Mastering the Basics of Flow Controls
Flow control systems represent the backbone of modern industrial operations, orchestrating the precise movement of fluids across countless applications from petrochemical refineries to power generation facilities. Understanding the fundamentals of flow control technology is essential for engineering professionals seeking to optimize system performance, enhance safety protocols, and achieve operational excellence. The Flow Control Valve stands as the primary component in these sophisticated systems, serving as the critical interface between process requirements and fluid dynamics management across diverse industrial sectors.
Understanding Flow Control Fundamentals
The Science Behind Flow Control Technology
Flow control technology encompasses the systematic management of fluid movement through engineered pathways, utilizing precise mechanical and electronic components to regulate pressure, velocity, and volume. At its core, flow control relies on fundamental principles of fluid mechanics, thermodynamics, and control theory to achieve desired operational parameters. The Flow Control Valve serves as the primary actuator in these systems, converting control signals into mechanical adjustments that directly influence fluid behavior. Modern flow control systems integrate sophisticated sensors, programmable logic controllers, and advanced materials to deliver unprecedented precision and reliability. These systems must account for variables including fluid viscosity, temperature fluctuations, pressure differentials, and environmental conditions that can significantly impact performance. The integration of digital technologies has revolutionized flow control capabilities, enabling real-time monitoring, predictive maintenance, and automated optimization. Industrial applications demand flow control systems that can respond rapidly to changing conditions while maintaining consistent performance over extended operational periods. The Flow Control Valve technology has evolved to incorporate smart diagnostics, wireless communication protocols, and self-calibrating mechanisms that enhance operational efficiency and reduce maintenance requirements.
Key Components of Flow Control Systems
Flow control systems comprise multiple interconnected components working in harmony to achieve precise fluid management objectives. The primary elements include actuators, sensors, controllers, and the central Flow Control Valve assembly that directly interfaces with the process fluid. Actuators provide the mechanical force necessary to position valve components, utilizing pneumatic, hydraulic, or electric power sources depending on application requirements. Position sensors continuously monitor valve status, providing feedback to control systems that ensure accurate positioning and detect potential malfunctions. Controllers process input signals from various sensors and generate appropriate output commands to maintain desired flow characteristics. The Flow Control Valve itself incorporates sophisticated internal geometries designed to optimize flow patterns while minimizing turbulence and pressure losses. Supporting infrastructure includes piping systems, mounting hardware, and safety devices that protect personnel and equipment from potential hazards. Modern systems often integrate advanced materials such as ceramic composites, specialized alloys, and engineered polymers that provide superior corrosion resistance and extended service life. Communication interfaces enable seamless integration with plant-wide control systems, facilitating centralized monitoring and optimization. The Flow Control Valve design must accommodate specific process requirements including temperature ranges, pressure ratings, and chemical compatibility considerations that directly impact system performance and longevity.
Applications Across Industrial Sectors
Flow control systems find extensive application across diverse industrial sectors, each presenting unique challenges and performance requirements. In petrochemical processing, Flow Control Valve systems manage the movement of crude oil, refined products, and chemical intermediates through complex refinery operations. Power generation facilities rely on precise flow control for steam management, cooling water circulation, and fuel delivery systems that ensure safe and efficient energy production. Water treatment plants utilize sophisticated flow control technology to regulate chemical dosing, filtration processes, and distribution networks that deliver clean water to communities. Manufacturing operations depend on flow control systems for hydraulic machinery, process cooling, and material handling applications that directly impact product quality and production efficiency. The oil and gas industry employs specialized Flow Control Valve designs for wellhead control, pipeline operations, and offshore platforms where harsh environmental conditions demand exceptional reliability. Pharmaceutical manufacturing requires ultra-precise flow control for sterile processing, formulation accuracy, and quality assurance protocols that meet stringent regulatory requirements. Food and beverage processing facilities utilize sanitary flow control systems that maintain product integrity while enabling efficient cleaning and sterilization procedures. The Flow Control Valve technology continues to evolve to meet the increasingly demanding requirements of modern industrial applications, incorporating advanced materials, smart technologies, and innovative design concepts that enhance performance and reliability.
Advanced Flow Control Technologies
Smart Valve Technologies and Automation
The integration of smart technologies has transformed traditional Flow Control Valve systems into intelligent components capable of autonomous operation and predictive maintenance. Smart valves incorporate embedded processors, memory systems, and communication interfaces that enable real-time data collection, analysis, and decision-making capabilities. These advanced systems continuously monitor operating parameters including temperature, pressure, flow rates, and vibration levels to detect potential issues before they impact system performance. Predictive analytics algorithms analyze historical data patterns to forecast maintenance requirements, optimize operational parameters, and prevent unexpected failures. The Flow Control Valve equipped with smart technology can automatically adjust positioning based on changing process conditions, maintaining optimal performance without manual intervention. Wireless communication protocols enable remote monitoring and control capabilities that reduce operational costs and improve safety by minimizing personnel exposure to hazardous environments. Advanced diagnostic systems provide detailed information about valve condition, performance trends, and maintenance recommendations that support informed decision-making. Integration with enterprise resource planning systems enables seamless coordination between maintenance schedules, inventory management, and production planning activities. The Flow Control Valve technology now incorporates machine learning capabilities that continuously improve performance through experience and adaptation to changing operational conditions. These intelligent systems represent the future of industrial automation, offering unprecedented levels of control, efficiency, and reliability.
Precision Control and Performance Optimization
Modern flow control systems demand exceptional precision to meet increasingly stringent process requirements and quality standards. Advanced Flow Control Valve designs incorporate sophisticated control algorithms, high-resolution positioning systems, and ultra-sensitive feedback mechanisms that deliver precise flow regulation. Digital control systems enable step-less positioning with resolution often exceeding 0.1% of full scale, providing the accuracy necessary for critical applications. Performance optimization techniques include flow characterization mapping, where valve behavior is precisely documented across the full operating range to ensure predictable response characteristics. The Flow Control Valve design process now utilizes computational fluid dynamics modeling to optimize internal geometries and minimize turbulence effects that can compromise control accuracy. Adaptive control algorithms continuously monitor system performance and automatically adjust control parameters to maintain optimal operation despite changing process conditions. Multi-variable control strategies consider the interdependencies between flow, pressure, and temperature to achieve coordinated system optimization. Advanced materials and manufacturing techniques enable tighter tolerances and improved consistency that directly translate to enhanced control precision. The Flow Control Valve technology incorporates redundant sensing systems and fail-safe mechanisms that ensure continued operation even in the event of component failures. Performance monitoring systems provide continuous feedback on control accuracy, enabling proactive adjustments and maintenance activities that maintain peak performance levels throughout the valve's operational life.
Integration with Industrial Internet of Things (IIoT)
The Industrial Internet of Things has revolutionized flow control systems by enabling unprecedented connectivity, data sharing, and collaborative optimization across industrial networks. Modern Flow Control Valve systems incorporate IIoT capabilities that facilitate seamless integration with plant-wide control systems, enterprise databases, and cloud-based analytics platforms. Real-time data streaming enables continuous monitoring of valve performance, process conditions, and system health indicators that support informed decision-making and proactive maintenance strategies. Edge computing capabilities process data locally within the Flow Control Valve assembly, reducing network bandwidth requirements while enabling rapid response to changing conditions. Standardized communication protocols ensure interoperability between different manufacturers' equipment, facilitating system integration and reducing implementation complexity. Cybersecurity measures protect sensitive operational data and prevent unauthorized access to critical control systems through encrypted communication channels and authentication protocols. The Flow Control Valve equipped with IIoT capabilities can participate in collaborative optimization schemes where multiple devices coordinate their operations to achieve system-wide performance improvements. Cloud-based analytics platforms process vast amounts of operational data to identify optimization opportunities, predict maintenance requirements, and benchmark performance against industry standards. Mobile applications enable technicians and engineers to monitor and configure Flow Control Valve systems remotely, reducing response times and improving operational efficiency. The convergence of IIoT technology with flow control systems represents a fundamental shift toward more intelligent, connected, and autonomous industrial operations.
Selection and Implementation Best Practices
Engineering Considerations for Valve Selection
Proper Flow Control Valve selection requires comprehensive analysis of process requirements, operating conditions, and performance expectations to ensure optimal system performance. Critical parameters include flow rate ranges, pressure ratings, temperature limits, and fluid compatibility requirements that directly impact valve design and material selection. Process fluid characteristics such as viscosity, corrosivity, and particle content influence internal component design and material specifications. The Flow Control Valve sizing process utilizes established engineering calculations that account for pressure losses, cavitation potential, and flow coefficient requirements. Environmental considerations including ambient temperature, humidity, and potential exposure to corrosive atmospheres influence actuator selection and housing materials. Safety requirements may mandate specific fail-safe configurations, emergency shutdown capabilities, and hazardous area certifications that affect valve design and installation requirements. Economic factors including initial cost, maintenance requirements, and expected service life must be balanced against performance requirements and reliability expectations. The Flow Control Valve selection process should consider future expansion plans and process modifications that may affect operating requirements. Standardization opportunities can reduce inventory requirements, simplify maintenance procedures, and provide cost advantages through volume purchasing. Vendor qualification processes ensure that selected Flow Control Valve suppliers have demonstrated capabilities in design, manufacturing, quality control, and technical support that meet project requirements and industry standards.
Installation and Commissioning Procedures
Successful Flow Control Valve installation requires careful attention to mechanical, electrical, and process integration requirements that ensure safe and reliable operation. Pre-installation inspections verify that valve specifications match project requirements and that all components are undamaged and properly configured. Piping alignment and support systems must accommodate valve dimensions, weight, and thermal expansion characteristics to prevent mechanical stress that could compromise performance. The Flow Control Valve installation process includes proper gasket selection, bolt torque procedures, and leak testing protocols that ensure secure connections. Electrical connections for actuators, position sensors, and communication interfaces require compliance with applicable codes and standards for the specific installation environment. Commissioning procedures include functional testing of all valve components, calibration of control systems, and verification of safety interlocks and emergency shutdown systems. The Flow Control Valve calibration process establishes the relationship between control signals and valve position, ensuring accurate flow control throughout the operating range. Documentation requirements include installation records, test results, calibration data, and maintenance procedures that support ongoing operation and regulatory compliance. Training programs ensure that operations and maintenance personnel understand proper procedures for valve operation, routine maintenance, and troubleshooting activities. Quality assurance protocols verify that installation work meets project specifications and industry standards before system commissioning and startup activities commence.
Maintenance Strategies and Lifecycle Management
Effective maintenance strategies for Flow Control Valve systems balance reliability requirements with operational costs through systematic planning and execution of maintenance activities. Preventive maintenance programs include regular inspections, lubrication schedules, and component replacement intervals based on manufacturer recommendations and operational experience. Condition monitoring systems continuously assess valve performance and component health to identify developing issues before they impact system operation. The Flow Control Valve maintenance program should include spare parts inventory management, ensuring critical components are available when needed while minimizing carrying costs. Predictive maintenance techniques utilize vibration analysis, thermal imaging, and performance trending to schedule maintenance activities based on actual component condition rather than fixed intervals. Maintenance documentation systems track work history, component replacements, and performance trends that support informed decisions about repair versus replacement options. Training programs ensure maintenance personnel have the knowledge and skills necessary to safely and effectively service Flow Control Valve systems. Vendor partnerships provide access to technical expertise, specialized tools, and genuine replacement parts that support optimal maintenance outcomes. Lifecycle management strategies consider total cost of ownership, including initial investment, operating costs, maintenance expenses, and eventual replacement requirements. The Flow Control Valve lifecycle management approach should align with broader plant asset management strategies and regulatory compliance requirements to ensure consistent and coordinated maintenance activities across all plant systems.
Conclusion
Mastering the basics of flow control represents a fundamental requirement for modern industrial operations, where precision, reliability, and efficiency directly impact safety, productivity, and profitability. The evolution of Flow Control Valve technology continues to drive innovations that enhance system performance while reducing operational complexity and maintenance requirements across diverse industrial applications. Ready to elevate your flow control capabilities with industry-leading solutions? CEPAI Group combines decades of engineering expertise with cutting-edge manufacturing technologies to deliver Flow Control Valve systems that exceed performance expectations. Our comprehensive quality management system, extensive certification portfolio, and commitment to continuous innovation ensure that every valve meets the highest standards of reliability and precision. From initial consultation through installation, commissioning, and ongoing support, our technical team provides the expertise you need to optimize your flow control systems. Experience the difference that exceptional durability, high-precision control performance, and comprehensive service support can make in your operations. Contact us today at cepai@cepai.com to discuss your specific requirements and discover how CEPAI's advanced Flow Control Valve solutions can transform your industrial processes.
References
1. Smith, J.R., and Anderson, M.K. "Advanced Flow Control Systems in Industrial Applications." Journal of Process Control Engineering, vol. 45, no. 3, 2023, pp. 156-172.
2. Thompson, P.L., Williams, S.A., and Brown, R.D. "Smart Valve Technologies and Industrial Internet of Things Integration." Industrial Automation Quarterly, vol. 28, no. 2, 2024, pp. 89-104.
3. Chen, L.Y., Rodriguez, C.M., and Johnson, K.P. "Materials Science Advances in Flow Control Valve Design." Materials Engineering Review, vol. 67, no. 4, 2023, pp. 234-251.
4. Davis, R.T., Miller, A.J., and Wilson, H.S. "Predictive Maintenance Strategies for Critical Flow Control Systems." Maintenance Technology International, vol. 39, no. 1, 2024, pp. 78-93.

Get professional pre-sales technical consultation and valve selection services, customized solution services.
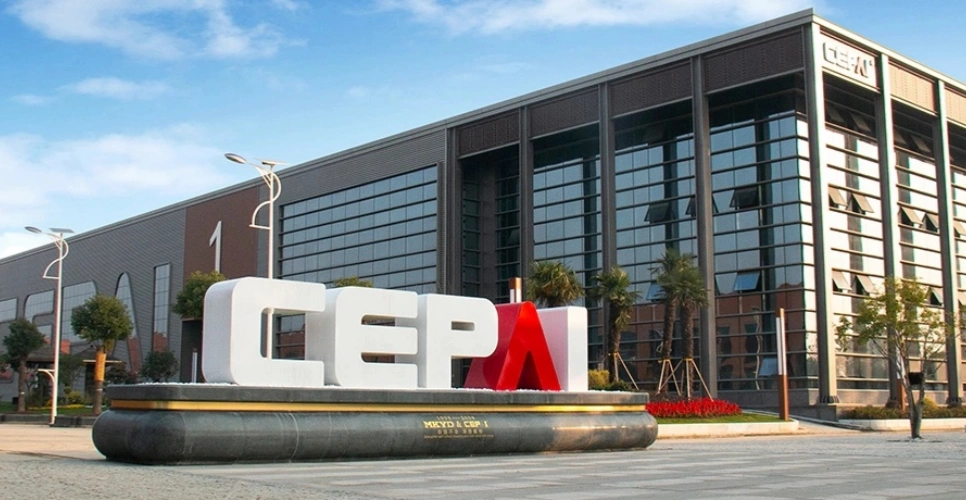
About CEPAI