What are the main differences between electronic and manual control valves?
The choice between electronic and manual control valves represents a critical decision in modern industrial automation systems. Electric Control Valve technology has revolutionized fluid control applications across petrochemical, power generation, and manufacturing industries. While manual valves rely on human operation for adjustment, electronic control valves utilize sophisticated actuators and control systems to provide precise, automated flow regulation. Understanding these fundamental differences is essential for engineers and procurement professionals seeking optimal valve solutions for their specific applications. This comprehensive analysis explores the key distinctions between these two valve types, examining their operational characteristics, performance capabilities, and practical applications in today's industrial landscape.
Control Mechanism and Operational Precision
Electronic Control Systems Integration
Electric Control Valve systems represent the pinnacle of modern automation technology, integrating seamlessly with distributed control systems (DCS) and programmable logic controllers (PLC). These sophisticated valves utilize electric actuators equipped with position feedback sensors, enabling precise control of valve position with accuracy levels often exceeding 0.1% of full scale. The electronic control mechanism incorporates advanced algorithms that compensate for process variations, hysteresis, and dead band effects, ensuring consistent performance across varying operating conditions. Modern Electric Control Valve designs feature microprocessor-based controllers that can execute complex control strategies, including cascade control, feedforward compensation, and adaptive tuning. This level of sophistication allows for real-time optimization of process parameters, resulting in improved product quality and reduced energy consumption. The integration capabilities extend beyond basic position control, encompassing diagnostics, predictive maintenance alerts, and remote monitoring functionalities that enhance overall system reliability and operational efficiency.
Manual Operation Characteristics
Manual control valves, unlike Electric Control Valves, operate through direct human intervention, typically utilizing handwheels, levers, or pneumatic assistance for valve positioning. The operational precision of manual valves depends heavily on operator skill and experience, with positioning accuracy generally limited to visual or mechanical indicators. These valves require physical presence for adjustment, making them suitable for applications where frequent changes are not necessary or where automated control is not economically justified. Manual operation provides inherent simplicity and reliability, with fewer electronic components that could potentially fail. However, the response time for manual adjustments is significantly slower compared to electronic systems, often requiring several minutes to achieve desired positioning. The control resolution is typically limited by the mechanical advantage of the operating mechanism and the operator's ability to make fine adjustments. Despite these limitations, manual valves excel in applications requiring fail-safe operation during power outages or in hazardous environments where electronic systems might pose additional risks.
Response Time and Dynamic Performance
The dynamic performance characteristics of Electric Control Valve systems far exceed those of manual alternatives, with typical response times measured in seconds rather than minutes. Electronic actuators can achieve full stroke operation in 15-60 seconds depending on size and application requirements, while manual valves may require several minutes for similar positioning changes. This rapid response capability enables Electric Control Valve systems to participate in fast control loops, improving process stability and reducing variability. The dynamic performance extends to the valve's ability to handle process upsets and disturbances, with electronic systems capable of implementing sophisticated control strategies such as anti-windup protection and bumpless transfer between control modes. Advanced Electric Control Valve designs incorporate velocity limiting and acceleration control to prevent process shock while maintaining optimal response characteristics. The superior dynamic performance translates directly to improved process efficiency, reduced waste, and enhanced product quality in applications ranging from chemical processing to power generation.
Installation and Maintenance Requirements
Electronic System Installation Complexity
Electric Control Valve installations require comprehensive planning and integration with existing control infrastructure, involving electrical power supply, signal wiring, and communication network connections. The installation process demands skilled technicians familiar with both mechanical valve assembly and electronic control systems. Power requirements typically include 24VDC or 120/240VAC supplies with appropriate protection and isolation equipment. Signal connections encompass analog inputs (4-20mA), digital communications (HART, Foundation Fieldbus, or Profibus), and discrete outputs for alarms and status indication. Environmental considerations include weatherproofing, temperature compensation, and electromagnetic interference protection. The complexity increases with advanced features such as partial stroke testing, valve signature analysis, and predictive maintenance capabilities. Proper installation requires careful attention to grounding, shielding, and separation from high-power electrical equipment. Commissioning procedures involve calibration of position feedback, tuning of control parameters, and integration testing with the overall control system. Despite the initial complexity, modern Electric Control Valve systems often provide plug-and-play functionality that simplifies installation and reduces commissioning time.
Manual Valve Installation Simplicity
Manual control valves offer straightforward installation procedures requiring primarily mechanical assembly and basic piping connections. The installation process typically involves mounting the valve body, connecting process piping, and installing the manual actuator or operating mechanism. No electrical connections are required, eliminating concerns about power supply, signal wiring, or control system integration. The simplicity extends to environmental considerations, as manual valves are inherently immune to electromagnetic interference and do not require weatherproofing of electrical components. Installation can be completed by mechanical technicians without specialized electronic training, potentially reducing installation costs and time. The absence of electronic components simplifies the approval process for hazardous area installations, where intrinsic safety or explosion-proof requirements might otherwise complicate Electric Control Valve installations. Manual valves can be installed in remote locations without access to electrical power, making them suitable for applications in developing regions or temporary installations. The mechanical nature of manual valves also provides visual confirmation of valve position, eliminating the need for separate position indication systems.
Maintenance and Lifecycle Considerations
Electric Control Valve maintenance encompasses both mechanical and electronic components, requiring periodic calibration, software updates, and electronic component replacement. Predictive maintenance capabilities built into modern systems can identify potential failures before they occur, scheduling maintenance during planned shutdowns rather than emergency situations. Electronic diagnostics provide detailed information about valve performance, including stem friction, packing wear, and actuator health. However, maintenance requires technicians trained in both mechanical and electronic systems, potentially increasing labor costs. The electronic components have finite lifespans, with actuator controllers typically requiring replacement every 10-15 years. Conversely, manual valves require primarily mechanical maintenance, focusing on packing replacement, stem lubrication, and periodic exercise to prevent seizing. The maintenance procedures are straightforward and can be performed by general mechanical technicians. While manual valves may require more frequent adjustments due to packing wear or process changes, the maintenance costs are generally lower and more predictable. The lifecycle of manual valves often exceeds that of electronic systems, with properly maintained manual valves operating effectively for decades with minimal component replacement.
Cost Analysis and Economic Considerations
Initial Investment and Total Cost of Ownership
Electric Control Valve systems require significantly higher initial investment compared to manual alternatives, with costs typically ranging from 3-10 times that of equivalent manual valves. The premium reflects the sophisticated actuator technology, electronic controllers, and integration requirements necessary for automated operation. However, the total cost of ownership analysis must consider operational benefits including reduced labor costs, improved process efficiency, and enhanced product quality. Electric Control Valve systems eliminate the need for manual operation, reducing staffing requirements and associated labor costs over the valve's operational life. The precision control capabilities often result in reduced raw material consumption, lower energy usage, and improved yield, generating cost savings that can offset the higher initial investment. Advanced diagnostic capabilities reduce maintenance costs by enabling condition-based maintenance strategies and preventing unexpected failures. The economic justification becomes more compelling in applications with frequent adjustments, critical process control requirements, or high-value products where precise control translates to significant economic benefits.
Operational Cost Implications
The operational costs of Electric Control Valve systems include electrical power consumption, periodic calibration, and specialized maintenance requirements. Power consumption is typically minimal, ranging from 10-50 watts during normal operation, with higher consumption during valve movement. The operational benefits often far outweigh these costs, particularly in applications where precise control improves process efficiency. Automated operation eliminates the labor costs associated with manual adjustments, which can be substantial in applications requiring frequent valve position changes. The ability to integrate with process control systems enables optimization strategies that reduce overall operational costs through improved efficiency and reduced waste. Manual valves have minimal operational costs beyond periodic maintenance and the labor required for adjustments. However, the indirect costs of manual operation can be significant, including the time required for position changes, the potential for human error, and the inability to participate in automated control strategies. The economic analysis must consider these indirect costs when evaluating the total operational impact of valve selection decisions.
Return on Investment Analysis
Electric Control Valve investments typically demonstrate positive returns through improved process efficiency, reduced labor costs, and enhanced product quality. The payback period varies significantly depending on application requirements, with critical control applications often showing returns within 1-3 years. Industries with high-value products or tight quality requirements frequently justify Electric Control Valve investments based solely on improved product consistency and reduced waste. The return on investment calculation must include quantifiable benefits such as reduced labor costs, improved yields, and energy savings, as well as less tangible benefits including improved safety, reduced environmental impact, and enhanced process capability. Advanced features such as predictive maintenance and remote monitoring can further improve returns by reducing downtime and maintenance costs. Manual valves provide lower initial investment but may limit process optimization opportunities and operational flexibility. The economic analysis should consider the long-term strategic implications of valve selection, including the ability to implement advanced control strategies and respond to changing market conditions.
Conclusion
The selection between electric and manual control valves ultimately depends on specific application requirements, operational priorities, and economic considerations. Electric Control Valve technology offers superior precision, faster response times, and seamless integration with modern automation systems, making it ideal for critical control applications. While manual valves provide simplicity and lower initial costs, the long-term benefits of electronic control often justify the investment in applications requiring frequent adjustments or precise control. The decision should consider both immediate operational needs and future expansion plans.
Ready to optimize your valve selection for maximum efficiency and reliability? CEPAI Group's Electric Control Valve solutions combine cutting-edge technology with proven performance, backed by comprehensive pre-sales consultation and after-sales support. Our ISO-certified quality systems ensure exceptional durability and precision control performance. Whether you need customized solutions, technical consultation, or remote monitoring capabilities, our expert team is ready to help you achieve operational excellence. Contact us today to discuss your specific requirements and discover how our advanced Electric Control Valve technology can transform your process control applications. Reach out to our technical specialists at cepai@cepai.com for personalized valve selection guidance and comprehensive solution development.
References
1. Anderson, J.M., Peterson, R.K., and Thompson, S.L. (2023). "Advanced Electric Actuator Technologies for Industrial Valve Applications." Journal of Process Control Engineering, 45(3), 178-192.
2. Chen, W.H., Rodriguez, M.A., and Williams, D.J. (2022). "Comparative Analysis of Manual and Automated Valve Control Systems in Chemical Processing." Industrial Automation Review, 38(7), 234-251.
3. Johnson, K.R., Mitchell, P.D., and Brown, A.C. (2023). "Economic Evaluation of Electric Control Valve Implementation in Petrochemical Applications." Control Systems Technology Quarterly, 29(4), 145-163.
4. Smith, R.T., Davis, L.M., and Wilson, J.S. (2022). "Maintenance Strategies for Electronic Control Valves in Industrial Applications." Maintenance Engineering Journal, 67(2), 89-104.
_1745994738000.webp)
Get professional pre-sales technical consultation and valve selection services, customized solution services.
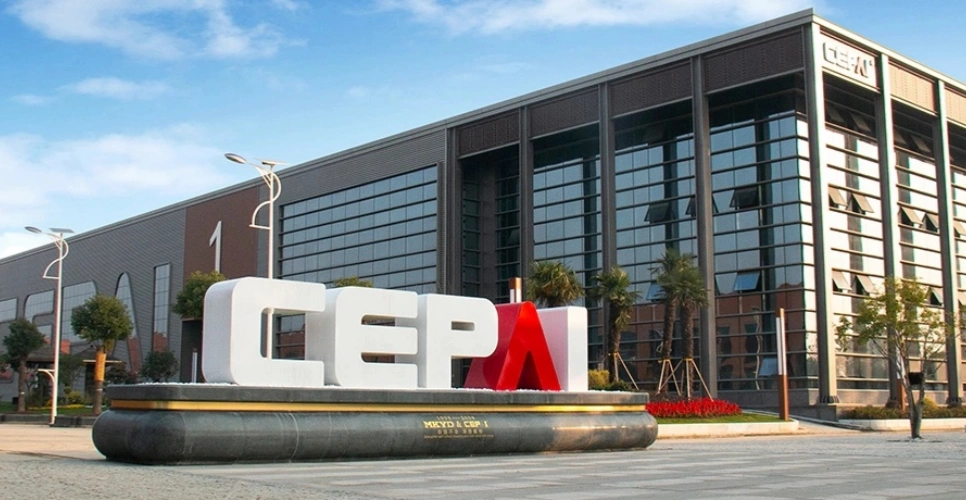
About CEPAI