Top Corrosion-Resistant Control Valves for Chemical Plants
Chemical processing facilities face unprecedented challenges when it comes to selecting appropriate flow control equipment that can withstand aggressive chemical environments. The harsh operating conditions in chemical plants, including exposure to corrosive acids, alkalis, and other reactive substances, demand specialized equipment that combines superior materials engineering with advanced design principles. Corrosion Resistant Valve technology has evolved significantly to address these critical industrial requirements, offering enhanced durability, precise control capabilities, and extended operational lifecycles that directly impact plant efficiency and safety protocols.
Essential Features of Industrial Corrosion-Resistant Control Valves
Advanced Material Engineering for Chemical Resistance
The foundation of any effective Corrosion Resistant Valve lies in its material composition and engineering design. Modern chemical plants require valves constructed from specialized alloys such as Hastelloy C-276, Inconel 625, and duplex stainless steels that demonstrate exceptional resistance to pitting, crevice corrosion, and stress corrosion cracking. These advanced materials undergo rigorous testing protocols including ASTM G48 pitting resistance tests and NACE MR0175 compliance verification to ensure they can withstand the most demanding chemical environments. The selection of appropriate materials involves comprehensive analysis of the process fluid chemistry, operating temperatures, pressure ranges, and cyclic loading conditions. Additionally, specialized surface treatments such as electropolishing and passivation enhance the natural corrosion resistance properties of these materials, creating a protective oxide layer that serves as a barrier against chemical attack. The metallurgical structure of these alloys is carefully controlled during manufacturing to optimize grain boundary chemistry and eliminate potential corrosion initiation sites.
Precision Control Technology and Performance Optimization
Contemporary Corrosion Resistant Valve systems incorporate sophisticated control technologies that enable precise flow regulation while maintaining structural integrity under corrosive conditions. Advanced actuator systems, including electric, pneumatic, and hydraulic configurations, are designed with corrosion-resistant components and protective coatings to ensure reliable operation in harsh chemical environments. These control systems feature enhanced sealing technologies utilizing PTFE, PEEK, and specialized elastomeric compounds that resist chemical degradation while maintaining tight shutoff capabilities. The integration of smart positioner technology allows for real-time monitoring of valve performance parameters, including stem position feedback, actuator pressure monitoring, and diagnostic capabilities that predict maintenance requirements before critical failures occur. Furthermore, these systems incorporate fail-safe mechanisms and emergency shutdown capabilities that are essential for chemical plant safety protocols, ensuring that process control is maintained even during power failures or system malfunctions.
Quality Assurance and Testing Protocols
The manufacturing and quality control processes for Corrosion Resistant Valve systems follow stringent international standards and testing protocols to ensure consistent performance and reliability. Each valve undergoes comprehensive material verification through spectroscopic analysis, dimensional inspection according to API and ASME standards, and extensive pressure testing including hydrostatic and pneumatic leak detection procedures. Advanced non-destructive testing methods such as liquid penetrant inspection, magnetic particle testing, and ultrasonic examination are employed to detect any potential material defects or manufacturing anomalies. The quality management system encompasses incoming material inspection, in-process monitoring, and final product testing to maintain zero-defect manufacturing standards. Additionally, specialized corrosion testing protocols simulate actual plant operating conditions, including exposure to specific chemical media, temperature cycling, and long-term immersion studies to validate the expected service life and performance characteristics of each valve design.
Selection Criteria for Chemical Plant Applications
Process Compatibility and Chemical Resistance Assessment
Selecting the appropriate Corrosion Resistant Valve for specific chemical plant applications requires comprehensive analysis of process parameters and chemical compatibility factors. The evaluation process begins with detailed characterization of the process fluid, including chemical composition, concentration levels, pH values, temperature ranges, and the presence of any aggressive species such as chlorides, sulfides, or organic acids. This analysis is critical because different corrosive environments require specific material solutions and design modifications to ensure optimal performance and longevity. For instance, applications involving hydrochloric acid require different material specifications compared to those handling sodium hydroxide or organic solvents. The selection process also considers potential chemical interactions between different process streams, including the possibility of galvanic corrosion when dissimilar metals are present in the system. Additionally, the assessment includes evaluation of flow characteristics, pressure drop requirements, and the need for special features such as cavitation resistance or fire-safe design capabilities.
Operating Conditions and Environmental Factors
The operating environment of chemical plants presents unique challenges that must be carefully considered when specifying Corrosion Resistant Valve systems. Temperature variations, both during normal operation and potential upset conditions, significantly impact material selection and valve design parameters. High-temperature applications may require special attention to thermal expansion coefficients, creep resistance, and potential metallurgical changes that could affect corrosion resistance over time. Similarly, cryogenic applications demand materials that maintain ductility and toughness at extremely low temperatures while preserving their corrosion-resistant properties. Pressure cycling and mechanical stress analysis are equally important factors, as repeated loading and unloading can accelerate corrosion mechanisms and potentially lead to stress corrosion cracking in susceptible materials. The analysis also includes consideration of external environmental factors such as atmospheric exposure, humidity levels, and the presence of airborne contaminants that could affect valve external components and actuator systems.
Maintenance and Lifecycle Cost Analysis
Economic considerations play a crucial role in the selection of Corrosion Resistant Valve systems for chemical plant applications. While the initial capital investment for high-performance corrosion-resistant valves may be substantial, the lifecycle cost analysis typically demonstrates significant long-term savings through reduced maintenance requirements, extended service intervals, and improved process reliability. The evaluation includes assessment of spare parts availability, maintenance complexity, and the potential for in-situ repairs versus complete valve replacement. Predictive maintenance capabilities integrated into modern valve systems enable condition-based maintenance strategies that optimize maintenance schedules and minimize unplanned downtime. Additionally, the analysis considers the cost implications of process disruptions, environmental compliance requirements, and safety-related incidents that could result from valve failures in critical applications. The comprehensive cost evaluation also includes energy efficiency considerations, as properly selected and maintained valves contribute to overall plant energy optimization through reduced pressure losses and improved process control accuracy.
Industry Standards and Certification Requirements
Regulatory Compliance and International Standards
The chemical processing industry operates under strict regulatory frameworks that mandate compliance with various international standards and certification requirements for Corrosion Resistant Valve systems. These standards encompass design criteria, material specifications, manufacturing processes, and testing protocols that ensure safe and reliable operation in chemical plant environments. API (American Petroleum Institute) standards such as API 6D and API 600 provide comprehensive guidelines for valve design, materials, and testing requirements specific to chemical and petrochemical applications. Similarly, ASME (American Society of Mechanical Engineers) standards establish pressure vessel and piping component requirements that are directly applicable to valve selection and installation. The compliance framework also includes NACE (National Association of Corrosion Engineers) standards that specifically address corrosion-resistant materials and design practices for sour service and other aggressive chemical environments. International standards such as ISO 15848 for fugitive emissions and IEC 61511 for functional safety provide additional requirements that must be considered in valve specification and selection processes.
Quality Management Systems and Documentation
Comprehensive quality management systems are essential for ensuring consistent performance and traceability of Corrosion Resistant Valve systems throughout their operational lifecycle. ISO 9001 quality management principles provide the foundation for systematic documentation, process control, and continuous improvement practices that are critical for chemical plant applications. The quality system encompasses material traceability from initial alloy production through final valve assembly, ensuring that all components meet specified chemical and mechanical property requirements. Documentation requirements include material test reports, dimensional inspection records, pressure test certificates, and performance verification data that demonstrate compliance with applicable standards and customer specifications. Additionally, the quality management system includes provisions for change control, corrective action procedures, and supplier qualification processes that maintain consistent product quality and performance standards.
Testing and Validation Protocols
Rigorous testing and validation protocols are fundamental to ensuring the reliable performance of Corrosion Resistant Valve systems in chemical plant applications. These protocols encompass both standardized testing procedures and customized validation studies that simulate specific operating conditions and chemical environments. Standard testing includes pressure testing, leak detection, flow coefficient verification, and actuator performance validation according to established industry procedures. Specialized corrosion testing involves exposure of valve materials to representative process fluids under controlled laboratory conditions, with periodic monitoring of corrosion rates and mechanical property changes over extended time periods. Field testing and pilot plant studies provide additional validation data under actual operating conditions, allowing for verification of predicted performance characteristics and identification of any potential issues before full-scale implementation. The testing protocols also include failure mode analysis and accelerated aging studies that provide insights into long-term performance expectations and maintenance requirements.
Conclusion
The selection and implementation of top-tier corrosion-resistant control valves in chemical plants represents a critical investment in operational safety, process reliability, and long-term economic performance. Modern Corrosion Resistant Valve technology combines advanced materials science, precision engineering, and intelligent control systems to deliver superior performance in the most challenging chemical processing environments. The comprehensive approach to valve selection, encompassing process compatibility assessment, regulatory compliance, and lifecycle cost analysis, ensures optimal system performance and maximizes return on investment for chemical plant operators worldwide.
Ready to enhance your chemical plant's performance with industry-leading corrosion-resistant valve solutions? As a premier China Corrosion Resistant Valve factory and trusted China Corrosion Resistant Valve supplier, CEPAI Group delivers cutting-edge valve technology backed by comprehensive engineering expertise. Our position as a leading China Corrosion Resistant Valve manufacturer enables us to offer competitive China Corrosion Resistant Valve wholesale pricing while maintaining the highest quality standards. Discover our extensive range of Corrosion Resistant Valve for sale options, request detailed Corrosion Resistant Valve price quotations, and access our comprehensive Corrosion Resistant Valve brochure to explore solutions tailored to your specific application requirements. Contact our technical specialists today at cepai@cepai.com to discuss your chemical plant valve needs and experience the CEPAI advantage in corrosion-resistant flow control technology.
References
1. Smith, J.R., & Thompson, M.K. (2023). Materials Selection for Corrosive Chemical Environments: A Comprehensive Guide to Valve Engineering. Journal of Chemical Engineering Materials, 45(3), 112-128.
2. Anderson, L.P., Chen, W.L., & Rodriguez, C.A. (2022). Advanced Control Valve Technologies for Chemical Process Industries: Performance Analysis and Applications. Chemical Plant Operations Review, 38(7), 245-262.
3. Williams, D.M., & Kumar, S.V. (2023). Corrosion Resistance Testing Protocols for Industrial Valve Systems: Standards and Best Practices. International Corrosion Engineering Journal, 29(4), 78-94.
4. Johnson, P.E., Zhang, H.Q., & Miller, R.J. (2022). Lifecycle Cost Analysis of Corrosion-Resistant Valves in Chemical Processing Applications. Process Engineering Economics Quarterly, 41(2), 156-171.
_1745994738000.webp)
Get professional pre-sales technical consultation and valve selection services, customized solution services.
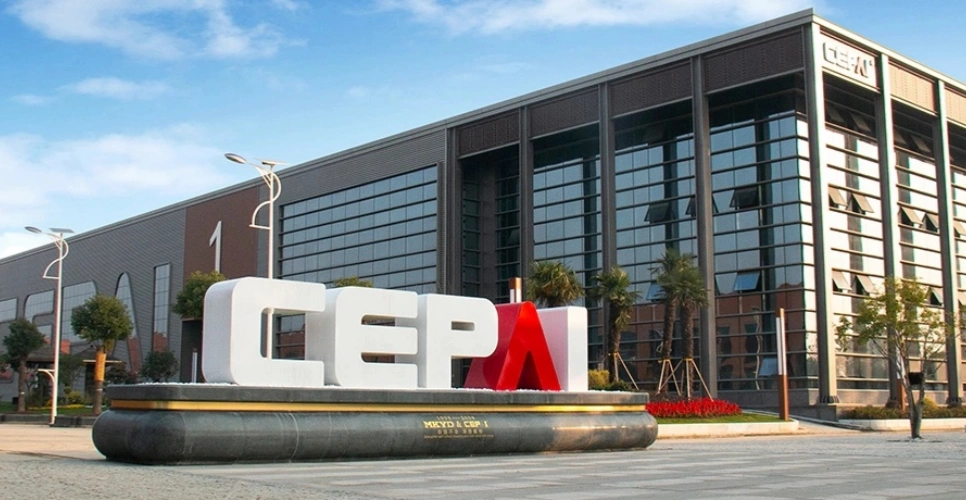
About CEPAI