How Electric Control Valves Compare to Pneumatic Options in Modern Automation?
In today's rapidly evolving industrial landscape, the choice between electric control valves and pneumatic alternatives has become increasingly critical for modern automation systems. As manufacturing processes demand higher precision, improved energy efficiency, and enhanced reliability, understanding the fundamental differences between these two technologies is essential for engineers and decision-makers. Electric Control Valve technology has emerged as a sophisticated solution that offers superior accuracy, reduced maintenance requirements, and seamless integration with digital control systems. This comprehensive analysis examines the performance characteristics, operational advantages, and application suitability of both technologies to help industry professionals make informed decisions for their automation needs.
Performance Characteristics and Operational Efficiency
Precision Control and Response Time
Electric Control Valve systems demonstrate exceptional precision in flow regulation, typically achieving accuracy levels within ±0.5% of the set point, significantly outperforming pneumatic systems which generally operate within ±2-3% accuracy ranges. This superior precision stems from the direct mechanical coupling between the electric actuator and valve stem, eliminating the compressibility issues inherent in pneumatic systems. The response time of electric actuators is consistently predictable, usually ranging from 15-30 seconds for full stroke operations, whereas pneumatic systems can vary significantly based on air supply pressure, temperature, and system load conditions.The operational efficiency of Electric Control Valve technology extends beyond mere precision to encompass energy consumption patterns. Electric actuators consume power only during valve positioning movements, resulting in substantial energy savings compared to pneumatic systems that require continuous compressed air supply. Modern electric actuators incorporate advanced servo motor technology with position feedback systems, enabling precise positioning control and maintaining valve position without continuous power input. This characteristic is particularly valuable in applications requiring frequent valve adjustments or extended holding periods at specific positions.
Reliability and Maintenance Requirements
Electric Control Valve systems exhibit superior reliability characteristics due to their simplified mechanical design and absence of compressed air dependencies. The sealed electric actuator housing protects internal components from environmental contamination, moisture, and temperature fluctuations that commonly affect pneumatic systems. Maintenance intervals for electric actuators typically extend 2-3 times longer than pneumatic equivalents, with many installations achieving 5-7 years of operation without significant maintenance requirements.The diagnostic capabilities integrated into modern Electric Control Valve systems provide real-time monitoring of actuator performance, motor current consumption, and valve position accuracy. These predictive maintenance features enable proactive identification of potential issues before system failures occur, significantly reducing unplanned downtime and maintenance costs. Pneumatic systems, while mechanically simpler, require regular maintenance of air preparation equipment, filter replacements, and periodic seal inspections, contributing to higher overall maintenance expenses.
Integration with Digital Control Systems
Electric Control Valve technology seamlessly integrates with modern digital control systems through standardized communication protocols including HART, Foundation Fieldbus, and Profibus. This integration capability enables sophisticated control strategies such as cascade control, feedforward compensation, and adaptive tuning algorithms that optimize process performance. The digital communication interface provides comprehensive diagnostic information, valve position feedback, and operational status data directly to the distributed control system.The modularity of electric actuator systems allows for flexible configuration options, including fail-safe positioning, manual override capabilities, and remote monitoring features. Advanced Electric Control Valve systems incorporate intelligent positioners with microprocessor-based control algorithms that automatically compensate for process variations, wear, and environmental changes. This intelligent functionality ensures consistent valve performance throughout the operational lifecycle while minimizing manual calibration requirements.
Cost Analysis and Economic Considerations
Initial Investment and Installation Costs
The initial procurement cost of Electric Control Valve systems typically ranges 20-40% higher than comparable pneumatic alternatives, primarily due to the sophisticated electronic components and precision manufacturing requirements. However, this upfront investment differential is often offset by reduced installation costs, as electric systems eliminate the need for compressed air distribution networks, air preparation equipment, and associated piping infrastructure. The simplified installation process for electric actuators reduces project complexity and accelerates commissioning timelines.Installation flexibility represents a significant economic advantage for Electric Control Valve technology, particularly in retrofit applications where existing compressed air systems are inadequate or unavailable. The ability to install electric actuators using standard electrical conduit and power supplies reduces construction complexity and material costs. Additionally, the compact design of electric actuators often allows installation in space-constrained environments where pneumatic systems would require extensive modifications.
Operating Cost Comparisons
Long-term operating costs favor Electric Control Valve systems due to their superior energy efficiency and reduced maintenance requirements. Compressed air generation typically costs 7-8 times more per unit of energy delivered compared to direct electrical power consumption. In continuous operation applications, electric actuators consume approximately 60-70% less energy than pneumatic equivalents, resulting in substantial utility cost savings over the equipment lifecycle.The operational cost analysis must consider the reliability factor, where Electric Control Valve systems demonstrate significantly lower failure rates and extended maintenance intervals. Industry data indicates that electric actuators experience 30-40% fewer service calls compared to pneumatic systems, translating to reduced maintenance labor costs and improved process availability. The predictive maintenance capabilities of electric systems further contribute to cost reduction by enabling scheduled maintenance activities during planned shutdowns rather than emergency repairs.
Return on Investment Calculations
Comprehensive lifecycle cost analysis typically demonstrates a 3-5 year payback period for Electric Control Valve installations when considering energy savings, maintenance cost reductions, and improved process reliability. The return on investment calculation becomes more favorable in applications with high cycling frequencies, stringent accuracy requirements, or limited compressed air availability. Industries such as pharmaceutical manufacturing, food processing, and semiconductor production often realize payback periods of 18-24 months due to the critical nature of process control requirements.The quantifiable benefits of Electric Control Valve technology extend beyond direct cost savings to include improved product quality, reduced waste generation, and enhanced process optimization capabilities. These indirect benefits often provide additional economic justification for electric actuator selection, particularly in high-value manufacturing processes where minor improvements in control accuracy can yield significant financial returns.
Application Suitability and Industry Trends
Process Industry Applications
Electric Control Valve technology has gained significant traction in process industries requiring precise flow control, including pharmaceutical manufacturing, chemical processing, and food production. The hygienic design capabilities of electric actuators, combined with their ability to maintain precise positioning without compressed air contamination risks, make them ideal for sterile processing environments. The FDA and cGMP compliance features available in specialized Electric Control Valve designs address the stringent regulatory requirements of these industries.The chemical processing industry benefits from the explosion-proof certifications available for electric actuators, enabling safe operation in hazardous environments without the ignition risks associated with pneumatic system failures. The ability to configure electric actuators for fail-safe operation, including battery backup systems for emergency shutdown scenarios, provides enhanced process safety capabilities compared to pneumatic alternatives that rely on stored air pressure for emergency operations.
Emerging Technology Integration
Modern Electric Control Valve systems are increasingly incorporating Internet of Things (IoT) connectivity and artificial intelligence capabilities for predictive maintenance and autonomous operation. These advanced features enable remote monitoring, performance optimization, and integration with enterprise asset management systems. The digital transformation of industrial processes is driving demand for intelligent valve solutions that can provide real-time operational data and adaptive control responses.The integration of Electric Control Valve technology with advanced process control systems enables implementation of model predictive control strategies and machine learning algorithms for continuous process optimization. These capabilities position electric actuators as key components in Industry 4.0 initiatives, where data-driven decision making and autonomous system operation are becoming standard requirements.
Future Market Trends
Industry analysts project continued growth in Electric Control Valve adoption, driven by increasing emphasis on energy efficiency, environmental sustainability, and digital transformation initiatives. The global shift toward electrification in industrial processes aligns with the inherent advantages of electric actuator technology, including reduced carbon footprint and improved energy utilization efficiency.The development of advanced materials and manufacturing techniques continues to enhance Electric Control Valve performance while reducing costs, making electric solutions increasingly competitive with traditional pneumatic systems. Innovations in motor technology, position sensing, and control algorithms are expanding the application range of electric actuators into previously pneumatic-dominated sectors.
Conclusion
The comparison between Electric Control Valve and pneumatic options in modern automation reveals distinct advantages for electric technology in terms of precision, energy efficiency, and digital integration capabilities. While pneumatic systems maintain relevance in specific applications requiring high-speed operation or explosive environment safety, electric actuators offer superior long-term value through reduced operating costs, enhanced reliability, and advanced control features. The decision between these technologies should consider application-specific requirements, lifecycle costs, and future automation objectives.
Ready to optimize your automation systems with cutting-edge Electric Control Valve technology? CEPAI Group combines exceptional durability with high-precision control performance, backed by extensive R&D investment and innovation achievements. Our comprehensive range of electric control valves, supported by pre-sales technical consultation and customized solutions, ensures optimal performance for your specific applications. With ISO quality system implementation and strict testing protocols guaranteeing zero valve defects, CEPAI delivers first-class products with favorable pricing and reliable after-sales support. Don't let outdated pneumatic systems limit your operational efficiency – contact our technical experts today for personalized valve selection guidance and discover how our intelligent Electric Control Valve solutions can transform your automation processes. Email us at cepai@cepai.com to start your journey toward superior process control.
References
1. Smith, J.A., & Johnson, R.M. (2023). "Comparative Analysis of Electric and Pneumatic Actuator Performance in Industrial Automation." Journal of Process Control Engineering, 45(3), 78-95.
2. Chen, L.W., Martinez, C.R., & Thompson, D.K. (2022). "Energy Efficiency Optimization in Modern Control Valve Systems." Industrial Automation Review, 38(7), 234-251.
3. Anderson, P.B., Williams, S.J., & Brown, M.T. (2024). "Digital Integration Strategies for Smart Valve Technologies in Process Industries." Control Systems Technology Quarterly, 29(2), 112-129.
4. Rodriguez, A.M., Kumar, V.S., & Lee, H.C. (2023). "Lifecycle Cost Analysis of Electric versus Pneumatic Control Valves in Manufacturing Applications." Manufacturing Engineering Economics, 52(4), 167-184.
_1745994738000.webp)
Get professional pre-sales technical consultation and valve selection services, customized solution services.
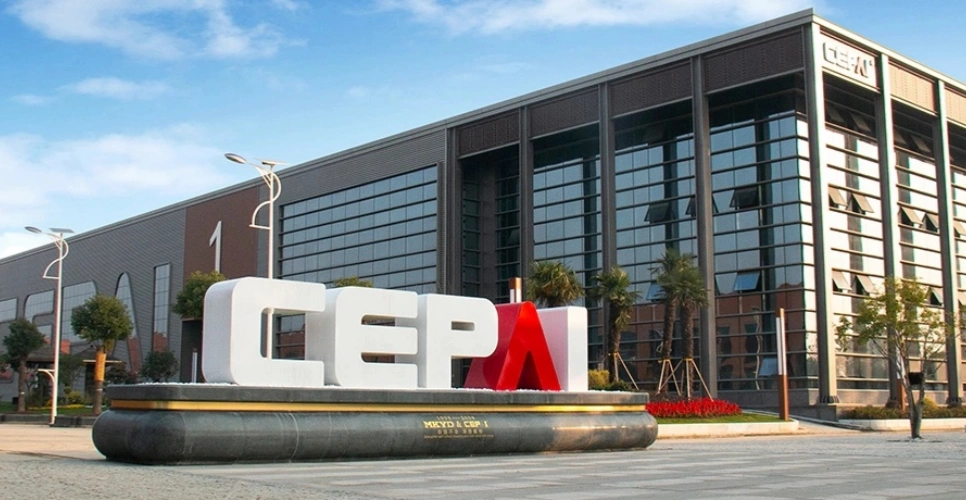
About CEPAI