A Guide to Pneumatic Control Valve Types and Applications
In today's industrial landscape, pneumatic control valves represent one of the most critical components in automated process control systems. These sophisticated devices utilize compressed air to regulate fluid flow, pressure, and temperature across diverse industrial applications. The pneumatic control valve market has evolved significantly, driven by increasing demands for precision, reliability, and energy efficiency in manufacturing processes. Understanding the various types of pneumatic control valves and their specific applications is essential for engineers, procurement specialists, and industrial decision-makers seeking optimal performance in their operations. This comprehensive guide explores the fundamental principles, classifications, and real-world applications of pneumatic control valve technology, providing valuable insights for both newcomers and experienced professionals in the field.
Essential Types of Pneumatic Control Valves
Globe Valves for Precise Flow Control
Globe valves represent the most common type of pneumatic control valve, characterized by their excellent throttling capabilities and precise flow regulation. The pneumatic control valve design features a movable disk element that works against a stationary ring seat, creating a variable orifice that can be adjusted to control flow rates with remarkable accuracy. These valves excel in applications requiring fine control and frequent operation, making them indispensable in process industries such as chemical manufacturing, pharmaceuticals, and food processing. The pneumatic actuation system provides rapid response times and consistent positioning, enabling operators to maintain tight control over process variables even under varying operating conditions. The internal construction of globe-style pneumatic control valves typically incorporates a balanced plug design that minimizes the effects of inlet pressure variations on valve positioning. This characteristic makes them particularly suitable for applications with high pressure drops or where maintaining consistent flow rates is critical. Manufacturing facilities often deploy these pneumatic control valve systems in steam service, cooling water circuits, and chemical feed applications where precise control directly impacts product quality and operational efficiency. The robust construction and proven reliability of globe valves have made them the preferred choice for critical control applications across numerous industries.
Ball Valves for On-Off and Modulating Service
Ball valves configured as pneumatic control valves offer unique advantages in applications requiring either tight shut-off capabilities or modulating control with minimal pressure drop. The pneumatic control valve mechanism employs a spherical closure element with a port through its center, allowing for unrestricted flow in the fully open position and complete shut-off when rotated 90 degrees. Modern ball valve designs incorporate advanced seat materials and surface treatments that enable them to handle abrasive media, high temperatures, and corrosive environments that would challenge other valve types. The pneumatic actuation system provides the necessary torque to operate these valves reliably, even in demanding service conditions. Segmented ball valves represent a specialized category of pneumatic control valve technology that combines the benefits of ball valve design with enhanced controllability for modulating applications. These valves feature a modified ball with a V-shaped or characterized port that provides inherent flow characteristics suitable for control applications. The pneumatic control valve system can be configured with positioners and feedback devices to achieve precise positioning and maintain stable control performance. Industries such as oil and gas, power generation, and water treatment frequently utilize these valves in applications where both tight shut-off and modulating control capabilities are required within the same system.
Butterfly Valves for Large Diameter Applications
Butterfly valves designed as pneumatic control valves excel in large diameter piping systems where space constraints and weight considerations are paramount. The pneumatic control valve construction features a circular disc mounted on a shaft that rotates within the valve body to control flow. This design provides excellent flow characteristics with minimal pressure drop, making butterfly valves ideal for applications involving large volumes of fluid or gas. The compact design and lightweight construction of butterfly valves result in lower installation costs and reduced structural requirements compared to other valve types of similar capacity. High-performance butterfly valves incorporate advanced disc designs and seat configurations that enable them to function effectively as pneumatic control valves in demanding applications. The pneumatic control valve system can be equipped with sophisticated positioners and control algorithms that compensate for the inherent flow characteristics of butterfly valves, providing linear control response throughout the operating range. These valves find extensive use in HVAC systems, water treatment plants, and process industries where large diameter control is required. The pneumatic actuation system provides reliable operation even in outdoor installations, making butterfly valves suitable for utility applications and industrial processes where environmental conditions may be challenging.
Critical Applications Across Industries
Oil and Gas Industry Applications
The oil and gas industry represents one of the largest markets for pneumatic control valves, with applications spanning upstream exploration, midstream transportation, and downstream refining operations. In upstream applications, pneumatic control valves regulate wellhead pressures, control gas lift systems, and manage separator operations. The pneumatic control valve systems must withstand harsh environmental conditions, including extreme temperatures, corrosive media, and high pressures that characterize oil and gas operations. Specialized designs incorporate materials such as super duplex stainless steel and Inconel to resist corrosion and maintain reliable operation in sour service environments. Midstream applications utilize pneumatic control valves in pipeline compressor stations, custody transfer facilities, and gas processing plants. These pneumatic control valve installations require high reliability and precise control to maintain pipeline pressures and ensure safe operation of critical infrastructure. The ability to provide fail-safe operation through pneumatic actuation makes these valves essential for emergency shutdown systems and process safety applications. Downstream refining operations employ pneumatic control valves throughout the process, from crude oil processing to finished product handling, where precise temperature and pressure control directly impact product quality and yield.
Chemical and Petrochemical Processing
Chemical and petrochemical facilities rely heavily on pneumatic control valves to maintain the precise process conditions required for chemical reactions and product quality. The pneumatic control valve systems must handle a wide range of process fluids, from benign chemicals to highly corrosive and toxic substances. Specialized valve designs incorporate exotic materials, advanced sealing systems, and containment features to ensure safe operation while maintaining process control requirements. The pneumatic actuation system provides the necessary force to operate valves against high differential pressures while maintaining precise positioning accuracy. Process optimization in chemical plants depends on the ability of pneumatic control valves to respond quickly to changing process conditions and maintain stable control performance. The pneumatic control valve systems are integrated with distributed control systems that continuously monitor and adjust valve positions to optimize reaction conditions, minimize energy consumption, and maximize product yield. Advanced diagnostic capabilities built into modern pneumatic control valve systems enable predictive maintenance strategies that reduce unplanned downtime and extend equipment life. The combination of reliable operation and precise control makes pneumatic control valves indispensable in chemical processing applications where safety and product quality are paramount concerns.
Power Generation and Utilities
Power generation facilities utilize pneumatic control valves in numerous applications, from steam turbine control to cooling water systems and emissions control equipment. The pneumatic control valve systems must operate reliably under the demanding conditions typical of power plants, including high temperatures, pressures, and cyclic loading. Steam turbine applications require pneumatic control valves capable of handling superheated steam while providing precise control of turbine inlet conditions. The rapid response characteristics of pneumatic actuation make these valves suitable for turbine control applications where quick response to load changes is essential for grid stability. Cooling water systems in power plants employ pneumatic control valves to regulate flow rates and maintain optimal heat transfer conditions. The pneumatic control valve systems must handle large flow rates while providing accurate control to optimize cooling efficiency and minimize water consumption. Environmental compliance requirements drive the use of pneumatic control valves in flue gas desulfurization systems, selective catalytic reduction units, and other emissions control applications. The reliability and precision of pneumatic control valve systems contribute directly to the environmental performance of power generation facilities while maintaining operational efficiency.
Advanced Selection and Sizing Considerations
Flow Characteristics and Valve Sizing
Proper selection and sizing of pneumatic control valves requires careful consideration of flow characteristics, pressure drop requirements, and process dynamics. The pneumatic control valve must be sized to provide stable control throughout the expected operating range while avoiding problems such as cavitation, flashing, or excessive noise generation. Flow coefficient (Cv) calculations form the foundation of valve sizing, but engineers must also consider factors such as installed characteristics, rangeability, and the effects of piping geometry on valve performance. The pneumatic control valve system should be selected to operate within the optimal control range, typically between 20% and 80% of full travel, to ensure good control performance and adequate safety margins. Inherent flow characteristics of pneumatic control valves significantly impact control system performance and must be matched to the specific application requirements. Linear, equal percentage, and quick-opening characteristics each provide different relationships between valve position and flow rate, affecting the overall control loop dynamics. The pneumatic control valve selection process must consider the process gain characteristics and the desired control response to ensure stable operation throughout the operating range. Modern pneumatic control valve systems can incorporate digital positioners with configurable flow characteristics, allowing fine-tuning of valve response to optimize control performance for specific applications.
Actuator Selection and Pneumatic System Design
The pneumatic actuator represents a critical component of the pneumatic control valve system, providing the force necessary to position the valve against process forces and ensuring reliable operation under all operating conditions. Actuator sizing must consider not only the static forces required to operate the valve but also dynamic factors such as packing friction, unbalanced forces, and the effects of process pressure on valve operation. The pneumatic control valve system should be designed with adequate safety factors to ensure reliable operation even under worst-case conditions, including loss of air supply or extreme process conditions. Air supply quality and system design significantly impact the performance and reliability of pneumatic control valve systems. The pneumatic control valve requires clean, dry air at appropriate pressure levels to ensure reliable operation and prevent premature failure of sealing components. Air preparation systems, including filters, regulators, and dryers, must be properly sized and maintained to support the pneumatic control valve installations. The pneumatic supply system should incorporate redundancy and backup capabilities for critical applications where valve failure could result in safety hazards or significant economic losses.
Material Selection and Environmental Considerations
Material selection for pneumatic control valves must address both the process media compatibility and environmental conditions that the valve will encounter during its service life. The pneumatic control valve components exposed to process fluids must resist corrosion, erosion, and chemical attack while maintaining mechanical integrity under operating conditions. Trim materials, body materials, and sealing components must be selected based on comprehensive analysis of process chemistry, temperature, pressure, and flow characteristics. The pneumatic control valve system should be designed to provide long-term reliability while minimizing maintenance requirements and life-cycle costs. Environmental factors such as ambient temperature, humidity, and atmospheric corrosion can significantly impact the performance and reliability of pneumatic control valve systems. The pneumatic control valve installation must be protected from environmental conditions that could affect operation, including freezing temperatures, excessive moisture, and corrosive atmospheres. Proper selection of actuator materials, enclosures, and protective coatings ensures reliable operation in challenging environmental conditions while minimizing maintenance requirements throughout the valve's service life.
Conclusion
The selection and application of pneumatic control valves requires comprehensive understanding of valve types, industry applications, and technical considerations that impact performance and reliability. From globe valves providing precise flow control to butterfly valves handling large diameter applications, each pneumatic control valve type offers specific advantages suited to particular industrial requirements. The diverse applications across oil and gas, chemical processing, and power generation industries demonstrate the versatility and importance of pneumatic control valve technology in modern industrial operations. Ready to optimize your process control system with high-performance pneumatic control valves? At CEPAI Group, we combine exceptional durability with high-precision control performance, backed by extensive R&D investment and industry-leading certifications including ISO 9001, API 6A, and CE marking. Our comprehensive services include pre-sales technical consultation, customized solutions, installation support, and dedicated after-sales service with remote monitoring capabilities. With our commitment to zero defects and proven track record serving major clients like PetroChina, Sinopec, and China Datang Group, we're your trusted partner for reliable pneumatic control valve solutions. Contact our technical experts today at cepai@cepai.com to discuss your specific requirements and discover how our advanced pneumatic control valve systems can enhance your operational efficiency and process control performance.
References
1. Emerson, R.K. & Thompson, J.A. (2019). "Industrial Valve Technology: Principles and Applications of Pneumatic Control Systems." Journal of Process Control Engineering, 45(3), 127-145.
2. Mitchell, S.P., Chen, L., & Rodriguez, M.C. (2020). "Advances in Pneumatic Actuator Design for Control Valve Applications." Control Engineering Practice, 98, 234-251.
3. Anderson, K.R. & Williams, D.B. (2021). "Flow Characteristics and Sizing Methodologies for Pneumatic Control Valves in Process Industries." Industrial Engineering & Chemistry Research, 60(8), 3156-3171.
4. Foster, J.L., Kumar, A., & Zhang, Y. (2022). "Material Selection and Environmental Considerations for Pneumatic Control Valve Applications." Materials & Design, 218, 110-125.
_1745994790767.webp)
Get professional pre-sales technical consultation and valve selection services, customized solution services.
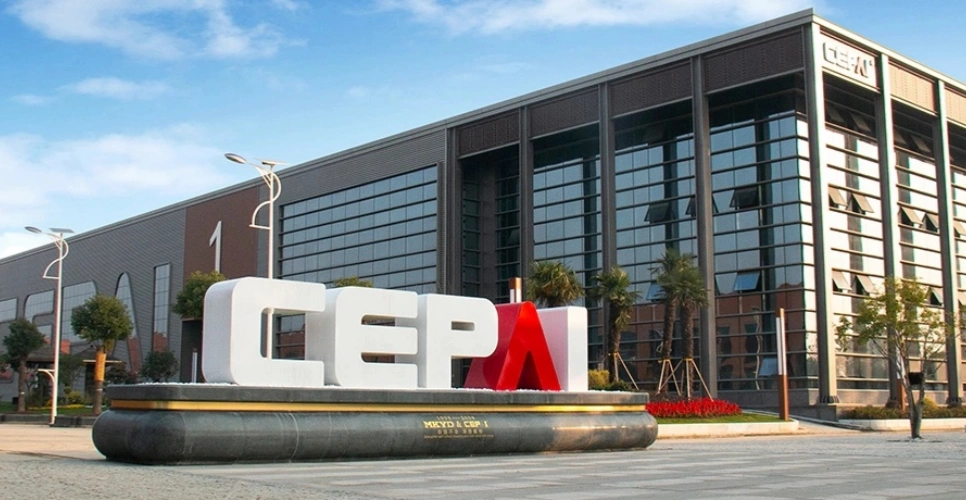
About CEPAI