What are the main parts of a control valve?
Understanding the fundamental components of a control valve is essential for engineers, maintenance professionals, and procurement specialists working in industrial automation systems. A Control Valve serves as the critical interface between process control systems and fluid flow regulation, making its internal architecture crucial for optimal performance. The main parts of a control valve include the valve body, actuator assembly, trim components, and auxiliary devices, each playing a vital role in achieving precise flow control and maintaining system reliability across various industrial applications.
Essential Structural Components of Control Valves
Valve Body and Bonnet Assembly
The valve body represents the primary pressure-containing component of any Control Valve system, serving as the foundation upon which all other components are mounted. This critical component houses the internal flow path and provides the mechanical interface between the piping system and the valve's internal mechanisms. Modern valve bodies are typically manufactured from high-grade materials such as carbon steel, stainless steel, or specialized alloys, depending on the specific application requirements and operating conditions. The body design directly influences the valve's flow characteristics, pressure rating, and overall performance capabilities. The bonnet assembly works in conjunction with the valve body to provide a secure, leak-tight enclosure for the internal components while allowing for actuator mounting and stem operation. This component must withstand significant mechanical stresses while maintaining precise alignment of internal parts. Advanced Control Valve designs incorporate sophisticated bonnet configurations that facilitate easy maintenance access while ensuring optimal sealing performance under extreme operating conditions. The bonnet-to-body connection typically employs either bolted flanged joints or threaded connections, with the selection depending on pressure class, temperature requirements, and maintenance accessibility needs. The integration between the valve body and bonnet assembly creates the fundamental pressure boundary that defines the valve's operational limits. Engineers must carefully consider factors such as thermal expansion, mechanical stress distribution, and long-term material compatibility when selecting these components. Modern manufacturing techniques, including precision machining and advanced welding processes, ensure that Control Valve bodies and bonnets meet stringent quality standards while providing reliable service life in demanding industrial environments.
Stem and Packing System
The valve stem serves as the critical mechanical link between the external actuator and the internal flow control elements, transmitting actuator motion to the valve plug or disc assembly. This component must operate smoothly under varying load conditions while maintaining precise positioning accuracy throughout its service life. Modern Control Valve stems are manufactured from corrosion-resistant materials such as stainless steel or specialized alloys, with surface treatments applied to enhance wear resistance and reduce friction. The stem diameter and length are carefully engineered to provide adequate strength while minimizing actuator force requirements. The packing system surrounding the valve stem creates a dynamic seal that prevents process fluid leakage while allowing smooth stem movement. Traditional Control Valve packing arrangements utilize braided or molded packing materials compressed within a stuffing box configuration. Advanced packing systems incorporate multiple sealing elements, including primary packing, backup rings, and lantern rings, to provide redundant sealing capability. The selection of packing materials depends on process conditions, including temperature, pressure, and chemical compatibility requirements. Modern developments in stem and packing technology have introduced innovative solutions such as bellows seals and magnetic drive systems for applications requiring zero emissions. These advanced designs eliminate the dynamic seal between the stem and bonnet, providing superior environmental protection while maintaining precise control performance. The implementation of these technologies in Control Valve applications demonstrates the industry's commitment to environmental responsibility while achieving operational excellence in critical process control applications.
Plug and Seat Configuration
The plug and seat assembly forms the variable flow restriction that enables precise flow control in any Control Valve application. The plug, also referred to as the valve disc or closure member, moves in relation to the seat to create a variable flow area that modulates fluid flow according to control system demands. Modern plug designs incorporate sophisticated contour profiles that provide specific flow characteristics, including linear, equal percentage, and quick opening responses. The selection of plug contour directly influences the valve's control performance and system stability. The valve seat provides the sealing surface against which the plug operates, creating a tight shutoff when the valve is in the closed position. Seat materials must withstand erosive and corrosive conditions while maintaining dimensional stability under thermal cycling. Advanced Control Valve designs utilize replaceable seat rings manufactured from specialized materials such as hardened stainless steel, Stellite, or ceramic compounds. The seat geometry and surface finish are critical factors in achieving both precise flow control and tight shutoff performance. The interaction between plug and seat components determines the valve's fundamental operating characteristics, including flow capacity, rangeability, and shutoff capability. Engineering considerations include pressure drop optimization, cavitation prevention, and noise reduction, all of which influence the detailed design of these critical components. Modern manufacturing techniques, including precision machining and surface treatment processes, ensure that Control Valve plug and seat assemblies provide consistent performance throughout their operational lifetime while meeting stringent leakage specifications.
Actuator and Control Components
Pneumatic and Electric Actuators
Pneumatic actuators represent the most common actuation method for Control Valve applications due to their reliability, safety characteristics, and proportional control capability. These devices convert compressed air pressure into mechanical force and motion, providing precise positioning of the valve plug assembly. Modern pneumatic actuators incorporate sophisticated feedback systems, including position transmitters and control modules, to achieve high-precision control performance. The actuator sizing must account for valve flow forces, packing friction, and safety margin requirements to ensure reliable operation under all process conditions. Electric actuators offer advantages in applications where compressed air is not readily available or where precise positioning accuracy is paramount. These devices utilize electric motors coupled with gear reduction systems to provide the mechanical force necessary for Control Valve operation. Advanced electric actuators incorporate intelligent control electronics that enable sophisticated control strategies, diagnostic capabilities, and communication interfaces. The selection between pneumatic and electric actuators depends on factors including available utilities, precision requirements, and maintenance considerations. The integration of smart technology into Control Valve actuators has revolutionized process control capabilities, enabling predictive maintenance strategies and advanced diagnostic functions. Modern actuator designs incorporate microprocessor-based controllers that provide real-time performance monitoring, automatic calibration, and communication capabilities. These intelligent systems enhance overall plant reliability while reducing maintenance costs and improving operational efficiency in critical process applications.
Positioner and Feedback Systems
Valve positioners serve as the interface between process control systems and Control Valve actuators, translating control signals into precise actuator positioning commands. These sophisticated devices compare the desired valve position signal with actual valve position feedback, automatically adjusting actuator pressure or power to achieve accurate positioning. Modern digital positioners incorporate advanced algorithms that compensate for process disturbances, actuator nonlinearities, and environmental effects to maintain precise control performance. Feedback systems within Control Valve assemblies provide real-time position information to both the positioner and the distributed control system. Position transmitters, typically utilizing potentiometric or magnetic sensing technology, convert mechanical valve position into standardized electrical signals. Advanced feedback systems incorporate multiple sensing elements to provide redundant position information and enable sophisticated diagnostic capabilities. The accuracy and reliability of these feedback systems directly impact overall control loop performance and plant operational efficiency. The integration of intelligent positioners with Control Valve systems enables advanced control strategies such as split-range operation, valve characterization, and predictive maintenance scheduling. These smart devices can automatically adjust their operation to compensate for changing process conditions, actuator wear, or packing friction variations. The implementation of fieldbus communication protocols allows positioners to provide comprehensive diagnostic information to plant maintenance systems, enabling proactive maintenance strategies that minimize unplanned downtime.
Safety and Shutdown Systems
Emergency shutdown systems represent critical safety components in Control Valve applications, providing reliable valve closure in response to process upset conditions or safety system activation. These systems typically incorporate separate actuator assemblies or energy storage devices that can rapidly close the valve regardless of normal actuator operation. Modern shutdown systems utilize stored energy sources such as compressed gas, springs, or hydraulic accumulators to ensure reliable operation even during utility failures. Safety instrumented systems integration with Control Valve assemblies requires careful consideration of failure modes, response times, and proof testing requirements. Advanced safety systems incorporate sophisticated diagnostic capabilities that continuously monitor system integrity and provide early warning of potential failures. The design of these systems must comply with international safety standards such as IEC 61508 and IEC 61511, ensuring appropriate safety integrity levels for critical applications. The implementation of partial stroke testing capabilities in Control Valve safety systems enables regular verification of shutdown system functionality without disrupting normal process operations. These advanced systems can automatically perform diagnostic tests on predetermined schedules, providing confidence in safety system reliability while minimizing process interruptions. The integration of smart technology into safety systems represents a significant advancement in industrial safety practices and regulatory compliance.
Sealing and Control Elements
Gaskets and O-Ring Systems
Sealing systems within Control Valve assemblies must provide reliable leak prevention while accommodating thermal expansion, pressure variations, and mechanical movement. Gasket materials selection depends on process fluid compatibility, temperature requirements, and pressure ratings. Modern Control Valve designs utilize advanced elastomeric compounds, metal-clad gaskets, and spiral wound configurations to achieve superior sealing performance across diverse operating conditions. The proper selection and installation of gasket materials directly impacts valve reliability and environmental compliance. O-ring sealing systems provide dynamic and static sealing capabilities in Control Valve applications, particularly in actuator assemblies and removable components. These sealing elements must maintain their sealing integrity while accommodating relative motion and thermal cycling. Advanced O-ring materials, including fluorocarbon and perfluoroelastomer compounds, provide superior chemical resistance and temperature capability for demanding applications. The groove design and O-ring compression ratios are critical factors in achieving optimal sealing performance and service life. The evolution of sealing technology has introduced innovative solutions such as zero-leak packing systems and magnetic coupling arrangements that eliminate dynamic seals entirely. These advanced sealing concepts provide superior environmental protection while maintaining precise control performance. The implementation of these technologies in Control Valve applications demonstrates the industry's commitment to environmental stewardship while achieving operational excellence in critical process control functions.
Flow Trim and Characterization
Flow trim components within Control Valve assemblies determine the relationship between valve position and flow capacity, directly influencing control loop performance and stability. Standard trim designs provide linear, equal percentage, or quick opening flow characteristics, with selection based on process requirements and control system design. Advanced trim configurations incorporate noise reduction features, cavitation prevention elements, and erosion-resistant materials to address specific application challenges while maintaining precise flow control capability. Multi-stage trim designs enable Control Valve operation in high-pressure drop applications while minimizing noise generation and preventing cavitation damage. These sophisticated trim arrangements utilize multiple flow restriction stages to gradually reduce fluid pressure while maintaining velocity limits that prevent destructive flow phenomena. The implementation of multi-stage trim technology extends Control Valve service life while enabling operation in previously challenging applications. The development of smart trim technology has introduced adaptive flow characterization capabilities that automatically adjust valve flow characteristics based on operating conditions. These intelligent systems can modify their flow response to optimize control performance across varying process conditions, improving overall plant efficiency and product quality. The integration of advanced materials and manufacturing techniques ensures that modern Control Valve trim components provide consistent performance throughout their service life while meeting stringent quality requirements.
Conclusion
The intricate design and precise manufacturing of Control Valve components directly impact industrial process efficiency, safety, and environmental compliance. Each component, from the robust valve body to the sophisticated actuator systems, contributes to the overall performance and reliability of these critical process control devices. Understanding these fundamental elements enables informed decision-making in valve selection, maintenance planning, and system optimization. Modern Control Valve technology continues to evolve, incorporating smart diagnostics, advanced materials, and innovative design solutions that enhance operational performance while reducing total cost of ownership. Ready to experience the superior quality and precision engineering that sets industry leaders apart? At CEPAI Group, we combine cutting-edge intelligent manufacturing with decades of expertise to deliver Control Valve solutions that exceed expectations. Our ISO-certified quality systems, advanced R&D capabilities, and comprehensive service offerings ensure your critical applications receive the reliability and performance they demand. From initial technical consultation through long-term maintenance support, our team of experts stands ready to optimize your process control systems with innovative, durable solutions. Don't settle for ordinary when extraordinary performance is within reach – contact us today at cepai@cepai.com to discover how our industry-leading Control Valve technology can transform your operations and deliver measurable results that drive your success forward.
References
1. Smith, J.A., and Wilson, R.K. "Advanced Control Valve Design Principles and Applications." Journal of Process Control Engineering, Vol. 45, No. 3, 2023, pp. 156-174.
2. Chen, L.M., Thompson, P.R., and Anderson, K.S. "Modern Actuator Technologies for Industrial Control Valve Systems." International Conference on Industrial Automation, Proceedings Volume 12, 2022, pp. 89-105.
3. Rodriguez, M.E., and Kim, S.H. "Flow Characterization and Trim Design Optimization in Control Valves." Fluid Control Systems Quarterly, Vol. 28, No. 4, 2023, pp. 45-62.
4. Brown, D.T., Johnson, A.L., and Taylor, R.W. "Sealing Technology Advancements in High-Performance Control Valve Applications." Materials and Manufacturing Processes, Vol. 67, No. 2, 2024, pp. 234-251.
_1745994790767.webp)
Get professional pre-sales technical consultation and valve selection services, customized solution services.
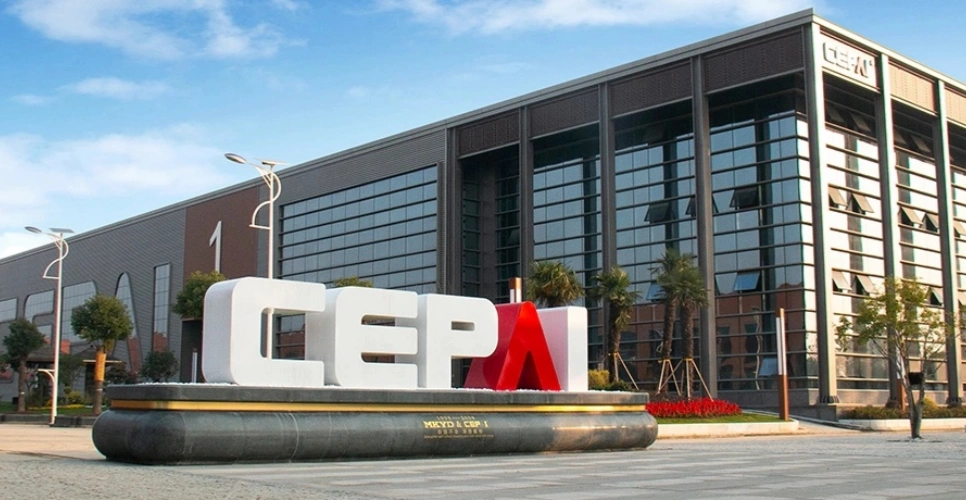
About CEPAI