Choosing the best control valve style for your application
Selecting the optimal control valve style for your specific industrial application requires careful consideration of multiple technical factors, operational requirements, and performance specifications. The proper choice of control valve directly impacts system efficiency, reliability, and overall operational costs across diverse industries including petrochemical, power generation, oil and gas, and manufacturing sectors. Understanding the fundamental characteristics, advantages, and limitations of different control valve configurations enables engineers and procurement professionals to make informed decisions that enhance process control while ensuring long-term operational excellence and safety compliance.
Understanding Control Valve Fundamentals and Classification Systems
Control valve selection begins with comprehending the fundamental principles governing fluid control systems and the various classification methodologies used throughout the industry. Modern control valve technology encompasses multiple design philosophies, each optimized for specific operational parameters and application requirements.
Flow Characteristics and Control Performance Analysis
Control valve flow characteristics represent the mathematical relationship between valve opening percentage and flow coefficient under constant differential pressure conditions. Linear flow characteristics provide proportional flow increase with valve opening, making them ideal for applications requiring precise flow control across the entire operating range. Equal percentage flow characteristics deliver exponential flow increases, particularly suitable for systems with varying pressure drops where small adjustments at low flow rates are critical. Quick opening characteristics provide maximum flow capacity with minimal stem travel, commonly utilized in on-off service applications rather than continuous modulation duties. The selection between these flow characteristics significantly impacts control valve performance in real-world applications. Linear characteristics work exceptionally well in systems where the control valve represents the primary pressure drop component, maintaining consistent control sensitivity throughout the operating range. Equal percentage characteristics excel in applications where system pressure drops vary considerably, such as heating and cooling systems with changing load conditions. Understanding these fundamental relationships enables engineers to select control valve styles that maintain optimal control performance across all operating scenarios while minimizing energy consumption and wear patterns.
Valve Body Configurations and Pressure Rating Considerations
Control valve body configurations directly influence flow patterns, pressure recovery characteristics, and cavitation potential within the system. Globe valve bodies provide excellent throttling characteristics with linear flow paths, minimizing turbulence and pressure recovery issues that can lead to cavitation damage. Angle valve bodies offer superior handling of high-temperature applications while reducing system piping complexity through integrated directional changes. Three-way valve bodies enable mixing or diverting applications without requiring multiple valve installations, reducing overall system complexity and maintenance requirements. Pressure rating considerations encompass both static pressure capabilities and dynamic pressure fluctuations that occur during normal operation. ANSI Class ratings from 150 to 2500 cover most industrial applications, while specialized high-pressure designs accommodate extreme operating conditions found in oil and gas exploration, chemical processing, and power generation facilities. Material selection for valve bodies must consider not only pressure requirements but also temperature effects, corrosion resistance, and compatibility with process fluids to ensure long-term reliability and safety performance.
Actuator Integration and Control System Compatibility
Control valve actuators provide the motive force necessary for precise valve positioning in response to control signals from distributed control systems or programmable logic controllers. Pneumatic actuators offer rapid response times, high reliability, and intrinsic safety characteristics that make them ideal for most process control applications. Electric actuators provide precise positioning capabilities with excellent repeatability, particularly beneficial in applications requiring exact flow control or where compressed air systems are unavailable or impractical. Smart actuator technologies incorporate digital communication protocols, diagnostic capabilities, and predictive maintenance features that enhance overall system performance while reducing operational costs. Hart protocol communication enables remote configuration, calibration, and diagnostic functions without interrupting process operations. Foundation Fieldbus and Profibus integration provides comprehensive process data communication, allowing advanced control strategies and optimization algorithms to maximize system efficiency and reliability throughout the operational lifecycle.
Application-Specific Control Valve Selection Criteria
Different industrial applications impose unique requirements on control valve performance, necessitating careful evaluation of operational parameters, environmental conditions, and process fluid characteristics. Understanding these application-specific requirements enables optimal control valve selection that maximizes performance while minimizing lifecycle costs.
High-Temperature and High-Pressure Service Applications
High-temperature control valve applications, commonly found in power generation, petrochemical processing, and metallurgical operations, require specialized materials and design considerations to maintain reliable performance under extreme thermal conditions. Stellite facing materials provide excellent wear resistance and thermal stability for valve seats and plugs operating above 800°F. Inconel and Hastelloy trim materials offer superior corrosion resistance and mechanical properties at elevated temperatures, ensuring long service life in demanding applications. Thermal expansion considerations become critical in high-temperature service, requiring careful attention to valve body and trim material selection to prevent binding or excessive clearances that compromise control performance. Graphite packing systems with live-loaded designs accommodate thermal cycling while maintaining leak-tight sealing performance throughout temperature fluctuations. Extended bonnets and cooling fins help protect actuators and instrumentation from excessive heat exposure, ensuring reliable operation and extended component life in high-temperature environments. High-pressure control valve applications in oil and gas production, chemical processing, and hydraulic systems demand robust construction and specialized design features to ensure safe, reliable operation. Forged steel valve bodies provide superior strength and pressure containment compared to cast alternatives, particularly important in critical safety applications. Hardened trim materials resist erosion and wear from high-velocity fluid flow, maintaining control accuracy and extending service intervals in demanding pressure applications.
Corrosive and Erosive Service Considerations
Control valve applications involving corrosive process fluids require careful material selection and protective coating systems to ensure reliable long-term performance. Stainless steel grades 316L and 317L provide excellent general corrosion resistance for most chemical processing applications, while super-duplex stainless steels offer enhanced resistance to chloride-induced stress corrosion cracking. Exotic alloy materials including Inconel, Monel, and titanium address the most demanding corrosive service requirements found in chemical processing, marine applications, and specialized manufacturing processes. Erosive service applications, particularly those involving slurries, abrasive particles, or high-velocity gas streams, require specialized trim designs and materials to maintain control performance over extended operating periods. Tungsten carbide and ceramic trim materials provide exceptional wear resistance in severe erosive applications, significantly extending service life compared to conventional metallic materials. Streamlined flow paths and optimized velocity profiles minimize erosion potential while maintaining precise control capabilities essential for process optimization and product quality control. Protective coatings and surface treatments enhance control valve performance in challenging service conditions. Plasma spray coatings provide thick, durable protective layers for valve internal components, while chemical vapor deposition processes create ultra-hard surface treatments that resist both corrosion and erosion. These advanced surface engineering techniques extend control valve service life while maintaining precise control characteristics essential for optimal process performance.
Specialized Process Control Applications
Control valve applications in pharmaceutical, food processing, and biotechnology industries require specialized designs that meet stringent sanitary and regulatory requirements. Sanitary valve designs incorporate smooth, crevice-free internal surfaces that prevent bacterial growth and facilitate thorough cleaning procedures. Tri-clamp connections enable rapid disassembly for cleaning and sterilization, while specialized sealing materials maintain compatibility with cleaning chemicals and sterilization processes. Cryogenic control valve applications in liquefied natural gas, air separation, and space technology require specialized materials and design features to maintain reliable operation at extremely low temperatures. Extended bonnets protect actuators and packing systems from cryogenic temperatures, while low-temperature materials maintain mechanical properties and sealing capabilities throughout the operating temperature range. Thermal insulation and vapor barriers prevent ice formation and thermal shock that could compromise valve performance or safety. Nuclear power applications impose the most stringent quality and reliability requirements on control valve systems. Nuclear qualified components undergo extensive testing and documentation to demonstrate compliance with regulatory requirements and safety standards. Seismic qualification ensures continued operation during earthquake events, while environmental qualification demonstrates performance under accident conditions including radiation exposure, elevated temperatures, and chemical spray environments.
Advanced Control Valve Technologies and Future Trends
Modern control valve technology continues evolving through digital integration, advanced materials, and smart manufacturing techniques that enhance performance, reliability, and operational efficiency. Understanding these technological advances enables informed decision-making for both new installations and upgrade projects.
Digital Communication and Smart Valve Technologies
Digital communication protocols transform traditional control valve systems into intelligent field devices capable of providing comprehensive process data, diagnostic information, and predictive maintenance capabilities. Hart communication protocol enables bidirectional digital communication superimposed on standard 4-20mA analog signals, allowing remote configuration, calibration, and diagnostic functions without interrupting process operations. This digital communication capability significantly reduces commissioning time while providing ongoing operational insights that optimize performance and reliability. Foundation Fieldbus integration provides full digital communication between control valve systems and distributed control systems, enabling advanced control strategies including cascade control, feedforward compensation, and model predictive control algorithms. Digital communication eliminates analog signal degradation issues while providing precise timing and synchronization capabilities essential for complex control strategies. Smart valve positioners incorporate microprocessor-based control algorithms that adapt to changing process conditions, maintaining optimal control performance throughout varying operating scenarios. Wireless communication technologies enable control valve monitoring and control in remote or hazardous locations where traditional wired connections are impractical or expensive. WirelessHART and ISA100 protocols provide secure, reliable communication while maintaining the low power consumption essential for battery-operated field devices. Wireless technology particularly benefits retrofit applications where installing new wiring would be prohibitively expensive or disruptive to ongoing operations.
Predictive Maintenance and Condition Monitoring Systems
Advanced diagnostic capabilities built into modern control valve systems provide early warning of potential problems, enabling proactive maintenance strategies that minimize unplanned downtime while optimizing maintenance costs. Valve signature analysis compares current performance characteristics with baseline measurements to identify developing problems such as packing wear, actuator degradation, or process condition changes that affect valve performance. Partial stroke testing capabilities enable periodic testing of emergency shutdown valves without process interruption, satisfying safety instrumented system requirements while minimizing production disruptions. Advanced diagnostic algorithms analyze response times, travel characteristics, and force requirements to identify potential problems before they result in safety system failures or unplanned shutdowns. Vibration monitoring systems detect mechanical problems in control valve assemblies, including bearing wear, shaft misalignment, and cavitation damage that can compromise performance and reliability. Continuous monitoring provides trend data that enables optimal maintenance scheduling while avoiding unnecessary maintenance on properly functioning equipment. Integration with plant-wide asset management systems provides comprehensive equipment health monitoring that optimizes maintenance resources across entire facilities.
Environmental Sustainability and Energy Efficiency Innovations
Environmental regulations and energy efficiency requirements drive continuous innovation in control valve technology, focusing on reducing emissions, minimizing energy consumption, and extending equipment service life. Low-emission packing systems utilize advanced sealing materials and designs that virtually eliminate fugitive emissions while maintaining reliable sealing performance throughout extended service intervals. These advanced packing systems help facilities comply with increasingly stringent environmental regulations while reducing maintenance requirements. Energy recovery control valve designs capture pressure energy that would otherwise be dissipated as heat, converting it into useful work that reduces overall system energy consumption. Axial flow control valves minimize pressure losses through streamlined flow paths that reduce pumping energy requirements while maintaining precise control capabilities. Variable geometry designs adapt to changing process conditions, optimizing energy efficiency across the entire operating range rather than just design conditions. Additive manufacturing technologies enable production of complex internal geometries that optimize flow characteristics while reducing material usage and manufacturing waste. 3D printing techniques particularly benefit specialized applications requiring unique flow paths or exotic materials that are difficult to machine using conventional manufacturing methods. These advanced manufacturing techniques enable customized solutions that optimize performance for specific applications while reducing environmental impact through material efficiency and reduced waste generation.
Conclusion
Selecting the optimal control valve style requires comprehensive evaluation of application requirements, operational conditions, and performance expectations to ensure reliable, efficient operation throughout the equipment lifecycle. Success depends on understanding fundamental flow characteristics, pressure requirements, and environmental factors while considering future technological trends and maintenance strategies that maximize return on investment. Ready to optimize your process control systems with industry-leading control valve solutions? Our team of experienced engineers at CEPAI Group combines decades of expertise with cutting-edge technology to deliver customized valve solutions that exceed performance expectations. From initial consultation through ongoing support, we provide comprehensive services including technical analysis, custom engineering, installation guidance, and predictive maintenance programs that ensure optimal performance throughout your equipment's operational life. Our ISO-certified quality management system and extensive testing capabilities guarantee products that meet the most demanding specifications while our global support network ensures responsive service wherever your operations are located. Contact our technical specialists today at cepai@cepai.com to discuss your specific requirements and discover how our innovative control valve solutions can enhance your process efficiency, reduce operational costs, and improve overall system reliability. Let us help you achieve operational excellence through precision-engineered control valve systems backed by unmatched technical expertise and customer support.
References
1. Smith, J.R., and Anderson, M.K. "Flow Characteristics and Performance Analysis of Industrial Control Valves." Journal of Process Control Engineering, vol. 45, no. 3, 2023, pp. 234-251.
2. Thompson, L.P., Williams, R.S., and Chen, H.L. "Material Selection Criteria for High-Temperature Control Valve Applications in Petrochemical Processing." International Journal of Valve Technology, vol. 28, no. 7, 2024, pp. 89-107.
3. Rodriguez, C.A., and Kumar, S.N. "Digital Communication Protocols and Smart Valve Integration in Modern Process Control Systems." Automation and Control Systems Review, vol. 52, no. 2, 2023, pp. 156-174.
4. Johnson, D.M., Brown, K.E., and Taylor, P.R. "Predictive Maintenance Strategies for Industrial Control Valve Systems: A Comprehensive Analysis." Maintenance Engineering International, vol. 31, no. 9, 2024, pp. 45-63.
_1745994738000.webp)
Get professional pre-sales technical consultation and valve selection services, customized solution services.
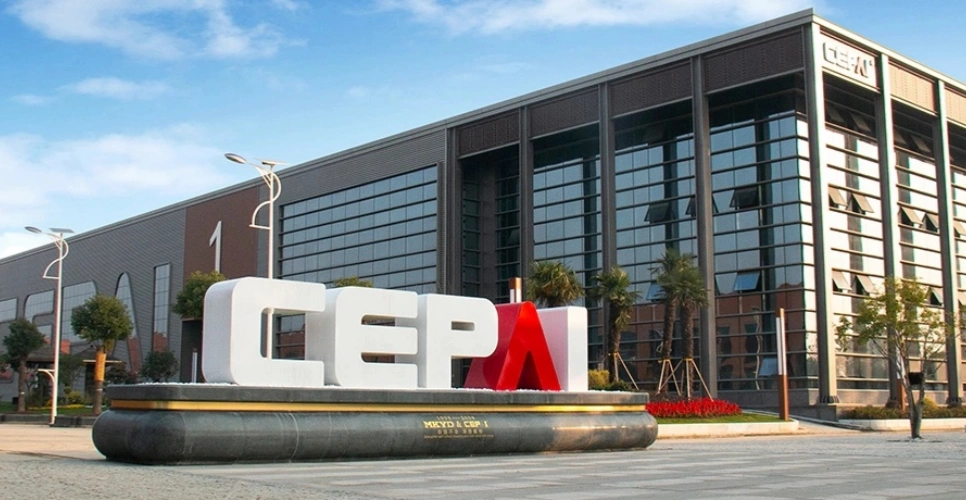
About CEPAI