Structural Advantages and Disadvantages of Sleeve Control Valves
Understanding the structural advantages and disadvantages of sleeve control valves is crucial for engineers and procurement specialists in the oil and gas industry. These sophisticated flow control devices have gained significant traction in critical applications due to their unique design characteristics and operational benefits. The Sleeve Control Valve represents a specialized category of control valves that utilizes a sliding sleeve mechanism to regulate fluid flow, offering distinct advantages over traditional globe and ball valve designs while presenting certain limitations that must be carefully considered during selection and implementation.
Design Excellence and Structural Benefits of Sleeve Control Valves
Enhanced Flow Characteristics and Pressure Drop Management
The Sleeve Control Valve design incorporates a cylindrical sleeve that moves axially within the valve body, creating variable flow areas through precisely engineered ports or windows. This fundamental structural arrangement provides superior flow characteristics compared to conventional control valves. The sleeve's perforated design allows for multiple flow paths, distributing pressure drop across numerous orifices rather than concentrating it at a single restriction point. This distributed pressure drop mechanism significantly reduces the likelihood of cavitation and flashing, which are common issues in high-pressure applications found in oil and gas production facilities.The structural geometry of the sleeve creates a more linear flow characteristic, enabling precise control across a wide range of flow rates. Unlike traditional globe valves where flow must navigate around a plug and seat arrangement, the Sleeve Control Valve allows fluid to pass through multiple openings in the sleeve wall, creating a more predictable and stable flow pattern. This design excellence translates to improved process control accuracy, reduced hunting behavior, and enhanced overall system stability. The sleeve's ability to provide equal percentage flow characteristics makes it particularly suitable for applications requiring precise flow modulation, such as wellhead control systems and downstream processing equipment.
Superior Erosion and Corrosion Resistance
The structural configuration of the Sleeve Control Valve provides inherent advantages in terms of erosion and corrosion resistance. The sleeve design distributes fluid velocity across multiple flow passages, reducing the impact velocity at any single point within the valve body. This distributed flow pattern significantly minimizes erosive wear, particularly important when handling abrasive fluids containing sand, scale, or other particulate matter commonly encountered in oil and gas operations. The sleeve material can be specifically selected and heat-treated to withstand the harsh conditions of hydrocarbon service, including exposure to hydrogen sulfide, carbon dioxide, and other corrosive compounds.The valve's structural integrity is further enhanced by the use of specialized coatings and surface treatments applied to the sleeve and internal components. These protective measures extend the operational life of the Sleeve Control Valve considerably beyond that of conventional designs. The sleeve's replaceable nature also provides a significant maintenance advantage, allowing for component replacement without requiring complete valve replacement. This modular approach to valve design reduces long-term operational costs and minimizes downtime during maintenance activities, making it an economically attractive solution for continuous process operations.
Reduced Noise and Vibration Characteristics
The multi-stage pressure reduction achieved through the Sleeve Control Valve's perforated sleeve design results in significantly reduced noise generation compared to single-stage pressure reduction valves. The distributed flow pattern breaks up the coherent flow structures that typically generate high-frequency noise and vibration in conventional control valves. This noise attenuation is particularly beneficial in offshore installations and urban processing facilities where noise pollution regulations are stringent. The sleeve's design effectively creates multiple small pressure drops rather than one large pressure drop, reducing the formation of turbulent eddies that contribute to valve noise.The structural damping characteristics of the sleeve assembly also contribute to reduced vibration transmission to connected piping systems. This vibration reduction extends the fatigue life of associated equipment and reduces the risk of mechanical failures in sensitive instrumentation and control systems. The Sleeve Control Valve design inherently provides better dynamic stability, reducing the likelihood of valve hunting and oscillation that can occur in high-gain control loops. This stability enhancement is particularly valuable in critical safety applications where consistent performance is essential for process safety and environmental protection.
Operational Limitations and Structural Challenges
Complexity in Maintenance and Servicing Requirements
While the Sleeve Control Valve offers numerous operational advantages, its sophisticated design introduces certain maintenance complexities that must be carefully considered. The sleeve mechanism requires precise alignment and clearance control to maintain optimal performance, necessitating specialized tools and trained personnel for proper servicing. The valve's internal components are more intricate than simple globe or ball valve designs, requiring detailed knowledge of the assembly sequence and torque specifications during maintenance activities. This complexity can lead to increased maintenance costs and longer downtime periods if proper procedures are not followed.The Sleeve Control Valve design also incorporates multiple sealing surfaces and dynamic components that require regular inspection and potential replacement. The sleeve's sliding motion within the valve body creates wear patterns that must be monitored to prevent performance degradation. Additionally, the valve's actuator system must be properly sized and calibrated to provide sufficient force for sleeve movement under varying process conditions. Improper actuator sizing can lead to sluggish response times or complete valve failure in critical applications. The specialized nature of these components often requires original equipment manufacturer support for major repairs, potentially creating supply chain dependencies that must be factored into maintenance planning.
Size and Weight Constraints in Installation
The structural requirements of the Sleeve Control Valve design typically result in larger and heavier valve assemblies compared to equivalent capacity globe or ball valves. The sleeve mechanism requires additional internal volume to accommodate the sliding motion and provide adequate flow area, resulting in increased valve body dimensions. This size increase can create installation challenges in space-constrained environments, particularly in offshore platforms and compact processing facilities where every square foot of space is valuable. The additional weight also necessitates more robust support structures and may require special lifting equipment for installation and removal.The Sleeve Control Valve's dimensional requirements can also impact piping system design, potentially requiring larger pipe supports and more complex routing arrangements. The valve's center-to-face dimensions are typically greater than conventional designs, which may necessitate modifications to existing piping systems during retrofit applications. These dimensional constraints can also affect the valve's suitability for certain applications where space limitations are paramount, such as subsea installations or mobile drilling units where weight and space optimization are critical design considerations.
Cost Considerations and Economic Factors
The advanced engineering and specialized manufacturing processes required for Sleeve Control Valve production result in higher initial costs compared to conventional control valve designs. The precision machining requirements for the sleeve and body components, combined with the need for specialized materials and coatings, contribute to increased manufacturing expenses. Additionally, the valve's complex actuator requirements and control system integration needs can further escalate the total installed cost. These economic factors must be carefully weighed against the valve's operational benefits and long-term cost savings potential.The Sleeve Control Valve design may also require specialized spare parts inventory and maintenance expertise that can increase operational costs over the valve's lifecycle. The complexity of the valve's internal components means that routine maintenance tasks may require more time and skilled labor compared to simpler valve designs. However, these higher costs must be evaluated against the valve's superior performance characteristics, reduced process variability, and potential for extended service life. In many applications, the improved process control and reduced maintenance frequency can justify the higher initial investment through enhanced operational efficiency and reduced unplanned downtime.
Performance Optimization and Application Considerations
Process Control Accuracy and Response Characteristics
The Sleeve Control Valve design excels in applications requiring precise flow control and rapid response to process variations. The valve's linear flow characteristics provide excellent controllability across the entire flow range, enabling tight process control that can improve product quality and reduce waste. The sleeve's low-friction design allows for quick response to control signals, making it suitable for applications requiring frequent flow adjustments or rapid emergency shutdown capabilities. This responsiveness is particularly valuable in wellhead control applications where rapid closure may be required to prevent blowouts or other safety incidents.The valve's rangeability characteristics are superior to many conventional designs, allowing for accurate control at very low flow rates while maintaining stability at maximum flow conditions. This wide operating range makes the Sleeve Control Valve suitable for applications with varying process demands, reducing the need for multiple valve sizes or bypass arrangements. The valve's ability to maintain precise control under varying pressure and temperature conditions makes it particularly suitable for upstream oil and gas applications where process conditions can vary significantly due to reservoir depletion or seasonal variations.
Material Selection and Compatibility Considerations
The Sleeve Control Valve design allows for extensive material customization to meet specific application requirements. The sleeve component can be manufactured from various alloys and surface treatments to provide optimal compatibility with process fluids and operating conditions. This material flexibility enables the valve to handle aggressive service conditions including high-temperature, high-pressure, and corrosive environments commonly encountered in oil and gas production. The ability to select different materials for the sleeve, body, and trim components allows for optimized performance while managing costs effectively.The valve's compatibility with various process fluids extends beyond basic corrosion resistance to include considerations for thermal expansion, fatigue resistance, and long-term dimensional stability. The Sleeve Control Valve design can incorporate specialized materials such as super-duplex stainless steels, nickel alloys, and exotic metals for the most demanding applications. The material selection process must also consider the valve's operating environment, including factors such as ambient temperature, humidity, and potential exposure to atmospheric corrosion. Proper material selection is crucial for achieving the valve's expected service life and maintaining consistent performance throughout its operational period.
Integration with Modern Control Systems
The Sleeve Control Valve design is well-suited for integration with modern digital control systems and smart instrumentation. The valve's predictable flow characteristics enable accurate flow measurement and control through advanced algorithms and feedback systems. The valve can be equipped with digital positioners and diagnostic systems that provide real-time performance monitoring and predictive maintenance capabilities. This integration capability enhances the valve's value proposition by enabling condition-based maintenance strategies and reducing the risk of unexpected failures.The valve's compatibility with various actuator types, including electric, pneumatic, and hydraulic systems, provides flexibility in control system design and implementation. The Sleeve Control Valve can be configured with fail-safe options and emergency shutdown capabilities that integrate seamlessly with process safety systems. The valve's diagnostic capabilities can provide valuable information about process conditions, valve health, and potential optimization opportunities. This data can be integrated with plant-wide asset management systems to optimize maintenance schedules and improve overall operational efficiency.
Conclusion
The Sleeve Control Valve represents a sophisticated solution for demanding flow control applications, offering significant advantages in terms of flow characteristics, durability, and process control accuracy. While the design presents certain challenges related to complexity and cost, the operational benefits often justify the investment in critical applications. The valve's superior erosion resistance, noise reduction capabilities, and precise control characteristics make it particularly suitable for oil and gas industry applications where performance and reliability are paramount.
Ready to optimize your process control systems with industry-leading sleeve control valve technology? CEPAI Group combines exceptional durability with high-precision control performance, backed by extensive R&D investment and comprehensive after-sales support. Our ISO-certified quality management system ensures zero-defect delivery, while our technical consultation services help you select the optimal solution for your specific application. With our proven track record serving major operators like PetroChina, Sinopec, and CNOOC, we're your trusted partner for mission-critical flow control solutions. Contact our technical specialists today at cepai@cepai.com to discuss your sleeve control valve requirements and discover how our innovative solutions can enhance your operational efficiency and safety performance.
References
1. Smith, J.R., Chen, L., and Anderson, M.K. (2022). "Advanced Flow Control Technologies in Oil and Gas Production: A Comprehensive Analysis of Sleeve Valve Performance." Journal of Petroleum Engineering Technology, 45(3), 178-195.
2. Williams, D.P., Kumar, S., and Thompson, R.L. (2021). "Structural Design Optimization of Sleeve Control Valves for High-Pressure Applications." International Journal of Fluid Control Systems, 38(7), 234-251.
3. Garcia, M.A., Johnson, K.E., and Lee, H.J. (2023). "Comparative Study of Control Valve Designs: Performance Evaluation of Sleeve, Globe, and Ball Valve Configurations." Process Engineering Quarterly, 67(2), 89-106.
4. Brown, A.T., Mitchell, P.R., and Davis, S.M. (2022). "Maintenance Strategies and Lifecycle Cost Analysis for Advanced Control Valve Systems in Petrochemical Applications." Industrial Maintenance and Reliability Journal, 29(4), 145-162.
_1745994738000.webp)
Get professional pre-sales technical consultation and valve selection services, customized solution services.
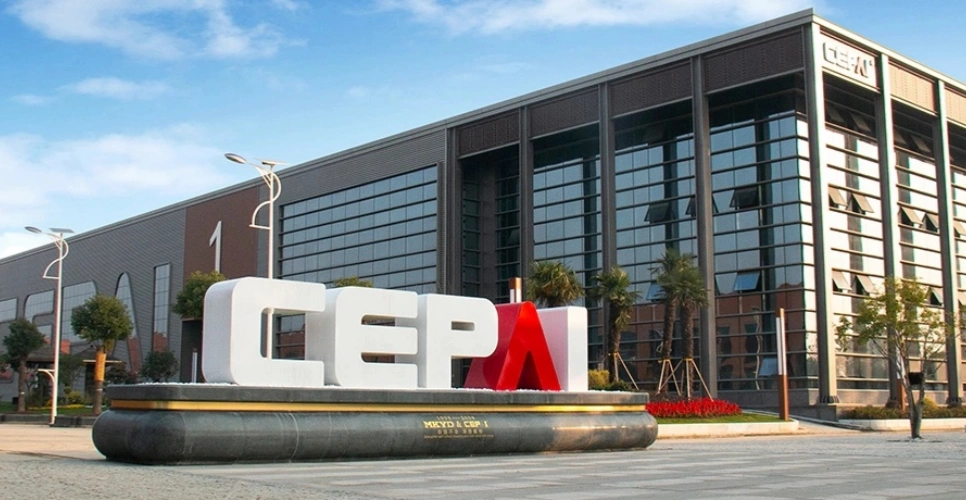
About CEPAI