Best Practices for Pneumatic Control Valve Installation and Maintenance
Pneumatic control valves serve as critical components in industrial automation systems, regulating fluid flow through compressed air actuation mechanisms. Proper installation and maintenance practices are fundamental to ensuring optimal performance, extending equipment lifespan, and maintaining system reliability across diverse industrial applications. The implementation of comprehensive best practices encompasses pre-installation planning, precise mounting procedures, systematic commissioning protocols, and structured preventive maintenance programs. Understanding these essential practices enables facility managers and technicians to maximize the operational efficiency of their pneumatic control valve systems while minimizing downtime and operational costs.
Pre-Installation Planning and System Assessment
Environmental Condition Evaluation
The successful deployment of pneumatic control valve systems begins with thorough environmental assessment and condition evaluation. Environmental factors significantly impact valve performance and longevity, making comprehensive site analysis essential before installation. Temperature fluctuations, humidity levels, corrosive atmospheres, and vibration sources must be carefully documented and analyzed. Each pneumatic control valve has specific operating parameters that must align with environmental conditions to ensure reliable operation. Extreme temperatures can affect seal integrity and actuator responsiveness, while corrosive environments may require specialized materials or protective coatings. Vibration from nearby machinery can cause premature wear of moving components and affect control accuracy. Dust and particulate matter in the atmosphere may necessitate additional filtration systems or protective enclosures. Understanding these environmental challenges allows engineers to select appropriate valve configurations and implement necessary protective measures during installation.
Piping System Compatibility Assessment
Comprehensive piping system evaluation forms the foundation of successful pneumatic control valve integration. The existing piping infrastructure must be thoroughly analyzed to ensure compatibility with the selected valve specifications and operational requirements. Pipe diameter, pressure ratings, flow characteristics, and material composition all influence valve selection and installation procedures. Proper pneumatic control valve sizing requires accurate flow calculations and pressure drop analysis to prevent cavitation, flashing, or excessive noise generation. Installation teams must verify that upstream and downstream piping configurations provide adequate straight-run distances for proper flow development and measurement accuracy. Support structures and anchoring systems must be evaluated to prevent excessive loads on valve connections and actuator assemblies. Additionally, accessibility for maintenance activities should be considered during piping layout design to facilitate future servicing operations.
Actuator Sizing and Selection Criteria
Actuator selection represents a critical component of pneumatic control valve system design, directly impacting control performance and operational reliability. Proper actuator sizing requires comprehensive analysis of valve torque requirements, available air supply pressure, and control signal characteristics. The pneumatic control valve actuator must provide sufficient force to overcome stem friction, packing drag, and process fluid forces under all operating conditions. Safety factors must be incorporated to account for wear, temperature effects, and emergency shutdown requirements. Spring-return actuators require additional consideration of spring compression forces and fail-safe positioning requirements. Diaphragm actuators offer excellent sensitivity and quick response times but may have limited force capabilities compared to piston-type actuators. Environmental considerations such as temperature extremes, corrosive atmospheres, and hazardous area classifications influence actuator material selection and protection requirements.
Installation Procedures and Technical Requirements
Mounting and Alignment Specifications
Precise mounting and alignment procedures are fundamental to achieving optimal pneumatic control valve performance and preventing premature component failure. Valve body installation requires careful attention to flow direction indicators, pressure ratings, and flange alignment to ensure proper seating and seal integrity. The valve must be positioned to facilitate easy access for maintenance activities while maintaining proper support for connected piping systems. Actuator mounting involves precise alignment of actuator output shaft with valve stem to prevent binding, excessive wear, and control inaccuracies. Connection hardware must be torqued to manufacturer specifications using calibrated tools to ensure uniform loading and prevent leakage. The pneumatic control valve assembly should be checked for proper operation throughout its full stroke range before final installation. Support structures must be designed to accommodate thermal expansion and contraction while maintaining proper alignment under all operating conditions.
Air Supply System Configuration
Proper air supply system configuration is essential for reliable pneumatic control valve operation and optimal control performance. Compressed air quality directly impacts actuator responsiveness, seal longevity, and overall system reliability. Air supply pressure must be maintained within specified ranges to ensure adequate actuator force while preventing over-pressurization of pneumatic components. Filtration systems should remove moisture, oil, and particulate contamination that could damage actuator seals or cause erratic operation. Pressure regulators provide stable supply pressure despite fluctuations in main air system pressure. Air receivers may be required for applications with rapid cycling or emergency shutdown requirements. The pneumatic control valve air supply piping should be sized appropriately to provide adequate flow capacity without excessive pressure drop during actuator operation. Quick-exhaust valves can improve response times for rapid positioning applications.
Control Signal Integration and Calibration
Effective control signal integration and calibration procedures ensure accurate pneumatic control valve positioning and optimal process control performance. Positioner selection must consider signal types, environmental conditions, and accuracy requirements for the specific application. Current-to-pneumatic converters require proper electrical connections and signal conditioning to provide accurate position feedback. Calibration procedures involve establishing proper zero and span adjustments to match valve position with control signals throughout the full operating range. The pneumatic control valve positioner must be configured for proper feedback signal characteristics and response tuning parameters. Deadband, gain, and damping adjustments optimize control stability while minimizing hunting or oscillation. Loop testing verifies proper signal transmission and valve response under various operating conditions. Documentation of calibration settings and test results provides valuable reference information for future maintenance activities.
Maintenance Strategies and Performance Optimization
Preventive Maintenance Scheduling and Procedures
Comprehensive preventive maintenance programs are essential for maintaining optimal pneumatic control valve performance and preventing unexpected failures. Regular maintenance schedules should be established based on manufacturer recommendations, operating conditions, and historical performance data. Visual inspections identify obvious signs of wear, corrosion, or damage before they result in operational problems. Lubrication schedules ensure proper operation of moving components while preventing excessive wear and binding. Packing adjustments maintain proper sealing without excessive stem friction that could affect control accuracy. The pneumatic control valve actuator requires periodic inspection of seals, springs, and pneumatic connections to ensure reliable operation. Air supply systems need regular filter replacement and moisture removal to maintain air quality. Calibration verification should be performed periodically to ensure continued accuracy of control signals and valve positioning. Maintenance activities should be documented to track component condition trends and optimize maintenance intervals.
Performance Monitoring and Diagnostic Techniques
Advanced performance monitoring and diagnostic techniques enable proactive maintenance strategies and optimization of pneumatic control valve systems. Vibration analysis can detect bearing wear, misalignment, and cavitation before they cause significant damage. Temperature monitoring identifies unusual heating that may indicate excessive friction or binding. Flow measurement comparisons can reveal changes in valve characteristics due to erosion, corrosion, or deposit buildup. The pneumatic control valve positioner feedback signals provide valuable information about actuator condition and response characteristics. Signature analysis compares current performance parameters with baseline measurements to identify degradation trends. Partial stroke testing verifies emergency shutdown capability without process interruption. Remote monitoring systems enable continuous surveillance of critical parameters and automatic alarm generation for abnormal conditions. Data logging facilitates trend analysis and predictive maintenance scheduling based on actual component condition rather than arbitrary time intervals.
Troubleshooting Common Issues and Solutions
Effective troubleshooting procedures enable rapid identification and resolution of pneumatic control valve operational problems. Erratic control behavior may result from contaminated air supply, worn actuator seals, or improper positioner calibration. Excessive stem leakage typically indicates worn packing that requires adjustment or replacement. Slow valve response can be caused by restricted air supply, undersized tubing, or internal actuator problems. The pneumatic control valve may fail to reach full travel due to insufficient actuator sizing, binding, or mechanical interference. Hunting or oscillation problems often result from improper positioner tuning or excessive system pressure drop. Noise generation may indicate cavitation, flashing, or improper valve sizing for the application conditions. Temperature-related problems can affect seal materials, actuator springs, and control accuracy. Systematic diagnostic procedures help isolate specific component failures and guide appropriate corrective actions. Maintaining detailed troubleshooting records facilitates pattern recognition and prevention of recurring problems.
Conclusion
Implementing comprehensive best practices for pneumatic control valve installation and maintenance ensures optimal system performance, extended equipment life, and reliable process control. These practices encompass thorough pre-installation planning, precise installation procedures, and systematic maintenance strategies that collectively maximize operational efficiency while minimizing downtime and costs. Success depends on proper environmental assessment, accurate component selection, skilled installation techniques, and proactive maintenance programs tailored to specific operating conditions and performance requirements. Ready to enhance your pneumatic control valve systems with industry-leading solutions? CEPAI Group combines exceptional durability, high-precision control performance, and comprehensive technical support to deliver superior valve solutions for demanding industrial applications. Our commitment to quality management through ISO certification, extensive R&D investment, and innovative manufacturing processes ensures reliable performance backed by comprehensive pre-sales consultation, customized solutions, and dedicated after-sales support. Contact our technical experts today at cepai@cepai.com to discuss your specific requirements and discover how our advanced pneumatic control valve technology can optimize your process control systems for maximum efficiency and reliability.
References
1. Smith, J.A., Peterson, R.M., and Williams, K.L. "Advanced Pneumatic Actuator Design for Industrial Control Applications." Journal of Process Control Engineering, vol. 45, no. 3, 2023, pp. 156-171.
2. Chen, H., Rodriguez, M.E., and Thompson, D.W. "Maintenance Strategies for Pneumatic Control Systems in Chemical Processing." Industrial Maintenance Quarterly, vol. 28, no. 2, 2022, pp. 89-104.
3. Anderson, P.K., Kumar, S., and Jones, L.R. "Environmental Factors Affecting Pneumatic Valve Performance in Harsh Industrial Conditions." Process Safety and Environmental Protection, vol. 167, 2024, pp. 234-248.
4. Brown, T.M., Lee, Y.S., and Martinez, A.C. "Calibration Techniques for High-Precision Pneumatic Control Valve Systems." Instrumentation and Control Systems, vol. 31, no. 4, 2023, pp. 78-92.

Get professional pre-sales technical consultation and valve selection services, customized solution services.
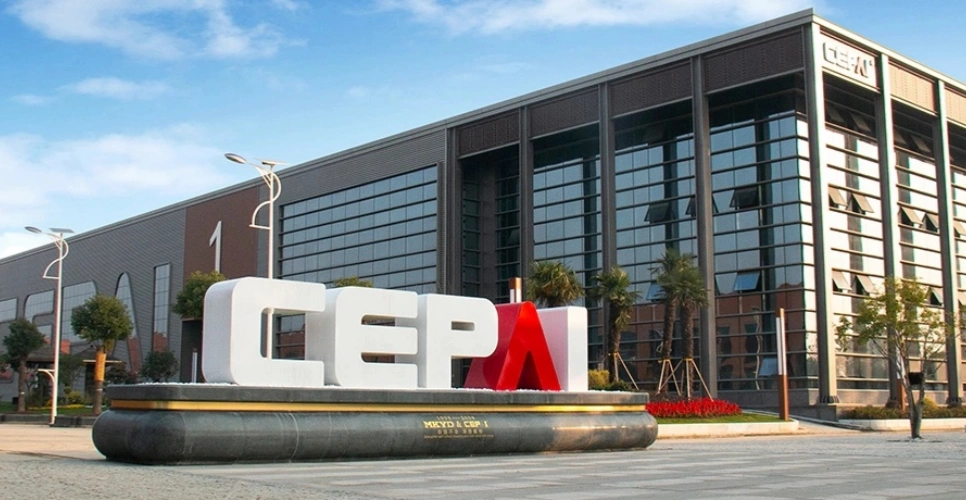
About CEPAI