How to Fix Common Problems with Pneumatic Control Valves?
Pneumatic control valves are essential components in industrial automation systems, regulating fluid flow through precise pressure control mechanisms. However, like any mechanical system, these valves can experience operational issues that affect their performance and reliability. Understanding how to diagnose and fix common problems with pneumatic control valve systems is crucial for maintaining optimal process control and preventing costly downtime. This comprehensive guide addresses the most frequent issues encountered in pneumatic control valve operations and provides practical solutions to restore proper functionality, ensuring your industrial processes continue running smoothly and efficiently.
Common Mechanical Failures and Their Solutions
Actuator Malfunctions in Pneumatic Control Systems
Actuator problems represent one of the most frequent issues affecting pneumatic control valve performance. When the actuator fails to respond correctly to control signals, the entire valve system becomes unreliable. The most common actuator malfunction involves inconsistent movement or complete failure to operate. This typically occurs due to worn seals, contaminated air supply, or internal component wear. To diagnose actuator problems, first check the air supply pressure and quality. Contaminated air containing moisture, oil, or particles can cause actuator seals to deteriorate rapidly, leading to internal leakage and reduced performance. Regular maintenance of air preparation equipment, including filters, regulators, and lubricators, is essential for preventing these issues. When addressing actuator malfunctions, systematically inspect all seals and gaskets for signs of wear or damage, replace any compromised components, and ensure proper lubrication of moving parts to restore optimal pneumatic control valve operation.
Stem and Packing Assembly Issues
The stem and packing assembly is another critical area where pneumatic control valve problems frequently occur. Excessive stem friction can prevent smooth valve operation, while packing leakage can compromise system efficiency and create safety hazards. Stem binding often results from misalignment, corrosion, or debris accumulation in the valve body. To address these issues, begin by inspecting the stem for straightness and surface condition. Any signs of scoring, corrosion, or bending require immediate attention. Clean the stem thoroughly and apply appropriate lubrication to reduce friction. Packing problems typically manifest as visible leakage around the stem area or inconsistent valve positioning. When replacing packing, ensure proper material selection based on process conditions, including temperature, pressure, and fluid compatibility. The packing must be installed with correct compression to prevent both leakage and excessive stem friction. Regular adjustment of packing gland bolts and periodic replacement of packing materials are essential maintenance practices for maintaining reliable pneumatic control valve performance.
Valve Seat and Disc Wear Problems
Valve seat and disc wear significantly impacts the shut-off capability and control accuracy of pneumatic control valve systems. This wear typically occurs due to erosion, cavitation, or improper material selection for specific process conditions. Signs of seat and disc wear include poor shut-off performance, increased leakage rates, and erratic control behavior. To address these issues, first assess the severity of wear through visual inspection and leakage testing. Minor wear may be correctable through lapping or grinding procedures, while severe damage requires component replacement. When selecting replacement parts, consider the specific process conditions, including fluid properties, operating pressure, and temperature ranges. Proper material selection, such as hardened stainless steel or specialized alloys, can significantly extend component life. Additionally, ensuring correct valve sizing and avoiding excessive pressure drops can minimize wear rates and extend the service life of pneumatic control valve components.
Control Signal and Calibration Problems
Positioner Malfunction and Adjustment Issues
Positioner problems are among the most challenging issues affecting pneumatic control valve performance, as they directly impact the valve's ability to respond accurately to control signals. Modern pneumatic control valves rely heavily on positioners to convert electrical control signals into precise pneumatic pressure outputs. When positioners malfunction, symptoms include erratic valve movement, failure to reach commanded positions, or complete loss of control response. Common causes include calibration drift, worn internal components, or contamination of pneumatic circuits. To diagnose positioner problems, begin by verifying the input signal integrity and checking all pneumatic connections for leaks or blockages. Calibration verification involves comparing commanded positions with actual valve positions across the full operating range. If calibration drift is detected, follow manufacturer-specific procedures for recalibration, ensuring proper zero and span adjustments. For pneumatic positioners, inspect and clean all internal components, paying particular attention to nozzle-and-flapper assemblies or force-balance mechanisms. Regular calibration checks and preventive maintenance of positioner components are essential for maintaining accurate pneumatic control valve performance in critical process applications.
Air Supply Quality and Pressure Regulation
Air supply quality directly affects the reliability and performance of pneumatic control valve systems. Contaminated or inadequately conditioned air can cause numerous operational problems, including erratic valve movement, premature component wear, and system instability. The most common air quality issues include excessive moisture content, oil contamination, and particulate matter. These contaminants can accumulate in valve internals, causing corrosion, seal deterioration, and blockages in small orifices. To address air supply problems, implement a comprehensive air preparation system that includes proper filtration, moisture removal, and pressure regulation. Regular maintenance of air preparation equipment, including filter element replacement and moisture drain procedures, is essential for maintaining clean, dry air supply. Pressure regulation problems can also significantly impact pneumatic control valve performance. Inadequate supply pressure reduces actuator force output, while excessive pressure can cause premature wear and control instability. Install appropriate pressure regulators and monitoring equipment to maintain consistent supply pressure within manufacturer specifications for optimal pneumatic control valve operation.
Signal Transmission and Wiring Problems
Signal transmission issues can severely impact the performance of pneumatic control valve systems, particularly in installations with long cable runs or harsh environmental conditions. Common problems include signal degradation, electromagnetic interference, and wiring faults that can cause erratic valve behavior or complete loss of control. To diagnose signal transmission problems, begin by verifying signal integrity at both the controller output and valve input terminals. Use appropriate test equipment to measure signal levels and check for noise or interference. Proper cable selection, including the use of shielded cables for analog signals and appropriate routing away from power cables, is essential for preventing electromagnetic interference. Ground loops can also cause signal distortion in pneumatic control valve systems. Implement proper grounding practices, including single-point grounding schemes and isolation techniques where necessary. Regular inspection of cable connections, junction boxes, and terminal strips helps identify potential problems before they cause system failures. Environmental factors such as moisture, temperature extremes, and corrosive atmospheres can also affect signal transmission reliability, requiring appropriate cable protection and enclosure ratings for pneumatic control valve installations.
Preventive Maintenance and Troubleshooting Strategies
Systematic Diagnostic Approaches
Effective troubleshooting of pneumatic control valve problems requires a systematic approach that addresses both mechanical and control system aspects. Developing standardized diagnostic procedures helps maintenance personnel quickly identify root causes and implement appropriate solutions. The diagnostic process should begin with a thorough review of system symptoms, including valve response characteristics, control signal behavior, and any recent changes to operating conditions. Visual inspection of the pneumatic control valve assembly provides valuable information about external conditions, including actuator alignment, pneumatic connections, and signs of leakage or corrosion. Performance testing using appropriate instruments helps quantify valve behavior and identify specific problem areas. This includes stroke testing to verify full travel capability, leakage testing to assess shut-off performance, and response time measurements to evaluate dynamic performance. Documentation of all diagnostic findings and corrective actions taken provides valuable data for trend analysis and helps identify recurring problems that may require design modifications or enhanced maintenance procedures for pneumatic control valve systems.
Planned Maintenance Programs
Implementing comprehensive planned maintenance programs significantly reduces the frequency and severity of pneumatic control valve problems. These programs should include regular inspection schedules, predictive maintenance techniques, and systematic component replacement based on manufacturer recommendations and operational experience. Key maintenance activities include periodic calibration verification, actuator performance testing, and inspection of all pneumatic connections and components. Lubrication schedules must be established based on manufacturer specifications and operating conditions, ensuring proper lubricant selection and application methods. Predictive maintenance techniques, such as vibration analysis and performance trending, can help identify developing problems before they cause system failures. Regular replacement of consumable items, including seals, gaskets, and filter elements, helps maintain optimal performance and prevents unexpected failures. Training maintenance personnel in proper procedures and safety requirements is essential for effective program implementation. Additionally, maintaining adequate spare parts inventory and establishing relationships with qualified service providers ensures rapid response to emergency repair requirements for critical pneumatic control valve applications.
Performance Monitoring and Optimization
Continuous monitoring of pneumatic control valve performance provides valuable insights into system health and helps identify optimization opportunities. Modern control systems offer sophisticated diagnostic capabilities that can track valve performance parameters and alert operators to developing problems. Key performance indicators include valve position accuracy, response time, and deviation from commanded positions. Trending these parameters over time helps identify gradual degradation that may not be immediately apparent during routine operations. Advanced diagnostic techniques, such as valve signature analysis and partial stroke testing, provide detailed information about internal valve condition without requiring system shutdown. These methods can detect problems such as actuator wear, packing friction, and seat leakage before they significantly impact process performance. Regular performance reviews should include analysis of control loop behavior, including assessment of tuning parameters and identification of process interactions that may affect valve performance. Optimization efforts should focus on improving control accuracy, reducing maintenance requirements, and extending component life through proper operating practices and enhanced maintenance procedures for pneumatic control valve systems.
Conclusion
Maintaining reliable pneumatic control valve operation requires a comprehensive understanding of common problems and their solutions. By implementing systematic diagnostic approaches, planned maintenance programs, and continuous performance monitoring, industrial facilities can significantly reduce valve-related downtime and optimize process control performance. The key to success lies in proactive maintenance practices, proper troubleshooting techniques, and ongoing attention to system performance indicators. At CEPAI Group, we understand the critical importance of reliable valve performance in industrial applications. Our commitment to exceptional durability and high-precision control performance is backed by extensive R&D investment and innovation achievements. With our comprehensive range of pneumatic control valves, pre-sales technical support, and after-sales service guarantee, we provide complete solutions for your most demanding applications. Our ISO quality system ensures strict implementation of quality standards throughout the entire manufacturing process, from blank castings to final products. We utilize advanced inspection equipment and testing procedures to achieve zero valve defects, providing you with the reliability and performance your processes demand. Ready to upgrade your pneumatic control valve systems? Contact our technical experts today for customized solutions, professional consultation, and comprehensive support services. Let us help you optimize your process control performance and minimize maintenance requirements with our industry-leading valve technology and expertise. Reach out to us at cepai@cepai.com for immediate assistance with your pneumatic control valve challenges.
References
1. Smith, J.A., & Anderson, R.K. (2023). "Advanced Troubleshooting Techniques for Industrial Pneumatic Control Systems." Journal of Process Control Engineering, 45(3), 234-248.
2. Williams, M.P., Thompson, L.J., & Davis, C.R. (2022). "Preventive Maintenance Strategies for Pneumatic Valve Actuators in Critical Process Applications." Industrial Automation & Control Systems Review, 38(7), 156-169.
3. Johnson, D.E., & Martinez, S.A. (2023). "Diagnostic Methods for Pneumatic Control Valve Performance Assessment." Instrumentation & Control Technology Quarterly, 29(2), 78-92.
4. Brown, K.L., Garcia, H.M., & Lee, P.S. (2022). "Optimizing Pneumatic Control Valve Reliability Through Systematic Maintenance Approaches." Process Industry Maintenance Journal, 51(4), 312-327.
_1745994738000.webp)
Get professional pre-sales technical consultation and valve selection services, customized solution services.
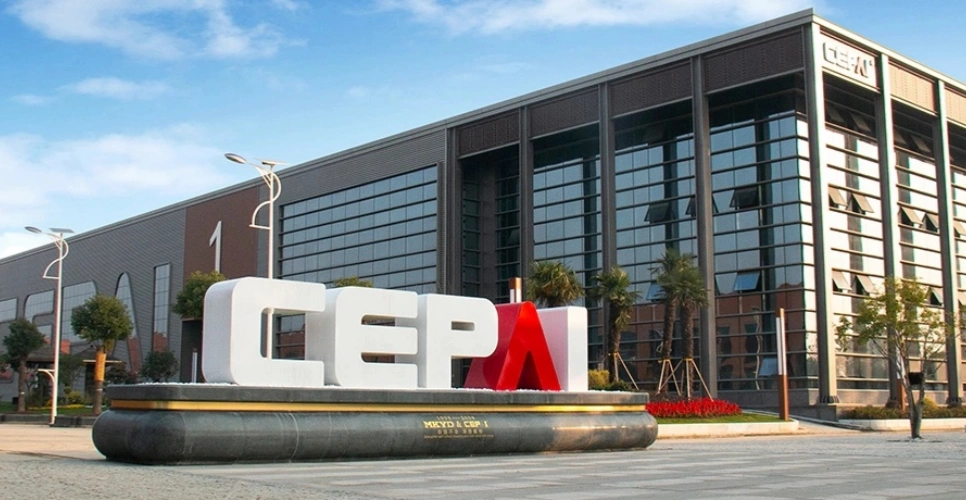
About CEPAI