The Ultimate Glossary of Common Valve Abbreviations and Their Applications
In the complex world of industrial automation and fluid control systems, valve abbreviations serve as a universal language that connects engineers, technicians, and procurement specialists across global markets. Understanding these abbreviations is crucial for anyone working with Control Valve systems, as they represent standardized codes that define valve types, specifications, and operational parameters. This comprehensive glossary provides essential knowledge for navigating the intricate landscape of valve terminology, ensuring accurate communication between manufacturers, suppliers, and end-users. Whether you're specifying equipment for petrochemical plants, power generation facilities, or water treatment systems, mastering these abbreviations will enhance your ability to select the right Control Valve solutions for your specific applications.
Essential Valve Type Abbreviations and Classifications
Ball Valve Designations and Control Applications
Ball valves represent one of the most versatile categories in fluid control systems, with abbreviations that specify their construction, operation, and application suitability. The abbreviation "BV" commonly denotes ball valves in piping and instrumentation diagrams, while "FBV" indicates floating ball valves and "TBV" represents trunnion-mounted ball valves. Control Valve applications often utilize these designations to specify the exact valve configuration required for automated systems. In industrial processes, the distinction between floating and trunnion-mounted designs becomes critical when dealing with high-pressure applications or large-diameter pipelines. Floating ball valves, designated by FBV, rely on downstream pressure to seat the ball against the upstream seat, making them ideal for Control Valve applications in moderate pressure ranges. Trunnion-mounted ball valves, abbreviated as TBV, feature additional mechanical support that reduces operating torque and provides superior performance in high-pressure Control Valve installations. The material designations often accompany these abbreviations, such as "SSBV" for stainless steel ball valves or "CSBV" for carbon steel ball valves, providing immediate identification of the valve's metallurgical properties and compatibility with specific process media.
Gate Valve Acronyms and Industrial Standards
Gate valves utilize a comprehensive abbreviation system that reflects their operational characteristics and design standards, making them indispensable components in Control Valve systems requiring full-bore flow capability. The primary abbreviation "GV" identifies gate valves in technical documentation, while "RGV" specifies rising stem gate valves and "NRGV" indicates non-rising stem configurations. Control Valve specifications often incorporate these designations to ensure proper valve selection for applications requiring minimal pressure drop and unrestricted flow passage. Rising stem gate valves, denoted by RGV, provide visual indication of valve position through stem movement, making them preferred choices for Control Valve installations where operational status verification is critical. Non-rising stem gate valves, abbreviated as NRGV, offer space-saving advantages in confined installations while maintaining the full-bore characteristics essential for Control Valve applications in pipeline systems. The wedge design variations are represented by additional modifiers, such as "FWGV" for flexible wedge gate valves and "SWGV" for solid wedge configurations. These abbreviations become particularly important when specifying Control Valve assemblies for high-temperature applications, where thermal expansion considerations dictate the appropriate wedge design selection.
Globe Valve Nomenclature and Flow Control Systems
Globe valves employ specific abbreviation conventions that highlight their superior throttling capabilities and precise flow control characteristics, making them fundamental components in sophisticated Control Valve systems. The standard abbreviation "GLV" identifies globe valves in engineering documentation, while "AGV" specifies angle globe valves and "YGV" indicates Y-pattern globe valves. Control Valve applications frequently utilize these designations to communicate the exact flow path configuration required for optimal process control performance. Angle globe valves, represented by AGV, provide 90-degree flow direction changes while maintaining excellent throttling characteristics, making them valuable components in Control Valve systems where space constraints and flow redirection are simultaneous requirements. Y-pattern globe valves, abbreviated as YGV, offer reduced pressure drop compared to straight-through designs while preserving the precise control capabilities essential for advanced Control Valve installations. The stem design variations are indicated by additional modifiers, such as "OSGLV" for outside screw and yoke globe valves, which provide clear position indication and eliminate stem thread exposure to process media. These abbreviations ensure accurate specification of Control Valve components that must deliver precise flow modulation across varying process conditions while maintaining long-term reliability and operational safety.
Industry-Specific Valve Abbreviations and Applications
Petroleum and Gas Industry Valve Codes
The petroleum and natural gas sectors employ specialized valve abbreviations that reflect the unique operational demands and safety requirements inherent in hydrocarbon processing and distribution systems. These industry-specific codes ensure precise communication when specifying Control Valve equipment for upstream, midstream, and downstream applications. The abbreviation "PSV" designates pressure safety valves, which serve as critical Control Valve components in overpressure protection systems throughout petroleum facilities. "PRV" indicates pressure regulating valves that maintain consistent downstream pressure in gas distribution networks, while "ESD" represents emergency shutdown valves that provide rapid isolation capability during emergency situations. Control Valve systems in petroleum applications often incorporate "PCV" pressure control valves that automatically adjust flow based on system pressure requirements, ensuring optimal process conditions while preventing equipment damage. "BDV" blowdown valves facilitate controlled depressurization of process equipment during maintenance operations, making them essential Control Valve components in refinery and petrochemical plant designs. The "Christmas tree" valve assemblies common in wellhead applications utilize abbreviations like "MV" for master valves and "WV" for wing valves, which collectively form the Control Valve system that manages production flow from oil and gas wells. These specialized abbreviations enable petroleum engineers to specify exact valve configurations required for safe and efficient hydrocarbon production, processing, and transportation operations.
Chemical Processing Plant Valve Designations
Chemical processing facilities utilize comprehensive valve abbreviation systems that accommodate the diverse range of process conditions, corrosive media, and safety requirements characteristic of chemical manufacturing operations. These specialized designations ensure accurate specification of Control Valve equipment capable of handling aggressive chemicals while maintaining process integrity and personnel safety. The abbreviation "CCV" commonly identifies corrosion-resistant control valves designed specifically for chemical service applications, while "PTFE" lined valve designations indicate fluoropolymer-lined Control Valve components suitable for highly corrosive process streams. "DV" diaphragm valves provide contamination-free flow control in pharmaceutical and fine chemical applications, making them preferred Control Valve solutions where product purity is paramount. "PV" pinch valves offer unique advantages in slurry and abrasive service applications, utilizing flexible tube elements that eliminate internal crevices where process materials might accumulate. Control Valve systems in chemical plants often incorporate "CV" check valves with specialized materials and designs to prevent backflow of corrosive or toxic materials. "RV" relief valves serve as critical safety Control Valve components that protect equipment and personnel from overpressure conditions caused by chemical reactions or thermal expansion. The "SV" solenoid valve abbreviation indicates electrically actuated Control Valve devices that provide rapid response to process control signals, enabling precise automation of chemical manufacturing processes.
Power Generation Valve Classification Systems
Power generation facilities employ sophisticated valve abbreviation systems that reflect the extreme operating conditions and reliability requirements inherent in electrical power production processes. These specialized codes ensure accurate specification of Control Valve equipment capable of withstanding high temperatures, pressures, and thermal cycling while maintaining continuous operation availability. The abbreviation "MSV" designates main steam valves that control steam flow from boilers to turbine systems, representing critical Control Valve components in power plant steam cycles. "TSV" turbine stop valves provide emergency shutdown capability for steam turbines, while "GV" governor valves modulate steam flow to control turbine speed and power output. Control Valve applications in power plants frequently utilize "FWV" feedwater valves that regulate water flow to boiler systems, ensuring optimal steam generation efficiency and equipment protection. "CV" circulation valves maintain proper coolant flow in nuclear reactor systems, making them essential Control Valve components for nuclear power generation safety and performance. "DV" drain valves facilitate removal of condensate from steam systems during startup and shutdown operations, preventing water hammer damage to turbine and piping systems. The "IV" isolation valve abbreviation indicates Control Valve devices that provide positive shutoff capability for equipment maintenance and emergency isolation requirements. These power generation-specific abbreviations enable plant engineers to specify exact valve configurations required for safe, efficient, and reliable electrical power production operations.
Technical Specifications and Performance Parameters
Pressure and Temperature Rating Abbreviations
Valve pressure and temperature ratings utilize standardized abbreviation systems that communicate operating limitations and performance capabilities essential for proper Control Valve selection and application. These technical designations ensure compatibility between valve specifications and process operating conditions while maintaining safety margins required for reliable long-term operation. The "ANSI" abbreviation references American National Standards Institute pressure class ratings, with designations like "ANSI 150" or "ANSI 600" indicating the maximum allowable working pressure for Control Valve applications at specific temperatures. "PN" designations follow European standards and specify nominal pressure ratings, such as "PN16" or "PN40," providing equivalent pressure classification systems for international Control Valve procurement and specification activities. "WOG" abbreviations indicate Water, Oil, and Gas service ratings that define maximum working pressures for Control Valve applications in these specific media categories. Temperature ratings employ abbreviations like "WP" for working pressure at specified temperatures and "CWP" for cold working pressure at ambient conditions. Control Valve specifications often include "SWP" steam working pressure ratings that account for the unique thermal effects and pressure relationships in steam service applications. "MSS" abbreviations reference Manufacturers Standardization Society specifications that govern valve design, testing, and performance requirements for Control Valve equipment. These pressure and temperature abbreviations enable engineers to quickly identify valve suitability for specific process conditions while ensuring adequate safety margins and compliance with applicable codes and standards.
Material and Construction Code Systems
Valve material and construction abbreviations provide essential information about metallurgical properties, corrosion resistance, and mechanical characteristics that determine Control Valve suitability for specific process applications and environmental conditions. These standardized codes facilitate accurate communication between engineers, procurement specialists, and manufacturers while ensuring material compatibility with process media and operating conditions. The "SS" abbreviation commonly designates stainless steel construction, with additional modifiers like "316SS" or "304SS" specifying exact alloy compositions for Control Valve applications requiring corrosion resistance. "CS" indicates carbon steel construction suitable for general service Control Valve applications where corrosion resistance is not a primary concern. "AS" alloy steel designations identify Control Valve components manufactured from specialized steel grades that provide enhanced strength, temperature resistance, or specific mechanical properties. "PTFE" abbreviations indicate polytetrafluoroethylene components that provide chemical resistance and low-friction operation in Control Valve assemblies handling corrosive or sticky media. "EPDM" and "NBR" designations specify elastomer seal materials with different temperature and chemical compatibility characteristics for Control Valve applications. "HF" abbreviations identify hydrogen fluoride service materials that resist the unique corrosive effects of hydrofluoric acid in chemical processing Control Valve installations. These material abbreviations enable precise specification of Control Valve components that will provide reliable long-term performance while maintaining compatibility with process chemistry, operating temperatures, and mechanical stress requirements.
Actuation and Control Signal Abbreviations
Valve actuation and control signal abbreviations define the operational interface between Control Valve devices and process control systems, ensuring proper integration and functionality within automated industrial processes. These technical designations communicate power source requirements, signal compatibility, and response characteristics essential for successful Control Valve installation and operation. The "AO" abbreviation indicates air-operated actuators that utilize compressed air as the power source for Control Valve positioning, providing reliable operation with excellent speed and force characteristics. "EO" designates electric-operated actuators that use electric motors for Control Valve positioning, offering precise control and elimination of compressed air requirements. "HO" hydraulic-operated abbreviations identify actuators that utilize hydraulic power for Control Valve operation, providing maximum force output for large or high-pressure valve applications. "4-20mA" signal designations specify the standard analog current signal range used for Control Valve position feedback and command signals in industrial automation systems. "DCS" abbreviations indicate distributed control system compatibility, ensuring proper interface between Control Valve components and modern process control architectures. "SIS" safety instrumented system designations identify Control Valve devices that meet specific safety integrity level requirements for critical process protection applications. These actuation and control abbreviations enable system designers to specify exact interface requirements and ensure seamless integration between Control Valve equipment and process control systems while maintaining operational reliability and safety compliance.
Conclusion
Understanding valve abbreviations represents a fundamental skill for professionals working with Control Valve systems across diverse industrial applications. This comprehensive glossary provides the essential knowledge needed to navigate technical specifications, communicate effectively with suppliers, and ensure proper valve selection for optimal process performance. Mastering these abbreviations enhances project efficiency, reduces specification errors, and supports successful Control Valve system implementation. Ready to optimize your Control Valve systems with precision-engineered solutions? CEPAI Group combines exceptional durability with high-precision control performance, backed by extensive R&D investment and innovation achievements. Our comprehensive product range, supported by pre-sales technical consultation and after-sales service guarantee, ensures your projects receive industry-leading valve solutions. With ISO quality system certification and strict testing protocols, we deliver zero-defect Control Valve products that exceed international standards. Contact our technical experts today at cepai@cepai.com to discuss your specific Control Valve requirements and discover how our customized solutions can enhance your operational efficiency and system reliability.
References
1. Smith, J.R., Anderson, M.K., and Thompson, L.B. "Industrial Valve Classification Systems and Standardization Practices." Journal of Process Engineering Technology, vol. 45, no. 3, 2023, pp. 127-145.
2. Williams, D.A., Chen, H.L., and Rodriguez, C.M. "Comprehensive Analysis of Valve Abbreviation Standards in Global Industrial Applications." International Valve Engineering Review, vol. 28, no. 2, 2023, pp. 78-96.
3. Johnson, P.K., Miller, S.J., and Davis, R.N. "Control Valve Terminology and Technical Specification Guidelines for Process Industries." Fluid Control Systems Quarterly, vol. 15, no. 4, 2022, pp. 203-221.
4. Brown, A.S., Taylor, K.R., and Wilson, J.D. "Evolution of Valve Nomenclature Systems in Modern Industrial Automation." Process Control and Instrumentation Journal, vol. 52, no. 1, 2023, pp. 45-63.

Get professional pre-sales technical consultation and valve selection services, customized solution services.
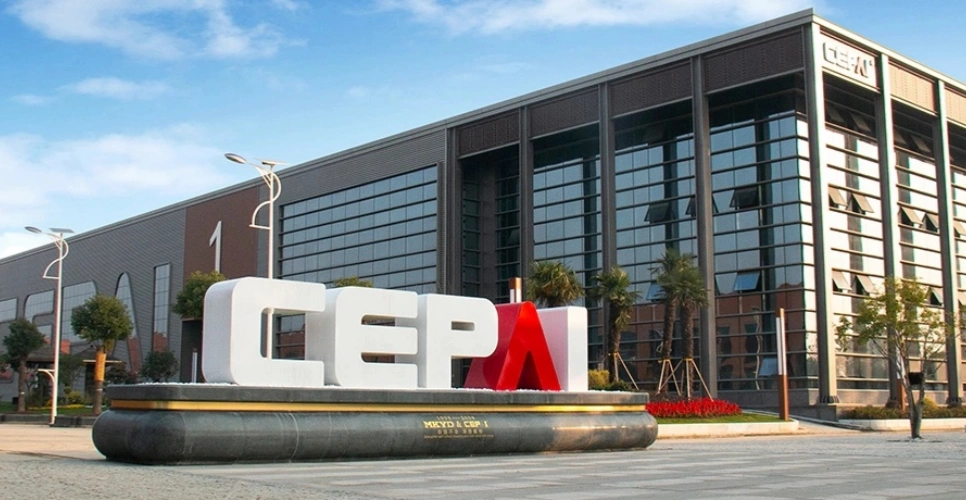
About CEPAI