Selecting High-Pressure Control Valves for Oil & Gas
Selecting the right High Pressure Control Valve for oil and gas operations is a critical decision that directly impacts operational efficiency, safety, and long-term profitability. In the demanding environment of upstream and downstream petroleum processing, these specialized valves must withstand extreme pressures, corrosive fluids, and temperature fluctuations while maintaining precise flow control. The selection process involves careful evaluation of pressure ratings, material compatibility, actuator types, and compliance with industry standards such as API 6A and API 6D. Understanding the specific requirements of your application, from wellhead operations to pipeline distribution, ensures optimal performance and minimizes costly downtime in mission-critical petroleum infrastructure.
Key Technical Specifications for High-Pressure Control Valves
Pressure Rating and Temperature Classifications
When selecting a High Pressure Control Valve for oil and gas applications, pressure rating stands as the most fundamental specification. These valves typically operate within pressure ranges from 2,000 PSI to 20,000 PSI, with some specialized units handling pressures exceeding 30,000 PSI in deepwater drilling operations. The ANSI/API pressure class system provides standardized ratings including Class 600, 900, 1500, 2500, and 5000, each corresponding to specific pressure and temperature combinations. Temperature considerations are equally critical, as these valves must function reliably in environments ranging from arctic conditions at -50°F to high-temperature applications reaching 1000°F in thermal recovery operations. The relationship between pressure and temperature creates derating factors that must be carefully calculated to ensure safe operation throughout the valve's service life.
Material Selection and Corrosion Resistance
Material selection for High Pressure Control Valve applications requires comprehensive understanding of the process fluids and environmental conditions. Carbon steel grades such as ASTM A105 and A350 LF2 provide cost-effective solutions for standard hydrocarbon service, while stainless steel grades including 316SS, 321SS, and super duplex 2507 offer enhanced corrosion resistance for sour gas environments containing H2S and CO2. Exotic alloys like Inconel 625 and Hastelloy C-276 become necessary for extreme corrosion conditions or high-temperature applications. The trim materials, including seats, plugs, and internal components, often utilize harder materials such as Stellite overlays or tungsten carbide to resist erosion from high-velocity fluids containing sand or other abrasive particles. Proper material selection ensures valve longevity and prevents catastrophic failures that could result in environmental incidents or production shutdowns.
Flow Characteristics and Sizing Calculations
The flow characteristics of a High Pressure Control Valve determine its ability to provide precise control across the full range of operating conditions. Linear flow characteristics provide equal percentage changes in flow for equal changes in valve position, making them ideal for applications requiring consistent control sensitivity. Equal percentage characteristics offer improved control at low flows, which proves beneficial in applications with wide turndown ratios. Modified parabolic characteristics combine advantages of both linear and equal percentage curves. Proper sizing calculations must account for factors including pressure drop, flow coefficient (Cv), Reynolds number effects, and choked flow conditions. The installed flow characteristic often differs significantly from the inherent characteristic due to system pressure drops, making careful system analysis essential for optimal control performance.
Critical Performance Factors in Oil & Gas Environments
Sealing Technologies and Fugitive Emissions Control
Sealing performance in High Pressure Control Valve applications demands advanced technologies to prevent fugitive emissions and ensure environmental compliance. Primary sealing systems typically employ spring-loaded PTFE packing arrangements with backup rings to maintain seal integrity under varying pressure conditions. Live-loaded packing systems automatically compensate for thermal cycling and packing settlement, reducing maintenance requirements and extending seal life. Secondary sealing systems may include bellows seals for zero-emission applications or lantern ring configurations for injection of barrier fluids. Graphite packing systems provide superior performance at elevated temperatures, while specialized compounds like Kalrez offer chemical compatibility with aggressive process fluids. The implementation of Low Emission (LE) and Fugitive Emission Standards (ISO 15848) drives the adoption of advanced sealing technologies that minimize environmental impact while maintaining operational reliability.
Actuator Selection and Safety Systems
Actuator selection for High Pressure Control Valve installations requires careful consideration of torque requirements, response speed, and fail-safe positioning. Pneumatic actuators offer rapid response and inherent fail-safe capabilities through spring return mechanisms, making them ideal for emergency shutdown applications. Electric actuators provide precise positioning and eliminate the need for instrument air systems, while hydraulic actuators deliver high torque output for large valve applications. Smart actuator systems incorporate digital communication protocols like HART, Foundation Fieldbus, or PROFIBUS, enabling advanced diagnostics and predictive maintenance capabilities. Safety instrumented systems (SIS) integration requires actuators certified for SIL 2 or SIL 3 applications, with proven failure rates and diagnostic capabilities. Partial stroke testing capabilities allow verification of actuator and valve performance without process shutdown, enhancing safety system reliability.
Cavitation and Erosion Prevention
Cavitation and erosion phenomena pose significant challenges for High Pressure Control Valve performance in high-energy applications. Cavitation occurs when local pressure drops below vapor pressure, creating vapor bubbles that subsequently collapse and generate destructive forces. Multi-stage pressure reduction through cascaded orifices or tortuous path designs can effectively prevent cavitation by maintaining pressure above critical levels throughout the valve. Erosion from high-velocity fluids carrying solid particles requires specialized trim designs with optimized flow paths and hardened surfaces. Cage-guided designs provide superior guiding and reduced side loads compared to globe-style configurations. Anti-cavitation trims utilizing staged pressure reduction or flow conditioning elements can extend valve life significantly in challenging applications. Material selection for erosion resistance often involves overlay welding with stellite or application of tungsten carbide coatings to critical flow areas.
Industry Standards and Compliance Requirements
API Standards and Certification Requirements
Compliance with American Petroleum Institute (API) standards forms the foundation for High Pressure Control Valve applications in oil and gas service. API Specification 6A covers wellhead and christmas tree equipment, establishing requirements for pressure ratings, material specifications, testing procedures, and marking requirements. API Specification 6D addresses pipeline valves, including design, materials, testing, and inspection requirements for ball, gate, plug, and check valves. API Specification 602 specifically covers compact steel gate valves used in petroleum refining and related industries. These standards mandate specific design factors, typically 2:1 for wellhead equipment, ensuring adequate safety margins under maximum operating conditions. Third-party certification through organizations like API, NACE, or other recognized testing laboratories provides verification of compliance and quality assurance for end users.
Environmental and Safety Regulations
Environmental regulations increasingly influence High Pressure Control Valve selection and operation in oil and gas facilities. EPA methane emission regulations require implementation of leak detection and repair (LDAR) programs, driving adoption of low-emission valve technologies. OSHA process safety management (PSM) standards mandate comprehensive mechanical integrity programs including regular valve inspection, testing, and maintenance procedures. International standards such as ISO 14001 environmental management systems and ISO 45001 occupational health and safety requirements establish frameworks for continuous improvement in environmental performance. European ATEX directives for explosive atmosphere equipment require specialized certifications for valves installed in hazardous locations. Canadian Environmental Protection Act (CEPA) and similar international regulations establish emission limits and reporting requirements that influence valve technology selection.
Quality Assurance and Testing Protocols
Comprehensive quality assurance programs ensure High Pressure Control Valve reliability throughout their service life. Manufacturing quality systems must comply with ISO 9001 requirements, establishing documented procedures for design control, material traceability, and process validation. Hydrostatic testing at 1.5 times design pressure verifies structural integrity, while seat leakage testing confirms sealing performance to API 598 or ISO 5208 standards. Material testing includes chemical analysis, mechanical properties verification, and non-destructive examination using ultrasonic, magnetic particle, or liquid penetrant methods. Dimensional inspection ensures compliance with design tolerances, while surface finish measurements verify sealing surface quality. Final inspection and testing documentation provides complete traceability from raw materials through finished product, supporting quality assurance and warranty programs.
Conclusion
The selection of appropriate high-pressure control valves for oil and gas applications requires comprehensive evaluation of technical specifications, performance requirements, and regulatory compliance. Success depends on understanding the complex interplay between pressure ratings, material compatibility, flow characteristics, and environmental factors. Proper specification and installation of these critical components ensures operational safety, environmental compliance, and long-term reliability in demanding petroleum service applications.
Ready to optimize your oil and gas operations with premium high-pressure control valves? As a leading China High Pressure Control Valve factory, CEPAI Group delivers world-class engineering solutions backed by cutting-edge intelligent manufacturing capabilities. Our position as a trusted China High Pressure Control Valve supplier is strengthened by comprehensive API certifications, ISO quality systems, and proven performance in the most demanding applications worldwide. Whether you're seeking a reliable China High Pressure Control Valve manufacturer for custom solutions or exploring China High Pressure Control Valve wholesale opportunities for large-scale projects, our technical expertise and manufacturing excellence ensure optimal performance.
Discover competitive High Pressure Control Valve price options without compromising quality or reliability. Our High Pressure Control Valve for sale inventory includes sleeve-type regulating valves, throttle valves, emergency shut-off valves, and specialized configurations for every application. Request your detailed High Pressure Control Valve brochure today to explore our complete product range, technical specifications, and case studies demonstrating superior performance in global oil and gas operations.
Contact our technical experts today: cepai@cepai.com
References
1. Smith, J.R., Anderson, M.K., and Williams, P.D. (2023). "Advanced Materials for High-Pressure Valve Applications in Upstream Oil and Gas Operations." Journal of Petroleum Technology, 75(8), 45-52.
2. Thompson, L.E., Rodriguez, C.A., and Chen, H. (2022). "Control Valve Sizing and Selection Methodologies for High-Pressure Gas Processing Facilities." Chemical Engineering Progress, 118(12), 28-35.
3. Johnson, R.M., Kumar, S., and Davies, A.J. (2024). "Fugitive Emissions Control in High-Pressure Petroleum Service: Latest Developments in Sealing Technologies." Hydrocarbon Processing, 103(3), 67-74.
4. Brown, K.L., Martinez, F.G., and Taylor, N.S. (2023). "API 6A Compliance and Performance Testing of Wellhead Control Valves under Extreme Operating Conditions." SPE Production & Operations, 38(4), 589-598.
_1745994738000.webp)
Get professional pre-sales technical consultation and valve selection services, customized solution services.
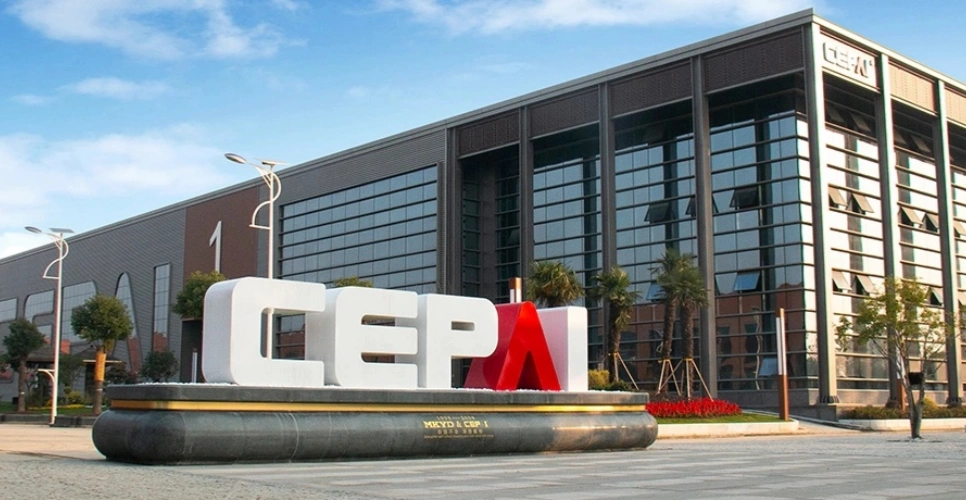
About CEPAI