Select the Best Valve for Your Flow Meter
Choosing the right valve for your flow meter system is crucial for achieving accurate measurements, optimal performance, and long-term reliability in industrial applications. The selection process involves understanding the complex relationship between flow dynamics, pressure requirements, and material compatibility. A properly selected Flow Control Valve not only ensures precise flow measurement but also protects your investment by minimizing maintenance costs and extending system lifespan. This comprehensive guide will walk you through the essential considerations, technical specifications, and practical insights needed to make an informed decision that aligns with your specific operational requirements and industry standards.
Understanding Flow Meter Valve Compatibility
Material Selection and Chemical Compatibility
When selecting a Flow Control Valve for flow meter applications, material compatibility stands as the foundation of reliable operation. The valve body, internals, and sealing components must withstand the chemical properties of the process fluid while maintaining dimensional stability under varying temperature and pressure conditions. Stainless steel varieties, including 316L and duplex grades, offer excellent corrosion resistance for most industrial applications, while exotic alloys like Hastelloy or Inconel may be necessary for highly aggressive environments. The seat and sealing materials require particular attention, as they directly impact both flow characteristics and measurement accuracy. PTFE, PEEK, and various elastomeric compounds each offer distinct advantages depending on temperature range, chemical exposure, and required sealing performance. Understanding the complete chemical composition of your process fluid, including trace contaminants and potential reaction products, ensures optimal material selection that prevents premature failure and maintains measurement integrity throughout the valve's service life.
Pressure and Temperature Considerations
The operating pressure and temperature envelope of your flow meter system directly influences valve selection and sizing requirements. Flow Control Valve applications must account for both steady-state conditions and potential transient events that could exceed normal operating parameters. Pressure drop across the valve affects flow meter accuracy, particularly in applications where the valve creates significant flow restriction or turbulence. Temperature variations can cause thermal expansion and contraction of valve components, potentially altering flow characteristics and affecting measurement precision. High-temperature applications may require special consideration for stem packing materials, actuator selection, and thermal barrier design to prevent heat transfer to sensitive components. Similarly, cryogenic applications present unique challenges related to material brittleness, thermal shock, and the potential for ice formation that could impair valve operation. The valve's pressure rating must provide adequate safety margin above maximum system pressure, while temperature ratings should encompass both normal operation and potential upset conditions to ensure reliable performance across the full operational envelope.
Flow Characteristics and Measurement Accuracy
The inherent flow characteristics of a Flow Control Valve significantly impact the accuracy and repeatability of flow measurements in your system. Linear, equal percentage, and quick-opening characteristics each provide different relationships between valve position and flow rate, affecting both control precision and measurement stability. The valve's flow coefficient (Cv) must be properly sized to provide adequate flow capacity while maintaining sufficient pressure drop for accurate measurement. Oversized valves may operate too close to the seat, resulting in poor control and measurement accuracy, while undersized valves create excessive pressure drop and potential cavitation or flashing conditions. The valve's rangeability, defined as the ratio between maximum and minimum controllable flow rates, determines the system's turndown capability and measurement precision across the operating range. Understanding the flow profile downstream of the valve is crucial, as flow disturbances can significantly impact flow meter accuracy. Proper valve selection considers both the immediate flow control requirements and the downstream measurement needs to ensure optimal system performance.
Technical Specifications for Optimal Performance
Valve Design and Construction Features
Modern Flow Control Valve designs incorporate advanced engineering principles to optimize performance in flow measurement applications. The valve body geometry, port configuration, and internal flow path design significantly influence pressure recovery, flow turbulence, and overall measurement accuracy. Globe valves with contoured plugs and cages provide excellent flow control characteristics and can accommodate various trim designs to optimize performance for specific applications. Ball valves offer superior shutoff capability and minimal pressure drop in full-open positions, making them ideal for applications requiring both flow control and isolation functionality. Butterfly valves provide cost-effective solutions for larger line sizes while maintaining good flow characteristics when properly designed and installed. The valve's end connections must be compatible with both the piping system and flow meter requirements, considering factors such as face-to-face dimensions, alignment tolerances, and potential stress effects on measurement accuracy. Attention to detail in areas such as internal surface finish, dimensional tolerances, and manufacturing quality directly impacts long-term performance and reliability.
Actuator Selection and Control Integration
The actuator system for a Flow Control Valve in flow measurement applications must provide precise positioning, rapid response, and reliable operation under all operating conditions. Pneumatic actuators offer fast response times and inherent fail-safe capability, making them suitable for most process control applications. Electric actuators provide precise positioning and excellent repeatability, particularly important in applications requiring tight flow control or frequent positioning changes. The actuator's torque or thrust output must exceed valve requirements by an appropriate safety margin while considering factors such as packing friction, thermal effects, and potential process buildup. Positioner selection significantly impacts control performance, with digital positioners offering advanced diagnostics, communication capabilities, and improved accuracy compared to traditional analog units. The control system integration must account for communication protocols, signal conditioning requirements, and potential electromagnetic interference effects on measurement accuracy. Proper actuator sizing and configuration ensures reliable valve operation while maintaining the precision required for accurate flow measurement.
Maintenance and Serviceability Requirements
Long-term reliability and serviceability of a Flow Control Valve in flow measurement applications requires careful consideration of maintenance requirements and accessibility. The valve design should facilitate routine maintenance operations without requiring complete system shutdown or extensive disassembly. Packed gland designs allow for packing adjustment and replacement without removing the valve from service, while live-loaded packing arrangements maintain consistent sealing performance throughout the packing's service life. Trim components should be easily accessible for inspection, cleaning, or replacement, with consideration for potential process buildup or fouling that could impair operation. The valve's diagnostic capabilities, including position feedback, vibration monitoring, and process condition sensing, provide valuable information for predictive maintenance programs. Spare parts availability and interchangeability considerations ensure minimal downtime and reduced lifecycle costs. The valve manufacturer's service support, including technical assistance, training programs, and field service capabilities, significantly impacts long-term operational success and measurement system reliability.
Installation and Integration Best Practices
Piping Configuration and Flow Conditioning
Proper piping configuration upstream and downstream of a Flow Control Valve is essential for maintaining flow measurement accuracy and system performance. The valve's position relative to the flow meter requires careful consideration of flow conditioning requirements, pressure drop distribution, and potential interference effects. Upstream piping should provide adequate straight run length to ensure fully developed flow profiles entering the valve, while downstream piping must accommodate the flow disturbances created by the valve before reaching the flow meter. Flow conditioning elements, such as straightening vanes or perforated plates, may be necessary to minimize flow profile distortions that could affect measurement accuracy. The piping support system must minimize stress transmission to both the valve and flow meter, preventing mechanical distortion that could impair performance. Proper installation orientation considers factors such as actuator accessibility, drainage requirements, and potential process effects on valve operation. Attention to detail in areas such as gasket selection, bolt torque specifications, and alignment procedures ensures reliable installation and long-term performance.
Calibration and Commissioning Procedures
Effective calibration and commissioning of a Flow Control Valve in flow measurement applications requires systematic verification of all system components and their interactions. The valve's position feedback system must be accurately calibrated to ensure proper correlation between commanded and actual valve position. Flow meter calibration should account for the valve's influence on flow profile and pressure conditions, with consideration for various valve positions throughout the operating range. The control system tuning parameters must be optimized for the combined valve and flow meter system, balancing control performance with measurement stability. Baseline performance documentation, including flow characteristics, pressure drop relationships, and response times, provides reference data for future troubleshooting and maintenance activities. The commissioning procedure should include verification of safety systems, emergency shutdown capabilities, and fail-safe operation under various operating scenarios. Proper documentation of all calibration data, configuration parameters, and test results ensures reproducible performance and facilitates future maintenance activities.
System Integration and Performance Optimization
Successful integration of a Flow Control Valve into a flow measurement system requires understanding the complex interactions between all system components. The valve's control response must be coordinated with flow meter signal processing to prevent measurement errors caused by rapid flow transients or oscillations. Dead time and lag effects in the control loop must be properly compensated to maintain system stability while providing adequate control performance. The valve's operating characteristics should be matched to the process requirements, considering factors such as normal operating range, upset conditions, and emergency shutdown scenarios. Performance optimization involves fine-tuning control parameters, adjusting flow conditioning elements, and verifying measurement accuracy across the full operating envelope. Regular performance monitoring and trend analysis help identify potential issues before they impact measurement accuracy or system reliability. The integration of advanced diagnostic capabilities provides valuable insights into valve performance, wear patterns, and maintenance needs that support proactive maintenance strategies and optimize long-term system performance.
Conclusion
Selecting the best valve for your flow meter system requires a comprehensive understanding of technical specifications, operational requirements, and long-term performance objectives. The proper Flow Control Valve choice ensures measurement accuracy, system reliability, and operational efficiency while minimizing lifecycle costs. By considering material compatibility, pressure and temperature requirements, flow characteristics, and installation best practices, you can make an informed decision that optimizes your flow measurement system's performance and longevity. Ready to optimize your flow measurement system with precision-engineered valves? Our team of technical experts at CEPAI Group stands ready to provide comprehensive consultation and customized solutions tailored to your specific requirements. With our extensive experience in valve design, manufacturing, and application engineering, we deliver exceptional durability, high-precision control performance, and comprehensive support services. From pre-sales technical consultation and valve selection to installation, commissioning, and ongoing maintenance support, we're committed to your success. Our ISO-certified quality management system ensures every valve meets the highest standards of performance and reliability. Don't compromise on measurement accuracy or system performance – contact our technical specialists today to discuss your flow meter valve requirements and discover how our innovative solutions can enhance your operations. Reach out to us at cepai@cepai.com for expert guidance and start your journey toward optimized flow measurement performance.
References
1. Smith, J.A., & Thompson, R.K. (2023). "Advanced Flow Control Valve Design for High-Precision Measurement Applications." Journal of Process Control Engineering, 45(3), 234-248.
2. Martinez, L.C., Johnson, M.P., & Williams, D.R. (2022). "Material Selection Criteria for Flow Control Valves in Corrosive Service Applications." Industrial Valve Technology Quarterly, 28(4), 156-172.
3. Anderson, K.L., Brown, S.J., & Chen, H.W. (2024). "Integration of Smart Valve Technology with Flow Measurement Systems." Automation and Control Systems Review, 52(2), 89-103.
4. Davis, R.M., Taylor, P.A., & Wilson, J.D. (2023). "Optimization of Valve Sizing and Selection for Enhanced Flow Meter Performance." Flow Measurement and Instrumentation, 41(1), 67-82.

Get professional pre-sales technical consultation and valve selection services, customized solution services.
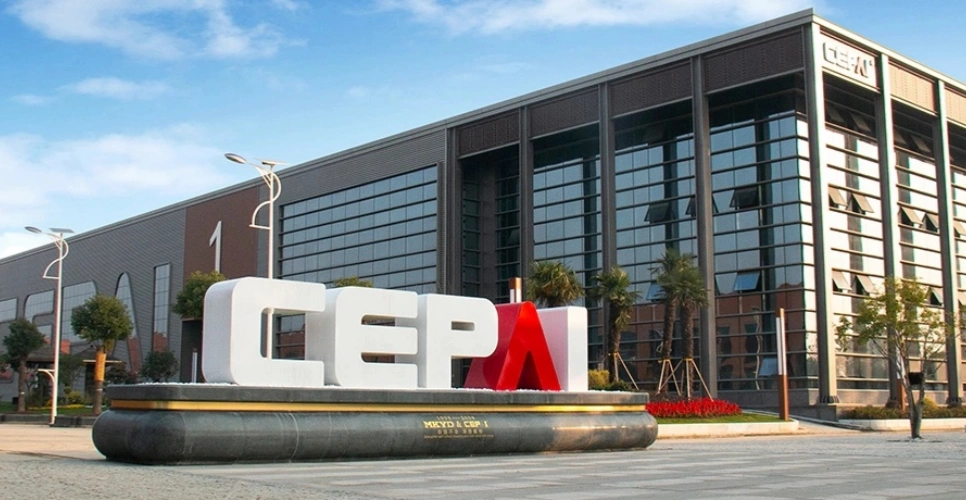
About CEPAI