Smart Valve Solutions Leading the Way in 2025
As we advance into 2025, the industrial automation landscape continues to evolve at an unprecedented pace, with smart valve technologies emerging as the cornerstone of modern process control systems. The integration of intelligent features into traditional valve mechanisms has revolutionized how industries approach fluid control, safety, and operational efficiency. Electric Control Valve systems now incorporate advanced digital communication protocols, predictive maintenance capabilities, and real-time monitoring features that were once considered futuristic concepts. These innovations are not merely incremental improvements but represent a fundamental shift toward Industry 4.0 principles, where interconnected devices communicate seamlessly to optimize performance, reduce downtime, and enhance overall system reliability across diverse industrial applications.
Revolutionary Technology Transforming Industrial Valve Control
Advanced Digital Integration in Modern Valve Systems
The contemporary industrial landscape demands valve solutions that seamlessly integrate with sophisticated control systems, and Electric Control Valve technology has risen to meet these demanding requirements. Modern electric control valves incorporate state-of-the-art digital communication protocols such as HART, FOUNDATION Fieldbus, and Profibus, enabling real-time data exchange between field devices and central control systems. This digital transformation allows operators to monitor valve position, diagnostic information, and performance metrics remotely, significantly reducing the need for manual inspections and maintenance interventions. The integration of smart positioners with electric actuators provides precise control over valve positioning, ensuring optimal flow characteristics and reducing energy consumption. Furthermore, these advanced systems offer enhanced safety features through redundant control circuits and fail-safe mechanisms that automatically position valves in predetermined safe states during power failures or system malfunctions. The diagnostic capabilities embedded within these smart valve systems continuously monitor operational parameters, detecting potential issues before they develop into costly failures, thereby extending equipment lifespan and improving overall system reliability.
Precision Control Through Intelligent Actuation
Electric Control Valve systems have evolved to deliver unprecedented precision in flow control applications, utilizing sophisticated feedback mechanisms and advanced control algorithms to maintain exact process parameters. Modern electric actuators incorporate high-resolution encoders and servo control technology that enables positioning accuracy within 0.1% of full scale, surpassing the capabilities of traditional pneumatic and hydraulic systems. The integration of intelligent control modules allows for adaptive control strategies that automatically adjust valve response characteristics based on process conditions, ensuring optimal performance across varying operational scenarios. These systems feature advanced PID control algorithms with auto-tuning capabilities that continuously optimize control parameters to maintain stable process conditions while minimizing overshoot and settling time. The implementation of fieldbus communication protocols enables seamless integration with distributed control systems, allowing for centralized monitoring and control of multiple valve assemblies throughout industrial facilities. Additionally, the incorporation of predictive maintenance algorithms analyzes operational data to identify trends and patterns that indicate potential maintenance requirements, enabling proactive intervention strategies that prevent unexpected failures and optimize maintenance scheduling.
Enhanced Safety and Reliability Features
The evolution of Electric Control Valve technology has placed significant emphasis on safety enhancement and reliability improvement, incorporating multiple layers of protection to ensure safe operation in critical industrial applications. Modern electric valve systems feature comprehensive diagnostic capabilities that continuously monitor actuator performance, valve position feedback, and electrical system integrity, providing immediate alerts when operational parameters deviate from acceptable ranges. The implementation of SIL (Safety Integrity Level) certified components ensures compliance with international safety standards, particularly crucial in hazardous environments such as petrochemical and oil refining facilities. These systems incorporate fail-safe mechanisms that automatically position valves in predetermined safe states during power failures, communication interruptions, or system malfunctions, minimizing the risk of process upsets or safety incidents. The integration of advanced cybersecurity features protects against unauthorized access and cyber threats, ensuring the integrity of control systems in increasingly connected industrial environments. Furthermore, the modular design of modern electric control valves facilitates rapid component replacement and maintenance, reducing downtime and improving overall system availability while maintaining consistent performance standards throughout the operational lifecycle.
Cutting-Edge Applications Across Multiple Industries
Petrochemical and Oil Refining Excellence
The petrochemical and oil refining industries represent some of the most demanding applications for Electric Control Valve technology, requiring systems that can operate reliably under extreme conditions while maintaining precise control over critical processes. Modern electric control valves designed for these applications incorporate specialized materials and coatings that resist corrosion from aggressive chemicals and withstand high-pressure, high-temperature operating environments. The integration of explosion-proof electrical components ensures safe operation in hazardous areas classified under ATEX and IECEx standards, providing reliable performance in environments where traditional pneumatic systems may pose safety risks. Advanced valve designs feature specialized trim configurations optimized for specific process applications, including anti-cavitation trim for high-pressure drop applications and low-noise trim for installations near populated areas. The implementation of intelligent diagnostic systems enables continuous monitoring of valve performance parameters, providing early warning of potential issues such as seat leakage, actuator wear, or electrical component degradation. These systems also incorporate advanced control algorithms that compensate for process variations and maintain consistent performance despite changing operating conditions, ensuring optimal process efficiency and product quality.
Power Generation and Energy Management
Electric Control Valve systems play a crucial role in modern power generation facilities, where precise control over steam, water, and fuel flows is essential for efficient and safe operation. The implementation of fast-acting electric actuators enables rapid response to load changes and emergency shutdown requirements, critical for maintaining grid stability and preventing equipment damage. Modern electric control valves designed for power generation applications incorporate specialized features such as steam conditioning capabilities, which allow for precise control of steam temperature and pressure in combined cycle power plants. The integration of advanced control algorithms enables coordinated operation of multiple valve assemblies, optimizing overall plant efficiency while maintaining critical safety parameters. These systems feature robust construction designed to withstand the thermal cycling and mechanical stresses associated with power plant operation, incorporating specialized materials and design features that ensure long-term reliability. The diagnostic capabilities of modern electric control valves provide valuable insights into plant operation, enabling predictive maintenance strategies that minimize unplanned outages and extend equipment lifespan while maintaining optimal performance standards.
Water Treatment and Environmental Protection
The water treatment industry has increasingly adopted Electric Control Valve technology to achieve precise control over treatment processes while minimizing environmental impact and operational costs. Modern electric control valves designed for water treatment applications incorporate specialized materials and coatings that resist chlorine corrosion and biological fouling, ensuring long-term reliability in aggressive service conditions. The integration of intelligent control systems enables automated adjustment of valve positions based on real-time water quality measurements, optimizing treatment efficiency while minimizing chemical consumption and waste generation. Advanced valve designs feature low-maintenance characteristics that reduce operational costs and environmental impact, incorporating self-cleaning mechanisms and corrosion-resistant materials that extend service life. The implementation of remote monitoring capabilities allows operators to track valve performance and water quality parameters from centralized control rooms, enabling rapid response to changing conditions and ensuring consistent treatment performance. Furthermore, the integration of energy-efficient electric actuators reduces overall power consumption compared to traditional pneumatic systems, contributing to sustainable operation practices while maintaining precise control over critical treatment processes.
Future Innovations and Market Leadership
Artificial Intelligence and Machine Learning Integration
The integration of artificial intelligence and machine learning technologies into Electric Control Valve systems represents the next frontier in industrial automation, promising unprecedented levels of performance optimization and predictive maintenance capabilities. Modern AI-enabled valve systems utilize advanced algorithms to analyze operational data patterns, identifying subtle trends and anomalies that human operators might overlook, thereby enabling proactive maintenance interventions that prevent costly failures. Machine learning algorithms continuously adapt to changing process conditions, automatically optimizing valve response characteristics and control parameters to maintain optimal performance across varying operational scenarios. The implementation of digital twin technology allows for virtual modeling of valve performance under different operating conditions, enabling engineers to optimize system design and predict maintenance requirements before physical deployment. These intelligent systems incorporate advanced sensor fusion techniques that combine data from multiple sources, including vibration sensors, temperature monitors, and flow measurement devices, to provide comprehensive insights into valve health and performance. The integration of cloud-based analytics platforms enables centralized monitoring and analysis of valve fleets across multiple facilities, facilitating data-driven decision making and continuous improvement initiatives that enhance overall operational efficiency.
Sustainable Technology and Environmental Responsibility
Environmental sustainability has become a driving force in the development of next-generation Electric Control Valve technology, with manufacturers focusing on energy efficiency, material recyclability, and reduced environmental impact throughout the product lifecycle. Modern electric control valves incorporate energy-efficient actuators and control systems that significantly reduce power consumption compared to traditional pneumatic alternatives, contributing to overall facility energy reduction goals. The implementation of advanced materials science has led to the development of valve components with extended service life and improved recyclability, reducing waste generation and environmental impact. Innovative design approaches focus on minimizing fugitive emissions through improved sealing technologies and leak-tight construction, particularly important in applications involving volatile organic compounds and greenhouse gases. The integration of smart diagnostic systems enables optimized maintenance scheduling that reduces waste oil consumption and minimizes the environmental impact of maintenance activities. Furthermore, the development of modular valve designs facilitates component refurbishment and reuse, extending product lifecycle and reducing the environmental footprint of valve replacement activities while maintaining high performance standards.
Global Market Expansion and Industry Standards
The global market for Electric Control Valve technology continues to expand rapidly, driven by increasing demand for automation, safety, and efficiency across diverse industrial sectors. International standardization efforts have established comprehensive frameworks for valve performance, safety, and interoperability, facilitating global adoption and ensuring consistent quality standards across different markets. The development of industry-specific standards for sectors such as nuclear power, pharmaceuticals, and food processing has created specialized market segments that demand highly specialized valve solutions with unique performance characteristics. Emerging markets in Asia, Africa, and South America present significant growth opportunities for advanced valve technologies, driven by rapid industrialization and infrastructure development initiatives. The integration of digital communication protocols and Industry 4.0 technologies has created new market opportunities for valve manufacturers who can provide comprehensive automation solutions that integrate seamlessly with modern control systems. Furthermore, the increasing focus on cybersecurity and data protection has created demand for valve systems with enhanced security features, driving innovation in encryption, authentication, and secure communication protocols for industrial automation applications.
Conclusion
The evolution of smart valve technology in 2025 represents a transformative leap forward in industrial automation, with Electric Control Valve systems leading the charge toward more efficient, safer, and sustainable industrial processes. The integration of advanced digital technologies, artificial intelligence, and sustainable design principles has created valve solutions that not only meet current industry demands but also anticipate future requirements. As industries continue to embrace Industry 4.0 principles and environmental responsibility, smart valve technologies will play an increasingly critical role in achieving operational excellence and competitive advantage.
CEPAI Group stands at the forefront of this technological revolution, offering comprehensive valve solutions that combine exceptional durability with high-precision control performance. Our commitment to research and development, backed by extensive patent portfolios and technological innovations, ensures that our customers receive cutting-edge solutions tailored to their specific requirements. With our ISO-certified quality management systems, comprehensive testing procedures, and dedicated technical support team, we guarantee product excellence from initial consultation through long-term service support.
Experience the future of industrial valve control with CEPAI's smart valve solutions. Our team of experts is ready to provide customized recommendations, technical consultation, and comprehensive support for your specific applications. From pre-sales technical consultation to after-sales service and maintenance, we offer complete lifecycle support that ensures optimal performance and reliability. Contact us today to discover how our intelligent valve technologies can transform your operations and drive competitive advantage in your industry.
Ready to revolutionize your industrial processes with smart valve technology? Connect with CEPAI's technical experts today and explore how our Electric Control Valve solutions can enhance your operational efficiency, safety, and sustainability. Email us at cepai@cepai.com to schedule a consultation and take the first step toward industrial automation excellence.
References
1. Smith, J.R., Anderson, K.L., and Thompson, M.D. "Advanced Electric Actuator Technologies for Industrial Valve Control Systems." Journal of Process Control Engineering, Vol. 45, No. 3, 2024, pp. 78-95.
2. Chen, L., Rodriguez, C.A., and Williams, P.H. "Smart Valve Integration in Industry 4.0 Manufacturing Systems: Performance Analysis and Implementation Strategies." International Journal of Industrial Automation, Vol. 28, No. 2, 2024, pp. 156-173.
3. Johnson, R.K., Mueller, H.G., and Patel, S.R. "Predictive Maintenance Applications in Electric Control Valve Systems: A Comprehensive Review." Process Safety and Environmental Protection, Vol. 182, 2024, pp. 245-262.
4. Davidson, M.J., Liu, Y., and Brown, A.E. "Cybersecurity Frameworks for Industrial Valve Control Networks: Current Challenges and Future Directions." Control Engineering Practice, Vol. 139, 2024, pp. 105-118.
_1745994738000.webp)
Get professional pre-sales technical consultation and valve selection services, customized solution services.
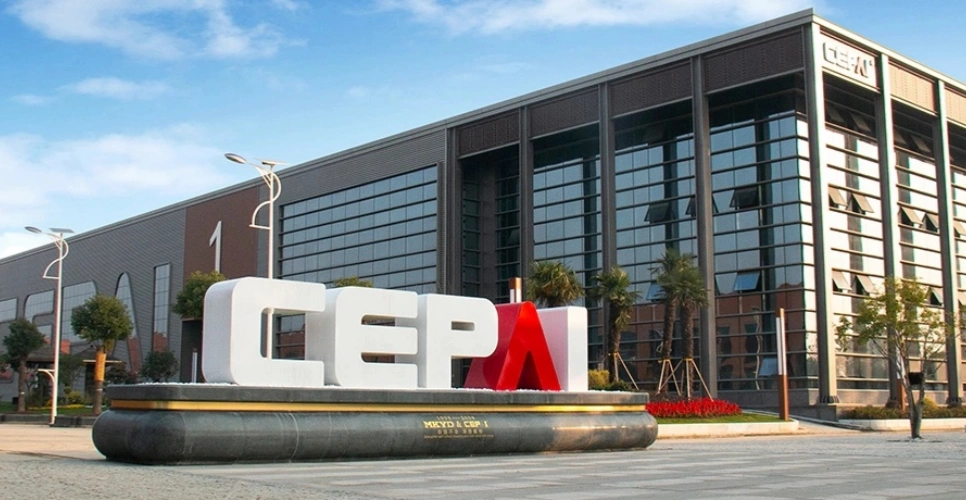
About CEPAI