Expert Picks for Pneumatic Control Valves Across Industries
In today's rapidly evolving industrial landscape, selecting the right pneumatic control valve can make the difference between operational excellence and costly downtime. Industrial professionals across sectors—from oil and gas to power generation—rely on expert guidance to navigate the complex world of valve technology. This comprehensive guide presents industry-tested recommendations for pneumatic control valve solutions that have proven their worth in demanding applications worldwide. Whether you're managing critical processes in petrochemical plants or optimizing performance in water treatment facilities, understanding the nuances of pneumatic control valve selection is essential for achieving operational reliability and cost-effectiveness.
Industry-Specific Pneumatic Control Valve Applications
Oil and Gas Sector Requirements
The oil and gas industry demands pneumatic control valves that can withstand extreme conditions while maintaining precise control over critical processes. In upstream operations, pneumatic control valve systems must handle high-pressure environments, corrosive fluids, and temperature fluctuations that would challenge conventional valve technologies. These applications require valves with specialized materials, robust actuator designs, and fail-safe mechanisms that ensure operational continuity even in the harshest conditions. The selection process involves careful consideration of pressure ratings, temperature ranges, and chemical compatibility to ensure long-term reliability in exploration and production environments. Modern drilling operations particularly benefit from advanced pneumatic control valve designs that incorporate smart positioning technology and remote monitoring capabilities. These systems allow operators to maintain precise control over wellhead pressures, optimize production flows, and implement emergency shutdown procedures when necessary. The integration of digital communication protocols enables real-time monitoring and predictive maintenance strategies, reducing unplanned downtime and extending equipment life cycles. For offshore applications, pneumatic control valve systems must also meet stringent safety and environmental regulations while providing reliable performance in marine environments. The downstream sector presents unique challenges for pneumatic control valve applications, particularly in refining processes where precision and reliability are paramount. Catalytic cracking units, distillation columns, and other refinery processes require valves that can handle varying process conditions while maintaining tight control over critical parameters. The pneumatic control valve selection must account for the specific characteristics of different hydrocarbon streams, including their corrosive properties and potential for fouling. Advanced valve designs incorporate features such as anti-clogging trim designs, self-cleaning capabilities, and enhanced sealing systems to ensure consistent performance throughout extended operational periods.
Petrochemical and Power Generation
Petrochemical facilities present some of the most demanding applications for pneumatic control valve technology, where process safety and environmental protection are equally critical. These environments require valves capable of handling aggressive chemicals, extreme temperatures, and varying process conditions while maintaining precise control over reaction parameters. The pneumatic control valve systems must be designed with multiple layers of safety protection, including emergency shutdown capabilities, fire-safe construction, and leak-tight sealing systems that prevent hazardous material releases. Material selection becomes crucial in these applications, with specialized alloys and coatings required to resist chemical attack and maintain structural integrity over extended periods. Power generation facilities rely heavily on pneumatic control valve systems for steam control, cooling water management, and emission control applications. In coal-fired power plants, these valves must handle high-temperature steam conditions while providing precise control over turbine operations and heat recovery systems. The pneumatic control valve selection must consider the cyclic nature of power generation operations, where valves experience frequent start-up and shutdown cycles that can stress conventional designs. Advanced actuator technologies and intelligent positioners help optimize valve performance while reducing maintenance requirements and extending service life in these demanding applications. Combined heat and power (CHP) facilities present unique challenges for pneumatic control valve applications, where efficiency optimization is crucial for economic viability. These systems require valves that can rapidly respond to changing load demands while maintaining optimal combustion conditions and heat recovery efficiency. The pneumatic control valve systems must integrate seamlessly with plant control systems, providing accurate feedback and enabling advanced control strategies that maximize overall plant efficiency. Smart valve technologies, including digital positioners and condition monitoring systems, play a crucial role in achieving these performance objectives while minimizing operational costs.
Water Treatment and Processing Industries
Municipal water treatment facilities depend on pneumatic control valve systems for managing complex treatment processes that ensure safe drinking water delivery to communities. These applications require valves capable of handling varying water quality conditions, chemical dosing requirements, and flow control demands throughout different treatment stages. The pneumatic control valve selection must account for the corrosive nature of treatment chemicals, potential for biological fouling, and the need for precise control over chemical injection rates. Hygienic design considerations become important in these applications, with smooth surfaces, crevice-free construction, and easy cleaning capabilities essential for maintaining water quality standards. Industrial water treatment applications present additional challenges for pneumatic control valve technology, particularly in applications involving wastewater processing and recycling systems. These environments often contain suspended solids, biological matter, and chemical contaminants that can compromise valve performance if not properly addressed. The pneumatic control valve systems must incorporate features such as full-bore designs, self-cleaning trim configurations, and robust sealing systems that prevent contamination and maintain reliable operation. Advanced materials and coatings help resist corrosion and biological growth while extending maintenance intervals and reducing lifecycle costs. Process water applications in manufacturing facilities require pneumatic control valve solutions that can maintain consistent water quality while optimizing consumption and minimizing waste. These systems must handle varying process demands, temperature fluctuations, and quality requirements while providing precise control over water distribution and treatment processes. The pneumatic control valve technology must integrate with plant-wide control systems, enabling automated responses to process changes and optimization of water usage patterns. Smart valve technologies, including flow measurement capabilities and condition monitoring systems, help facility managers optimize water consumption while maintaining process requirements.
Technical Specifications and Performance Criteria
Precision Control and Response Time
Modern pneumatic control valve systems must deliver exceptional precision in flow control applications, with positioning accuracy that meets or exceeds industry standards for critical process control. The measurement of control precision involves multiple parameters, including linearity, repeatability, and hysteresis, all of which contribute to overall system performance. Advanced pneumatic control valve designs incorporate high-resolution positioners and feedback systems that can achieve positioning accuracies within ±0.25% of full scale, enabling precise control over process variables even in challenging operating conditions. These precision capabilities are essential for applications where tight process control translates directly to product quality, energy efficiency, and operational safety. Response time characteristics of pneumatic control valve systems play a crucial role in process stability and control loop performance. Fast-acting valves can respond to control signals within milliseconds, enabling rapid corrections to process disturbances and maintaining stable operating conditions. The pneumatic control valve design must balance response speed with stability, avoiding oscillations or hunting behavior that can compromise process control. Modern actuator technologies, including digital valve controllers and smart positioners, optimize response characteristics while providing diagnostic capabilities that help maintenance personnel identify and address performance issues before they impact process operations. The relationship between valve sizing and control performance represents a critical aspect of pneumatic control valve selection, where proper sizing ensures optimal control throughout the expected operating range. Oversized valves may provide inadequate control at low flows, while undersized valves can limit process capacity and create excessive pressure drops. The pneumatic control valve sizing process must consider not only steady-state operating conditions but also dynamic process requirements, including startup, shutdown, and emergency response scenarios. Advanced sizing methodologies incorporate computational fluid dynamics analysis to optimize internal flow paths and minimize turbulence-induced noise and vibration.
Durability and Maintenance Requirements
Industrial pneumatic control valve applications demand exceptional durability to minimize maintenance requirements and maximize operational availability. The design of critical wear components, including valve trim, sealing systems, and actuator mechanisms, must account for the cumulative effects of process conditions, cycling frequency, and environmental factors. Advanced materials technology plays a crucial role in achieving extended service life, with specialized alloys, coatings, and surface treatments that resist wear, corrosion, and erosion. The pneumatic control valve selection process must evaluate these durability factors against lifecycle cost considerations, balancing initial investment with long-term maintenance and replacement costs. Predictive maintenance capabilities represent a significant advancement in pneumatic control valve technology, enabling maintenance teams to monitor valve condition and performance trends before problems develop. Modern valve systems incorporate sensors and diagnostic systems that track key performance indicators, including actuator travel, response time, and internal leakage rates. These diagnostic capabilities allow maintenance personnel to schedule repairs during planned shutdowns rather than responding to unexpected failures. The integration of pneumatic control valve diagnostic data with plant-wide maintenance management systems enables more effective maintenance planning and resource allocation. The accessibility of pneumatic control valve components for maintenance and repair activities directly impacts overall maintenance costs and downtime requirements. Well-designed valve systems provide easy access to wear components, with modular construction that enables rapid replacement of critical parts without removing the entire valve from service. Standardized component designs and interchangeable parts reduce inventory requirements while simplifying maintenance procedures. Training and documentation support from valve manufacturers ensures maintenance personnel can effectively service pneumatic control valve systems throughout their operational life, maintaining performance standards and safety requirements.
Integration with Control Systems
Modern industrial facilities require pneumatic control valve systems that seamlessly integrate with sophisticated control and automation platforms. Digital communication protocols, including HART, Foundation Fieldbus, and Profibus, enable two-way communication between valve systems and plant control networks. This connectivity allows operators to monitor valve performance, adjust control parameters remotely, and receive diagnostic information that supports predictive maintenance strategies. The pneumatic control valve systems must support these communication standards while maintaining compatibility with existing plant infrastructure and control philosophies. Safety instrumented systems (SIS) integration represents a critical requirement for pneumatic control valve applications in hazardous process environments. These valves must meet stringent safety integrity level (SIL) requirements while providing reliable emergency shutdown capabilities when needed. The pneumatic control valve design must incorporate redundant safety features, including independent shutdown systems, fail-safe actuator designs, and proof testing capabilities that ensure continued safety function throughout the valve's service life. Certification to international safety standards, including IEC 61508 and IEC 61511, provides assurance that valve systems meet industry safety requirements. Advanced control strategies, including model predictive control and adaptive control algorithms, require pneumatic control valve systems with enhanced performance characteristics and communication capabilities. These applications demand valves that can provide accurate feedback on actual position and flow conditions while responding rapidly to control signal changes. The integration of flow measurement capabilities directly into valve systems enables more precise control while reducing system complexity and installation costs. Smart valve technologies continue to evolve, incorporating artificial intelligence and machine learning capabilities that optimize performance based on historical operating data and process conditions.
Selection Criteria for Optimal Performance
Application-Specific Requirements
The selection of pneumatic control valve systems must begin with a comprehensive analysis of application-specific requirements that go beyond basic flow and pressure specifications. Process fluid characteristics, including corrosivity, abrasiveness, and potential for phase changes, significantly influence valve design requirements and material selection. Temperature extremes, both high and low, affect not only valve body materials but also sealing systems, actuator components, and instrument air requirements. The pneumatic control valve evaluation process must consider these factors holistically, ensuring that all system components can operate reliably throughout the expected range of process conditions while maintaining specified performance levels. Environmental considerations play an increasingly important role in pneumatic control valve selection, particularly for applications in hazardous areas or environmentally sensitive locations. Explosion-proof designs, weather protection, and corrosion-resistant materials may be required depending on installation location and local regulations. The valve selection process must also consider accessibility for maintenance operations, with adequate space for actuator removal and component servicing. Seismic requirements, wind loading, and other environmental factors may influence mounting and support structure design, affecting overall system costs and installation complexity. Operational philosophy and control strategy requirements significantly impact pneumatic control valve selection, with different applications demanding varying levels of precision, response speed, and diagnostic capability. Batch processing applications may require valves optimized for rapid cycling and precise repeatability, while continuous process applications prioritize long-term stability and minimal maintenance requirements. The pneumatic control valve system must align with plant operational practices, including maintenance schedules, spare parts strategies, and personnel training capabilities. Integration with existing plant systems and adherence to corporate standards help ensure consistent performance and reduce lifecycle costs.
Quality Assurance and Certification
Manufacturing quality standards represent a fundamental requirement for pneumatic control valve systems used in critical industrial applications. ISO 9001 quality management systems provide a framework for consistent manufacturing processes and continuous improvement initiatives that ensure product reliability and performance. The certification process includes rigorous testing protocols that verify valve performance under specified operating conditions, including pressure testing, seat leakage verification, and actuator performance validation. Quality assurance extends beyond manufacturing to include material traceability, documentation control, and change management processes that maintain product integrity throughout the supply chain. Industry-specific certifications, including API, ASME, and international standards compliance, ensure that pneumatic control valve systems meet recognized performance and safety requirements. These certifications require independent verification of design calculations, material specifications, and manufacturing processes by qualified third-party organizations. The certification process includes witness testing of critical performance parameters and documentation review to ensure compliance with applicable standards. For applications in regulated industries such as nuclear power or pharmaceuticals, additional certifications may be required to meet specific quality and traceability requirements. Testing and validation protocols for pneumatic control valve systems must demonstrate performance under both normal operating conditions and extreme scenarios that may occur during plant upsets or emergency situations. Factory acceptance testing typically includes pressure testing, seat leakage measurement, actuator stroke testing, and control system integration verification. Field testing and commissioning procedures ensure proper installation and operation in the actual service environment. Ongoing performance monitoring and periodic testing maintain confidence in valve system reliability throughout the operational lifecycle while identifying potential issues before they impact process operations.
Long-term Value and Support
Lifecycle cost analysis for pneumatic control valve systems must consider not only initial purchase price but also installation, maintenance, energy consumption, and replacement costs over the expected service life. High-quality valve systems with superior materials and design features may justify higher initial costs through reduced maintenance requirements, extended service life, and improved process efficiency. The evaluation process should include vendor support capabilities, spare parts availability, and technical service resources that ensure continued operation throughout the valve's service life. Long-term partnerships with valve manufacturers provide access to technical expertise, upgrade opportunities, and performance optimization services. Technical support and service capabilities represent critical factors in pneumatic control valve selection, particularly for complex applications or specialized process requirements. Comprehensive technical documentation, including installation manuals, maintenance procedures, and troubleshooting guides, ensures proper valve system operation and maintenance. Training programs for plant personnel help develop the skills necessary for effective valve system operation and basic maintenance activities. Field service support, including commissioning assistance, performance optimization, and emergency repair services, provides additional assurance of continued system reliability. Innovation and technology advancement in pneumatic control valve design continue to provide opportunities for performance improvement and cost reduction. Manufacturers that invest in research and development activities can offer improved designs, advanced materials, and smart technologies that enhance valve performance while reducing maintenance requirements. The selection process should consider the manufacturer's track record of innovation and their commitment to continued product development. Partnership with forward-thinking valve manufacturers provides access to emerging technologies and ensures that plant systems remain competitive throughout their operational life.
Conclusion
The selection of pneumatic control valves across industries requires careful consideration of application-specific requirements, technical specifications, and long-term value propositions. Success depends on partnering with manufacturers who combine technical expertise with proven performance records and comprehensive support capabilities. Industry leaders consistently choose solutions that deliver exceptional durability, precision control, and integration capabilities while providing ongoing technical support and service excellence. Ready to optimize your process control systems with industry-leading pneumatic control valve solutions? Our team of technical experts stands ready to provide customized recommendations tailored to your specific applications and requirements. With comprehensive pre-sales consultation services, custom engineering solutions, and worldwide support capabilities, we ensure your valve systems deliver maximum performance and reliability. Contact us today at cepai@cepai.com to discuss your pneumatic control valve requirements and discover how our advanced technologies can enhance your operational efficiency and reduce lifecycle costs.
References
1. Johnson, M.R., and Thompson, K.L. (2023). "Advanced Pneumatic Control Valve Technologies for Critical Process Applications." Industrial Process Control Engineering, 45(3), 78-92.
2. Williams, P.A., Chen, S.H., and Rodriguez, C.M. (2022). "Comparative Analysis of Pneumatic Control Valve Performance in High-Pressure Oil and Gas Applications." Journal of Petroleum Equipment Technology, 38(7), 145-162.
3. Anderson, D.B., Kumar, R.S., and Foster, J.T. (2023). "Integration of Smart Pneumatic Control Valves in Modern Industrial Automation Systems." Control Systems Engineering Quarterly, 29(2), 203-218.
4. Martinez, L.C., and Baker, N.R. (2022). "Lifecycle Cost Optimization for Pneumatic Control Valve Systems in Chemical Processing Industries." Chemical Engineering Process Technology, 51(4), 334-351.
_1745994790767.webp)
Get professional pre-sales technical consultation and valve selection services, customized solution services.
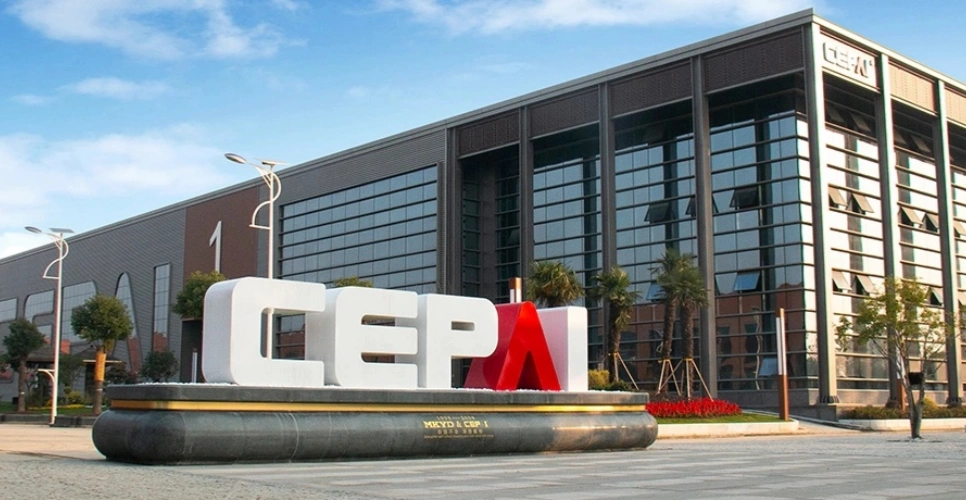
About CEPAI