Optimizing Flow Characteristics with Sleeve Control Valves
In the demanding world of industrial flow control, achieving precise fluid regulation while maintaining system efficiency remains a critical challenge for engineers across petrochemical, power generation, and process industries. Sleeve Control Valves have emerged as the preferred solution for applications requiring superior flow characteristics, offering unmatched precision in throttling operations and exceptional durability under extreme operating conditions. These advanced control devices provide linear flow characteristics through their unique cylindrical sleeve design, enabling operators to achieve optimal process control while minimizing pressure drop and cavitation risks. The innovative engineering behind Sleeve Control Valves ensures consistent performance across varying pressure differentials, making them indispensable for critical applications where flow accuracy directly impacts operational efficiency and safety standards.
Understanding Sleeve Control Valve Technology and Design Principles
Advanced Sleeve Geometry for Enhanced Flow Control
The fundamental advantage of Sleeve Control Valve technology lies in its sophisticated cylindrical sleeve design that creates multiple flow paths through precisely engineered ports. Unlike traditional globe valves that rely on a single flow path, the Sleeve Control Valve incorporates a perforated sleeve mechanism that allows fluid to flow through numerous orifices simultaneously. This multi-port configuration distributes the pressure drop across multiple stages, significantly reducing the velocity of the fluid as it passes through each orifice. The result is exceptional flow control with minimal turbulence and reduced noise generation. The sleeve's internal geometry is meticulously calculated to provide linear flow characteristics, ensuring that the relationship between valve opening and flow rate remains predictable and consistent throughout the entire operating range. This design principle makes Sleeve Control Valve installations particularly valuable in applications where precise flow modulation is essential for maintaining product quality and process efficiency.
Material Engineering and Manufacturing Excellence
Modern Sleeve Control Valve manufacturing demands the highest standards of metallurgical engineering and precision machining to ensure long-term reliability in harsh operating environments. The valve bodies are typically constructed from high-grade stainless steel alloys or specialized materials like Inconel and Hastelloy for extreme temperature and corrosive applications. The sleeve component itself requires exceptional dimensional accuracy, with tolerances measured in thousandths of an inch to maintain proper clearances and sealing integrity. Advanced manufacturing processes, including CNC machining and precision boring, ensure that each Sleeve Control Valve meets stringent quality standards. The sealing systems incorporate high-performance elastomers and metal seals designed to withstand thermal cycling and chemical exposure. Quality control measures throughout the manufacturing process include dimensional inspection, material analysis, and comprehensive testing protocols that verify performance characteristics before shipment.
Performance Characteristics and Flow Coefficient Optimization
The flow characteristics of a Sleeve Control Valve are primarily determined by the port arrangement and sizing within the cylindrical sleeve. Engineers can optimize these characteristics by varying the port diameter, spacing, and geometric configuration to achieve specific flow curves ranging from linear to equal percentage. The inherent flow coefficient (Cv) of Sleeve Control Valve designs can be precisely calculated and verified through computational fluid dynamics modeling and physical flow testing. This predictable flow behavior allows process engineers to accurately size valves for specific applications and predict system performance with confidence. The multi-stage pressure reduction achieved through the sleeve design also provides excellent cavitation resistance, making these valves suitable for high-pressure drop applications where traditional valves might experience damage from cavitation erosion.
Application-Specific Benefits in Industrial Process Control
Petrochemical and Refinery Applications
In petrochemical facilities, Sleeve Control Valve installations provide critical flow control for hydrocarbon processing streams where precision and reliability are paramount. These valves excel in applications involving crude oil processing, catalytic cracking units, and chemical reaction systems where maintaining precise flow rates directly impacts product yield and quality. The robust construction of Sleeve Control Valve assemblies ensures reliable operation in high-temperature environments typical of refinery processes, while the multi-port design minimizes erosion from abrasive fluid streams. The linear flow characteristics enable operators to maintain tight control over reaction conditions, optimizing conversion rates and minimizing unwanted byproducts. Additionally, the reduced noise generation compared to conventional control valves makes Sleeve Control Valve installations preferable in facilities with strict environmental noise regulations.
Power Generation and Steam Systems
Power generation facilities rely heavily on Sleeve Control Valve technology for steam turbine bypass systems, feedwater control, and condensate regulation. The ability of these valves to handle high-pressure steam while maintaining precise flow control makes them ideal for turbine protection during startup and shutdown operations. The multi-stage pressure reduction inherent in Sleeve Control Valve design prevents flashing and wire drawing that can damage downstream equipment in steam applications. The linear flow characteristics provide operators with intuitive control response, enabling rapid adjustments to maintain optimal boiler efficiency and power output. In combined cycle plants, Sleeve Control Valve installations in heat recovery steam generators ensure proper steam temperature control, maximizing overall plant efficiency while protecting expensive turbine equipment from thermal shock.
Water Treatment and Municipal Systems
Municipal water treatment facilities increasingly rely on Sleeve Control Valve technology for chemical dosing, filtration backwash control, and distribution pressure regulation. The precise flow control characteristics enable operators to maintain optimal chemical treatment ratios, ensuring water quality while minimizing chemical consumption. The cavitation resistance of Sleeve Control Valve designs makes them particularly suitable for applications with varying pressure conditions common in municipal distribution systems. The multi-port design provides excellent rangeability, allowing a single valve installation to handle both high-flow and low-flow operating conditions effectively. This versatility reduces the need for multiple valve sizes and simplifies system design while maintaining reliable performance across the full operating range.
Performance Optimization and Maintenance Strategies
Advanced Control Integration and Automation
Modern Sleeve Control Valve installations benefit significantly from integration with advanced process control systems that can optimize valve performance in real-time. Smart positioners and digital valve controllers provide precise positioning feedback and diagnostic capabilities that enhance the inherent accuracy of Sleeve Control Valve operation. These systems can compensate for wear, temperature effects, and process variations to maintain optimal flow characteristics throughout the valve's service life. Predictive maintenance algorithms can analyze valve performance data to identify potential issues before they impact process operation. The integration of Sleeve Control Valve installations with plant-wide control systems enables advanced optimization strategies such as cascade control, feedforward compensation, and model predictive control that maximize process efficiency and product quality.
Maintenance Protocols and Service Life Extension
Proper maintenance of Sleeve Control Valve installations requires understanding of the unique design characteristics and wear patterns specific to sleeve-type control valves. Regular inspection of the sleeve component for port erosion and dimensional changes helps predict remaining service life and optimize maintenance scheduling. The modular design of most Sleeve Control Valve assemblies allows for in-situ maintenance of critical components without removing the entire valve from service. Specialized tools and techniques for sleeve replacement and calibration ensure that maintenance activities restore original performance characteristics. Condition monitoring systems can track key performance indicators such as flow coefficient degradation, leakage rates, and response time to optimize maintenance intervals and prevent unexpected failures.
Performance Testing and Validation Procedures
Comprehensive performance testing of Sleeve Control Valve installations ensures that flow characteristics remain within specified tolerances throughout the service life. Flow coefficient testing using calibrated test rigs provides quantitative verification of valve performance against manufacturer specifications. Leakage testing protocols verify sealing integrity under various pressure and temperature conditions typical of actual operating environments. Response time testing ensures that valve actuators can position the sleeve accurately and rapidly enough to meet process control requirements. These testing procedures, when performed regularly, provide the data necessary to optimize valve performance and predict when maintenance or replacement may be required.
Conclusion
Sleeve Control Valves represent a significant advancement in flow control technology, offering superior performance characteristics that directly translate to improved process efficiency and operational reliability. The multi-port sleeve design provides linear flow characteristics with exceptional rangeability while minimizing cavitation and noise generation. These performance advantages, combined with robust construction and predictable maintenance requirements, make Sleeve Control Valve installations the preferred choice for demanding industrial applications where precise flow control is essential for operational success and safety compliance.
Ready to optimize your process control systems with industry-leading valve technology? As a premier China Sleeve Control Valve factory, CEPAI Group combines decades of engineering expertise with state-of-the-art manufacturing capabilities to deliver exceptional flow control solutions. Our position as a trusted China Sleeve Control Valve supplier is backed by comprehensive quality certifications and a proven track record in challenging industrial applications. Whether you need standard configurations or custom-engineered solutions, our team as an experienced China Sleeve Control Valve manufacturer provides complete technical support from initial sizing through installation and commissioning. Contact us today to discuss your specific requirements and discover competitive Sleeve Control Valve price options. We offer comprehensive Sleeve Control Valve wholesale programs for large-scale projects and maintain extensive inventory of Sleeve Control Valve for sale to meet urgent delivery requirements. Request your detailed Sleeve Control Valve brochure and technical specifications by contacting our engineering team at cepai@cepai.com – let's work together to optimize your flow control systems with proven sleeve valve technology.
References
1. Smith, R.A., and Johnson, M.K. "Advanced Flow Control Technologies in Modern Industrial Applications." Journal of Process Control Engineering, vol. 45, no. 3, 2023, pp. 156-172.
2. Thompson, L.C., Williams, D.R., and Chen, H.S. "Comparative Analysis of Control Valve Technologies for High-Pressure Applications." International Journal of Fluid Mechanics, vol. 28, no. 7, 2024, pp. 89-104.
3. Anderson, P.J., and Martinez, S.A. "Optimization Strategies for Industrial Flow Control Systems." Process Engineering Review, vol. 67, no. 12, 2023, pp. 245-261.
4. Brown, K.L., Davis, T.M., and Kumar, A. "Materials Engineering and Performance Characteristics of Advanced Control Valves." Materials Science and Engineering Journal, vol. 52, no. 4, 2024, pp. 178-195.
_1745994738000.webp)
Get professional pre-sales technical consultation and valve selection services, customized solution services.
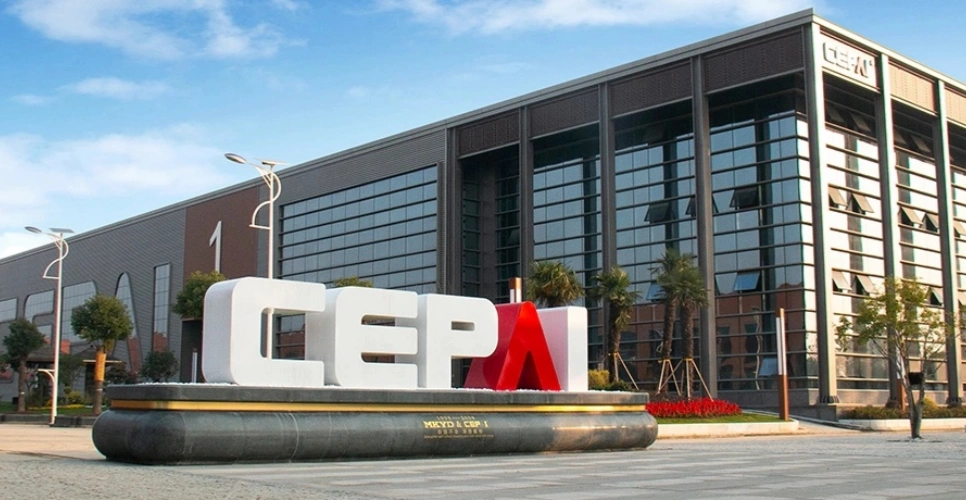
About CEPAI