How to Choose the Perfect Pneumatic Control Valve for Your Needs?
Selecting the right pneumatic control valve is crucial for ensuring optimal performance, efficiency, and reliability in your fluid control systems. Pneumatic control valves play a vital role in regulating flow, pressure, and temperature across diverse industrial applications, from oil and gas processing to chemical manufacturing and power generation. Making an informed choice requires understanding various factors including valve types, sizing considerations, material compatibility, and control characteristics. This comprehensive guide will walk you through the essential criteria to consider when selecting the perfect pneumatic control valve tailored specifically to your operational requirements.
Understanding the Fundamentals of Pneumatic Control Valve Selection
Design and Working Principles of Pneumatic Control Valves
Pneumatic control valves operate on the principle of using compressed air to control the movement of the valve stem, which in turn regulates the flow of media through the valve. The design typically consists of a valve body, actuator, positioner, and various accessories. The pneumatic actuator converts air pressure into mechanical force, moving the valve plug to control flow. Understanding these fundamental components is essential for proper selection. Different pneumatic control valve designs offer varying advantages: diaphragm actuators provide stable, precise control for smaller valves; piston actuators deliver higher thrust capabilities for larger applications; and rotary actuators enable quarter-turn operation for ball, butterfly, and plug valves. Selection should be based on your specific process conditions, required control precision, and environmental factors. The right pneumatic control valve design ensures optimal performance while minimizing energy consumption and maintenance requirements over its operational lifespan.
Key Performance Parameters to Consider
When selecting a pneumatic control valve, several critical performance parameters must be evaluated to ensure optimal operation. Flow coefficient (Cv) is perhaps the most important parameter, indicating the flow capacity of the valve under specified conditions. Rangeability, the ratio between maximum and minimum controllable flow, determines the valve's ability to handle varying process demands. Response time measures how quickly the valve reacts to control signals, critical in applications requiring rapid adjustments. Additionally, consider the pneumatic control valve's leakage class, which defines the maximum allowable leakage when the valve is in the closed position. Proper shutdown capability and fail-safe position (open, closed, or last position) are essential safety considerations. Pneumatic pressure requirements, including minimum and maximum supply pressure for actuator operation, must match your available air supply. Hysteresis and deadband characteristics affect control precision and stability. Evaluating these parameters comprehensively ensures your selected pneumatic control valve will deliver reliable, accurate control under all anticipated operating conditions.
Industry-Specific Requirements and Standards
Different industries have unique requirements for pneumatic control valves based on their specific processes, safety concerns, and regulatory environments. In the oil and gas sector, pneumatic control valves must comply with API standards (API 6D, API 6A) and often require fire-safe design, fugitive emissions control, and sour service compliance. Chemical processing applications demand chemical compatibility, corrosion resistance, and adherence to standards like ASME B16.34. Power generation facilities require pneumatic control valves that can withstand high temperatures and pressures while meeting stringent reliability requirements. Pharmaceutical and food processing industries necessitate sanitary designs compliant with FDA regulations and 3-A standards. When selecting a pneumatic control valve, it's essential to identify all applicable industry standards, certifications, and compliance requirements. High-quality manufacturers like CEPAI Group provide comprehensive documentation of their pneumatic control valves' compliance with relevant standards, including appropriate certifications such as NACE MR0175/ISO 15156 for sour service, SIL certification for safety applications, and ISO 9001 for quality management systems. Ensuring your valve meets these industry-specific requirements is crucial for regulatory compliance, safety, and optimal performance.
Advanced Technical Considerations for Optimal Valve Performance
Material Selection for Different Process Media
Choosing the right materials for your pneumatic control valve components is critical for ensuring longevity and reliable performance in specific process environments. Body materials must withstand process pressure, temperature, and media characteristics—carbon steel suits standard applications; stainless steel offers superior corrosion resistance; and specialty alloys like Hastelloy or Monel handle highly corrosive media. Trim materials (seat, plug, stem) directly contact process media and must resist erosion, corrosion, and wear—hardened stainless steel, stellite-faced components, or ceramic options may be necessary for severe service. Sealing materials must maintain integrity across the entire temperature range and chemical exposure profile—PTFE, EPDM, Viton, graphite, and metal seals each offer specific advantages for different applications. When selecting pneumatic control valve materials, consider not just current process conditions but also potential upsets, cleaning procedures, and long-term operation. Reputable manufacturers like CEPAI Group provide extensive material selection guidance based on decades of field experience across diverse industries. Their pneumatic control valve experts can recommend optimal material combinations based on your specific media characteristics, temperature ranges, and pressure conditions, ensuring maximum service life while minimizing the risk of unexpected failures that could impact production.
Sizing and Capacity Calculations
Accurate sizing is perhaps the most critical factor in pneumatic control valve selection, directly impacting control performance, energy efficiency, and valve lifespan. Undersized pneumatic control valves cannot deliver required flow rates, causing process bottlenecks and control instability, while oversized valves lead to poor rangeability, excessive wear from operating near closed positions, and control issues like hunting. Proper sizing begins with gathering comprehensive process data: normal, maximum, and minimum flow rates; inlet and outlet pressures under all operating conditions; process media properties including density, viscosity, and phase changes; and temperature ranges. These parameters feed into standardized equations to calculate the required flow coefficient (Cv) for your pneumatic control valve. The calculation must account for installed characteristics, including pipe geometry, valve location, and potential flashing or cavitation conditions. High-quality pneumatic control valve manufacturers like CEPAI Group offer sophisticated sizing software that considers these complexities, helping engineers select valves with appropriate capacity and characteristics. Many sizing failures occur from using incomplete data or overlooking operating scenarios like startup, shutdown, or process upsets. CEPAI's technical specialists can assist in thorough sizing analysis, providing detailed documentation of calculations and recommendations for pneumatic control valve specifications optimized for your specific application requirements.
Control Characteristics and Response Time
The control characteristic of a pneumatic control valve—the relationship between valve opening and flow rate—fundamentally determines its controllability in your specific application. Quick-opening characteristics deliver large flow changes with small initial stem movements, making them suitable for on-off or bypass applications. Linear characteristics maintain a proportional relationship between valve position and flow, ideal for liquid level or pressure control where system pressure drop varies proportionally with flow. Equal percentage characteristics, where equal increments of valve travel produce equal percentage changes in flow, excel in applications with large pressure drop variations. The pneumatic control valve's installed characteristic, which factors in system effects, often differs from its inherent characteristic, requiring careful analysis during selection. Response time—how quickly the valve reaches a new position after a signal change—depends on actuator sizing, positioner capabilities, and accessories like volume boosters or quick exhaust valves. Applications with rapid process changes require faster-responding pneumatic control valves to maintain stable control. Modern digital positioners can enhance response characteristics through adaptive tuning algorithms. CEPAI Group offers advanced pneumatic control valves with customizable control characteristics and precisely engineered actuator-positioner combinations to achieve optimal response times. Their application engineers can help match these critical performance aspects to your specific process control requirements, ensuring stable, accurate control under all operating conditions.
Implementation and Maintenance Considerations
Installation Best Practices and System Integration
Proper installation of pneumatic control valves is crucial for achieving optimal performance and longevity. Begin with careful inspection upon receipt, verifying specifications match order requirements and checking for any shipping damage. Consider accessibility for maintenance when determining mounting location, ensuring sufficient clearance for actuator removal and valve servicing. Pneumatic control valves should be installed with proper support to prevent pipeline stress from transferring to the valve body, which can cause misalignment and premature failure. Flow direction must match the arrow on the valve body, as reverse installation can damage trim components and reduce control effectiveness. For pneumatic systems, clean, dry instrument air meeting ISO 8573-1 standards is essential—install appropriate filtration and drying equipment to prevent moisture and particulate contamination that can damage sensitive components. Integration with control systems requires careful calibration of positioners and ensuring signal compatibility. Modern pneumatic control valves often include digital communication capabilities through protocols like HART, Foundation Fieldbus, or Profibus, enabling advanced diagnostics and integration with plant-wide asset management systems. CEPAI Group provides comprehensive installation guidelines and offers installation supervision services to ensure their pneumatic control valves are properly integrated into your system, maximizing performance and reliability from day one.
Preventive Maintenance Strategies
Implementing structured preventive maintenance programs significantly extends pneumatic control valve service life while minimizing unexpected failures and production interruptions. Begin with regular visual inspections to identify external leaks, unusual noise, or vibration that might indicate developing issues. Pneumatic system components require particular attention—inspect air filters and regulators monthly, replacing filter elements as needed to ensure clean air supply. Actuator diaphragms and seals should be inspected according to manufacturer recommendations, typically annually, with replacement parts kept in inventory for critical valves. Partial stroke testing can verify emergency shutdown capability without disrupting production. Modern pneumatic control valves equipped with digital positioners enable condition-based maintenance through diagnostic capabilities that monitor parameters like friction, air consumption, and cycle counts. These diagnostics help identify developing issues before they cause failures, allowing maintenance to be scheduled during planned outages. CEPAI Group's pneumatic control valves feature advanced diagnostic capabilities and are designed for easy maintenance with standardized components. Their valve maintenance training programs equip technical staff with the knowledge to perform proper inspection and service procedures. Additionally, CEPAI offers comprehensive maintenance contracts with scheduled inspections, performance testing, and priority emergency service to maximize the reliability and performance of their pneumatic control valves throughout their operational lifetime.
Troubleshooting Common Issues
Even well-designed and properly maintained pneumatic control valves may occasionally experience operational issues. Understanding common problems and their potential causes enables rapid diagnosis and resolution, minimizing downtime. Hunting or oscillation—where the valve constantly moves between positions without stabilizing—typically results from oversizing, excessive friction, or improper positioner tuning. Sluggish response might indicate insufficient air supply, actuator sizing issues, or sticky valve components requiring lubrication or cleaning. Leakage through a closed pneumatic control valve often stems from debris between seating surfaces, worn seats or plugs, or insufficient actuator thrust to achieve tight shutoff. High air consumption points to leaks in actuator diaphragms, positioner components, or pneumatic fittings. Inconsistent control accuracy may result from hysteresis caused by friction, loose linkages, or worn components. When troubleshooting, follow a systematic approach: verify input signals are correct, check air supply pressure and quality, inspect for visible damage or wear, and use diagnostic tools to isolate specific components causing issues. CEPAI Group provides comprehensive troubleshooting guides for their pneumatic control valves, along with 24/7 technical support. Their service engineers can perform advanced diagnostics using specialized equipment to identify root causes of persistent issues. For critical applications, CEPAI's remote monitoring services can continuously analyze valve performance data, providing early warning of developing problems before they impact production, demonstrating their commitment to ensuring their pneumatic control valves deliver reliable, precise control throughout their operational life.
Conclusion
Selecting the perfect pneumatic control valve requires careful consideration of design principles, performance parameters, material compatibility, sizing calculations, and maintenance requirements. By thoroughly evaluating these factors in relation to your specific application needs, you can ensure optimal performance, reliability, and longevity. CEPAI Group, with its state-of-the-art manufacturing facilities, extensive R&D capabilities, and comprehensive quality management systems, stands ready to provide customized pneumatic control valve solutions backed by expert technical support and reliable after-sales service. For personalized assistance with your valve selection process or to discuss your specific application challenges, contact our team of experts today at cepai@cepai.com.
References
1. Smith, J.R. (2023). Pneumatic Control Valve Engineering Handbook. Industrial Press, New York.
2. Johnson, A.B. & Williams, P.T. (2024). Advanced Process Control: Valve Selection and Implementation. Chemical Engineering Journal, 56(3), 112-128.
3. International Society of Automation. (2023). ISA-75.01.01: Flow Equations for Sizing Control Valves. Research Triangle Park, NC.
4. Zhang, L. & Thompson, R.D. (2024). Material Selection for Control Valves in Corrosive Environments. Materials Performance, 63(2), 45-52.
5. Pneumatic Control Valve Manufacturers Association. (2024). Best Practices for Pneumatic Valve Maintenance and Troubleshooting. Industry Standards Quarterly, 41(1), 87-93.
6. Chen, W., Li, Y., & Anderson, K.L. (2023). Comparative Analysis of Control Valve Characteristics in Process Industries. Journal of Control Engineering Practice, 89, 204-217.

Get professional pre-sales technical consultation and valve selection services, customized solution services.
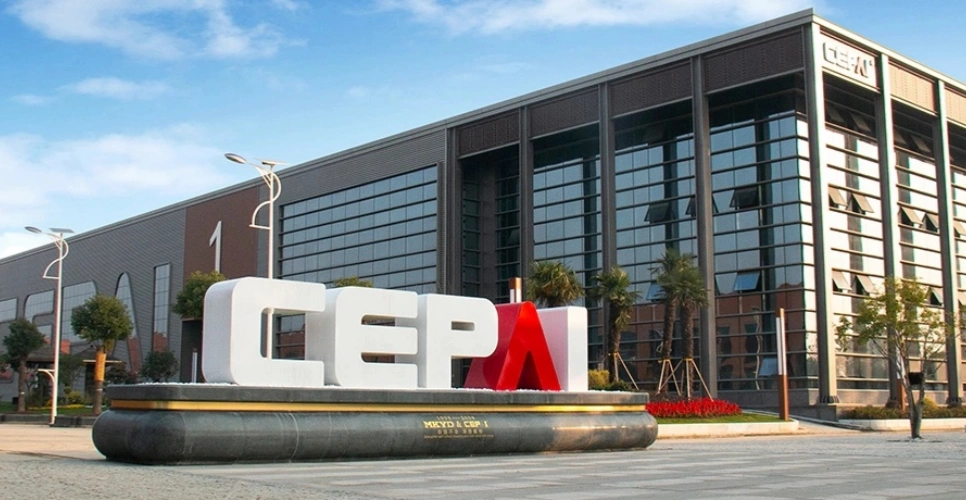
About CEPAI