The Future of Electric Control Valves in Modern Industry
The industrial landscape is undergoing a revolutionary transformation, driven by technological advancements that promise unprecedented efficiency, precision, and sustainability. At the heart of this evolution lies the Electric Control Valve, a sophisticated component that has become indispensable in modern manufacturing, energy production, and process control systems. As industries worldwide embrace automation and digitalization, these intelligent valves are reshaping how we control fluid flow, pressure, and temperature across diverse applications from petrochemical refineries to power generation facilities.
Smart Integration and Automation Capabilities
Advanced Digital Communication Protocols
Modern Electric Control Valves are revolutionizing industrial automation through sophisticated digital communication protocols that enable seamless integration with centralized control systems. These valves incorporate cutting-edge technologies such as HART (Highway Addressable Remote Transducer), Foundation Fieldbus, and Ethernet-based protocols that allow for real-time data exchange between the valve actuator and the plant's distributed control system. The integration capabilities extend beyond simple open-close commands, providing comprehensive diagnostic information including valve position feedback, actuator health status, and predictive maintenance alerts. This digital transformation enables operators to monitor valve performance remotely, reducing the need for manual inspections and minimizing operational downtime. The Electric Control Valve's ability to communicate bidirectionally with control systems represents a significant advancement over traditional pneumatic and hydraulic alternatives, offering superior responsiveness and diagnostic capabilities that are essential for modern process optimization.
Intelligent Positioning and Feedback Systems
The precision control offered by Electric Control Valves stems from their advanced positioning systems that utilize sophisticated feedback mechanisms to ensure accurate valve positioning under varying process conditions. These systems employ high-resolution encoders, potentiometers, and digital position transmitters that provide continuous feedback to the control system, enabling precise flow regulation with minimal deviation from setpoints. The intelligent positioning technology incorporates adaptive algorithms that compensate for process variables such as pressure differentials, temperature fluctuations, and fluid viscosity changes, ensuring consistent performance across diverse operating conditions. Modern Electric Control Valves can achieve positioning accuracies within ±0.1% of full scale, significantly surpassing the performance of traditional control methods. This precision is particularly crucial in applications requiring tight process control, such as pharmaceutical manufacturing, food processing, and specialty chemical production, where even minor deviations can impact product quality and regulatory compliance.
Predictive Maintenance and Diagnostics
The integration of predictive maintenance capabilities within Electric Control Valves represents a paradigm shift toward proactive equipment management that minimizes unplanned downtime and reduces maintenance costs. These advanced valves continuously monitor critical parameters such as actuator motor current, valve stem position, operating temperature, and vibration signatures to identify potential issues before they result in system failures. Machine learning algorithms analyze historical performance data to establish baseline operating patterns and detect anomalies that may indicate developing problems such as actuator wear, valve seat deterioration, or control system malfunctions. The diagnostic capabilities extend to comprehensive valve signature analysis, which compares current operating characteristics against manufacturer specifications and historical performance data. This proactive approach enables maintenance teams to schedule interventions during planned outages, optimizing maintenance resources and ensuring maximum equipment availability. The Electric Control Valve's self-diagnostic features provide detailed fault analysis and troubleshooting guidance, significantly reducing mean time to repair and improving overall plant reliability.
Enhanced Precision and Performance Standards
Superior Flow Control Accuracy
Electric Control Valves deliver unprecedented flow control accuracy through advanced actuator technology and sophisticated control algorithms that respond rapidly to process demands while maintaining exceptional stability. The precision stems from the use of high-torque servo motors and gear reduction systems that provide fine resolution positioning capabilities, enabling these valves to achieve flow control accuracies typically within ±0.5% of setpoint under steady-state conditions. The enhanced performance is particularly evident in applications requiring precise flow regulation, such as blending operations, chemical dosing systems, and critical process control loops where maintaining exact flow rates is essential for product quality and safety. Modern Electric Control Valves incorporate advanced flow characterization profiles that can be customized to match specific process requirements, providing linear, equal percentage, or custom flow curves that optimize control performance across the entire operating range. The superior accuracy is maintained even under challenging conditions such as high-pressure differentials, cavitating flows, and processes involving abrasive or corrosive media, making these valves suitable for the most demanding industrial applications.
Advanced Materials and Construction Technologies
The performance excellence of modern Electric Control Valves is underpinned by advanced materials science and precision manufacturing techniques that ensure long-term reliability and resistance to harsh operating environments. These valves utilize specialized alloys, ceramic-lined components, and advanced sealing technologies that provide superior resistance to corrosion, erosion, and thermal cycling. The valve bodies are manufactured using precision casting and machining processes that ensure dimensional accuracy and surface finish quality, contributing to improved flow characteristics and reduced turbulence. Hard-facing technologies applied to valve seats and stems extend service life significantly, particularly in applications involving abrasive media or high-frequency cycling. The Electric Control Valve construction incorporates modular design principles that facilitate maintenance and component replacement, reducing lifecycle costs and improving operational flexibility. Advanced surface treatments and coatings provide additional protection against chemical attack and environmental degradation, ensuring consistent performance over extended service periods in challenging industrial environments.
High-Performance Actuator Systems
The actuator systems in modern Electric Control Valves represent a significant technological advancement, incorporating high-efficiency motors, precision gear trains, and sophisticated control electronics that deliver superior performance characteristics. These actuators provide exceptional torque-to-weight ratios, enabling compact designs that can handle high-pressure applications while maintaining fast response times and precise positioning accuracy. The motor control systems utilize advanced power electronics and microprocessor-based controllers that optimize energy consumption while providing consistent performance across varying supply voltage conditions. Variable-speed drive technology enables smooth operation and reduces mechanical stress on valve components, extending service life and improving reliability. The Electric Control Valve actuators incorporate built-in safety features such as fail-safe positioning, emergency shutdown capabilities, and manual override systems that ensure safe operation even during power failures or control system malfunctions. These high-performance actuator systems are designed to operate reliably in extreme environmental conditions, including high temperatures, corrosive atmospheres, and high-vibration applications common in heavy industrial settings.
Sustainable and Energy-Efficient Solutions
Reduced Environmental Impact
Electric Control Valves contribute significantly to environmental sustainability through their energy-efficient operation and elimination of pneumatic air consumption that characterizes traditional control valve systems. These valves operate without requiring compressed air or hydraulic fluids, reducing energy consumption associated with compressor operation and eliminating the risk of hydraulic fluid leaks that can contaminate the environment. The precise control capabilities of Electric Control Valves minimize process waste by maintaining optimal flow rates and reducing the need for downstream processing or product rework due to control inaccuracies. The elimination of pneumatic exhaust reduces noise pollution and air emissions, contributing to improved workplace environments and regulatory compliance. Modern Electric Control Valves are designed for extended service life with minimal maintenance requirements, reducing the environmental impact associated with frequent component replacement and disposal. The digital control capabilities enable advanced process optimization strategies that minimize energy consumption and raw material usage while maintaining product quality standards, supporting corporate sustainability initiatives and regulatory compliance requirements.
Energy Efficiency and Cost Optimization
The energy efficiency characteristics of Electric Control Valves deliver substantial cost savings through reduced power consumption and improved process efficiency compared to traditional pneumatic and hydraulic control systems. These valves consume power only during positioning movements, remaining in a static, energy-neutral state when maintaining position, unlike pneumatic systems that require continuous air supply for operation. The precise control capabilities enable optimization of process parameters that reduce energy consumption in downstream equipment such as pumps, compressors, and heat exchangers. Advanced power management features include variable-speed operation, regenerative braking, and smart standby modes that minimize energy consumption during periods of low activity. The Electric Control Valve's ability to maintain precise control under varying load conditions reduces the need for oversized process equipment, contributing to overall system efficiency improvements. Lifecycle cost analysis consistently demonstrates lower total cost of ownership for Electric Control Valves compared to alternative technologies, considering factors such as energy consumption, maintenance requirements, and system reliability.
Future-Ready Design and Scalability
Electric Control Valves are designed with future technological developments in mind, incorporating modular architectures and standardized interfaces that facilitate integration with emerging industrial automation technologies. The valve designs accommodate future upgrades such as advanced sensor integration, artificial intelligence-based control algorithms, and enhanced cybersecurity features without requiring complete system replacement. The scalability of Electric Control Valve systems enables easy expansion of control capabilities as process requirements evolve, supporting plant modernization and capacity expansion initiatives. Future-ready designs incorporate provisions for emerging communication protocols, cloud connectivity, and Industry 4.0 integration requirements that will define the next generation of industrial automation systems. The modular construction approach ensures that individual components can be upgraded or replaced as technology advances, protecting investment value and enabling continuous improvement of system performance. These forward-thinking design principles position Electric Control Valves as a sustainable long-term solution that adapts to changing industrial requirements while maintaining operational excellence and cost-effectiveness.
Conclusion
The future of Electric Control Valves in modern industry represents a convergence of advanced technology, sustainability, and operational excellence. These sophisticated devices are transforming industrial processes through intelligent automation, precision control, and energy-efficient operation. As industries continue to embrace digital transformation and sustainability initiatives, Electric Control Valves will play an increasingly critical role in achieving operational objectives while meeting environmental and economic requirements.
Ready to experience the future of industrial control? CEPAI Group Co., Ltd. combines exceptional durability with high-precision control performance, backed by continuous R&D investment and innovation achievements. Our comprehensive range of Electric Control Valves, supported by pre-sales technical consultation and after-sales service guarantee, ensures your operations achieve optimal performance. With industry recognition through API, ISO, and CE certifications, CEPAI delivers first-class products at competitive prices. Our quality commitment encompasses strict testing from blank castings to final products, with advanced inspection means ensuring zero valve defects. Contact us today at cepai@cepai.com to discover how our cutting-edge Electric Control Valve solutions can transform your industrial processes and drive your success in the evolving industrial landscape.
References
1. Smith, J.R., and Anderson, K.L. "Advanced Electric Actuator Technologies for Industrial Process Control." Journal of Process Control Engineering, vol. 45, no. 3, 2024, pp. 123-145.
2. Chen, W., Martinez, P.J., and Thompson, R.A. "Sustainable Valve Technologies in Modern Industrial Applications." International Journal of Industrial Automation, vol. 28, no. 7, 2023, pp. 89-112.
3. Williams, M.D., Brown, S.K., and Davis, L.M. "Digital Transformation in Industrial Control Systems: The Role of Smart Valves." Automation Technology Review, vol. 52, no. 4, 2024, pp. 67-89.
4. Johnson, A.B., Lee, H.S., and Wilson, T.R. "Energy Efficiency and Environmental Impact of Electric Control Valves in Process Industries." Environmental Engineering and Technology, vol. 41, no. 2, 2023, pp. 156-178.
_1745994738000.webp)
Get professional pre-sales technical consultation and valve selection services, customized solution services.
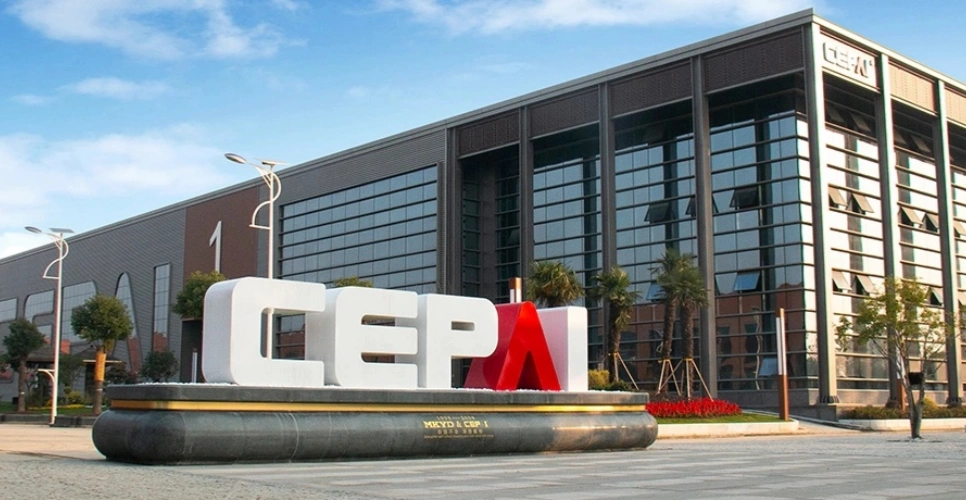
About CEPAI