Different Types of Control Valves: Key Features and Applications
In the complex landscape of industrial automation and process control, selecting the right Control Valve is crucial for maintaining optimal system performance, ensuring safety, and maximizing operational efficiency. Control valves serve as the final control elements in process control loops, regulating fluid flow, pressure, temperature, and level across diverse industrial applications. Understanding the different types of control valves, their unique features, and specific applications enables engineers and procurement professionals to make informed decisions that directly impact system reliability, maintenance costs, and overall plant productivity. This comprehensive guide explores the fundamental categories of control valves, examining their distinctive characteristics, operational principles, and the critical factors that determine their suitability for various industrial processes.
Essential Control Valve Categories and Their Operational Principles
Linear Motion Control Valves
Linear motion control valves represent one of the most widely utilized categories in industrial applications, characterized by their straight-line stem movement that directly controls the flow area through the valve seat. Globe valves stand as the most common type within this category, featuring a plug or disc that moves perpendicular to the seat to regulate flow. The Control Valve design of globe valves provides excellent throttling characteristics and precise flow control, making them ideal for applications requiring fine regulation and tight shutoff capabilities. Their inherent design allows for easy maintenance and repair, as the internal components can be accessed without removing the valve from the pipeline. The balanced plug design in modern globe Control Valve units minimizes the actuator force requirements, reducing operational costs and improving response times. Angle valves, another variant of linear motion Control Valve systems, offer similar control characteristics to globe valves but with a 90-degree flow path change. This design provides excellent flow characteristics for high-pressure drop applications and reduces the number of pipe fittings required in installations where direction changes are necessary. The streamlined flow path in angle Control Valve configurations minimizes pressure losses and reduces the potential for cavitation and flashing, making them particularly suitable for steam service and high-velocity fluid applications. Gate valves, while primarily designed for on-off service, can also function as Control Valve units in specific applications where full-bore flow and minimal pressure drop are critical requirements. Diaphragm valves utilize a flexible membrane to control flow, offering unique advantages in applications involving corrosive or contaminated fluids. The Control Valve mechanism in diaphragm valves provides complete isolation of the actuating mechanism from the process fluid, preventing contamination and eliminating the need for packing glands. This design makes diaphragm Control Valve systems particularly valuable in pharmaceutical, food processing, and chemical industries where product purity is paramount. The smooth flow path and absence of crevices in the valve body minimize the risk of bacterial growth and facilitate thorough cleaning and sterilization procedures.
Rotary Motion Control Valves
Rotary motion control valves operate through the rotation of a closure member, typically offering superior flow characteristics and reduced pressure drops compared to linear motion alternatives. Ball valves, featuring a spherical closure element with a through-hole, provide excellent flow capacity and minimal pressure loss when fully open. The Control Valve application of ball valves is particularly effective in situations requiring quick shutoff, high flow rates, and reliable sealing performance. The quarter-turn operation of ball Control Valve systems enables rapid response times and reduces actuator power requirements, making them cost-effective solutions for large-scale industrial installations. Butterfly valves represent another significant category of rotary Control Valve systems, utilizing a disc that rotates within the valve body to regulate flow. The compact design and lightweight construction of butterfly valves make them economical choices for large diameter applications where space and weight constraints are critical factors. Modern butterfly Control Valve designs incorporate advanced disc profiles and seat materials that provide reliable sealing and extended service life. The inherent flow characteristics of butterfly valves make them suitable for applications requiring proportional control, though their performance in high-pressure drop situations may require careful consideration of cavitation and choked flow conditions. Plug valves, featuring a cylindrical or tapered plug with a through-hole, offer robust construction and reliable performance in demanding industrial environments. The Control Valve functionality of plug valves provides excellent shutoff capabilities and can handle abrasive or viscous fluids that might cause problems for other valve types. Multi-port plug Control Valve configurations enable complex flow routing and mixing applications, making them valuable in process industries where multiple flow paths must be managed simultaneously. The simple mechanical design of plug valves contributes to their reliability and ease of maintenance, particularly in applications where frequent operation is required.
Specialized Control Valve Technologies
Pressure-reducing valves represent a specialized category of Control Valve systems designed to maintain downstream pressure at predetermined levels regardless of upstream pressure variations. These valves incorporate internal sensing mechanisms that automatically adjust the valve opening to compensate for pressure changes, providing stable downstream conditions without external control systems. The Control Valve technology in pressure-reducing applications often includes pilot-operated designs that enhance sensitivity and accuracy while reducing the main valve size requirements. Self-contained pressure Control Valve systems eliminate the need for external air supplies or electrical connections, making them ideal for remote installations or emergency applications. Temperature control valves utilize thermostatic elements or remote temperature sensors to regulate fluid flow based on temperature variations. These specialized Control Valve systems are essential in applications where temperature control is critical for product quality, process efficiency, or equipment protection. Three-way mixing valves, a common type of temperature Control Valve, blend hot and cold fluids to maintain desired temperature setpoints in heating, ventilation, and process cooling applications. The thermal response characteristics of these valves must be carefully matched to the application requirements to ensure stable control and prevent temperature oscillations. Safety relief valves, while primarily designed for overpressure protection, can also function as specialized Control Valve systems in certain applications. These valves incorporate spring-loaded or pilot-operated mechanisms that open at predetermined pressure levels to prevent equipment damage or personnel injury. The Control Valve principles applied in relief valve design ensure reliable operation under emergency conditions while minimizing leakage during normal operation. Advanced relief valve designs incorporate features such as balanced bellows assemblies and soft seat materials that enhance performance and extend service intervals.
Critical Selection Factors and Performance Optimization
Flow Characteristics and Sizing Considerations
The flow characteristics of a Control Valve define the relationship between valve opening and flow rate, directly impacting system stability and control performance. Linear flow characteristics provide a constant change in flow rate for each increment of valve opening, making them suitable for applications where the system pressure drop remains relatively constant. Equal percentage flow characteristics, where each increment of valve opening produces a percentage change in flow proportional to the current flow rate, are preferred for applications with variable system pressure drops or where wide rangeability is required. The selection of appropriate flow characteristics in Control Valve applications significantly influences the control loop's ability to maintain stable operation across varying process conditions. Proper sizing of Control Valve systems requires careful consideration of flow capacity, pressure drop, and cavitation potential. The valve flow coefficient (Cv) determines the valve's capacity to pass fluid under specific conditions, and accurate calculation of this parameter is essential for optimal performance. Oversized Control Valve installations may result in poor control characteristics and hunting behavior, while undersized valves may not provide adequate flow capacity or may operate near their maximum capacity, reducing control authority. The pressure recovery factor and critical pressure ratio for the specific Control Valve design must be considered to avoid cavitation damage and ensure reliable operation. Cavitation and flashing phenomena can severely impact Control Valve performance and longevity, particularly in liquid service applications with high pressure drops. Cavitation occurs when local pressure drops below the liquid's vapor pressure, causing vapor bubbles to form and subsequently collapse as pressure recovers. This process generates shock waves that can damage valve internals and create noise and vibration problems. Anti-cavitation Control Valve designs incorporate features such as staged pressure reduction, tortuous flow paths, and specialized trim materials to minimize cavitation effects and extend valve service life.
Material Selection and Environmental Compatibility
The selection of appropriate materials for Control Valve construction depends on the process fluid characteristics, operating temperature and pressure, and environmental conditions. Valve body materials must provide adequate strength and corrosion resistance while maintaining dimensional stability under operating conditions. Stainless steel grades such as 316L offer excellent corrosion resistance for most general applications, while exotic alloys like Hastelloy or Inconel may be required for highly corrosive or high-temperature services. The Control Valve trim materials, including the plug, seat, and cage components, require particular attention as they experience the most severe service conditions and directly impact valve performance and longevity. Elastomeric sealing materials in Control Valve applications must be compatible with the process fluid and operating temperature range while providing reliable sealing performance. PTFE-based materials offer excellent chemical compatibility and low friction characteristics, making them suitable for many Control Valve applications. However, temperature limitations and potential for cold flow must be considered when selecting PTFE seals. Graphite-based packing materials provide superior temperature resistance and are commonly used in high-temperature Control Valve applications, though they may require higher breakaway forces and more frequent maintenance. Environmental factors such as ambient temperature, humidity, and atmospheric corrosion can significantly impact Control Valve performance and maintenance requirements. Protective coatings and materials must be selected to withstand local environmental conditions while maintaining long-term reliability. Special consideration must be given to Control Valve installations in marine environments, chemical processing areas, or locations subject to extreme temperature variations. The selection of appropriate actuator materials and enclosures is equally important to ensure reliable operation under adverse environmental conditions.
Integration with Control Systems and Automation
Modern Control Valve systems must integrate seamlessly with distributed control systems (DCS) and programmable logic controllers (PLC) to provide optimal process control performance. Smart Control Valve positioners incorporate digital communication protocols such as HART, Foundation Fieldbus, or Profibus that enable advanced diagnostic capabilities and remote configuration. These intelligent devices provide real-time feedback on valve position, actuator performance, and potential maintenance issues, enabling predictive maintenance strategies and improved system reliability. The dynamic response characteristics of Control Valve systems significantly impact control loop performance and stability. Fast-acting valves may cause system instability or hunting in applications with slow process dynamics, while slow-responding valves may result in poor disturbance rejection and sluggish setpoint tracking. The proper matching of Control Valve response characteristics to process requirements involves consideration of process time constants, dead time, and control algorithm parameters. Advanced control strategies such as cascade control, feedforward control, or model predictive control may require specific Control Valve performance characteristics to achieve optimal results. Fail-safe considerations are critical in Control Valve applications where process safety or product quality could be compromised by valve failure. Fail-open, fail-closed, and fail-in-place strategies must be carefully evaluated based on the consequences of each failure mode. The Control Valve actuator and positioner must be designed to provide reliable fail-safe operation while maintaining the ability to resume normal operation after power restoration. Emergency shutdown systems may require specialized Control Valve designs with rapid closure capabilities and independent safety instrumented system (SIS) integration.
Conclusion
The selection and application of appropriate Control Valve technologies play a pivotal role in achieving optimal industrial process performance, safety, and reliability. Understanding the fundamental differences between linear and rotary motion valves, specialized applications, and critical selection criteria enables informed decision-making that directly impacts operational success. As industrial processes become increasingly complex and demanding, the importance of selecting the right Control Valve solution continues to grow, making comprehensive knowledge of available technologies and their applications essential for engineering professionals. Ready to optimize your process control systems with industry-leading Control Valve solutions? CEPAI Group combines exceptional durability, high-precision control performance, and comprehensive R&D innovation to deliver valve technologies that exceed industry standards. Our extensive product range, backed by rigorous ISO quality systems and international certifications, ensures reliable performance across diverse industrial applications. From pre-sales technical consultation and customized solutions to comprehensive after-sales support and remote monitoring services, our team of experts is committed to your operational success. With advanced testing equipment, strict quality control processes, and a dedication to achieving zero valve defects, CEPAI Group stands ready to meet your most demanding Control Valve requirements. Contact our technical specialists today at cepai@cepai.com to discuss your specific application needs and discover how our innovative valve solutions can enhance your process efficiency, reduce maintenance costs, and improve overall system reliability.
References
1. Baumann, H.D. (2019). Control Valve Engineering: Principles and Applications in Chemical Process Industries. Industrial Press Inc.
2. Emerson Process Management. (2018). Control Valve Handbook: Fifth Edition. Fisher Controls International LLC.
3. Hutchison, J.W. (2020). ISA Handbook of Control Valves: Design, Selection, and Application Standards. International Society of Automation.
4. Skousen, P.L. (2021). Valve Handbook: Third Edition - Control Valve Selection, Installation, and Maintenance. McGraw-Hill Professional.
_1745994738000.webp)
Get professional pre-sales technical consultation and valve selection services, customized solution services.
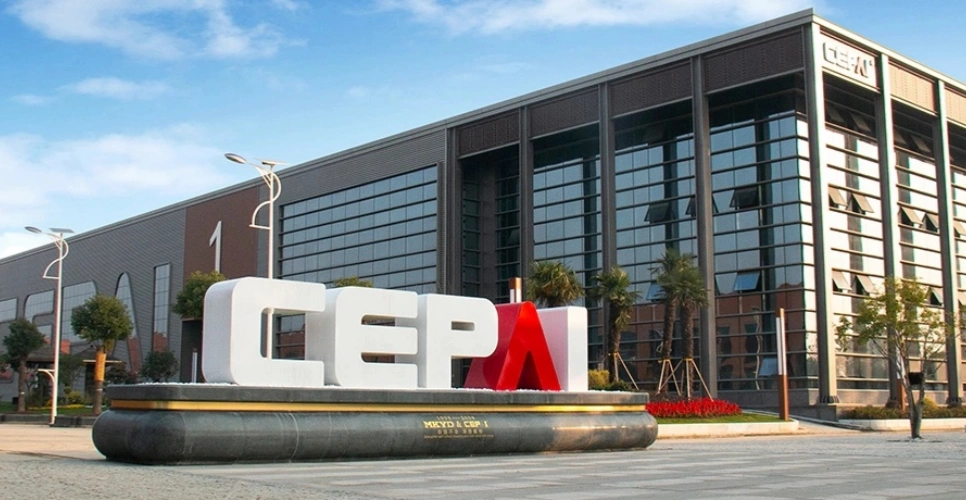
About CEPAI