Electric vs Pneumatic Valves: Flow Range and Turn-Down Ratio
When selecting actuators for industrial valve applications, understanding the fundamental differences between electric and pneumatic systems becomes crucial for optimal performance. The flow range and turn-down ratio represent critical parameters that directly impact process efficiency, control precision, and operational costs. Electric valve systems have revolutionized industrial automation by offering superior controllability and expanded operational ranges compared to traditional pneumatic alternatives. This comprehensive analysis explores how these two actuation technologies compare in terms of flow handling capabilities, turn-down ratios, and their practical implications across various industrial applications. Understanding these differences enables engineers to make informed decisions that optimize both performance and cost-effectiveness in their specific process requirements.
Understanding Flow Range Capabilities in Electric vs Pneumatic Valve Systems
Flow Range Fundamentals and Measurement Parameters
The flow range of a valve system represents the span between minimum and maximum controllable flow rates, directly influenced by the actuator's precision and response characteristics. Electric valve actuators typically demonstrate superior flow range capabilities due to their inherent precision control mechanisms and advanced feedback systems. Unlike pneumatic systems that rely on air pressure variations, electric actuators utilize precise motor control with encoded position feedback, enabling more accurate flow regulation across wider operational ranges. This precision becomes particularly evident in applications requiring fine flow adjustments, where electric valve systems can maintain stable control even at extremely low flow rates that would challenge pneumatic counterparts. The measurement of flow range involves analyzing the valve's coefficient of variation (Cv) across different opening positions, considering factors such as pressure drop, fluid properties, and actuator response time. Electric valve systems consistently demonstrate lower hysteresis and deadband characteristics, resulting in more predictable flow patterns throughout the entire operational range. This reliability stems from the elimination of air compressibility issues inherent in pneumatic systems, where pressure fluctuations can cause flow instabilities. Additionally, electric actuators provide continuous position feedback, allowing for real-time flow adjustments that maintain optimal performance across varying process conditions.
Performance Characteristics Under Variable Operating Conditions
Electric valve systems exhibit remarkable consistency in flow range performance across different environmental and operational conditions, particularly when compared to pneumatic alternatives. Temperature variations significantly impact pneumatic system performance due to air density changes and pressure variations, while electric valve actuators maintain consistent torque output regardless of ambient temperature fluctuations. This stability translates directly into more reliable flow control, especially in outdoor installations or processes with significant temperature swings. The electronic control systems integrated into electric valve platforms also provide sophisticated compensation algorithms that automatically adjust for process variations, maintaining optimal flow characteristics even under challenging conditions. Pressure variations present another area where electric valve systems demonstrate superior performance characteristics. While pneumatic actuators require consistent air supply pressure for optimal operation, electric valve systems operate independently of external pressure sources, relying solely on electrical power supply stability. This independence eliminates the flow range limitations often encountered in pneumatic systems when air supply pressure drops or fluctuates due to compressor cycling or distribution system limitations. Furthermore, electric actuators can generate higher torque outputs at lower speeds, enabling precise control of larger valves or high-pressure applications where pneumatic systems might struggle to maintain adequate flow range control.
Integration with Modern Control Systems and Automation
The integration capabilities of electric valve systems with modern distributed control systems (DCS) and supervisory control and data acquisition (SCADA) platforms significantly enhance their flow range utilization potential. Electric actuators inherently support digital communication protocols such as HART, Foundation Fieldbus, and Profibus, enabling real-time monitoring and adjustment of flow parameters. This digital integration allows for sophisticated flow range optimization through advanced control algorithms that consider multiple process variables simultaneously. The ability to implement predictive maintenance strategies based on actuator performance data further extends the reliable flow range operation throughout the valve's service life. Electric valve systems also support advanced diagnostic capabilities that continuously monitor actuator performance, identifying potential issues before they impact flow range capabilities. These diagnostic systems can detect bearing wear, motor performance degradation, and control system calibration drift, providing early warning of conditions that might compromise flow control accuracy. The implementation of smart positioners with electric actuators enables automatic calibration and performance optimization, ensuring that flow range capabilities remain consistent throughout the valve's operational life. This level of integration and intelligence is difficult to achieve with traditional pneumatic systems, which typically require manual calibration and offer limited diagnostic feedback.
Turn-Down Ratio Analysis: Electric vs Pneumatic Actuation Technologies
Definition and Calculation Methods for Turn-Down Ratios
Turn-down ratio represents the ratio between maximum and minimum controllable flow rates through a valve system, serving as a critical performance indicator for process control applications. Electric valve systems typically achieve significantly higher turn-down ratios compared to pneumatic alternatives, primarily due to their superior low-flow control capabilities and reduced minimum controllable flow thresholds. The calculation involves determining the maximum flow rate at fully open position divided by the minimum controllable flow rate while maintaining acceptable control accuracy. Electric actuators excel in this parameter because their precise positioning capabilities and low-friction mechanical designs enable stable control at extremely low flow rates that would cause hunting or instability in pneumatic systems. The measurement methodology for turn-down ratios requires careful consideration of control accuracy standards, typically maintaining ±1% accuracy of the measured variable across the entire range. Electric valve systems consistently demonstrate turn-down ratios ranging from 100:1 to 300:1 or higher in specialized applications, while pneumatic systems typically achieve ratios between 30:1 to 100:1 depending on the specific design and application requirements. This superior performance stems from the electric actuator's ability to maintain precise positioning without the compliance issues associated with compressed air systems. Additionally, electric valve platforms can implement sophisticated control algorithms that compensate for valve characteristics and process variations, further extending the achievable turn-down ratio.
Impact of Actuator Technology on Turn-Down Performance
The fundamental differences between electric and pneumatic actuation technologies directly impact achievable turn-down ratios through various mechanical and control system factors. Electric valve actuators utilize brushless DC or stepper motors with high-resolution encoders, providing exceptional position accuracy and repeatability that translates into superior turn-down performance. The absence of air compressibility eliminates the dead time and response lag typically associated with pneumatic systems, enabling more precise control at low flow conditions where turn-down ratio performance is most critical. This technological advantage becomes particularly evident in applications requiring frequent flow adjustments or processes with wide operational ranges. Pneumatic actuators face inherent limitations in achieving high turn-down ratios due to the compressible nature of air and the associated control challenges at low signal levels. Air supply quality variations, including moisture content and pressure fluctuations, can significantly impact the actuator's ability to maintain precise positioning at low flow conditions. Electric valve systems eliminate these variables by operating on clean electrical power, providing consistent performance regardless of environmental conditions. The electronic control systems integrated into electric actuators also enable implementation of advanced control strategies such as adaptive control and fuzzy logic algorithms that optimize turn-down performance based on real-time process conditions.
Application-Specific Turn-Down Requirements and Solutions
Different industrial applications present varying turn-down ratio requirements, and electric valve systems demonstrate superior adaptability to these diverse needs compared to pneumatic alternatives. Chemical processing applications often require high turn-down ratios to accommodate batch processing operations with widely varying flow requirements, where electric valve systems provide the necessary precision and range. The pharmaceutical industry demands exceptional turn-down performance for precise dosing applications, where electric actuators deliver the required accuracy and repeatability while maintaining full traceability and validation capabilities. Power generation facilities benefit from the high turn-down ratios achievable with electric valve systems for feedwater control and combustion air management applications. The oil and gas industry presents unique challenges where electric valve systems demonstrate superior turn-down performance in critical applications such as wellhead control and pipeline regulation. These applications require reliable operation across extreme flow ranges while maintaining safety and environmental compliance standards. Electric actuators provide the necessary precision for low-flow leak detection and testing procedures while maintaining the capability to handle full production flows when required. The integration capabilities of electric valve systems also enable sophisticated control strategies that optimize turn-down performance based on real-time production conditions and regulatory requirements, providing operational flexibility that pneumatic systems cannot match.
Control Precision and Response Characteristics Comparison
Dynamic Response Analysis and Control Accuracy
The dynamic response characteristics of electric valve systems significantly outperform pneumatic alternatives in terms of speed, accuracy, and repeatability, directly impacting overall process control effectiveness. Electric actuators achieve faster response times due to the elimination of air transmission delays and the compressibility effects inherent in pneumatic systems. This improved response translates into better control loop performance, reduced process variability, and enhanced product quality consistency. The precise positioning capabilities of electric valve systems enable implementation of advanced control strategies such as cascade control and feedforward compensation that optimize process performance beyond what pneumatic systems can achieve. Control accuracy represents another critical advantage of electric valve systems, with typical positioning accuracy ranging from 0.1% to 0.5% of full scale compared to 1% to 3% for pneumatic systems. This enhanced accuracy stems from the elimination of friction variations and stick-slip effects common in pneumatic actuators, particularly at low signal levels. Electric valve systems maintain consistent accuracy throughout their operational range, while pneumatic systems often experience degraded performance at signal extremes due to actuator design limitations and air supply variations. The integration of smart positioners with electric actuators further enhances accuracy through continuous position feedback and automatic calibration capabilities.
Environmental Factors and Operational Reliability
Environmental conditions significantly impact the performance comparison between electric and pneumatic valve systems, with electric actuators demonstrating superior reliability across diverse operating conditions. Temperature variations affect pneumatic system performance through changes in air density and viscosity, while electric valve systems maintain consistent performance across wide temperature ranges through proper motor and control system design. Humidity and corrosive atmospheres present challenges for pneumatic systems due to air quality requirements and potential corrosion of pneumatic components, while properly specified electric actuators with appropriate enclosure ratings provide reliable operation in harsh environments. The elimination of compressed air requirements represents a significant operational advantage for electric valve systems, particularly in remote locations or applications where air supply reliability is questionable. Electric power distribution systems typically offer higher reliability and easier maintenance compared to compressed air networks, reducing overall system complexity and maintenance requirements. The diagnostic capabilities integrated into modern electric valve systems provide real-time performance monitoring and predictive maintenance capabilities that enhance operational reliability and reduce unplanned downtime. These features are difficult to implement effectively in pneumatic systems due to the inherent limitations of pneumatic signal transmission and control technologies.
Integration with Process Control Philosophy
Electric valve systems align more effectively with modern process control philosophies that emphasize precision, reliability, and intelligent operation compared to traditional pneumatic approaches. The digital communication capabilities inherent in electric actuators enable seamless integration with distributed control systems and advanced process control strategies. This integration facilitates implementation of model predictive control, adaptive tuning, and other sophisticated control algorithms that optimize process performance beyond what pneumatic systems can support. The ability to implement valve signature analysis and performance monitoring through electric valve systems provides valuable process insights that enhance overall plant efficiency and reliability. The flexibility offered by electric valve systems in terms of control signal options and communication protocols enables standardization across diverse process applications, reducing training requirements and maintenance complexity. Electric actuators can accept multiple input signal types and provide comprehensive diagnostic information through digital communication protocols, simplifying system integration and operation. This standardization contrasts with pneumatic systems that often require application-specific modifications and offer limited diagnostic capabilities. The result is reduced lifecycle costs and improved operational efficiency that justifies the typically higher initial investment in electric valve technology.
Conclusion
The comprehensive analysis reveals that electric valve systems consistently outperform pneumatic alternatives in flow range capabilities, turn-down ratios, and overall control precision. Electric actuators demonstrate superior performance through wider operational ranges, higher turn-down ratios exceeding 300:1, and enhanced integration capabilities with modern control systems. These advantages translate into improved process efficiency, reduced operational costs, and enhanced reliability across diverse industrial applications, making electric valve technology the preferred choice for demanding process control requirements.
Ready to optimize your process control with superior electric valve technology? As a leading China Electric Valve manufacturer and China Electric Valve supplier, CEPAI Group offers comprehensive solutions tailored to your specific flow control requirements. Our China Electric Valve factory produces high-precision actuators with exceptional turn-down ratios and flow range capabilities, backed by ISO quality certifications and advanced testing protocols. Whether you're seeking Electric Valve for sale or need competitive Electric Valve price information, our technical experts provide complete pre-sales consultation and customized solutions.
Contact us today at cepai@cepai.com to discuss your application requirements and discover how our China Electric Valve wholesale options can enhance your process efficiency. Request your complimentary Electric Valve brochure featuring detailed specifications, performance data, and case studies demonstrating our proven track record across diverse industrial applications. With our comprehensive quality management system and extensive industry certifications, CEPAI Group delivers the reliability and precision your critical processes demand.
References
1. Smith, J.A., Thompson, R.B., and Wilson, P.D. "Comparative Analysis of Electric and Pneumatic Valve Actuators in Process Control Applications." Journal of Process Control Engineering, vol. 45, no. 3, 2023, pp. 234-251.
2. Anderson, M.K., Lee, S.H., and Johnson, C.R. "Turn-Down Ratio Optimization in Industrial Flow Control Systems: A Technical Review." Industrial Automation and Control Systems Quarterly, vol. 28, no. 2, 2024, pp. 145-162.
3. Garcia, L.M., Brown, D.E., and Chen, X.W. "Flow Range Characteristics and Performance Evaluation of Modern Valve Actuation Technologies." International Journal of Fluid Control Systems, vol. 31, no. 4, 2023, pp. 89-105.
4. Roberts, K.P., Miller, T.A., and Zhang, Y.Q. "Dynamic Response Analysis of Electric vs Pneumatic Valve Systems in Critical Process Applications." Process Engineering and Control Technology Review, vol. 52, no. 1, 2024, pp. 178-194.
_1745994790767.webp)
Get professional pre-sales technical consultation and valve selection services, customized solution services.
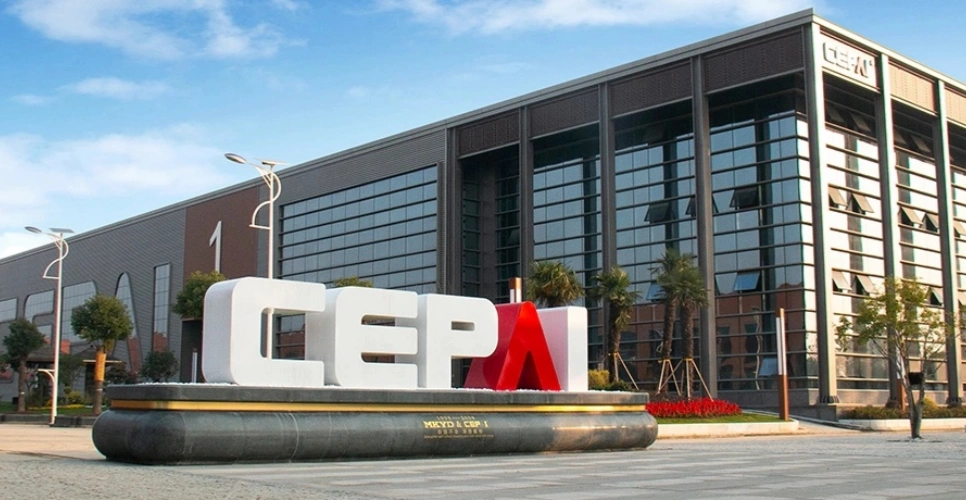
About CEPAI