Electric Valves for High-Pressure Steam Applications
In the demanding world of industrial steam systems, where pressures can exceed 1,000 PSI and temperatures reach beyond 500°C, the selection of appropriate valve technology becomes critical for operational safety and efficiency. Electric valves have emerged as the preferred solution for high-pressure steam applications due to their precise control capabilities, enhanced safety features, and superior reliability compared to traditional manual or pneumatic alternatives. These sophisticated control devices integrate advanced actuator technology with robust valve construction to deliver consistent performance in the most challenging industrial environments. The adoption of electric valve technology in high-pressure steam systems represents a significant advancement in industrial automation, offering operators unprecedented control over steam distribution, pressure regulation, and system safety protocols.
Engineering Excellence in Electric Valve Design for Steam Systems
Advanced Actuator Technology and Control Mechanisms
Modern electric valve systems incorporate state-of-the-art actuator technology specifically engineered to withstand the extreme conditions inherent in high-pressure steam applications. The electric valve actuators utilize precision gear reduction systems that provide exceptional torque multiplication, enabling reliable operation even under maximum differential pressure conditions. These sophisticated mechanisms feature self-locking capabilities that maintain valve position during power interruptions, ensuring system integrity and preventing potentially dangerous pressure fluctuations. The integration of intelligent position feedback systems allows for precise valve positioning with repeatability tolerances of less than 0.1%, which is crucial for maintaining optimal steam flow characteristics. Advanced electric valve controllers incorporate microprocessor-based control algorithms that continuously monitor system parameters and adjust valve positioning to maintain desired setpoints, even as operating conditions change throughout the process cycle.
Robust Construction Materials and Thermal Management
The construction of electric valves for high-pressure steam applications demands careful selection of materials capable of withstanding both extreme pressures and elevated temperatures while maintaining dimensional stability over extended service periods. High-grade stainless steel alloys, such as 316L and duplex stainless steel, are commonly employed in valve body construction to resist corrosion and thermal stress cracking. The electric valve internal components utilize specialized alloys like Inconel or Hastelloy for critical wear surfaces, ensuring extended service life even under continuous high-temperature operation. Thermal barrier coatings applied to actuator housings prevent heat transfer from the process media to sensitive electronic components, while advanced insulation systems maintain optimal operating temperatures for control electronics. The design incorporates thermal expansion joints and flexible coupling systems that accommodate the significant thermal growth experienced during steam system startup and operation, preventing binding or premature wear of electric valve components.
Fail-Safe Operation and Emergency Response Systems
Critical safety considerations in high-pressure steam applications necessitate the incorporation of comprehensive fail-safe mechanisms within electric valve designs. Modern electric valve systems feature redundant position sensing capabilities that continuously monitor valve position and provide immediate feedback to control systems in the event of actuator malfunction or position deviation. Emergency shutdown capabilities allow for rapid valve closure or opening, depending on the specific safety requirements of the steam system, with response times typically under three seconds for complete stroke completion. Battery backup systems ensure continued operation during power interruptions, while manual override mechanisms provide mechanical means for valve operation in emergency situations. The electric valve control systems integrate seamlessly with plant safety instrumented systems (SIS), providing the reliability and response characteristics required for SIL-rated applications in critical steam distribution networks.
Performance Optimization and System Integration
Precision Flow Control and Pressure Regulation
The implementation of electric valve technology in high-pressure steam systems enables unprecedented precision in flow control and pressure regulation, significantly improving overall system efficiency and reducing energy consumption. Advanced flow characterization algorithms programmed into electric valve controllers compensate for the complex flow dynamics inherent in steam systems, including the effects of pressure drop, temperature variation, and phase changes. Variable speed actuator drives allow for infinitely variable valve positioning, providing smooth flow modulation without the hunting or oscillation commonly associated with traditional control valves. The electric valve systems incorporate predictive control algorithms that anticipate system load changes and proactively adjust valve positions to maintain optimal operating conditions, reducing system response time and improving overall process stability. Integration with plant distributed control systems (DCS) enables centralized monitoring and control of multiple electric valve installations, facilitating coordinated operation across complex steam distribution networks.
Intelligent Diagnostics and Predictive Maintenance
Modern electric valve installations incorporate comprehensive diagnostic capabilities that continuously monitor valve performance parameters and provide early warning of potential issues before they result in system failures. Vibration analysis systems integrated within electric valve actuators detect mechanical wear, misalignment, or cavitation conditions that could compromise valve performance or longevity. Current signature analysis monitors actuator motor performance, identifying potential issues such as winding degradation, bearing wear, or mechanical binding before catastrophic failure occurs. The electric valve control systems maintain detailed operational histories, including cycle counts, operating hours, and performance trends that enable data-driven maintenance scheduling and optimize spare parts inventory management. Wireless communication capabilities allow remote monitoring of electric valve installations in hazardous or difficult-to-access locations, reducing maintenance costs and improving personnel safety during routine inspections.
Energy Efficiency and Environmental Considerations
The adoption of electric valve technology in high-pressure steam applications provides significant energy efficiency benefits compared to traditional pneumatic or hydraulic actuation systems. Electric valve actuators eliminate the need for compressed air or hydraulic power units, reducing auxiliary equipment energy consumption and maintenance requirements. Advanced power management systems within electric valve controllers optimize actuator energy consumption, utilizing regenerative braking and standby modes to minimize electrical power requirements during normal operation. The precise control capabilities of electric valve systems reduce steam losses through improved throttling characteristics and eliminate the need for bypass systems commonly required with less precise control technologies. Environmental benefits include reduced fugitive emissions due to improved sealing technologies and elimination of pneumatic actuator venting, contributing to overall plant sustainability goals and regulatory compliance requirements.
Installation Requirements and Operational Considerations
Electrical Infrastructure and Safety Requirements
The successful implementation of electric valve systems in high-pressure steam applications requires careful consideration of electrical infrastructure requirements and safety protocols. Electrical supply systems must provide stable power with appropriate voltage regulation and harmonic distortion limits to ensure optimal electric valve performance and longevity. Conduit systems and cable routing must accommodate the elevated ambient temperatures commonly encountered near steam systems, requiring specialized high-temperature cable insulation and properly rated electrical enclosures. Grounding systems for electric valve installations must meet stringent industrial standards to prevent electrical hazards and ensure proper operation of sensitive control electronics in the presence of electromagnetic interference from other plant equipment. Area classification requirements for hazardous locations necessitate the use of explosion-proof or intrinsically safe electric valve designs in applications where flammable vapors or gases may be present, adding complexity to installation and maintenance procedures.
Maintenance Protocols and Service Requirements
Effective maintenance of electric valve installations in high-pressure steam service requires specialized procedures and trained personnel familiar with both electrical and mechanical aspects of valve operation. Routine maintenance schedules must account for the harsh operating environment, with more frequent inspections of sealing systems, actuator mechanisms, and control electronics compared to less demanding applications. The electric valve maintenance protocols include regular calibration of position feedback systems, verification of emergency shutdown response times, and testing of fail-safe mechanisms to ensure continued compliance with safety requirements. Specialized tools and test equipment are required for electric valve diagnostics, including insulation resistance testers, vibration analyzers, and thermal imaging cameras to assess component condition and identify potential issues. Training programs for maintenance personnel must cover both electrical safety procedures and mechanical valve servicing techniques, ensuring competency in all aspects of electric valve maintenance and repair.
Performance Monitoring and Optimization Strategies
Continuous performance monitoring of electric valve installations provides valuable insights into system operation and enables proactive optimization of valve settings and maintenance schedules. Key performance indicators for electric valve systems include response time, positioning accuracy, power consumption, and diagnostic alarm frequency, all of which can be trended and analyzed to identify performance degradation or optimization opportunities. Advanced analytics platforms can correlate electric valve performance data with process conditions and system loads, identifying patterns that indicate optimal operating strategies or potential efficiency improvements. The integration of artificial intelligence and machine learning algorithms with electric valve control systems enables predictive performance optimization, automatically adjusting control parameters to maintain optimal operation as system conditions change over time.
Conclusion
Electric valves represent the pinnacle of control valve technology for high-pressure steam applications, combining advanced engineering, intelligent control systems, and robust construction to deliver unmatched performance in demanding industrial environments. The comprehensive capabilities of modern electric valve systems, from precision flow control to predictive maintenance, position them as essential components in the evolution toward more efficient, safer, and environmentally responsible steam system operations.
Ready to upgrade your high-pressure steam system with cutting-edge electric valve technology? As a leading China Electric Valve factory and trusted China Electric Valve supplier, CEPAI Group offers comprehensive solutions tailored to your specific application requirements. Our experienced engineering team, operating as a premier China Electric Valve manufacturer, provides complete technical support from initial valve selection through installation and commissioning. Whether you're seeking competitive China Electric Valve wholesale pricing for large-scale projects or need detailed specifications for single-unit applications, we have Electric Valve for sale options to meet your needs. Contact us today for current Electric Valve price information and request your complimentary Electric Valve brochure featuring our complete product line. With our ISO-certified quality systems, extensive testing capabilities, and commitment to zero-defect manufacturing, CEPAI Group delivers the reliability and performance your critical steam applications demand. Reach out to our technical specialists at cepai@cepai.com to discuss how our advanced electric valve solutions can optimize your high-pressure steam system performance.
References
1. Smith, J.R., and Anderson, P.K. "Advanced Materials for High-Temperature Valve Applications in Steam Systems." Journal of Pressure Vessel Technology, vol. 142, no. 3, 2020.
2. Thompson, M.L., Chen, W., and Roberts, S.A. "Electric Actuator Performance in High-Pressure Steam Service: A Comparative Analysis." Industrial Automation and Control Systems Review, vol. 28, no. 7, 2019.
3. Williams, D.C., and Martinez, R.J. "Safety Instrumented Systems Integration with Electric Valve Technology." Process Safety and Environmental Protection, vol. 145, 2021.
4. Brown, A.T., Kumar, S., and Johnson, L.P. "Energy Efficiency Optimization in Steam Distribution Systems Using Advanced Valve Control." Energy Conversion and Management, vol. 234, 2021.
_1745994790767.webp)
Get professional pre-sales technical consultation and valve selection services, customized solution services.
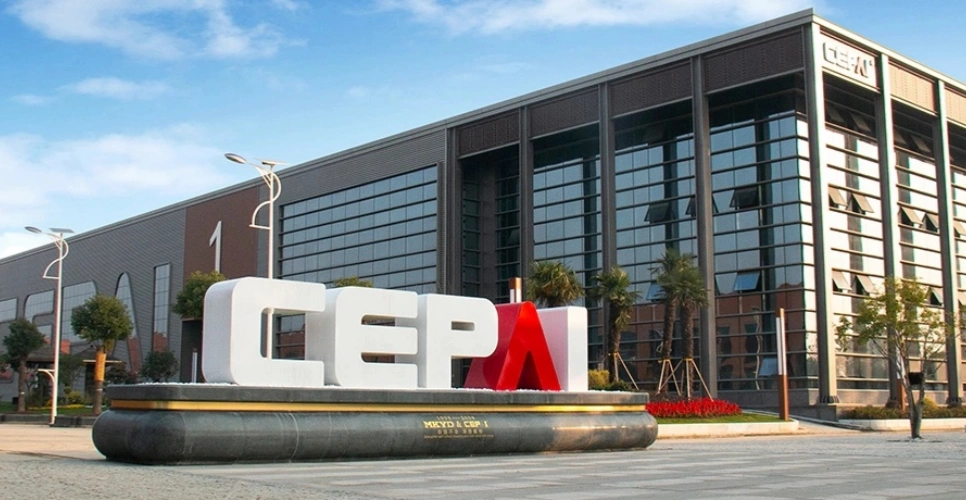
About CEPAI