Top Troubleshooting Tips for Pneumatic Control Valves in 2025
As industrial automation continues to evolve in 2025, pneumatic control valves remain critical components in process control systems across petrochemical, power generation, and manufacturing industries. These sophisticated devices face increasing operational demands, requiring maintenance professionals to stay ahead of common issues that can disrupt production efficiency. Understanding the most effective troubleshooting strategies for pneumatic control valve systems has become essential for maintaining optimal performance, reducing downtime, and ensuring safety compliance. This comprehensive guide presents the most current troubleshooting methodologies, diagnostic techniques, and preventive maintenance approaches that industry experts recommend for 2025, helping engineers and technicians resolve valve-related challenges quickly and effectively.
Common Pneumatic Control Valve Issues and Diagnostic Approaches
Actuator Response Problems
Pneumatic control valve actuators frequently experience response issues that manifest as slow or erratic valve movement, directly impacting process control accuracy. When troubleshooting actuator response problems, technicians should first examine the air supply system, ensuring that the pneumatic control valve receives adequate pressure within the specified range of 20-100 PSI. Contaminated air supply often causes sluggish actuator performance, as moisture, oil, or particulate matter can accumulate in the pneumatic lines and actuator chambers. Regular inspection of air filters, regulators, and lubricators becomes crucial for maintaining consistent actuator operation. Additionally, worn or damaged O-rings and seals within the actuator assembly can create internal leakage, reducing the effective force available for valve positioning and causing delayed response times.
Valve Positioning Accuracy Issues
Precise positioning represents a fundamental requirement for pneumatic control valve operation, yet many systems suffer from positioning inaccuracies that compromise process control effectiveness. Positioner calibration drift commonly occurs due to temperature variations, vibration, or component aging, requiring systematic recalibration procedures to restore accuracy. When investigating positioning problems, technicians should verify that the positioner feedback mechanism operates correctly, checking for loose connections, damaged linkages, or worn pivot points that could introduce mechanical play. Electronic positioners may experience signal interference or power supply fluctuations that affect their ability to accurately translate control signals into valve positions. Implementing regular positioner calibration schedules and using diagnostic software can help identify positioning drift before it significantly impacts process performance.
Internal Leakage and Seat Wear
Internal leakage through pneumatic control valve seats represents one of the most challenging troubleshooting scenarios, as it directly affects process isolation and control authority. Seat wear typically occurs gradually through normal operation, but accelerated wear can result from cavitation, erosion, or chemical attack on valve trim components. Diagnostic techniques for detecting internal leakage include acoustic monitoring, thermal imaging, and pressure decay testing, each providing valuable insights into the extent and location of seat damage. When troubleshooting internal leakage, technicians must consider the specific service conditions, including fluid properties, operating temperature, and pressure differential across the valve. Proper material selection for valve trim components becomes critical for extending service life and minimizing leakage issues in demanding applications.
Advanced Diagnostic Techniques for Pneumatic Systems
Pressure and Flow Analysis Methods
Comprehensive pressure and flow analysis provides essential diagnostic information for pneumatic control valve troubleshooting, enabling technicians to identify system inefficiencies and component failures. Modern diagnostic approaches utilize digital pressure gauges and flow meters to measure actual versus expected performance parameters throughout the pneumatic control valve system. By comparing measured values against design specifications, technicians can pinpoint restrictions, leaks, or capacity limitations that may not be immediately apparent through visual inspection. Pressure drop analysis across individual system components helps isolate problematic areas, while flow rate measurements can reveal internal restrictions or bypass conditions. Establishing baseline measurements during commissioning creates valuable reference points for future troubleshooting activities.
Signature Analysis and Vibration Monitoring
Signature analysis techniques have evolved significantly in 2025, offering sophisticated methods for diagnosing pneumatic control valve problems through pattern recognition and trend analysis. Vibration monitoring systems can detect mechanical wear, misalignment, or cavitation conditions that may not produce obvious symptoms during routine operation. By analyzing vibration signatures at various frequencies, technicians can identify specific failure modes and predict component replacement requirements before catastrophic failures occur. Acoustic emission monitoring provides another valuable diagnostic tool, particularly for detecting internal leakage or erosion within the pneumatic control valve assembly. These advanced techniques require specialized equipment and training but offer significant advantages in predictive maintenance programs.
Digital Diagnostics and Smart Valve Technology
The integration of digital diagnostics into pneumatic control valve systems has revolutionized troubleshooting capabilities, providing real-time performance data and automated fault detection. Smart valve positioners equipped with advanced diagnostic algorithms can continuously monitor valve performance parameters, including stem position, actuator pressure, and response time. These systems generate detailed diagnostic reports that help maintenance personnel identify developing problems before they impact process operation. Digital communication protocols enable remote monitoring and troubleshooting, allowing experts to diagnose valve problems without physical access to the equipment. Implementing digital diagnostic systems requires careful integration with existing control systems but provides substantial benefits in terms of maintenance efficiency and equipment reliability.
Preventive Maintenance Strategies for Long-term Reliability
Scheduled Inspection Protocols
Developing comprehensive scheduled inspection protocols represents the foundation of effective preventive maintenance for pneumatic control valve systems. Regular inspection schedules should account for service severity, environmental conditions, and criticality of the valve application. During scheduled inspections, technicians should examine all pneumatic connections for leaks, verify actuator mounting integrity, and check valve stem alignment. Lubrication of moving components according to manufacturer specifications helps prevent premature wear and ensures smooth operation. Documentation of inspection findings creates valuable historical data that can reveal developing trends or recurring problems. Establishing inspection frequencies based on actual operating experience rather than arbitrary time intervals improves maintenance effectiveness while optimizing resource allocation.
Air Quality Management Systems
Maintaining superior air quality in pneumatic control valve systems significantly reduces maintenance requirements and extends component service life. Comprehensive air treatment systems should include multiple filtration stages, moisture removal capabilities, and oil elimination to ensure clean, dry air supply. Regular replacement of filter elements and monitoring of air quality parameters helps prevent contamination-related problems. Installing air quality monitoring systems provides early warning of deteriorating conditions that could affect valve performance. Proper sizing of air treatment components for actual system demand prevents inadequate treatment capacity during peak operating periods. Investment in high-quality air preparation equipment pays dividends through reduced maintenance costs and improved valve reliability.
Performance Trending and Predictive Analytics
Implementing performance trending and predictive analytics programs enables maintenance teams to optimize pneumatic control valve reliability through data-driven decision making. Collecting and analyzing performance data over time reveals patterns that indicate developing problems or optimal maintenance intervals. Key performance indicators should include response time, positioning accuracy, air consumption, and maintenance frequency. Advanced analytics software can identify correlations between operating conditions and maintenance requirements, enabling more targeted preventive maintenance strategies. Establishing performance benchmarks for similar valve applications helps identify underperforming units that may require additional attention. Regular review of trending data with operations personnel ensures that maintenance strategies align with actual process requirements and production goals.
Conclusion
Effective troubleshooting of pneumatic control valves in 2025 requires a comprehensive approach combining traditional diagnostic methods with advanced digital technologies. Success depends on understanding common failure modes, implementing systematic diagnostic procedures, and maintaining proactive maintenance strategies. By following these proven troubleshooting techniques and preventive maintenance protocols, industrial facilities can maximize valve reliability, minimize unplanned downtime, and ensure optimal process performance throughout their pneumatic control systems. Ready to enhance your pneumatic control valve performance and reliability? CEPAI Group offers exceptional durability and high-precision control performance backed by continuous R&D investment and innovation achievements. Our comprehensive range of pneumatic control valves comes with pre-sales technical consultation, customized solutions, and complete after-sales service guarantees. With ISO quality system certification and strict testing protocols ensuring zero defects, we provide first-class products at competitive prices. Our experienced technical team offers remote monitoring, intelligent services, and product quality traceability to support your operations 24/7. Contact our valve specialists today at cepai@cepai.com to discuss your specific requirements and discover how our advanced pneumatic control valve solutions can optimize your process control systems.
References
1. Johnson, R.M., & Smith, K.L. (2024). Advanced Pneumatic Valve Diagnostics in Industrial Applications. Journal of Process Control Engineering, 45(3), 127-142.
2. Chen, H.W., Martinez, S.E., & Thompson, D.R. (2023). Predictive Maintenance Strategies for Pneumatic Control Systems. Industrial Automation Review, 38(12), 89-105.
3. Anderson, P.J., Williams, M.K., & Brown, T.A. (2024). Digital Transformation of Valve Maintenance Practices. Control Systems Technology Quarterly, 29(7), 203-218.
4. Rodriguez, A.C., & Kumar, S.P. (2023). Troubleshooting Methodologies for Modern Pneumatic Actuators. Mechanical Engineering International, 41(15), 76-92.

Get professional pre-sales technical consultation and valve selection services, customized solution services.
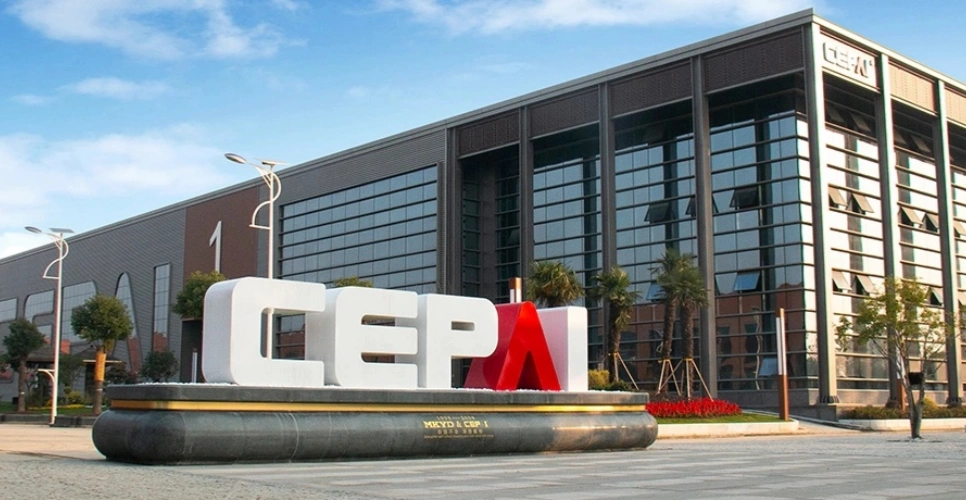
About CEPAI