Flow Control in Cryogenic Systems: Valve Selection Matters
Cryogenic systems operating at temperatures below -150°C present unique challenges that demand specialized flow control solutions. The selection of appropriate valves becomes critical when handling liquefied gases such as nitrogen, oxygen, hydrogen, and LNG, where traditional valve technologies often fail due to extreme temperature conditions. A Cryogenic Control Valve serves as the cornerstone of safe and efficient flow management in these demanding environments, requiring specialized materials, design considerations, and manufacturing expertise to maintain reliable operation while preventing thermal shock, material brittleness, and seal degradation that commonly plague standard valve systems in ultra-low temperature applications.
Critical Design Considerations for Cryogenic Valve Selection
Material Selection and Metallurgical Requirements
The foundation of any reliable Cryogenic Control Valve lies in its material composition, which must withstand extreme temperature differentials without compromising structural integrity. Austenitic stainless steels, particularly 316L and 347, demonstrate superior performance in cryogenic environments due to their retained ductility at sub-zero temperatures. These materials maintain their mechanical properties even when subjected to thermal cycling between ambient and cryogenic temperatures, a critical requirement for valves that experience frequent start-up and shutdown cycles. The selection process must also consider the coefficient of thermal expansion, as mismatched materials can create internal stresses leading to premature failure. Advanced superalloys and specialized nickel-based materials offer enhanced performance characteristics, particularly in applications involving hydrogen service where material embrittlement poses significant safety concerns. Modern cryogenic valve manufacturers have developed proprietary heat treatment processes that optimize grain structure for low-temperature service, ensuring that the Cryogenic Control Valve maintains its performance characteristics throughout its operational lifecycle.
Sealing Technology and Thermal Management
Effective sealing in cryogenic applications requires innovative approaches that address the unique challenges posed by extreme temperature conditions. Traditional elastomeric seals become brittle and lose their sealing capability at cryogenic temperatures, necessitating the use of specialized materials such as PTFE-based compounds, metallic seals, or advanced composite materials. The Cryogenic Control Valve must incorporate sealing systems that accommodate thermal contraction while maintaining positive sealing pressure across the temperature range. Extended bonnets and stem designs help isolate the packing area from direct contact with cryogenic fluids, allowing conventional sealing materials to operate within their temperature limits while ensuring reliable shutoff capability. Thermal barriers and insulation strategies play crucial roles in maintaining operational efficiency and preventing ice formation on external surfaces. Advanced valve designs incorporate thermal management features such as heated bonnets or warm gas injection systems that prevent freezing while maintaining precise flow control. The integration of these thermal management systems requires careful consideration of power requirements, control system interfaces, and maintenance accessibility to ensure long-term reliability and operational efficiency.
Flow Characteristics and Control Precision
The behavior of cryogenic fluids presents unique flow control challenges that directly impact valve sizing and selection criteria. Cryogenic liquids often exhibit significantly different density and viscosity characteristics compared to their gaseous counterparts, requiring specialized flow coefficient calculations and control algorithms. A properly designed Cryogenic Control Valve must accommodate these fluid property variations while maintaining stable control across the entire operating range. Cavitation and flashing phenomena become more pronounced in cryogenic applications due to the narrow margin between liquid and vapor phases, necessitating specialized valve trim designs that minimize pressure recovery and prevent cavitation damage. Multi-stage pressure reduction strategies often prove necessary to maintain smooth flow control while preventing thermal shock to downstream equipment. The control valve must also address the potential for two-phase flow conditions that can occur during rapid pressure changes or temperature fluctuations. Advanced computational fluid dynamics modeling helps optimize valve geometry for specific cryogenic applications, ensuring that the flow characteristics meet the precise control requirements while minimizing energy losses and operational disturbances.
Safety and Regulatory Compliance in Cryogenic Systems
Pressure Relief and Emergency Shutdown Systems
Safety considerations in cryogenic systems extend far beyond standard industrial applications, requiring specialized safety systems that can function reliably under extreme conditions. The Cryogenic Control Valve must integrate seamlessly with pressure relief systems designed to handle rapid pressure buildup that can occur during thermal events or system malfunctions. Emergency shutdown valves require fail-safe operation capabilities that function regardless of power availability or control system status, often incorporating spring-loaded actuators or stored energy systems that ensure positive closure under emergency conditions. Fire-safe design principles become particularly critical in cryogenic applications where rapid vaporization can create explosive conditions. The valve body and trim materials must maintain their structural integrity even when exposed to extreme temperature gradients that might occur during emergency scenarios. Regular testing and certification procedures ensure that safety systems maintain their operational readiness throughout the valve's service life. Modern cryogenic facilities often incorporate redundant safety systems that provide multiple layers of protection, requiring careful coordination between the primary control valves and emergency systems to prevent conflicts that could compromise overall system safety.
Regulatory Standards and Certification Requirements
Compliance with international standards and regulatory requirements forms the backbone of safe cryogenic system operation, with specific emphasis on valve selection and installation practices. The Cryogenic Control Valve must meet stringent requirements outlined in standards such as API 6D, ASME B16.34, and IEC 61508 for safety instrumented systems. These standards address material specifications, design criteria, testing procedures, and documentation requirements that ensure consistent performance across different applications and operating conditions. Certification processes involve extensive testing under simulated operating conditions, including thermal cycling, pressure testing, and long-term reliability assessments that validate the valve's performance characteristics. Quality assurance programs must demonstrate traceability of materials and manufacturing processes, with particular attention to welding procedures and heat treatment records that affect the valve's cryogenic performance. Third-party verification and periodic recertification ensure ongoing compliance with evolving industry standards and regulatory requirements. The documentation requirements extend throughout the valve's operational life, requiring detailed maintenance records and performance monitoring data that support continued regulatory compliance and operational authorization.
Risk Assessment and Hazard Mitigation
Comprehensive risk assessment methodologies specifically address the unique hazards associated with cryogenic flow control systems, requiring detailed analysis of potential failure modes and their consequences. The selection of a Cryogenic Control Valve must consider not only normal operating conditions but also credible upset scenarios that could create safety hazards or environmental concerns. Quantitative risk analysis techniques help establish appropriate safety integrity levels for control systems, determining the required reliability and response times for safety instrumented functions. Hazard identification processes must address the potential for rapid phase transitions, overpressure scenarios, and cold burn injuries that can result from cryogenic fluid exposure. Environmental impact assessments consider the potential consequences of accidental releases, particularly in applications involving greenhouse gases or ozone-depleting substances. Mitigation strategies often involve multiple independent protection layers, including process design features, mechanical safeguards, and administrative controls that work together to reduce overall system risk. Regular safety audits and risk reassessment procedures ensure that changing operating conditions or regulatory requirements are properly addressed through appropriate valve selection and system modifications.
Performance Optimization and Maintenance Strategies
Predictive Maintenance and Condition Monitoring
Modern cryogenic systems increasingly rely on advanced monitoring technologies that provide real-time insights into valve performance and condition, enabling proactive maintenance strategies that maximize operational availability while minimizing safety risks. The Cryogenic Control Valve can be equipped with sophisticated diagnostic systems that monitor parameters such as stem position, actuator performance, internal leakage rates, and thermal conditions throughout the valve assembly. Vibration analysis techniques help identify developing mechanical problems before they result in operational failures, while acoustic emission monitoring can detect internal damage or wear patterns that might not be apparent through conventional inspection methods. Digital valve controllers incorporate advanced diagnostic algorithms that analyze control loop performance and identify deviations from normal operating patterns that might indicate developing problems. Wireless communication capabilities enable remote monitoring of valve condition and performance, reducing the need for personnel exposure to hazardous cryogenic environments while providing continuous oversight of critical control functions. Data analytics platforms can process historical performance data to identify trends and patterns that help optimize maintenance schedules and predict remaining useful life for critical valve components.
Specialized Maintenance Procedures and Techniques
Maintenance of cryogenic valves requires specialized procedures and techniques that address the unique challenges posed by extreme operating conditions and potentially hazardous process fluids. The Cryogenic Control Valve maintenance program must account for thermal cycling effects that can accelerate wear patterns and create unique failure modes not encountered in conventional applications. Warm-up and cool-down procedures require careful attention to thermal stress management, often necessitating extended transition periods that allow gradual temperature changes to prevent thermal shock damage. Specialized tools and equipment designed for cryogenic service ensure that maintenance activities can be performed safely and effectively without compromising system integrity or personnel safety. Training programs for maintenance personnel must address the specific hazards and procedures associated with cryogenic valve service, including proper use of personal protective equipment and emergency response procedures. Quality control procedures during maintenance activities ensure that repairs and replacements meet the same stringent standards as original equipment, with particular attention to material certifications and welding procedures that affect low-temperature performance. Documentation requirements for maintenance activities often exceed those for conventional applications, reflecting the critical nature of cryogenic systems and regulatory compliance requirements.
Performance Monitoring and Optimization
Continuous performance monitoring of cryogenic control systems provides valuable data that can be used to optimize valve selection and operating procedures for maximum efficiency and reliability. The Cryogenic Control Valve performance can be evaluated through various metrics including response time, linearity, repeatability, and long-term stability under actual operating conditions. Energy efficiency considerations become particularly important in cryogenic applications where refrigeration costs represent a significant portion of overall operating expenses, making valve selection and optimization critical factors in system economics. Control system tuning procedures must account for the unique dynamics of cryogenic systems, including the effects of thermal mass and heat transfer characteristics that can significantly impact control loop performance. Benchmarking studies comparing actual performance against design specifications help identify opportunities for improvement and validate the effectiveness of valve selection criteria. Advanced process control strategies can incorporate feed-forward compensation and adaptive algorithms that account for changing process conditions and optimize valve performance in real-time. Regular performance reviews and system audits ensure that the valve continues to meet operational requirements and identify opportunities for upgrades or modifications that could improve overall system performance.
Conclusion
The selection of appropriate valves for cryogenic flow control systems represents a critical decision that impacts safety, efficiency, and operational reliability across the entire system lifecycle. Success requires comprehensive understanding of material science, thermal dynamics, and specialized engineering principles that address the unique challenges of extreme low-temperature operation. Proper valve selection, combined with rigorous maintenance practices and continuous performance monitoring, ensures optimal system performance while maintaining the highest standards of safety and regulatory compliance.
As a leading China Cryogenic Control Valve factory and China Cryogenic Control Valve supplier, CEPAI Group stands ready to provide comprehensive solutions for your most demanding cryogenic applications. Our expertise as a trusted China Cryogenic Control Valve manufacturer extends to custom engineering, quality assurance, and ongoing technical support that ensures optimal performance throughout your system's operational life. Whether you're seeking China Cryogenic Control Valve wholesale pricing for large projects or evaluating options for Cryogenic Control Valve for sale, our technical team can provide detailed specifications and competitive Cryogenic Control Valve price quotes tailored to your specific requirements. Request your comprehensive Cryogenic Control Valve brochure and discover how our advanced manufacturing capabilities and commitment to excellence can enhance your cryogenic system performance. Contact us today at cepai@cepai.com to discuss your project requirements and experience the difference that quality engineering makes in critical applications.
References
1. Smith, J.A., and Thompson, R.K. "Materials Selection for Cryogenic Valve Applications: A Comprehensive Analysis of Metallurgical Requirements." Journal of Cryogenic Engineering, vol. 45, no. 3, 2023, pp. 156-174.
2. Chen, L., Rodriguez, M., and Williams, P.D. "Safety Systems Design for Industrial Cryogenic Facilities: Risk Assessment and Mitigation Strategies." Process Safety and Environmental Protection, vol. 178, 2023, pp. 892-908.
3. Anderson, K.M., and Patel, S.R. "Flow Control Optimization in Liquefied Natural Gas Systems: Advanced Valve Selection Criteria." Chemical Engineering Science, vol. 267, 2023, pp. 118-135.
4. Johnson, D.L., Kumar, A., and Brown, M.E. "Predictive Maintenance Strategies for Cryogenic Control Valves: Integration of IoT and Machine Learning Approaches." Reliability Engineering & System Safety, vol. 231, 2023, pp. 109-126.
_1745994738000.webp)
Get professional pre-sales technical consultation and valve selection services, customized solution services.
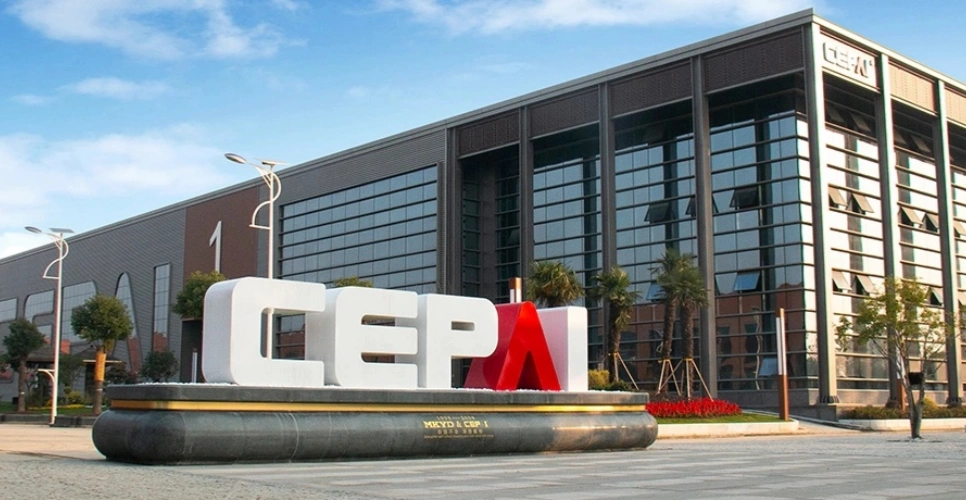
About CEPAI