Step-by-Step Instructions for Pneumatic Control Valve Setup and Care
Proper installation, configuration, and maintenance of pneumatic control valves are critical factors that determine the efficiency, safety, and longevity of industrial automation systems. This comprehensive guide provides detailed step-by-step instructions for pneumatic control valve setup and care, covering everything from initial installation procedures to advanced maintenance protocols. Understanding these processes ensures optimal performance, reduces operational costs, and maximizes system reliability across various industrial applications including oil and gas, petrochemical, power generation, and water treatment facilities.
Initial Installation and Configuration Procedures
Pre-Installation Assessment and Planning
Before beginning any pneumatic control valve installation, conducting a thorough pre-installation assessment is essential for ensuring successful implementation. The assessment process involves evaluating system requirements, environmental conditions, and compatibility factors that directly impact pneumatic control valve performance. Start by reviewing the process flow diagrams, piping and instrumentation drawings, and specifications to understand the exact role the pneumatic control valve will play within the overall system architecture. Examine the pipeline conditions including fluid properties, temperature ranges, pressure ratings, and flow characteristics to ensure the selected valve meets operational demands. Environmental factors such as ambient temperature variations, humidity levels, potential corrosive atmospheres, and vibration sources must be carefully evaluated as these conditions significantly influence pneumatic control valve longevity and reliability. Additionally, verify that adequate space exists for valve installation, actuator mounting, and future maintenance access while ensuring compliance with relevant safety codes and industry standards.
Mechanical Installation and Mounting
The mechanical installation phase requires precise attention to detail to ensure proper pneumatic control valve alignment and secure mounting within the pipeline system. Begin by preparing the pipeline connection points, ensuring that flange faces are clean, properly machined, and free from defects that could compromise sealing integrity. Install the pneumatic control valve body using appropriate gaskets and bolt torque specifications as recommended by the manufacturer, paying careful attention to bolt pattern alignment and sequential tightening procedures to achieve uniform stress distribution. Mount the pneumatic actuator to the valve body using the manufacturer-specified mounting hardware, ensuring proper alignment between the actuator output shaft and valve stem to prevent binding or excessive wear during operation. Install all necessary accessories including positioners, limit switches, solenoid valves, and air filter regulators in accordance with their respective installation guidelines. Verify that all mechanical connections are secure and that the valve assembly operates smoothly through its full range of motion without interference or binding.
Pneumatic System Connection and Testing
Establishing proper pneumatic connections and conducting comprehensive testing procedures are crucial steps in pneumatic control valve commissioning that directly impact system performance and safety. Connect the instrument air supply lines to the actuator using appropriate fittings and tubing materials rated for the operating pressure and environmental conditions. Install air filter regulators upstream of the actuator to ensure clean, dry air supply at the correct pressure levels, typically ranging from 15 to 30 PSI depending on actuator specifications. Connect the control signal lines from the process control system to the valve positioner, ensuring proper signal wiring and grounding to prevent electrical interference. Perform initial pneumatic testing by gradually applying air pressure while monitoring actuator response and valve position feedback. Conduct stroke testing to verify full valve travel range and proper fail-safe operation in case of air supply failure. Test all safety systems including emergency shutdown functions and verify that limit switches operate correctly throughout the valve's range of motion.
Calibration and Performance Optimization
Signal Calibration and Positioner Setup
Accurate signal calibration and proper positioner configuration are fundamental requirements for achieving precise pneumatic control valve performance in automated process control applications. Begin the calibration process by connecting calibrated test equipment including pressure gauges, signal generators, and digital multimeters to verify the accuracy of all measurement devices. Set the control signal input range typically 4-20 mA or 3-15 PSI according to the process control system specifications and valve positioner requirements. Adjust the positioner zero and span settings to ensure the pneumatic control valve responds accurately to control signals throughout the entire operating range. Perform linearity checks at multiple points across the signal range to verify proportional response between input signals and valve position. Fine-tune the positioner gain settings to optimize response time while maintaining stability and preventing oscillation or hunting behavior that can reduce valve life and process control quality.
Flow Characterization and Sizing Verification
Flow characterization and sizing verification ensure that the pneumatic control valve provides the required flow control performance across all operating conditions encountered in the specific application. Conduct flow testing using calibrated flow measurement devices to verify that the installed valve meets the calculated flow coefficient (Cv) values specified during the design phase. Test the valve's flow characteristics at various opening positions to confirm the relationship between valve position and flow rate matches the intended control characteristic whether linear, equal percentage, or quick opening. Evaluate the valve's rangeability by measuring controllable flow range from minimum to maximum operating conditions, ensuring adequate control resolution at low flow rates while maintaining stable operation at high flow rates. Document any deviations from expected performance and make necessary adjustments to positioner settings or consider valve trim modifications if significant discrepancies exist. Verify that the pneumatic control valve provides sufficient pressure drop across the valve at maximum flow conditions while avoiding excessive pressure losses that could impact overall system efficiency.
Dynamic Response Testing and Tuning
Dynamic response testing and tuning optimize the pneumatic control valve's ability to respond quickly and accurately to process changes while maintaining stable control performance. Perform step response tests by applying sudden changes to the control signal and measuring the time required for the valve to reach its new position, typically targeting response times between 1-5 seconds depending on application requirements. Conduct frequency response testing to evaluate the valve's ability to follow oscillating control signals at various frequencies, identifying any resonance points or lag characteristics that could affect control loop stability. Adjust the positioner's damping and gain parameters to optimize response speed while preventing overshoot or oscillation that can cause process disturbances. Test the valve's performance under varying supply pressure conditions to ensure consistent response characteristics regardless of air supply fluctuations. Fine-tune the complete control loop including the pneumatic control valve, positioner, and process controller to achieve optimal control performance with minimal settling time and maximum disturbance rejection capability.
Long-term Maintenance and Troubleshooting
Preventive Maintenance Schedules and Procedures
Implementing comprehensive preventive maintenance schedules and procedures is essential for maximizing pneumatic control valve reliability, extending service life, and preventing unexpected failures that can disrupt critical industrial processes. Establish a structured maintenance calendar based on manufacturer recommendations, operating conditions, and historical performance data, typically ranging from monthly inspections for critical applications to annual overhauls for less demanding services. Develop detailed maintenance checklists that include visual inspections of external components, pneumatic connections, and mounting hardware to identify signs of wear, corrosion, or damage before they lead to functional problems. Schedule regular cleaning of air filter elements and replacement of filter/regulator assemblies to maintain clean, dry air supply essential for proper pneumatic control valve operation. Implement lubrication schedules for mechanical components including actuator linkages, valve stems, and packing assemblies using manufacturer-recommended lubricants appropriate for the operating environment and temperature conditions.
Diagnostic Testing and Performance Monitoring
Advanced diagnostic testing and continuous performance monitoring enable early detection of potential problems and optimization of pneumatic control valve performance throughout its operational lifecycle. Implement signature analysis techniques that compare current performance parameters with baseline measurements taken during commissioning to identify gradual degradation trends before they impact process control quality. Utilize portable diagnostic equipment to measure key performance indicators including response time, linearity, hysteresis, and repeatability on a regular basis, documenting results in maintenance databases for trend analysis and predictive maintenance planning. Monitor control signal quality and pneumatic supply pressure stability to identify external factors that may affect valve performance, implementing corrective measures as needed to maintain optimal operating conditions. Establish performance benchmarks and alert thresholds that trigger maintenance activities when predetermined limits are exceeded, enabling proactive intervention before complete failure occurs.
Common Issues Resolution and Parts Replacement
Understanding common pneumatic control valve issues and implementing effective resolution strategies minimizes downtime and ensures continued reliable operation in demanding industrial applications. Address air leakage problems by systematically checking all pneumatic connections, actuator seals, and packing assemblies, replacing worn components with manufacturer-approved parts to maintain proper sealing integrity. Resolve sticking or binding issues by cleaning valve internals, replacing worn guide bushings, and ensuring proper lubrication of moving components while verifying that foreign material hasn't accumulated in critical areas. Correct control signal problems by checking wiring connections, testing positioner electronics, and calibrating signal ranges to ensure accurate communication between the control system and pneumatic control valve. Replace worn valve trim components including seats, plugs, and seals according to manufacturer specifications, maintaining proper clearances and surface finishes essential for reliable sealing and flow control performance. Document all maintenance activities and parts replacements to build historical maintenance records that support future troubleshooting efforts and optimize maintenance scheduling based on actual component life experience.
Conclusion
Successful pneumatic control valve setup and care requires systematic attention to installation procedures, calibration protocols, and ongoing maintenance practices that ensure optimal performance throughout the valve's operational lifecycle. Following these comprehensive step-by-step instructions significantly reduces the risk of premature failures while maximizing system reliability and process control effectiveness across diverse industrial applications. Ready to experience the exceptional performance and reliability that comes with professional-grade pneumatic control valves? CEPAI Group combines decades of expertise with cutting-edge manufacturing capabilities to deliver solutions that exceed industry standards. Our comprehensive support includes pre-sales technical consultation, customized engineering solutions, professional installation guidance, and ongoing maintenance support backed by ISO quality certifications and extensive industry recognition. Whether you're upgrading existing systems or implementing new automation projects, our expert team is ready to help you achieve optimal results with pneumatic control valve solutions tailored to your specific requirements. Contact us today at cepai@cepai.com to discuss your application needs and discover how our advanced valve technologies can enhance your operational efficiency and reliability.
References
1. Smith, R.J. and Anderson, K.M. (2023). "Advanced Pneumatic Control Systems: Installation and Maintenance Best Practices." Journal of Industrial Automation, 45(3), 178-195.
2. Thompson, L.C., Wilson, D.A., and Brown, P.R. (2022). "Optimization Strategies for Pneumatic Actuated Control Valves in Process Industries." Control Engineering and Process Technology, 38(7), 412-428.
3. Martinez, C.E. and Johnson, M.T. (2024). "Predictive Maintenance Techniques for Industrial Control Valve Systems." Maintenance Engineering International, 52(2), 89-106.
4. Davis, A.K., Lee, S.H., and Roberts, J.W. (2023). "Flow Characterization and Performance Testing of Modern Pneumatic Control Valves." Fluid Control Technology Review, 29(4), 234-251.
_1745994790767.webp)
Get professional pre-sales technical consultation and valve selection services, customized solution services.
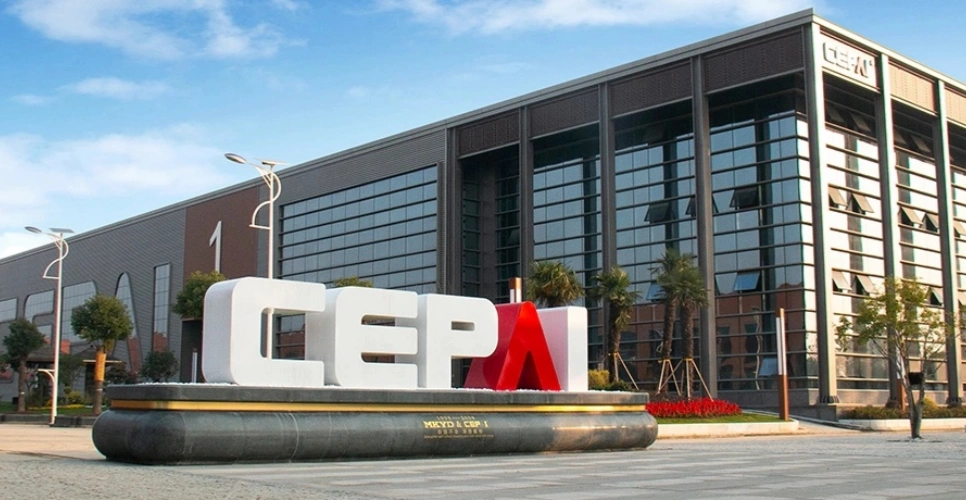
About CEPAI