Troubleshooting Common Pneumatic Control Valve Problems
Pneumatic control valves are critical components in modern industrial control systems, regulating flow, pressure, and temperature across numerous applications. When these precision instruments malfunction, they can disrupt entire processes, leading to decreased efficiency, product quality issues, and potential safety hazards. Understanding how to effectively troubleshoot common pneumatic control valve problems is essential for maintaining operational reliability and minimizing costly downtime. This comprehensive guide explores the most frequent issues encountered with pneumatic control valves and provides practical, expert-level solutions to quickly identify, diagnose, and resolve these challenges.
Identifying Common Pneumatic Control Valve Performance Issues
Air Supply and Pressure-Related Problems
Pneumatic control valves rely heavily on consistent air supply to function properly. Inadequate or fluctuating air pressure is one of the most common sources of valve malfunction. When the instrument air supply fails to maintain the required pressure levels, valves may respond sluggishly or fail to reach their full stroke position. This results in imprecise flow control that compromises process stability. Regular inspection of air supply systems is crucial, including checking compressors, filters, regulators, and supply lines for leaks or blockages. A well-maintained air supply system should deliver clean, dry air at consistent pressure to ensure optimal performance of pneumatic control valves. It's worth noting that air supply pressure should typically be maintained at least 10 psi above the maximum spring range of the actuator to ensure proper operation. In systems where multiple pneumatic control valves share an air supply, ensure that the system is properly sized to accommodate peak demand without pressure drops that could affect valve performance. Installing pressure gauges at strategic points in the air supply system allows for quick identification of pressure-related issues before they significantly impact valve operation.
Leakage Detection and Resolution
Leakage in pneumatic control valves can occur in various components, including diaphragms, seals, gaskets, or connections. These leaks not only waste compressed air—a costly utility in industrial settings—but also compromise valve positioning accuracy and response time. To detect air leaks, technicians should conduct regular inspections using soap-water solutions applied to suspected leak points, ultrasonic leak detectors, or thermal imaging technology for more advanced detection. When leaks are identified in a pneumatic control valve system, proper resolution involves not just replacing the damaged components but also investigating the root cause. Excessive wear might indicate misalignment, improper installation, or incompatibility with process media. Additionally, environmental factors such as temperature extremes or corrosive atmospheres can accelerate seal degradation. Implementing a preventive maintenance program that includes regular inspection and replacement of wear-prone components before failure occurs can significantly reduce unexpected leakage issues and extend the service life of pneumatic control valves. High-quality replacement parts that meet or exceed original equipment specifications should always be used to ensure reliable performance after repairs.
Calibration Drift and Correction Methods
Over time, pneumatic control valves may experience calibration drift due to mechanical wear, environmental conditions, or changes in the process requirements. This drift manifests as discrepancies between the control signal and the actual valve position, leading to inaccurate process control. Identifying calibration issues requires regular testing of valve positioning at various signal points across the operating range. Modern calibration techniques utilize digital positioners with diagnostic capabilities that can detect and quantify positioning errors. When correcting calibration drift in pneumatic control valves, technicians should follow a systematic approach that begins with verifying the input signal and establishing a proper zero point. The span adjustment should then be calibrated to ensure the valve achieves full travel at the maximum input signal. For critical applications, hysteresis and linearity should also be measured and adjusted if necessary. It's important to note that calibration should be performed under conditions that closely match normal operating parameters whenever possible. Some advanced pneumatic control valve positioners offer self-calibration features that continuously adjust for minor positioning errors, significantly reducing the need for manual intervention. However, these systems still require periodic verification against traceable standards to ensure they remain within acceptable tolerances.
Diagnosing Mechanical and Structural Failures
Actuator Diaphragm and Spring Issues
The actuator diaphragm and spring assembly form the heart of many pneumatic control valves, converting air pressure signals into mechanical positioning force. When these components fail, valve operation becomes erratic or completely compromised. Diaphragm failures often present as continuous air leakage from the actuator housing or sudden loss of control capability. Visual inspection may reveal tears, holes, or material degradation in the diaphragm. Spring issues typically manifest as incorrect valve positioning or failure to return to the proper fail-safe position when air pressure is removed. Troubleshooting these components requires careful disassembly and inspection according to manufacturer guidelines. When addressing actuator diaphragm and spring issues in pneumatic control valves, it's critical to consider the operating environment and application requirements. Diaphragms exposed to high temperatures or corrosive environments may require specialized materials such as PTFE-coated or composite constructions rather than standard elastomers. Similarly, actuator springs must be selected with appropriate spring rates and materials to withstand cyclic fatigue and environmental challenges. During maintenance, proper reassembly is crucial—ensuring correct diaphragm alignment and uniform compression prevents premature failure. Additionally, technicians should verify that the pneumatic control valve actuator sizing remains appropriate for the application, as changes in process conditions may require actuators capable of generating different force outputs to maintain proper control.
Stem and Trim Component Wear Analysis
The valve stem and internal trim components (seats, plugs, cages, etc.) are subject to continuous mechanical stress and potential erosion or corrosion during operation. Wear in these areas leads to increased leakage, reduced control precision, and eventually complete valve failure. Signs of trim wear include increased flow noise, inability to achieve tight shutoff, and erratic control behavior. Analyzing stem and trim wear requires isolation of the valve from the process, careful disassembly, and thorough inspection of all components using precision measurement tools. Careful examination of pneumatic control valve stem and trim components can reveal valuable information about process conditions and potential system issues. For example, asymmetrical wear patterns might indicate misalignment or uneven flow distribution, while particular erosion patterns can point to cavitation or flashing conditions that need to be addressed at a system level. When replacing worn components, consider upgrades to materials or designs that offer enhanced resistance to the specific wear mechanisms identified. Hardened surfaces, stellite overlays, or ceramic components may provide significantly longer service life in challenging applications. Modern pneumatic control valve designs often feature quick-change trim arrangements that reduce maintenance time and improve interchangeability. Additionally, implementing proper installation practices such as ensuring correct pipe alignment and adequate support can significantly reduce mechanical stresses that accelerate stem and trim wear.
Positioner and Feedback Mechanism Troubleshooting
Positioners and feedback mechanisms ensure that pneumatic control valves achieve and maintain their commanded positions accurately. Failures in these systems lead to positioning errors, oscillations, or complete loss of control capability. Common issues include clogged air passages, worn feedback linkages, or electronic component failures in electro-pneumatic positioners. Troubleshooting these systems begins with verifying proper supply pressure and signal quality, followed by systematic checking of mechanical connections and electronic circuitry as applicable. The feedback mechanism's calibration and condition should be thoroughly inspected for signs of wear or damage. Advanced troubleshooting of pneumatic control valve positioners requires understanding the specific technology employed, whether traditional pneumatic, electro-pneumatic, or digital. For pneumatic positioners, nozzle and flapper assemblies must be checked for debris or damage that could obstruct the precise air flows required for accurate positioning. In digital positioners, diagnostic information stored in the device memory can often provide valuable clues about intermittent issues or developing problems. Proper grounding and protection from electromagnetic interference are essential for reliable operation of electronic components in modern positioners. When replacements are necessary, consider the benefits of upgrading to current-generation smart positioners that offer enhanced diagnostics, improved control algorithms, and communication capabilities that enable preventive maintenance approaches. These advanced positioners can often identify developing problems in the pneumatic control valve system before they cause operational issues, allowing for planned maintenance rather than emergency repairs.
Implementing Preventive Maintenance Strategies
Predictive Maintenance Using Advanced Diagnostics
Modern pneumatic control valves increasingly incorporate smart positioners equipped with advanced diagnostic capabilities that continuously monitor valve performance parameters. These systems can detect developing issues such as increased friction, positioning errors, air leakage, or supply pressure problems before they cause operational failures. Implementing predictive maintenance using these diagnostics involves establishing baseline performance parameters for each pneumatic control valve and monitoring trends over time to identify deviations that indicate impending problems. This approach allows maintenance to be scheduled based on actual equipment condition rather than arbitrary time intervals, optimizing resource allocation and minimizing unplanned downtime. Effective implementation of predictive maintenance for pneumatic control valves requires more than just installing diagnostic-capable equipment—it demands a systematic approach to data collection, analysis, and response. Establishing clear thresholds for various parameters helps maintenance teams distinguish between normal variations and actionable deterioration. For critical pneumatic control valves, continuous online monitoring may be justified, while less critical applications might utilize periodic data collection during routine inspections. Modern valve diagnostic systems can often be integrated with plant-wide asset management platforms, enabling correlation with other process variables and facilitating comprehensive health assessments. Training maintenance personnel to properly interpret diagnostic data is essential—advanced systems can generate significant information that must be correctly prioritized and acted upon. When properly implemented, these predictive approaches can reduce maintenance costs by 25-30% while significantly improving reliability of pneumatic control valve systems across the facility.
Routine Inspection and Testing Protocols
Even with advanced diagnostics, regular physical inspection and testing of pneumatic control valves remain essential components of a comprehensive maintenance strategy. Developing standardized protocols for these activities ensures consistency and thoroughness. Routine inspections should include visual examination of external components for signs of damage or leakage, verification of mounting hardware tightness, checking air connections and filter condition, and observation of valve operation through at least one complete cycle. Periodic stroke testing, where the valve is moved through its full range of motion while monitoring parameters such as air consumption and response time, can identify developing issues not apparent during normal operation. Creating detailed inspection checklists tailored to each type of pneumatic control valve in the facility ensures that critical aspects aren't overlooked during routine maintenance activities. The frequency of inspections should be determined based on the criticality of the application, operating conditions, and historical performance data. Valves in severe service applications or controlling critical processes may require monthly inspections, while those in less demanding roles might be adequately served by quarterly or semi-annual checks. Documentation of inspection findings creates a valuable history that can reveal long-term trends and recurring issues. Incorporating visual inspection ports or test connections in pneumatic control valve installations can simplify routine testing without requiring complete disassembly or process interruption. Training maintenance personnel to recognize subtle indicators of developing problems—such as unusual sounds, slight stem movement hesitation, or minor changes in operating characteristics—enables early intervention before catastrophic failures occur.
Environmental Impact and Protection Measures
The environment surrounding pneumatic control valves significantly impacts their reliability and longevity. Extreme temperatures, humidity, corrosive atmospheres, and vibration can all accelerate component deterioration and cause premature failures. Implementing protective measures tailored to the specific environmental challenges faced by each valve installation can dramatically extend service life and reduce maintenance requirements. These measures might include installing protective enclosures, applying specialized coatings, implementing heating or cooling systems for temperature control, or utilizing vibration dampening mounts. Regular assessment of environmental conditions should be incorporated into maintenance routines to identify changing conditions that might necessitate additional protection. Protecting pneumatic control valves from harsh environmental conditions requires consideration of multiple factors. In outdoor installations, weatherproof enclosures with appropriate NEMA or IP ratings should be selected to prevent moisture ingress and UV damage. For valves operating in corrosive environments, material selection becomes critical—stainless steel, specialized alloys, or composite materials may offer superior resistance to chemical attack compared to standard carbon steel components. Temperature extremes present particular challenges for pneumatic control valves: excessive heat can degrade soft components and lubricants, while cold temperatures can cause condensation and freezing in air passages. Installing air dryers and using low-temperature-rated components may be necessary in cold environments. Vibration protection requires attention to mounting methods, pipe support, and potentially the addition of flexible connectors to isolate the valve from system-induced stresses. For pneumatic control valves in hazardous areas, ensuring appropriate certifications and maintaining the integrity of explosion-proof or intrinsically safe installations is essential for both reliability and safety compliance.
Conclusion
Effective troubleshooting and maintenance of pneumatic control valves are essential for maintaining operational efficiency and reliability in industrial processes. By understanding common issues related to air supply, mechanical components, and electronic systems, technicians can quickly identify and resolve problems before they cause significant disruption. Implementing comprehensive preventive maintenance strategies, including advanced diagnostics and routine inspections, further enhances system reliability and extends service life.
At CEPAI Group, we pride ourselves on our exceptional durability, high-precision control performance, and continuous R&D investment. Our pneumatic control valves are backed by numerous patents, technological innovations, and comprehensive service guarantees. Whether you need pre-sales technical consultation, customized solutions, installation support, or ongoing maintenance services, our expert team is ready to assist you. Experience the difference that ISO-certified quality management and rigorous testing standards make in valve performance and reliability. Ready to solve your pneumatic control valve challenges? Contact our technical team today at cepai@cepai.com and discover how our industry-leading solutions can optimize your operations.
References
1. Smith, J.R. & Thompson, K.L. (2023). "Advanced Troubleshooting Techniques for Industrial Pneumatic Control Systems." Journal of Control Engineering Practice, 89, 115-132.
2. Zhang, Y., Wang, H., & Miller, R. (2024). "Predictive Maintenance Strategies for Critical Control Valves in Process Industries." International Journal of Pressure Vessels and Piping, 205, 104720.
3. Anderson, P.M. (2023). "Analysis of Failure Modes in Pneumatic Valve Actuators: A 10-Year Industry Study." Reliability Engineering & System Safety, 229, 108866.
4. Williams, D.B. & Chen, L. (2022). "Environmental Effects on the Performance and Longevity of Control Valve Components." ISA Transactions, 130, 436-451.
5. Patel, S. & Nakamura, T. (2024). "Digital Transformation in Valve Diagnostics: Implementation Cases and Results." IEEE Transactions on Industrial Electronics, 71(5), 4892-4901.
6. Johnson, M.R. & García-Hernández, A. (2023). "Best Practices in Pneumatic Control Valve Selection and Maintenance for Energy-Intensive Industries." Energy Procedia, 198, 589-604.

Get professional pre-sales technical consultation and valve selection services, customized solution services.
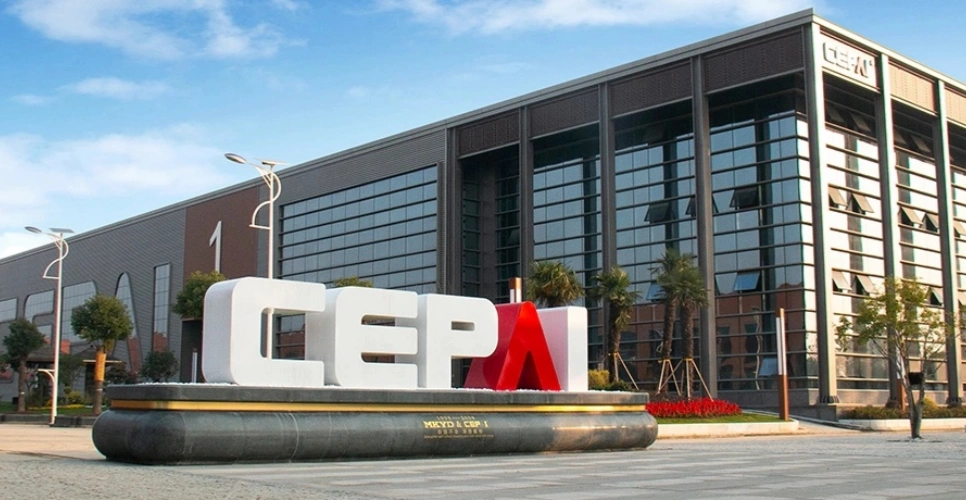
About CEPAI