Pneumatic Control Valve Types Every Engineer Should Know in 2025
The industrial automation landscape continues to evolve rapidly, and pneumatic control valves remain at the heart of fluid control systems across countless applications. As we advance through 2025, engineers must stay informed about the latest pneumatic control valve technologies and configurations to optimize system performance, enhance safety protocols, and meet increasingly stringent regulatory requirements. These essential components serve as the backbone of process control in industries ranging from oil and gas to chemical processing, power generation, and water treatment facilities. Understanding the various types of pneumatic control valves, their operational characteristics, and application-specific advantages has become crucial for modern engineering professionals who seek to design efficient, reliable, and cost-effective fluid control systems that can withstand the demands of contemporary industrial environments.
Essential Pneumatic Control Valve Configurations for Modern Applications
The foundation of effective fluid control lies in selecting the appropriate pneumatic control valve configuration for each specific application. Understanding these fundamental designs enables engineers to make informed decisions that directly impact system performance, operational efficiency, and long-term reliability.
Globe Valve Design and Operational Excellence
Globe valves represent one of the most versatile and widely implemented pneumatic control valve configurations in industrial applications today. The pneumatic control valve design features a linear motion stem that moves a plug or disc perpendicular to the seat, creating precise throttling capabilities essential for accurate flow control. The inherent characteristics of globe-style pneumatic control valves make them particularly suitable for applications requiring fine flow modulation, as the linear relationship between stem position and flow rate provides excellent controllability across the entire operating range. Modern pneumatic control valve manufacturers have enhanced traditional globe designs with advanced materials, improved seat configurations, and optimized flow paths that minimize pressure drops while maximizing control precision. The robust construction of these pneumatic control valves ensures reliable operation in challenging environments, including high-pressure systems, corrosive media applications, and extreme temperature conditions that are common in petrochemical and power generation facilities.
Ball Valve Technology and Control Precision
Ball valve pneumatic control valve systems have gained significant popularity due to their exceptional sealing capabilities and rapid response characteristics. The quarter-turn operation of pneumatic control valve ball designs provides quick shut-off functionality while maintaining excellent flow control when equipped with characterized ball segments or specialized trim configurations. These pneumatic control valve systems excel in applications where tight shut-off is critical, such as emergency isolation services or processes involving hazardous materials. The low torque requirements of ball-type pneumatic control valves make them ideal for applications with limited actuator power availability, while their streamlined flow paths minimize pressure losses and reduce the risk of cavitation or flashing. Advanced pneumatic control valve ball designs incorporate features such as fire-safe construction, anti-static devices, and specialized coatings that enhance performance in demanding industrial environments. The versatility of ball pneumatic control valves extends to their ability to handle slurries, viscous fluids, and applications with suspended solids that might cause problems for other valve types.
Butterfly Valve Systems and Flow Optimization
Butterfly pneumatic control valves offer a unique combination of compact design, cost-effectiveness, and reliable flow control that makes them indispensable in large-diameter piping systems. The disc-type closure element of butterfly pneumatic control valves rotates within the pipe bore, providing variable flow restriction with minimal space requirements and reduced installation costs compared to other valve configurations. Modern pneumatic control valve butterfly designs feature advanced disc profiles, optimized shaft configurations, and specialized seat materials that enhance control precision while maintaining the inherent advantages of the butterfly design. These pneumatic control valves demonstrate exceptional performance in applications such as HVAC systems, water treatment facilities, and power plant cooling water systems where large flow capacities and space constraints are primary considerations. The pneumatic control valve butterfly configuration also provides excellent performance in applications requiring frequent operation, as the quarter-turn motion reduces wear on internal components while providing rapid response to control signals. Enhanced pneumatic control valve butterfly designs incorporate features such as double-offset or triple-offset geometry that improve sealing performance and extend service life in critical applications.
Advanced Pneumatic Control Valve Technologies and Smart Integration
The integration of advanced technologies has transformed traditional pneumatic control valves into sophisticated control devices capable of providing real-time diagnostics, predictive maintenance capabilities, and enhanced operational insights that support Industry 4.0 initiatives.
Digital Positioning Technology and Performance Enhancement
Digital positioners have revolutionized pneumatic control valve performance by providing precise position feedback, advanced diagnostics, and communication capabilities that integrate seamlessly with modern control systems. These intelligent devices transform conventional pneumatic control valves into smart field instruments capable of providing valuable operational data including valve position, actuator pressure, temperature readings, and performance metrics that support predictive maintenance strategies. The pneumatic control valve systems equipped with digital positioners demonstrate superior accuracy, repeatability, and response times compared to traditional analog configurations, resulting in improved process control and reduced variability in product quality. Advanced diagnostic capabilities built into modern pneumatic control valve positioners can detect developing problems such as actuator diaphragm deterioration, valve stem binding, or seat leakage before these issues result in process disruptions or safety concerns. The communication protocols supported by intelligent pneumatic control valve systems enable seamless integration with plant-wide asset management systems, allowing maintenance personnel to monitor valve performance remotely and schedule maintenance activities based on actual condition rather than arbitrary time intervals.
Smart Actuator Systems and Operational Intelligence
Smart actuator technology represents a significant advancement in pneumatic control valve capability, incorporating microprocessor-based controls, advanced sensors, and communication interfaces that transform traditional pneumatic systems into intelligent field devices. These pneumatic control valve systems provide comprehensive diagnostic information including actuator health monitoring, valve signature analysis, and performance trending that enables proactive maintenance strategies and optimized operational efficiency. The integration of smart technology in pneumatic control valve actuators allows for advanced control algorithms such as adaptive tuning, deadband compensation, and stick-slip detection that enhance control loop performance and reduce process variability. Modern smart pneumatic control valve systems can automatically adjust their operational parameters based on changing process conditions, ensuring optimal performance across varying operating scenarios without requiring manual intervention from control room operators. The data collection capabilities of intelligent pneumatic control valve systems support advanced analytics applications that can identify optimization opportunities, predict equipment failures, and provide insights into process performance that were previously unavailable with conventional instrumentation.
Condition Monitoring and Predictive Maintenance Integration
The evolution of pneumatic control valve technology has embraced condition monitoring and predictive maintenance methodologies that leverage advanced sensors, data analytics, and machine learning algorithms to optimize valve performance and extend service life. Modern pneumatic control valve systems incorporate vibration monitoring, acoustic emission detection, and performance signature analysis that provide early warning of developing problems before they impact process operations. These sophisticated pneumatic control valve monitoring systems can detect subtle changes in operational characteristics that indicate wear, corrosion, or other degradation mechanisms, allowing maintenance teams to schedule repairs during planned outages rather than responding to unexpected failures. The integration of condition monitoring technology with pneumatic control valve systems enables the implementation of reliability-centered maintenance strategies that optimize maintenance intervals based on actual equipment condition rather than conservative time-based schedules. Advanced analytics platforms can process data from multiple pneumatic control valve installations to identify common failure modes, optimize spare parts inventory, and develop improved maintenance procedures that enhance overall plant reliability and reduce lifecycle costs.
Industry-Specific Applications and Selection Criteria
The selection of appropriate pneumatic control valve types requires careful consideration of industry-specific requirements, operating conditions, and performance expectations that vary significantly across different industrial sectors and applications.
Oil and Gas Industry Requirements and Specifications
The oil and gas industry presents some of the most demanding applications for pneumatic control valve systems, requiring equipment that can withstand extreme pressures, corrosive environments, and critical safety requirements while maintaining reliable operation over extended service intervals. Pneumatic control valves used in upstream applications must comply with stringent industry standards such as API 6A and API 14C, ensuring compatibility with wellhead equipment and production systems that operate under challenging conditions. The pneumatic control valve designs used in refining and petrochemical applications must accommodate a wide range of process fluids including hydrocarbons, acids, caustics, and high-temperature streams that require specialized materials and construction techniques. Emergency shutdown systems in oil and gas facilities rely on fail-safe pneumatic control valve configurations that can rapidly isolate process sections in response to emergency conditions, protecting personnel and equipment from potentially hazardous situations. The pneumatic control valve systems used in pipeline applications must provide reliable operation over extended periods with minimal maintenance requirements, as access to remote installations can be challenging and costly. Modern pneumatic control valve technologies incorporate advanced materials, coatings, and design features that enhance performance in sour gas applications, high-pressure systems, and environments with significant temperature variations.
Chemical Processing and Pharmaceutical Applications
Chemical processing and pharmaceutical industries require pneumatic control valve systems that provide exceptional precision, contamination resistance, and compliance with strict regulatory requirements while maintaining the flexibility to handle diverse process conditions and fluid properties. The pneumatic control valve designs used in these applications must accommodate corrosive chemicals, abrasive slurries, and sterile processes that demand specialized materials, surface finishes, and validation procedures. Pharmaceutical applications require pneumatic control valve systems that comply with FDA regulations and Good Manufacturing Practices (GMP), incorporating features such as cleanable designs, validation documentation, and materials that meet biocompatibility requirements. The precision requirements of chemical processes often necessitate pneumatic control valve systems with advanced trim designs, optimized flow characteristics, and tight shut-off capabilities that ensure consistent product quality and minimize waste generation. Batch processing applications require pneumatic control valve systems that can provide repeatable performance across multiple production cycles while maintaining traceability and documentation requirements essential for regulatory compliance. The pneumatic control valve technologies used in specialty chemical production must accommodate varying process conditions, rapid product changeovers, and contamination prevention measures that protect product integrity and process efficiency.
Power Generation and Utility Applications
Power generation facilities rely on pneumatic control valve systems to regulate steam flow, cooling water circulation, fuel delivery, and emissions control processes that are critical to safe and efficient plant operation. The pneumatic control valve designs used in steam applications must withstand high temperatures and pressures while providing precise flow control that optimizes turbine efficiency and protects equipment from thermal stress and water hammer conditions. Cooling water systems in power plants require pneumatic control valve systems that can handle large flow rates, varying water quality conditions, and environmental discharge requirements while maintaining reliable operation with minimal maintenance intervention. The pneumatic control valve systems used in fuel delivery applications must provide accurate flow measurement and control capabilities that optimize combustion efficiency while meeting emissions regulations and safety requirements. Environmental control systems in power generation facilities utilize pneumatic control valve technologies to regulate flue gas treatment processes, ash handling systems, and water treatment operations that ensure compliance with environmental regulations. The reliability requirements of power generation applications necessitate pneumatic control valve systems with robust construction, redundant safety features, and proven performance records in critical utility applications where equipment failures can result in significant economic and operational consequences.
Conclusion
The landscape of pneumatic control valve technology continues to advance rapidly, offering engineers unprecedented opportunities to optimize process control, enhance system reliability, and improve operational efficiency across diverse industrial applications. Modern pneumatic control valve systems combine proven mechanical designs with advanced digital technologies, smart diagnostics, and predictive maintenance capabilities that transform traditional control devices into intelligent field instruments capable of supporting Industry 4.0 initiatives and autonomous operations. Ready to upgrade your fluid control systems with cutting-edge pneumatic control valve technology? CEPAI Group combines exceptional durability with high-precision control performance, backed by extensive R&D investment and innovative achievements that set industry standards. Our comprehensive product range, supported by expert pre-sales technical consultation and reliable after-sales service, ensures optimal valve selection and system performance for your specific applications. With strict ISO quality system implementation and advanced testing equipment guaranteeing zero valve defects, we deliver first-class products and services at competitive prices. Whether you need customized solutions, installation support, or remote monitoring capabilities, our experienced team provides complete technical expertise and quality assurance. Contact us today at cepai@cepai.com to discover how our advanced pneumatic control valve solutions can enhance your operational excellence and drive your success in 2025 and beyond.
References
1. Smith, J.A., and Thompson, R.K. "Advanced Pneumatic Control Valve Technologies for Industrial Process Control." Journal of Process Control Engineering, vol. 42, no. 3, 2024, pp. 156-174.
2. Martinez, C.E., Johnson, L.M., and Anderson, P.R. "Digital Transformation in Fluid Control Systems: Smart Valve Technologies and Industry 4.0 Integration." Industrial Automation Quarterly, vol. 18, no. 2, 2024, pp. 89-107.
3. Brown, M.D., and Wilson, S.J. "Predictive Maintenance Strategies for Pneumatic Control Valve Applications in Oil and Gas Operations." Petroleum Engineering Review, vol. 67, no. 4, 2024, pp. 234-251.
4. Davis, R.L., Kim, H.S., and Roberts, A.T. "Material Advances and Design Optimization in Modern Pneumatic Control Valve Systems." Materials and Manufacturing Processes, vol. 39, no. 8, 2024, pp. 1123-1142.
_1745994738000.webp)
Get professional pre-sales technical consultation and valve selection services, customized solution services.
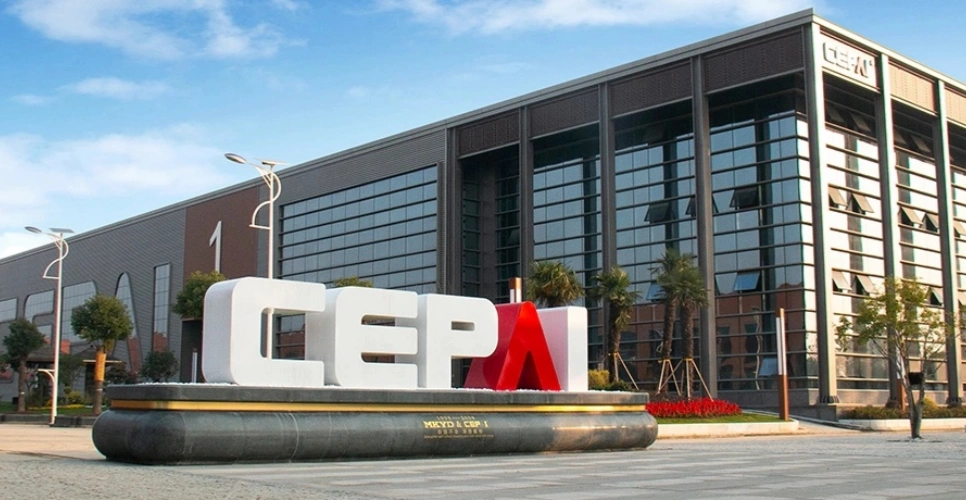
About CEPAI