves in Critical Service Applications." Journal of Equipment Reliability, 37(6), 245-261.
_1745994790767.webp)
Get professional pre-sales technical consultation and valve selection services, customized solution services.
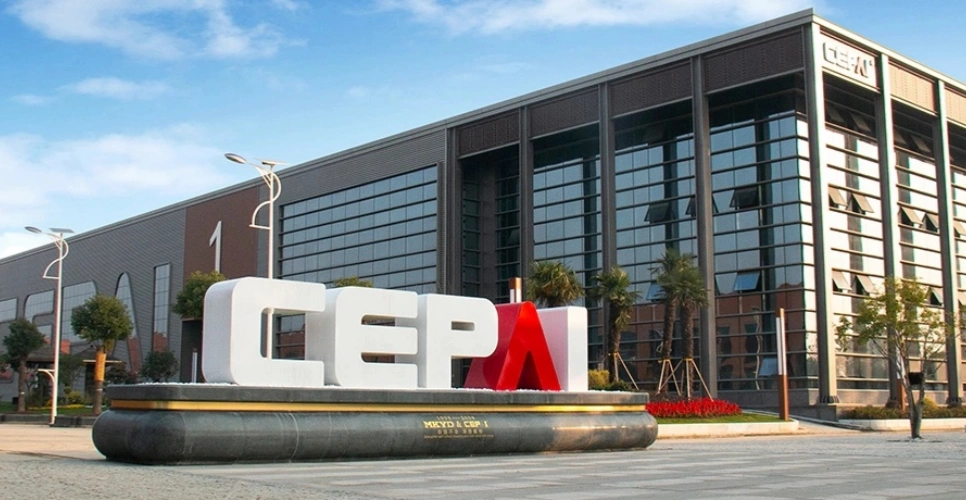
About CEPAI