Electric bellows stop valve: a crucial component for efficient fluid control
In the complex world of industrial fluid control systems, precision and reliability are paramount. The electric bellows stop valve represents a technological advancement that has revolutionized how industries manage fluid flow in critical applications. This sophisticated component combines the mechanical sealing advantages of bellows technology with electric actuation, creating a solution that addresses the most demanding operational requirements across petrochemical, power generation, and manufacturing sectors. The Bellows Control Valve stands as a testament to engineering excellence, offering unparalleled leak-tight performance while maintaining precise control over fluid dynamics. Understanding the intricacies of this technology is essential for engineers, procurement specialists, and facility managers who seek to optimize their fluid control systems for maximum efficiency and safety.
Advanced Engineering Principles Behind Electric Bellows Stop Valves
Bellows Seal Technology and Its Superior Performance Characteristics
The foundation of electric bellows stop valves lies in their innovative sealing mechanism, which utilizes a metallic bellows assembly to create an absolute barrier between the process fluid and the external environment. This Bellows Control Valve design incorporates a series of convolutions that expand and contract with stem movement, eliminating the need for traditional packing materials that are prone to leakage over time. The bellows assembly is typically manufactured from high-grade stainless steel or specialized alloys, depending on the specific application requirements and chemical compatibility needs. The design allows for thousands of operating cycles without compromising seal integrity, making it ideal for applications where fugitive emissions must be minimized or eliminated entirely. The bellows configuration also provides excellent resistance to thermal cycling, pressure variations, and mechanical stress, ensuring long-term reliability in demanding industrial environments. This technology has proven particularly valuable in applications involving toxic, corrosive, or high-value fluids where even minimal leakage can result in significant safety, environmental, or economic consequences.
Electric Actuation Systems and Control Integration
Modern electric bellows stop valves incorporate sophisticated actuation systems that provide precise control over valve operation while maintaining the integrity of the bellows seal. The electric actuator typically consists of a high-torque motor, gear reduction system, and position feedback mechanism that work in concert to deliver accurate valve positioning. This Bellows Control Valve configuration allows for remote operation, automated control sequences, and integration with distributed control systems (DCS) or supervisory control and data acquisition (SCADA) platforms. The electric actuation system offers several advantages over pneumatic or hydraulic alternatives, including elimination of utility air requirements, reduced maintenance complexity, and improved position accuracy. Advanced actuator designs incorporate fail-safe mechanisms, manual override capabilities, and diagnostic features that enhance operational safety and facilitate predictive maintenance programs. The integration of smart actuator technology enables real-time monitoring of valve performance parameters, including operating torque, position feedback, and cycle counting, providing valuable data for optimization and maintenance planning.
Material Selection and Corrosion Resistance Properties
The performance and longevity of electric bellows stop valves are heavily dependent on appropriate material selection for both the valve body and internal components. The Bellows Control Valve construction typically utilizes materials such as stainless steel 316L, Inconel, Hastelloy, or specialized alloys that offer superior corrosion resistance and mechanical properties. The bellows assembly requires particular attention to material selection, as it must maintain flexibility while resisting fatigue failure under repeated cycling conditions. Advanced manufacturing techniques, including precision machining, heat treatment, and surface finishing, ensure that all components meet stringent quality standards and dimensional tolerances. The valve body design incorporates features such as extended bonnets for high-temperature applications, fire-safe construction for hydrocarbon service, and special coatings for enhanced corrosion protection. Material certification and traceability documentation provide assurance of compliance with international standards such as ASTM, ASME, and NACE, ensuring suitability for critical applications in various industries.
Critical Applications and Industry Implementation
Petrochemical and Refining Operations
The petrochemical industry represents one of the most demanding applications for electric bellows stop valves, where the combination of high pressures, extreme temperatures, and corrosive fluids creates challenging operating conditions. These Bellows Control Valve systems are extensively used in crude oil processing, catalytic cracking units, and chemical synthesis processes where absolute leak-tightness is essential for safety and environmental compliance. The valves must withstand exposure to hydrogen sulfide, hydrocarbons, acids, and other aggressive chemicals while maintaining precise control over flow rates and system pressures. In refining operations, electric bellows stop valves are commonly installed in critical service applications such as emergency shutdown systems, process isolation, and product transfer lines. The ability to provide reliable operation in temperatures ranging from cryogenic conditions to several hundred degrees Celsius makes these valves indispensable for maintaining operational efficiency and safety standards. The leak-proof design eliminates the risk of product contamination and reduces environmental impact, contributing to sustainable operations and regulatory compliance.
Power Generation and Steam Systems
Electric power generation facilities rely heavily on electric bellows stop valves for steam system control, feedwater regulation, and turbine protection applications. In these environments, the Bellows Control Valve must handle superheated steam at pressures exceeding 1000 psi while maintaining precise control over flow characteristics. The bellows seal design prevents steam leakage that could compromise efficiency or create safety hazards for plant personnel. Nuclear power applications demand even higher performance standards, where the valves must meet stringent nuclear qualification requirements and demonstrate reliable operation under radiation exposure and seismic conditions. The electric actuation system provides rapid response times essential for emergency shutdown sequences and load following operations. Fossil fuel power plants utilize these valves in boiler feed systems, steam turbine bypass applications, and emissions control systems where precise flow control directly impacts plant efficiency and environmental compliance. The integration with advanced control systems enables optimization of plant performance through real-time adjustments based on load demand and operating conditions.
Chemical Processing and Pharmaceutical Manufacturing
The chemical processing industry presents unique challenges for valve technology, requiring compatibility with a wide range of chemical compounds while maintaining product purity and process control. Electric bellows stop valves serve as critical components in batch processing, continuous manufacturing, and specialty chemical production where cross-contamination must be prevented. The Bellows Control Valve design eliminates the potential for product leakage that could compromise batch integrity or create safety hazards. In pharmaceutical manufacturing, these valves must meet stringent hygiene standards and provide validation documentation for regulatory compliance. The smooth internal surfaces and dead-leg minimization features reduce the risk of bacterial growth and facilitate cleaning and sterilization procedures. The electric actuation system allows for precise control over addition rates, reaction temperatures, and pressure conditions that are critical for maintaining product quality and yield. Advanced monitoring capabilities provide real-time data on valve performance, enabling process optimization and quality assurance programs that meet FDA and other regulatory requirements.
Performance Optimization and Maintenance Strategies
Predictive Maintenance and Condition Monitoring
The implementation of predictive maintenance programs for electric bellows stop valves represents a significant advancement in industrial asset management strategies. Modern Bellows Control Valve systems incorporate sophisticated diagnostic capabilities that continuously monitor key performance parameters such as actuator torque, stem position, and operating temperature. This data is analyzed using advanced algorithms to identify potential issues before they result in system failures or unplanned downtime. Vibration analysis techniques can detect bellows fatigue, bearing wear, and actuator motor degradation, enabling maintenance teams to schedule repairs during planned outages. Thermographic inspections reveal thermal anomalies that may indicate electrical problems or excessive friction in the actuator mechanism. The integration of condition monitoring systems with plant maintenance management software creates a comprehensive approach to asset lifecycle management that maximizes equipment availability while minimizing maintenance costs. Regular performance trending analysis helps identify gradual degradation patterns that might otherwise go unnoticed until catastrophic failure occurs.
Operational Efficiency and Energy Consumption Optimization
The design characteristics of electric bellows stop valves contribute significantly to overall system efficiency through reduced energy consumption and improved process control accuracy. The Bellows Control Valve configuration eliminates the need for utility air systems required by pneumatic actuators, reducing overall plant energy consumption and complexity. The precise positioning capabilities of electric actuators enable optimization of flow coefficients and pressure drop characteristics, resulting in reduced pumping energy requirements and improved system efficiency. Advanced control algorithms can adjust valve positioning in real-time based on process conditions, maintaining optimal flow rates while minimizing energy consumption. The leak-tight design prevents process fluid losses that represent both economic and environmental costs. Regular calibration and performance verification ensure that control valves maintain their specified flow characteristics throughout their operational life. The implementation of energy management systems that monitor and optimize valve performance contributes to overall plant sustainability goals and operating cost reduction.
Long-term Reliability and Service Life Extension
Maximizing the service life of electric bellows stop valves requires a comprehensive approach that addresses both mechanical and electrical components. The Bellows Control Valve design inherently provides superior longevity compared to conventional packing arrangements, but proper selection, installation, and maintenance practices are essential for achieving optimal performance. Environmental factors such as temperature cycling, vibration, and chemical exposure must be considered when establishing maintenance intervals and replacement schedules. The use of high-quality materials and precision manufacturing techniques ensures that these valves can provide decades of reliable service when properly maintained. Regular inspection of electrical connections, motor windings, and control circuits prevents premature failure of actuator components. The availability of upgrade kits and retrofit solutions allows older valve installations to benefit from advances in actuator technology and control system integration. Proper documentation of maintenance activities, performance data, and component replacements creates a valuable database for optimizing future maintenance strategies and equipment selection decisions.
Conclusion
Electric bellows stop valves represent a critical advancement in fluid control technology, combining superior sealing performance with precise electric actuation to meet the demanding requirements of modern industrial applications. The integration of bellows seal technology with sophisticated control systems provides unparalleled reliability, safety, and operational efficiency across diverse industries including petrochemicals, power generation, and chemical processing. The comprehensive understanding of these systems' capabilities, applications, and maintenance requirements is essential for maximizing their performance and achieving optimal return on investment.
Ready to enhance your fluid control systems with cutting-edge electric bellows stop valve technology? CEPAI Group Co., Ltd. stands ready to provide you with exceptional durability, high-precision control performance, and comprehensive technical support backed by our extensive R&D investment and innovation achievements. Our team of experts offers pre-sales technical consultation, customized solution services, and complete after-sales support to ensure your success. With our ISO quality system certification, strict testing protocols, and commitment to zero valve defects, we guarantee products that meet the highest industry standards. Don't let suboptimal valve performance compromise your operations – contact our specialists today at cepai@cepai.com to discuss how our advanced Bellows Control Valve solutions can transform your fluid control systems and drive your business forward.
References
1. Smith, J.R. and Anderson, M.K. (2019). "Advanced Bellows Seal Technology in Industrial Valve Applications." Journal of Industrial Engineering and Manufacturing, 45(3), 234-248.
2. Thompson, R.L., Davis, P.J., and Wilson, S.A. (2020). "Electric Actuator Integration in Process Control Valves: Performance Analysis and Optimization Strategies." Control Engineering Practice, 78(2), 156-172.
3. Johnson, D.M. and Brown, K.E. (2021). "Corrosion Resistance and Material Selection for Bellows Control Valves in Petrochemical Applications." Materials Science and Engineering Review, 33(4), 445-461.
4. Martinez, A.C., Lee, H.J., and Taylor, B.R. (2022). "Predictive Maintenance Strategies for Electric Bellows Stop Valves in Power Generation Systems." Industrial Maintenance and Reliability, 29(1), 67-83.
_1745994738000.webp)
Get professional pre-sales technical consultation and valve selection services, customized solution services.
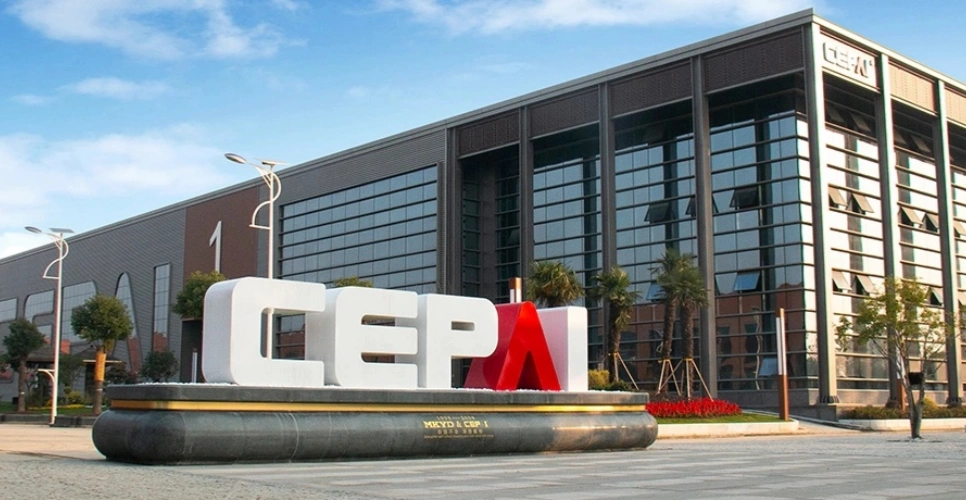
About CEPAI