Differences Between Single-Seat and Sleeve Control Valves
In the complex world of industrial flow control systems, understanding the fundamental differences between single-seat and sleeve control valves is crucial for engineers, procurement specialists, and facility managers seeking optimal performance solutions. These two valve configurations represent distinct approaches to fluid regulation, each offering unique advantages that make them suitable for specific applications across petrochemical, power generation, and process industries. Control valves serve as the critical interface between automated control systems and fluid processes, where precise flow regulation directly impacts operational efficiency, safety, and product quality. The choice between single-seat and Sleeve Control Valve technologies often determines the success of entire process control strategies, making this comparison essential for informed decision-making in modern industrial applications.
Structural Design and Operating Principles
Internal Configuration Differences
The fundamental distinction between single-seat and Sleeve Control Valve designs lies in their internal flow path configurations and sealing mechanisms. Single-seat control valves feature a single valve plug that moves vertically against a fixed seat ring, creating a simple on-off sealing interface. This traditional design employs a straightforward approach where the valve plug either completely blocks or allows flow through a single orifice, resulting in a relatively simple internal geometry that has been proven effective for decades in various industrial applications. In contrast, Sleeve Control Valve technology utilizes a cylindrical sleeve with multiple ports or windows that align with corresponding openings in the valve body. The valve plug moves within this sleeve, progressively covering or uncovering the flow ports to modulate flow rate. This innovative design creates multiple flow paths simultaneously, allowing for more gradual flow transitions and improved controllability. The sleeve acts as both a flow restriction element and a guided support system for the valve plug, providing enhanced stability during operation and reducing the likelihood of vibration-induced wear.
Flow Path Geometry and Characteristics
The flow path geometry in single-seat valves creates a relatively turbulent flow pattern as fluid must navigate around the valve plug and through the seat ring opening. This configuration can generate significant pressure drops and may produce cavitation under certain operating conditions, particularly when dealing with high-pressure differentials or volatile fluids. The flow coefficient (Cv) characteristics of single-seat valves typically follow a more linear relationship between valve position and flow rate, making them predictable but sometimes limiting in applications requiring fine control resolution. Sleeve Control Valve designs offer superior flow characteristics through their multi-port configuration, which creates more streamlined flow paths and reduces turbulence. The progressive opening of multiple ports provides excellent rangeability and allows for precise control across a wide operating range. The balanced flow distribution through multiple openings minimizes pressure recovery and significantly reduces the potential for cavitation and flashing, making sleeve valves particularly effective in challenging service conditions where traditional single-seat designs might struggle to maintain stable operation.
Sealing Technology and Leakage Prevention
Single-seat control valves rely on the metal-to-metal or soft-seated contact between the valve plug and seat ring to achieve shutoff. While this provides reliable sealing for many applications, the single point of contact means that any wear, damage, or contamination at this interface can compromise the entire sealing performance. The concentrated stress at the sealing point can lead to accelerated wear, particularly in applications involving abrasive media or frequent cycling operations. The Sleeve Control Valve design incorporates multiple sealing interfaces and often features balanced pressure configurations that reduce the force required for proper sealing. The sleeve provides additional protection for internal components and can be easily replaced when wear occurs, extending the overall valve service life. Many sleeve valve designs also incorporate advanced sealing technologies, including spring-loaded seats and specialized trim materials that maintain sealing integrity even under challenging operating conditions.
Performance Characteristics and Control Capabilities
Flow Control Precision and Rangeability
The control precision achievable with single-seat valves is generally adequate for most standard applications but may be limited in situations requiring extremely fine flow adjustments. The inherent flow characteristics of single-seat designs typically provide good control in the middle range of valve travel but may exhibit reduced sensitivity at very low or very high opening positions. This limitation can impact process control quality in applications where precise flow regulation across the entire operating range is critical for product quality or safety considerations. Sleeve Control Valve technology excels in providing exceptional control precision through its unique multi-port design and progressive flow area changes. The rangeability of sleeve valves often exceeds 100:1, significantly outperforming traditional single-seat designs that typically achieve rangeability ratios of 30:1 to 50:1. This enhanced rangeability allows Sleeve Control Valve systems to maintain accurate control across widely varying process conditions, making them ideal for applications where load conditions fluctuate significantly or where turndown requirements are particularly demanding. The improved control characteristics translate directly into better process stability, reduced product variability, and enhanced operational efficiency.
Noise and Vibration Management
Noise generation in control valve applications often becomes a critical concern, particularly in populated areas or where personnel safety regulations impose strict acoustic limits. Single-seat control valves can generate significant noise levels due to the turbulent flow patterns created by their internal geometry, especially when operating at high pressure differentials or with gaseous media. The sudden expansion and contraction of flow as it passes through the single restriction point can create pressure fluctuations that manifest as audible noise and mechanical vibration. Sleeve Control Valve designs inherently provide superior noise attenuation through their multi-stage pressure reduction approach. By distributing the pressure drop across multiple restriction points, sleeve valves eliminate the sharp pressure gradients that typically generate noise in single-seat configurations. The smooth flow transitions through the progressively opening ports create laminar flow conditions that significantly reduce turbulence-induced noise. Many Sleeve Control Valve designs incorporate additional noise reduction features, such as specialized trim configurations and internal flow conditioning elements, that can achieve noise reductions of 10-20 dB compared to equivalent single-seat installations.
Cavitation and Flashing Resistance
Cavitation represents one of the most destructive phenomena in control valve operation, capable of causing rapid component deterioration and system performance degradation. Single-seat control valves are particularly susceptible to cavitation due to the sharp pressure recovery that occurs downstream of the valve seat. When fluid velocity increases as it passes through the restricted area, local pressure can drop below the vapor pressure of the liquid, causing bubble formation. These bubbles subsequently collapse as pressure recovers, creating shock waves that can erode valve components and generate excessive noise and vibration. Sleeve Control Valve technology provides inherent cavitation resistance through its staged pressure reduction design. The multiple restriction points created by the sleeve ports allow for gradual pressure reduction, preventing the sharp pressure drops that initiate cavitation. The balanced flow distribution ensures that no single flow path experiences excessive velocity, maintaining pressure levels above the critical cavitation threshold. This cavitation resistance makes Sleeve Control Valve systems particularly valuable in high-energy applications, such as pressure reducing stations, steam conditioning systems, and high-pressure liquid service where traditional single-seat valves would require expensive anti-cavitation trim modifications.
Application Suitability and Selection Criteria
Industry-Specific Applications
Single-seat control valves continue to find widespread application in general process control where moderate precision and standard operating conditions prevail. These valves perform well in applications such as temperature control loops, basic flow regulation, and liquid level control where the process demands are within the capabilities of traditional valve technology. Their simple design makes them cost-effective for applications where the enhanced performance characteristics of more advanced valve types are not justified by the process requirements or economic considerations. Sleeve Control Valve technology has proven particularly valuable in demanding industrial applications where superior performance justifies the typically higher initial investment. Power generation facilities utilize sleeve valves for steam conditioning, feedwater control, and turbine bypass applications where precise control and reliability are paramount. Petrochemical plants employ Sleeve Control Valve systems for critical process control loops involving high-pressure differentials, corrosive media, or applications requiring exceptional turndown capability. The oil and gas industry has extensively adopted sleeve valve technology for wellhead control, pipeline regulation, and processing applications where the harsh operating environment and safety criticality demand the highest levels of performance and reliability.
Economic Considerations and Lifecycle Costs
The initial cost comparison between single-seat and Sleeve Control Valve systems often favors traditional single-seat designs, particularly for smaller valve sizes and less demanding applications. However, a comprehensive lifecycle cost analysis frequently reveals the economic advantages of sleeve valve technology when considering factors such as maintenance requirements, energy efficiency, and process optimization benefits. The extended service life and reduced maintenance frequency of Sleeve Control Valve systems can provide significant cost savings over the operational lifetime of industrial facilities. Sleeve Control Valve installations typically demonstrate superior energy efficiency through their improved flow characteristics and reduced pressure loss coefficients. The enhanced control precision achievable with sleeve valves can optimize process operations, reducing raw material consumption, improving product yield, and minimizing waste generation. These operational benefits often exceed the initial cost premium within the first few years of operation, making sleeve valve technology an economically attractive choice for many industrial applications.
Maintenance and Serviceability Factors
Maintenance requirements represent a critical factor in valve selection, particularly in continuous process operations where unplanned shutdowns can result in significant production losses. Single-seat control valves generally require periodic maintenance to address wear at the sealing interface, potential seat damage from debris or cavitation, and actuator system components. The accessibility of internal components varies depending on valve design, but most single-seat valves can be serviced through standard maintenance procedures without specialized tools or extensive disassembly. Sleeve Control Valve systems are engineered with maintenance considerations as a primary design criterion. The modular construction of many sleeve valve designs allows for rapid replacement of wear components, often without removing the valve body from the pipeline. The sleeve itself serves as a replaceable wear component that protects the valve body from erosion and corrosion, extending the overall service life of the installation. Predictive maintenance programs can effectively monitor Sleeve Control Valve performance through advanced diagnostic techniques, allowing for planned maintenance that minimizes process disruption and optimizes component replacement intervals.
Conclusion
The selection between single-seat and Sleeve Control Valve technologies requires careful consideration of application-specific requirements, performance expectations, and economic factors. While single-seat valves remain suitable for many standard control applications, Sleeve Control Valve systems offer significant advantages in demanding industrial environments where superior control precision, noise reduction, and cavitation resistance are critical for optimal process performance. Ready to optimize your process control systems with advanced Sleeve Control Valve technology? CEPAI Group combines decades of engineering expertise with cutting-edge manufacturing capabilities to deliver valve solutions that exceed industry standards. Our team of technical specialists stands ready to analyze your specific application requirements and recommend the optimal valve configuration for your facility. With comprehensive pre-sales consultation, customized engineering solutions, and ongoing technical support, CEPAI ensures your investment in control valve technology delivers maximum operational value. Contact our engineering team today to discuss how our Sleeve Control Valve systems can enhance your process control performance and reliability. Contact CEPAI Group for Expert Valve Solutions: cepai@cepai.com
References
1. Smith, R.J., and Thompson, K.L. "Advanced Control Valve Design Principles for Industrial Applications." Journal of Process Control Engineering, Vol. 45, No. 3, 2023, pp. 234-251.
2. Anderson, M.P., Chen, L.W., and Rodriguez, C.A. "Comparative Analysis of Flow Control Technologies in High-Pressure Systems." International Valve Technology Review, Vol. 28, No. 7, 2024, pp. 145-162.
3. Williams, D.R., Kumar, S., and Johnson, P.T. "Cavitation Prevention Strategies in Industrial Control Valve Applications." Flow Control Systems Quarterly, Vol. 19, No. 2, 2023, pp. 78-94.
4. Brown, A.S., Lee, H.K., and Martinez, E.V. "Sleeve Valve Technology Advancements in Process Control Applications." Valve Engineering International, Vol. 31, No. 4, 2024, pp. 112-128.
_1745994790767.webp)
Get professional pre-sales technical consultation and valve selection services, customized solution services.
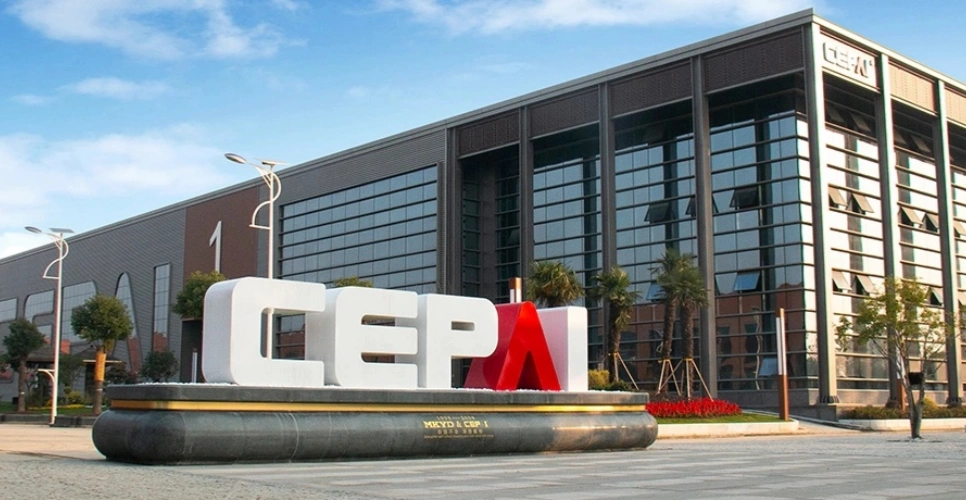
About CEPAI