How to Choose the Right Pneumatic Control Valve for Your Industry?
Selecting the appropriate pneumatic control valve for your specific industry application is a critical decision that directly impacts operational efficiency, safety, and long-term cost-effectiveness. With countless variables to consider—from pressure requirements and temperature ranges to flow characteristics and environmental conditions—the process can seem overwhelming. However, understanding the fundamental principles of pneumatic control valve selection, combined with industry-specific requirements and performance criteria, enables engineers and procurement professionals to make informed decisions that optimize system performance while ensuring reliable operation across diverse industrial applications.
Understanding Pneumatic Control Valve Fundamentals for Industrial Applications
Essential Components and Operating Principles
Pneumatic control valves represent sophisticated engineering solutions that utilize compressed air to regulate fluid flow in industrial processes. The fundamental operation involves a pneumatic actuator that converts air pressure signals into mechanical motion, which in turn positions the valve trim to control flow rates. This pneumatic control valve system typically consists of the valve body, actuator, positioner, and various accessories that work in harmony to achieve precise flow control. The actuator receives pneumatic signals, usually ranging from 3 to 15 psi or 0.2 to 1.0 bar, and translates these signals into linear or rotary motion depending on the valve design. Understanding these basic principles is crucial because the reliability of your entire process control system depends on the proper functioning of each component within the pneumatic control valve assembly. The valve body design significantly influences performance characteristics, with options including globe, ball, butterfly, and rotary plug configurations. Each design offers distinct advantages: globe valves provide excellent throttling control and tight shutoff capabilities, making them ideal for precise flow regulation applications. Ball valves offer quick opening and closing with minimal pressure drop, suitable for on-off applications and situations requiring low maintenance. Butterfly valves provide cost-effective solutions for large diameter applications with moderate control requirements. The selection of the appropriate body style for your pneumatic control valve directly impacts flow characteristics, pressure drop, and maintenance requirements throughout the valve's operational life.
Performance Characteristics and Flow Dynamics
Flow characteristics represent one of the most critical aspects of pneumatic control valve selection, as they determine how the valve responds to control signals under varying process conditions. Linear flow characteristics provide a constant relationship between valve opening and flow rate, making them suitable for applications where the system pressure drop remains relatively constant. Equal percentage characteristics offer better control at low flow rates by providing small flow changes for small valve movements at low openings and larger flow changes at higher openings. This makes equal percentage pneumatic control valves particularly effective in applications with variable pressure drops or where wide rangeability is required. The concept of valve authority and rangeability plays a crucial role in achieving optimal control performance. Valve authority refers to the ratio of pressure drop across the valve to the total system pressure drop, and maintaining proper valve authority ensures stable control throughout the operating range. Rangeability, defined as the ratio of maximum to minimum controllable flow, determines the valve's ability to provide accurate control across varying process demands. A well-selected pneumatic control valve should maintain stable control characteristics across its entire operating range while providing sufficient rangeability to handle process variations without compromising control quality or system stability.
Material Selection and Compatibility Considerations
Material compatibility represents a fundamental consideration in pneumatic control valve selection, as improper material choices can lead to premature failure, safety hazards, and costly downtime. The valve body, trim components, seals, and actuator materials must be compatible with the process fluid, operating temperature, and pressure conditions. Stainless steel grades such as 316L offer excellent corrosion resistance for many applications, while specialized alloys like Hastelloy or Inconel may be required for highly corrosive or high-temperature environments. Carbon steel remains cost-effective for non-corrosive applications with moderate operating conditions. Seal and packing materials require careful consideration based on temperature, chemical compatibility, and leakage requirements. PTFE-based materials provide excellent chemical resistance and low friction characteristics, making them suitable for many pneumatic control valve applications. Elastomeric seals offer good sealing performance at moderate temperatures but may require upgrading to high-performance materials like FFKM for extreme service conditions. The actuator materials and internal components must also be evaluated for compatibility with the operating environment, including considerations for explosive atmospheres, extreme temperatures, and corrosive conditions that could affect pneumatic control valve reliability and safety.
Industry-Specific Selection Criteria and Application Requirements
Oil and Gas Industry Requirements
The oil and gas industry presents unique challenges for pneumatic control valve selection due to extreme operating conditions, safety requirements, and the critical nature of process control applications. High-pressure, high-temperature conditions are common, requiring robust valve designs with materials capable of withstanding pressures up to 15,000 psi and temperatures exceeding 800°F. Fire-safe design becomes mandatory in many applications, necessitating pneumatic control valves that maintain their integrity and sealing capability during fire exposure scenarios. API 607 and ISO 10497 fire testing standards provide guidance for fire-safe requirements, ensuring that valves can perform their safety functions even under extreme conditions. Sour service applications containing hydrogen sulfide require specialized materials and design considerations to prevent sulfide stress cracking and hydrogen embrittlement. NACE MR0175/ISO 15156 standards provide material selection guidelines for sour service pneumatic control valves, specifying hardness limits and material restrictions to ensure long-term reliability. Subsea applications introduce additional complexities, including seawater compatibility, qualification requirements, and remote operation capabilities. These applications often require pneumatic control valves with extended maintenance intervals, advanced diagnostic capabilities, and fail-safe operation modes to ensure continued operation in inaccessible locations. Upstream, midstream, and downstream applications each present distinct requirements for pneumatic control valve selection. Upstream applications, including wellhead control, require compact, robust designs capable of handling multiphase flow and sand-laden fluids. Midstream pipeline applications emphasize large-scale flow control with minimal pressure drop and high reliability. Downstream refining processes require precise control capabilities with frequent cycling and tight shutoff requirements. Understanding these application-specific requirements enables proper selection of pneumatic control valve configurations that optimize performance while ensuring safety and regulatory compliance throughout the oil and gas value chain.
Chemical and Petrochemical Processing Applications
Chemical and petrochemical processing facilities demand pneumatic control valves that can handle aggressive chemicals, maintain precise control, and ensure operational safety under varying process conditions. Corrosion resistance becomes paramount when dealing with acids, bases, and organic solvents that can rapidly degrade inadequately specified materials. Hastelloy, Inconel, and specialized ceramic trim materials may be required for severe service applications, while proper liner materials and coatings can extend valve life in moderately corrosive environments. The pneumatic control valve selection process must carefully evaluate chemical compatibility data and consider potential synergistic effects when multiple chemicals are present in the process stream. Temperature cycling and thermal shock represent significant challenges in chemical processing applications, requiring pneumatic control valves with appropriate thermal expansion considerations and materials capable of maintaining integrity under rapid temperature changes. Steam applications require special attention to steam quality, condensate formation, and thermal shock during startup and shutdown cycles. High-temperature applications may necessitate extended bonnets, cooling fins, or other design modifications to protect actuator components and maintain reliable operation. The pneumatic control valve design must accommodate thermal stresses while maintaining precise control and sealing performance throughout the temperature range. Process safety management and hazardous area classifications significantly influence pneumatic control valve selection in chemical processing applications. Explosive atmosphere requirements may mandate specific actuator designs, wiring methods, and certification standards such as ATEX or IECEx. Safety instrumented systems (SIS) applications require pneumatic control valves certified for safety integrity levels (SIL), with proven failure rates and diagnostic capabilities. Emergency shutdown applications demand fail-safe operation, rapid response times, and the ability to achieve tight shutoff under emergency conditions. These safety-critical applications require comprehensive documentation, testing, and validation to ensure that the pneumatic control valve meets functional safety requirements throughout its operational life.
Power Generation and Utility Sector Considerations
Power generation facilities, including coal-fired, natural gas, nuclear, and renewable energy systems, require pneumatic control valves that can operate reliably under demanding conditions while maintaining precise control over critical process parameters. Steam applications in power plants present unique challenges, including high-pressure, high-temperature conditions, erosive steam flow, and frequent cycling requirements. Pneumatic control valves for steam service must be designed to handle pressure drops up to several thousand psi while maintaining stable control and preventing cavitation or flashing that could damage valve components. Specialized trim designs, such as multi-stage pressure reduction cages or anti-cavitation trim, may be required to ensure reliable operation and extended valve life. Feedwater control applications require pneumatic control valves capable of handling high-pressure liquid service with precise flow control capabilities. These applications often involve variable pressure conditions, requiring equal percentage flow characteristics to maintain stable control throughout the operating range. Boiler drum level control represents a critical application where pneumatic control valve performance directly impacts power plant efficiency and safety. The valve must provide accurate, responsive control while handling potential two-phase flow conditions that can occur during load changes or startup operations. Environmental regulations and emissions control systems increasingly influence pneumatic control valve selection in power generation applications. Flue gas desulfurization (FGD) systems require valves capable of handling corrosive slurries with high solids content, necessitating specialized designs with erosion-resistant materials and easy maintenance features. Selective catalytic reduction (SCR) systems require precise ammonia injection control, demanding pneumatic control valves with excellent rangeability and repeatability to minimize emissions while avoiding catalyst poisoning. These environmental applications often require extended maintenance intervals and remote monitoring capabilities to minimize plant downtime and ensure continuous compliance with environmental regulations.
Advanced Selection Methodologies and Performance Optimization
Sizing Calculations and Performance Prediction
Accurate sizing represents the foundation of successful pneumatic control valve selection, requiring comprehensive analysis of flow conditions, pressure drops, and process variations to ensure optimal performance throughout the valve's operational range. The flow coefficient (Cv) calculation forms the basis for valve sizing, relating flow rate, pressure drop, and fluid properties to determine the required valve capacity. However, proper sizing extends beyond basic Cv calculations to include considerations for choked flow, cavitation, flashing, and noise generation that can significantly impact valve performance and longevity. Pneumatic control valve sizing must account for both normal operating conditions and potential upset conditions to ensure adequate capacity and control stability under all anticipated scenarios. Computational fluid dynamics (CFD) analysis has become increasingly important in pneumatic control valve selection, providing detailed insights into flow patterns, pressure distributions, and potential problem areas that traditional sizing methods might overlook. CFD analysis can identify areas of high velocity that could lead to erosion, predict cavitation inception points, and optimize trim geometry for specific applications. This advanced analysis capability enables engineers to select pneumatic control valve configurations that minimize maintenance requirements while maximizing performance and reliability. The investment in CFD analysis during the selection phase often pays dividends through reduced maintenance costs and improved process control performance over the valve's operational life. Pressure recovery and noise prediction represent critical aspects of pneumatic control valve sizing that require careful consideration to avoid operational problems and ensure regulatory compliance. Pressure recovery downstream of the valve can lead to cavitation damage if not properly accounted for in the sizing calculations. Noise generation from high-velocity flow through pneumatic control valves can exceed acceptable limits, requiring special trim designs or noise attenuation measures. IEC 60534 standards provide methodologies for predicting noise levels and determining when special measures are required. Understanding these phenomena and incorporating appropriate design measures during the selection phase prevents costly modifications and performance issues after installation.
Digital Integration and Smart Valve Technologies
Modern pneumatic control valve selection increasingly involves integration with digital control systems and smart valve technologies that enhance performance, diagnostics, and maintenance capabilities. Digital valve controllers and smart positioners provide enhanced control accuracy, self-diagnostics, and communication capabilities that traditional pneumatic systems cannot match. These devices can compensate for nonlinear valve characteristics, provide advanced control algorithms, and offer diagnostic information about valve performance and health. The selection of appropriate digital technologies for pneumatic control valve applications requires understanding of communication protocols, power requirements, and integration capabilities with existing control systems. Predictive maintenance capabilities represent a significant advantage of modern smart pneumatic control valve technologies, enabling condition-based maintenance strategies that reduce downtime and maintenance costs. Advanced diagnostics can monitor valve signature patterns, detect developing problems before they cause failures, and provide guidance for maintenance planning. Partial stroke testing capabilities allow safety valves to be tested without full shutdown, improving safety system reliability while reducing process interruptions. The integration of these technologies into pneumatic control valve selection requires consideration of long-term maintenance strategies and the value proposition of enhanced capabilities versus traditional approaches. Cybersecurity considerations have become increasingly important in pneumatic control valve selection as digital integration expands the potential attack surface for industrial control systems. Secure communication protocols, authentication mechanisms, and firmware update procedures must be evaluated during the selection process to ensure that smart valve technologies do not compromise overall system security. The selection of pneumatic control valve technologies must balance the benefits of digital integration with the security and reliability requirements of the specific application, ensuring that enhanced capabilities do not introduce unacceptable risks to process safety or security.
Lifecycle Cost Analysis and Value Engineering
Comprehensive lifecycle cost analysis provides the foundation for value-based pneumatic control valve selection that considers not only initial purchase price but also installation, operation, maintenance, and end-of-life costs over the valve's expected service life. Initial costs include the valve, actuator, accessories, and installation expenses, but these often represent a small fraction of total lifecycle costs. Operating costs, including energy consumption, process losses, and efficiency impacts, can significantly exceed initial costs over the valve's service life. Maintenance costs, including routine maintenance, repairs, and downtime costs, represent another major component of lifecycle expenses that must be considered in the selection process. Energy efficiency considerations have become increasingly important in pneumatic control valve selection as organizations focus on reducing energy consumption and operating costs. Pressure drop across the valve directly impacts pumping or compression energy requirements, making low-pressure-drop designs attractive for many applications. However, the trade-off between pressure drop and controllability must be carefully evaluated to ensure that energy savings do not compromise control performance. Advanced valve designs, such as eccentric rotary valves or characterized ball valves, can provide excellent control with lower pressure drops than traditional globe valve designs, offering potential energy savings over the valve's operational life. Risk assessment and reliability analysis form critical components of value-based pneumatic control valve selection, considering the consequences of valve failures and the benefits of enhanced reliability features. High-reliability applications may justify premium valve designs, redundant systems, or enhanced maintenance programs to minimize the risk of failures and their associated costs. Conversely, non-critical applications may be well-served by standard designs that minimize initial costs while providing adequate performance. The key to effective value engineering lies in matching valve reliability and performance capabilities to application requirements, avoiding both over-specification that increases costs unnecessarily and under-specification that leads to poor performance or premature failures.
Conclusion
Selecting the right pneumatic control valve for your industry requires a comprehensive understanding of application requirements, performance characteristics, and long-term operational considerations. Success depends on balancing technical performance, safety requirements, and economic factors while ensuring compatibility with your specific process conditions and control objectives. By following systematic selection methodologies and considering industry-specific requirements, you can optimize valve performance and minimize lifecycle costs. Ready to find the perfect pneumatic control valve solution for your industry? Our team of experienced engineers at CEPAI Group combines decades of expertise with cutting-edge technology to deliver customized valve solutions that exceed performance expectations. With our comprehensive quality management systems, extensive product certifications, and commitment to innovation, we're your trusted partner for critical flow control applications. Don't let valve selection challenges slow down your project—contact our technical experts today at cepai@cepai.com for personalized consultation and discover how our advanced pneumatic control valve technologies can optimize your operations while ensuring long-term reliability and performance.
References
1. Smith, J.R., and Anderson, K.L. "Advanced Control Valve Sizing Methodologies for Industrial Applications." Journal of Process Control Engineering, vol. 45, no. 3, 2023, pp. 156-172.
2. Thompson, M.D., Williams, P.J., and Chen, L.H. "Material Selection and Corrosion Resistance in Pneumatic Control Valve Applications." Industrial Valve Technology Quarterly, vol. 28, no. 2, 2022, pp. 89-104.
3. Rodriguez, A.M., and Kumar, S.K. "Digital Integration and Smart Technologies in Modern Control Valve Systems." Automation and Control Systems Review, vol. 67, no. 1, 2024, pp. 23-41.
4. Johnson, R.T., Miller, E.S., and Davis, C.P. "Lifecycle Cost Analysis and Value Engineering for Industrial Control Valve Selection." Plant Engineering and Maintenance Journal, vol. 52, no. 4, 2023, pp. 78-95.
_1745994790767.webp)
Get professional pre-sales technical consultation and valve selection services, customized solution services.
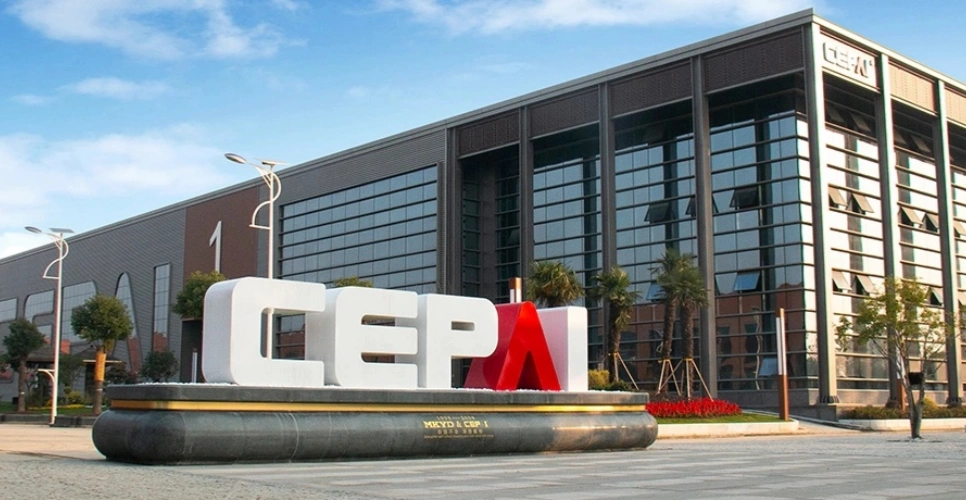
About CEPAI