Precision Valve Selection Guide for Chemical Processes
The chemical processing industry demands unparalleled precision, reliability, and safety in every component of its operations. Among the most critical elements in any chemical process system are valves, which control the flow, pressure, and direction of various substances throughout complex manufacturing processes. Selecting the right valve technology can mean the difference between optimal efficiency and costly downtime, between precise product quality and batch failures. The Precision Control Valve stands as the cornerstone of modern chemical processing operations, offering engineers and plant operators the sophisticated flow control capabilities necessary to maintain stringent process parameters while ensuring operational safety and regulatory compliance.
Understanding Chemical Process Requirements for Valve Selection
Process Conditions and Operating Parameters
Chemical processes operate under diverse and often extreme conditions that place unique demands on valve systems. Temperature variations in chemical processing can range from cryogenic applications at -196°C to high-temperature processes exceeding 650°C, requiring valves that maintain structural integrity and sealing capabilities across this entire spectrum. The Precision Control Valve must demonstrate exceptional thermal stability, with materials selected specifically for their resistance to thermal expansion and contraction cycles. Pressure requirements in chemical applications frequently exceed standard industrial parameters, with some processes demanding valve ratings up to 420 bar or higher. These extreme pressure conditions necessitate robust valve body construction, typically employing forged steel or specialized alloy materials that can withstand the mechanical stresses without compromising operational safety. Furthermore, chemical processes often involve rapid pressure transitions and pulsating flow conditions that can cause valve components to experience fatigue stress, making material selection and design engineering critical factors in ensuring long-term reliability and preventing catastrophic failures that could endanger personnel and equipment.
Chemical Compatibility and Corrosion Resistance
The chemical compatibility of valve materials represents one of the most crucial considerations in valve selection for chemical processes. Different chemicals exhibit varying degrees of aggressiveness toward metallic and non-metallic valve components, with some substances capable of causing rapid degradation of inadequately specified materials. The Precision Control Valve designed for chemical applications must incorporate materials specifically chosen for their resistance to the particular chemicals they will encounter during operation. Stainless steel grades such as 316L and duplex steels like 2205 offer excellent corrosion resistance for many chemical applications, while exotic alloys including Hastelloy C-276, Inconel 625, and titanium provide superior performance in highly corrosive environments. Seal materials require equally careful consideration, with fluoropolymer seals like PTFE and FFKM offering exceptional chemical resistance while maintaining sealing integrity over extended service periods. The selection process must also account for potential chemical interactions between different process streams, as mixing incompatible chemicals can create unexpected corrosion mechanisms that standard material compatibility charts may not address. Advanced surface treatments and coatings can provide additional protection, extending valve service life and reducing maintenance requirements in challenging chemical environments.
Flow Characteristics and Control Requirements
Chemical processes demand precise flow control to maintain product quality, optimize reaction conditions, and ensure safe operations. The Precision Control Valve must provide accurate and repeatable flow characteristics that match the specific requirements of each application. Linear flow characteristics are preferred in applications where consistent control response is required across the entire flow range, while equal percentage characteristics excel in applications with wide turndown requirements or varying process conditions. The valve's inherent flow characteristics must be matched to the installed system characteristics to achieve optimal control performance, considering factors such as pump curves, system pressure drops, and process load variations. Cavitation and flashing represent significant concerns in chemical processing applications, particularly when handling volatile liquids or operating with high pressure drops across the valve. Advanced valve designs incorporate anti-cavitation trim configurations that minimize the formation and collapse of vapor bubbles, reducing noise, vibration, and potential damage to valve components. The control valve's rangeability, defined as the ratio between maximum and minimum controllable flow rates, must be sufficient to accommodate the full range of operating conditions expected in the chemical process while maintaining acceptable control accuracy throughout the entire range.
Critical Factors in Chemical Valve Specification
Safety and Environmental Considerations
Safety considerations in chemical valve applications extend far beyond basic operational requirements, encompassing personnel protection, environmental compliance, and emergency response capabilities. The Precision Control Valve in chemical service must incorporate design features that minimize the risk of fugitive emissions, which can pose serious health and environmental hazards while also representing significant economic losses. Low-emission valve designs featuring live-loaded packing systems, dual sealing arrangements, and bellows-sealed bonnet constructions provide enhanced containment of hazardous chemicals while reducing maintenance requirements and extending service intervals. Fire-safe valve designs become mandatory in applications involving flammable or explosive chemicals, requiring valve components to maintain their integrity and sealing capability even when exposed to external fire conditions. These designs typically incorporate metal-to-metal sealing surfaces that remain effective after soft seal materials have been compromised by high temperatures. Emergency shutdown capabilities must be integrated into critical valve applications, allowing for rapid process isolation in response to abnormal operating conditions or safety system triggers. The valve actuation system must be designed to fail in a predetermined safe position, whether fail-open or fail-closed, depending on the specific process safety requirements and consequence analysis.
Maintenance and Lifecycle Cost Considerations
The total cost of ownership for chemical process valves extends well beyond the initial purchase price, encompassing maintenance costs, spare parts availability, and potential production losses during maintenance activities. The Precision Control Valve selected for chemical applications must demonstrate not only initial cost-effectiveness but also long-term economic viability through reduced maintenance requirements and extended service life. Valve designs that facilitate in-line maintenance without system shutdown provide significant advantages in continuous chemical processes where production interruptions result in substantial economic losses. Replaceable seat and trim designs allow for maintenance of critical sealing surfaces without complete valve replacement, reducing both material costs and maintenance duration. The availability of spare parts and technical support from the valve manufacturer becomes crucial for maintaining operational continuity, particularly for specialized chemical applications requiring unique materials or configurations. Predictive maintenance capabilities, including condition monitoring sensors and diagnostic systems, enable proactive maintenance scheduling that minimizes unexpected failures while optimizing maintenance intervals based on actual operating conditions rather than arbitrary time schedules. The valve manufacturer's global service network and technical expertise in chemical applications contribute significantly to the overall value proposition and long-term operational success.
Performance Validation and Testing Requirements
Chemical process applications demand rigorous validation of valve performance characteristics to ensure compliance with process requirements and regulatory standards. The Precision Control Valve must undergo comprehensive testing protocols that verify its performance under the specific conditions it will encounter in service. Factory acceptance testing typically includes pressure testing at 150% of the design pressure, seat leakage testing to verify shut-off capabilities, and flow characteristic verification across the full operating range. Material certifications must trace all pressure-retaining components to their original heat of manufacture, providing documented evidence of chemical composition and mechanical properties that meet or exceed specification requirements. In chemical applications involving hazardous or regulated substances, additional testing may be required to demonstrate compliance with industry standards such as API, ASME, or international equivalents. Third-party testing and certification provide additional assurance of valve performance and regulatory compliance, particularly important for applications subject to governmental oversight or international trade requirements. Ongoing performance monitoring through process instrumentation and data analysis enables continuous validation of valve performance and early detection of degradation trends that might indicate the need for maintenance or replacement.
Implementation Strategies for Chemical Process Valve Systems
Integration with Process Control Systems
Modern chemical processes rely heavily on sophisticated process control systems that require seamless integration with valve actuation and monitoring equipment. The Precision Control Valve must be compatible with existing control system architectures while providing the necessary feedback and diagnostic information for optimal process control. Digital communication protocols such as HART, Foundation Fieldbus, or Profibus enable advanced valve diagnostics and configuration capabilities that enhance both control performance and maintenance efficiency. Smart valve positioners incorporate microprocessor-based control algorithms that provide superior positioning accuracy, faster response times, and advanced diagnostic capabilities compared to traditional pneumatic positioners. These intelligent devices can compensate for valve stem friction, hysteresis, and dead band effects while providing real-time feedback on valve position, actuator pressure, and internal diagnostics. Integration with distributed control systems enables centralized monitoring and control of all valve functions while maintaining local control capabilities for safety and emergency operations. The communication infrastructure must be designed to provide reliable data transmission in the challenging electromagnetic environment typically found in chemical processing facilities, with consideration for grounding, shielding, and surge protection requirements.
Installation and Commissioning Best Practices
Proper installation and commissioning of chemical process valves significantly impact their long-term performance and reliability. The Precision Control Valve installation must follow manufacturer specifications and industry best practices to ensure optimal performance and safety. Piping design considerations include providing adequate upstream and downstream straight pipe runs to minimize flow disturbances that could affect valve performance or cause premature wear. Proper pipe support and alignment prevent mechanical stress on valve bodies and connections that could lead to leakage or premature failure. During installation, particular attention must be paid to gasket selection and torque specifications for flanged connections, as improper installation can result in leakage of hazardous chemicals. The valve orientation must be appropriate for the specific application, considering factors such as self-draining capability, accessibility for maintenance, and actuator mounting requirements. Commissioning procedures should include verification of all control system interfaces, calibration of positioning equipment, and functional testing under actual operating conditions. Documentation of installation procedures, test results, and configuration parameters provides valuable reference information for future maintenance and troubleshooting activities while ensuring compliance with quality assurance requirements.
Optimization and Performance Monitoring
Continuous optimization of valve performance in chemical processes requires ongoing monitoring and analysis of operating data to identify opportunities for improvement. The Precision Control Valve equipped with advanced diagnostic capabilities provides valuable insight into process behavior and valve condition that enables proactive optimization strategies. Performance monitoring should include tracking of key parameters such as valve position, actuator pressure, process flow rates, and system pressures to identify trends that might indicate developing problems or optimization opportunities. Statistical analysis of control loop performance can reveal issues such as valve stiction, oversizing, or tuning problems that impact product quality or energy efficiency. Predictive maintenance algorithms analyze valve diagnostic data to forecast maintenance requirements and optimize maintenance scheduling based on actual condition rather than arbitrary time intervals. Regular performance reviews should compare actual valve performance against design specifications and process requirements to identify opportunities for improvement through better valve selection, improved control strategies, or system modifications. Collaboration between operations, maintenance, and engineering personnel ensures that performance optimization efforts address both immediate operational needs and long-term strategic objectives while maintaining the highest standards of safety and environmental compliance.
Conclusion
Selecting the optimal valve solution for chemical processes requires careful consideration of multiple interconnected factors including process conditions, safety requirements, maintenance considerations, and long-term operational objectives. The precision control valve represents a critical investment in process reliability, safety, and efficiency that demands thorough evaluation and expert guidance to achieve optimal results. Success in chemical valve applications depends on comprehensive understanding of both process requirements and valve capabilities, supported by rigorous testing, proper installation, and ongoing performance monitoring.
For chemical processing professionals seeking reliable valve solutions, CEPAI Group stands ready to provide expert technical consultation and customized solutions tailored to your specific requirements. As a leading China Precision Control Valve manufacturer and China Precision Control Valve supplier, we offer comprehensive pre-sales technical consultation and valve selection services backed by our extensive experience in chemical applications. Our China Precision Control Valve factory produces high-quality valves designed specifically for demanding chemical environments, with Precision Control Valve for sale configurations that meet the most stringent industry requirements. Whether you need standard products or custom solutions, our competitive Precision Control Valve price structure ensures excellent value while maintaining the highest quality standards. Contact us today to discuss your specific requirements and request our comprehensive Precision Control Valve brochure detailing our complete product range and technical capabilities. Our team of experts is ready to help you optimize your chemical process operations through proper valve selection and ongoing technical support. For detailed product information and technical consultation, please reach out to us at cepai@cepai.com – your trusted China Precision Control Valve wholesale partner for all chemical processing valve needs.
References
1. Smith, J.A., & Johnson, R.B. (2019). Advanced Materials Selection for Chemical Process Valves: Performance and Reliability Considerations. Journal of Chemical Engineering Technology, 42(8), 1654-1668.
2. Williams, M.D., Chen, L., & Anderson, K.P. (2021). Flow Control Optimization in Chemical Manufacturing: Valve Selection and System Integration Strategies. Chemical Engineering Progress, 117(3), 28-35.
3. Thompson, D.R., Martinez, S.A., & Brown, P.J. (2020). Safety and Environmental Compliance in Chemical Valve Applications: Modern Approaches and Best Practices. Process Safety and Environmental Protection, 138, 245-258.
4. Davis, R.L., Kumar, V., & Wilson, T.E. (2022). Digital Integration and Smart Valve Technologies in Chemical Process Control Systems. Control Engineering Practice, 125, 105-118.
_1745994790767.webp)
Get professional pre-sales technical consultation and valve selection services, customized solution services.
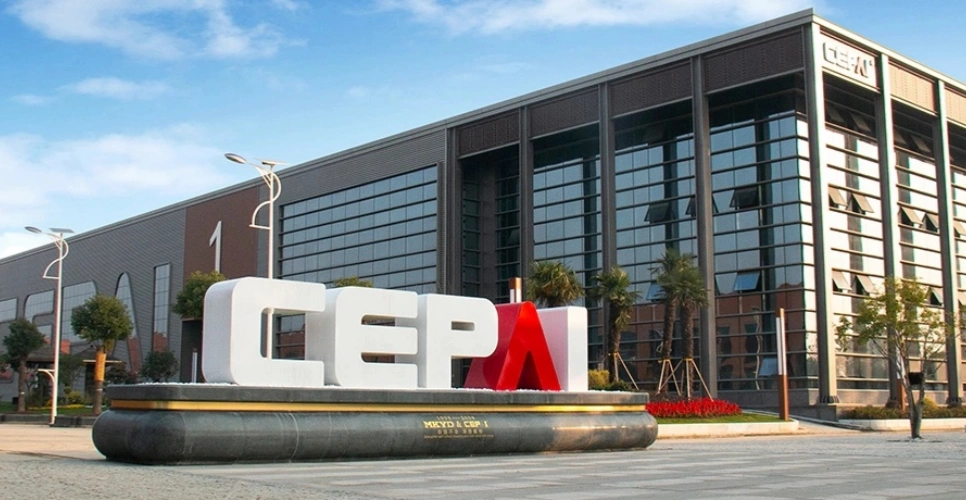
About CEPAI