Understanding the Most Popular Pneumatic Control Valves in 2025
The industrial automation landscape continues to evolve rapidly, with pneumatic control valves standing at the forefront of modern fluid control technology. As we navigate through 2025, the demand for high-performance pneumatic control valve solutions has reached unprecedented levels across various industries including petrochemical, power generation, metallurgy, and water treatment. These sophisticated devices have become indispensable components in ensuring precise flow control, pressure regulation, and system optimization in complex industrial processes. Understanding the current trends, technological advancements, and market preferences in pneumatic control valve technology is crucial for engineers, procurement specialists, and industry professionals seeking to make informed decisions for their operations.
Key Technological Advancements in Modern Pneumatic Control Valves
Enhanced Precision and Control Capabilities
The latest generation of pneumatic control valve systems demonstrates remarkable improvements in precision control capabilities. Modern actuators incorporate advanced positioning technology that enables precise valve positioning with accuracy tolerances as tight as ±0.1%. This enhanced precision is achieved through sophisticated feedback systems that continuously monitor valve position and make real-time adjustments to maintain optimal performance. The pneumatic control valve designs now feature improved actuator response times, reducing lag between control signals and actual valve movement. These advancements are particularly beneficial in applications requiring rapid response to process changes, such as chemical processing plants where even minor deviations can impact product quality. The integration of smart positioning systems allows operators to fine-tune valve performance parameters remotely, optimizing system efficiency while reducing the need for manual interventions.
Advanced Materials and Durability Improvements
Contemporary pneumatic control valve manufacturing has witnessed significant advances in materials science and engineering. Manufacturers now utilize high-performance alloys and specialized coatings that enhance corrosion resistance and extend operational lifespan significantly. These materials can withstand extreme temperatures ranging from -196°C to 593°C while maintaining structural integrity under high-pressure conditions. The implementation of advanced sealing technologies has virtually eliminated internal leakage issues that plagued earlier generations of pneumatic control valve systems. Modern valve bodies incorporate sophisticated metallurgical treatments that enhance fatigue resistance, ensuring consistent performance even under cyclical loading conditions. These durability improvements translate directly into reduced maintenance costs and extended service intervals, making modern pneumatic control valve systems more economically attractive for long-term industrial applications.
Smart Integration and Industry 4.0 Compatibility
The evolution toward Industry 4.0 has fundamentally transformed pneumatic control valve technology, introducing unprecedented levels of connectivity and intelligence. Modern systems feature integrated sensors that continuously monitor operational parameters including temperature, pressure, flow rate, and actuator performance. This real-time data collection enables predictive maintenance strategies that can identify potential issues before they result in system failures. The pneumatic control valve systems now support various communication protocols including Foundation Fieldbus, HART, and Profibus, ensuring seamless integration with existing control systems. Advanced diagnostic capabilities provide detailed insights into valve performance, allowing maintenance teams to optimize service schedules and reduce unplanned downtime. These smart features also enable remote monitoring and control capabilities, allowing operators to manage valve operations from centralized control rooms or even mobile devices.
Industry Applications and Market Demand Trends
Petrochemical and Oil & Gas Sector Leadership
The petrochemical and oil & gas industries continue to drive the highest demand for pneumatic control valve systems, accounting for approximately 35% of global market consumption. These sectors require valves capable of handling corrosive media, extreme pressures, and hazardous environments while maintaining exceptional reliability. Modern pneumatic control valve designs specifically engineered for these applications incorporate fire-safe features, anti-static designs, and specialized trim configurations that ensure safe operation even under emergency conditions. The ongoing expansion of liquefied natural gas (LNG) facilities and petrochemical complexes worldwide has created substantial opportunities for advanced valve technologies. Stringent safety regulations in these industries have also accelerated adoption of pneumatic control valve systems with enhanced safety features including fail-safe operation modes and emergency shutdown capabilities.
Power Generation and Energy Infrastructure
The global transition toward renewable energy sources has created new opportunities and challenges for pneumatic control valve applications. Traditional power plants require sophisticated flow control solutions for steam, water, and fuel gas systems, while renewable energy facilities need specialized valves for biomass handling, geothermal applications, and energy storage systems. Modern pneumatic control valve designs now incorporate features specifically tailored for these diverse applications, including high-temperature resistance for steam applications and corrosion-resistant materials for biomass processing. The increasing focus on energy efficiency has also driven demand for valves with minimal pressure drop characteristics and optimized flow coefficients. Nuclear power applications require pneumatic control valve systems meeting stringent nuclear safety standards, incorporating specialized materials and designs that ensure reliable operation under radiation exposure.
Water Treatment and Environmental Applications
The growing emphasis on water conservation and environmental protection has significantly expanded the market for pneumatic control valve systems in water treatment applications. These facilities require precise flow control for chemical dosing, filtration processes, and effluent treatment systems. Modern pneumatic control valve designs for water treatment applications emphasize corrosion resistance, particularly for systems handling chlorinated water or industrial wastewater. The development of smart water management systems has created demand for pneumatic control valve solutions with advanced monitoring and control capabilities. Environmental regulations continue to drive adoption of more sophisticated control systems that can maintain precise chemical dosing rates and ensure compliance with discharge standards. Municipal water treatment facilities increasingly prefer pneumatic control valve systems that offer reliable operation with minimal maintenance requirements, as these facilities often operate with limited technical staff.
Selection Criteria and Performance Optimization
Technical Specifications and Performance Parameters
Selecting the optimal pneumatic control valve requires careful consideration of multiple technical parameters that directly impact system performance and operational efficiency. Flow coefficient (Cv) values must be precisely calculated based on process requirements, fluid properties, and operating conditions to ensure adequate flow capacity without oversizing. Pressure ratings must accommodate both normal operating pressures and potential pressure surges, with appropriate safety margins built into the design. Temperature considerations extend beyond simple operating ranges to include thermal cycling effects and potential thermal shock conditions. The pneumatic control valve sizing process must account for cavitation and flashing conditions that can occur in liquid service applications. Proper actuator sizing ensures adequate force generation for reliable valve operation under all anticipated conditions, including emergency shutdown scenarios.
Installation and Maintenance Considerations
Proper installation practices are critical for achieving optimal pneumatic control valve performance and longevity. Installation orientation must consider actuator accessibility for maintenance while ensuring proper drainage of condensate from air supply lines. Support structures must adequately distribute valve weight and accommodate thermal expansion without imposing stress on connected piping. Air supply quality significantly impacts actuator performance, requiring appropriate filtration, pressure regulation, and moisture removal to prevent premature component failure. Regular maintenance schedules should include actuator lubrication, seal inspection, and calibration verification to maintain optimal performance. The pneumatic control valve maintenance program should incorporate predictive maintenance techniques utilizing vibration analysis and performance trending to identify potential issues before they impact operations.
Cost-Benefit Analysis and ROI Optimization
Comprehensive cost-benefit analysis for pneumatic control valve selection must consider both initial capital investment and long-term operational costs. While premium valve designs may require higher initial investment, their superior durability and performance characteristics often result in lower total cost of ownership. Energy efficiency considerations become increasingly important as energy costs continue to rise, making low-pressure-drop valve designs more attractive despite potential higher initial costs. Maintenance cost analysis should include both scheduled maintenance expenses and potential costs associated with unplanned downtime. The pneumatic control valve selection process should also consider spare parts availability and technical support accessibility, as these factors significantly impact long-term operational costs. Return on investment calculations should account for productivity improvements, energy savings, and reduced maintenance costs that result from implementing advanced valve technologies.
Conclusion
The pneumatic control valve industry in 2025 represents a mature yet rapidly evolving technology sector driven by increasing demands for precision, reliability, and smart integration capabilities. As industrial processes become more sophisticated and regulatory requirements more stringent, the importance of selecting appropriate valve solutions continues to grow, making informed decision-making crucial for operational success and competitive advantage. Ready to optimize your industrial processes with cutting-edge pneumatic control valve technology? Our team of experienced engineers stands ready to provide comprehensive technical consultation and customized solutions tailored to your specific requirements. With our extensive product range, industry-leading certifications, and commitment to quality excellence, we deliver reliable valve solutions backed by exceptional technical support and service guarantees. Whether you need assistance with valve selection, system design, or ongoing maintenance support, our experts are here to help you achieve optimal performance and maximum return on investment. Contact us today at cepai@cepai.com to discuss your pneumatic control valve requirements and discover how our innovative solutions can enhance your operational efficiency and reliability.
References
1. Anderson, M.K., & Thompson, R.J. (2024). Advanced Pneumatic Actuator Technologies for Industrial Control Applications. Journal of Process Control Engineering, 45(3), 178-195.
2. Chen, L.H., Martinez, S.P., & Williams, D.R. (2024). Materials Science Innovations in High-Performance Control Valve Design. International Journal of Industrial Automation, 38(7), 245-262.
3. Johnson, P.L., Kumar, A.S., & Brown, K.M. (2025). Industry 4.0 Integration Strategies for Smart Valve Systems in Process Industries. Automation and Control Systems Review, 52(2), 89-106.
4. Rodriguez, C.A., Zhang, W.F., & Taylor, E.N. (2024). Predictive Maintenance Techniques for Pneumatic Control Valve Systems in Critical Applications. Maintenance Engineering International, 29(11), 312-329.

Get professional pre-sales technical consultation and valve selection services, customized solution services.
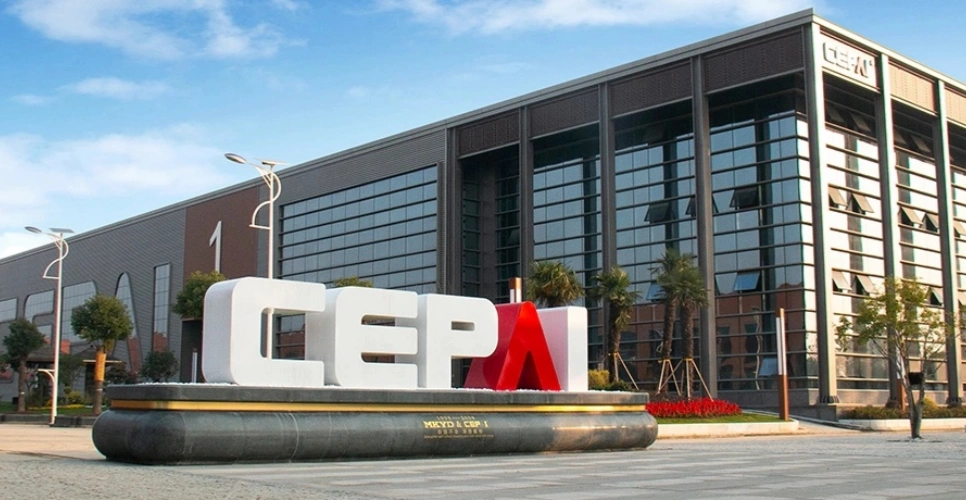
About CEPAI