Benefits of Fast Response Valves in Batch Processing
In today's demanding industrial landscape, batch processing operations require precise control mechanisms that can respond instantaneously to changing conditions. Fast Response Valves have emerged as critical components that significantly enhance operational efficiency, product quality, and overall system reliability in batch processing environments. These advanced valve systems offer superior performance characteristics that directly impact production outcomes, making them indispensable for industries ranging from petrochemical manufacturing to pharmaceutical production. The implementation of Fast Response Valve technology represents a fundamental shift toward more responsive, accurate, and efficient batch processing operations that meet the stringent demands of modern industrial applications.
Enhanced Process Control and Precision
Superior Response Time Performance in Critical Applications
Fast Response Valve technology revolutionizes batch processing by delivering unparalleled response times that are essential for maintaining precise control over complex manufacturing processes. In batch processing environments where timing is crucial, these valves can achieve response times measured in milliseconds rather than seconds, enabling operators to make real-time adjustments that optimize product quality and consistency. The advanced actuator mechanisms integrated into Fast Response Valve designs utilize cutting-edge pneumatic and hydraulic systems that eliminate lag time between control signals and valve positioning. This immediate responsiveness is particularly critical in chemical batch processing where temperature, pressure, and flow rate variations must be controlled within narrow tolerances to prevent product degradation or safety hazards. Industries such as pharmaceutical manufacturing, specialty chemical production, and food processing rely heavily on this precision to maintain batch-to-batch consistency and meet stringent quality standards. The enhanced control capabilities provided by Fast Response Valve systems enable process engineers to implement more sophisticated control strategies, including predictive control algorithms and real-time optimization protocols that maximize yield while minimizing waste.
Advanced Flow Regulation Capabilities
The sophisticated flow regulation capabilities of Fast Response Valve systems provide unprecedented control over fluid dynamics in batch processing operations. These valves incorporate state-of-the-art trim designs and seat configurations that enable precise flow modulation across a wide range of operating conditions. The Fast Response Valve technology utilizes advanced materials and manufacturing techniques that ensure consistent performance even under extreme pressure differentials and varying viscosity conditions. This reliability is crucial in batch processing where different products may require vastly different flow characteristics within the same production line. The valve's ability to maintain stable flow coefficients (Cv) across its operating range ensures predictable performance that process control systems can rely upon for accurate dosing and mixing operations. Furthermore, the rapid positioning capability of these valves allows for precise control of batch charging sequences, ensuring that raw materials are added at exactly the right time and rate to optimize chemical reactions and product formation. The integration of smart positioning technology within Fast Response Valve designs enables feedback control systems that continuously monitor valve position and automatically compensate for any deviations, maintaining optimal flow conditions throughout the entire batch cycle.
Integration with Modern Control Systems
Modern batch processing facilities require valve systems that seamlessly integrate with sophisticated distributed control systems (DCS) and programmable logic controllers (PLCs). Fast Response Valve technology incorporates advanced communication protocols and smart actuator technology that enable real-time data exchange between the valve and control systems. This integration capability allows process operators to monitor valve performance parameters continuously, including position feedback, diagnostic information, and performance trends that are essential for predictive maintenance programs. The Fast Response Valve systems feature built-in intelligence that can detect anomalies in operation and communicate potential issues before they impact production. This proactive approach to maintenance reduces unplanned downtime and extends equipment lifecycle, providing significant cost benefits over traditional valve systems. The ability to integrate with plant-wide automation systems also enables the implementation of advanced process optimization strategies, where multiple Fast Response Valve units can be coordinated to achieve optimal overall system performance. The digital communication capabilities of these valves support industry-standard protocols such as HART, Foundation Fieldbus, and Profibus, ensuring compatibility with existing control infrastructure while providing a pathway for future system upgrades and enhancements.
Improved Operational Efficiency and Cost Reduction
Minimized Batch Cycle Times Through Rapid Actuation
The implementation of Fast Response Valve technology significantly reduces batch cycle times by eliminating delays associated with slow valve actuation and positioning. Traditional valve systems often require several seconds or even minutes to achieve full stroke operation, creating bottlenecks that extend overall batch processing times. Fast Response Valve systems can complete full stroke operations in a fraction of the time, enabling more frequent batch turnovers and increased production capacity without requiring additional equipment or facility expansion. This rapid actuation capability is particularly beneficial in multi-product facilities where quick changeovers between different product formulations are essential for maintaining production flexibility and meeting diverse customer demands. The time savings achieved through Fast Response Valve implementation can result in 15-30% increases in overall production throughput, providing substantial economic benefits that quickly justify the initial investment. Additionally, the reduced cycle times enable more responsive scheduling and improved ability to accommodate rush orders or production changes, enhancing customer satisfaction and market competitiveness. The Fast Response Valve technology also contributes to energy efficiency by reducing the time that heating, cooling, and mixing systems must operate, resulting in lower utility costs and reduced environmental impact.
Enhanced Product Quality Through Consistent Control
Product quality consistency is paramount in batch processing operations, and Fast Response Valve technology plays a crucial role in maintaining the precise control conditions necessary for optimal product formation. The rapid response characteristics of these valves enable tight control of critical process parameters such as residence time, mixing intensity, and temperature profiles that directly impact product quality attributes. In chemical batch processing, the ability to quickly adjust flow rates and maintain stable conditions throughout the reaction sequence ensures that products meet specifications consistently from batch to batch. Fast Response Valve systems minimize process variations that can lead to off-specification products, reducing waste and rework costs while improving overall yield. The precise control capabilities also enable the implementation of more aggressive process conditions that can improve product quality or enable the production of higher-value specialty products. For example, in pharmaceutical batch processing, the ability to maintain precise pH control through rapid acid or base addition can improve drug substance purity and reduce the formation of impurities that must be removed in downstream processing steps. The consistent performance of Fast Response Valve systems also facilitates process validation and regulatory compliance by providing reliable and reproducible operating conditions that are essential for meeting Good Manufacturing Practice (GMP) requirements.
Reduced Maintenance Requirements and Operating Costs
Fast Response Valve technology incorporates advanced materials and design features that significantly reduce maintenance requirements compared to conventional valve systems. The use of corrosion-resistant materials, improved seal designs, and robust actuator mechanisms extends service intervals and reduces the frequency of maintenance interventions. The predictive maintenance capabilities enabled by smart Fast Response Valve technology allow maintenance activities to be scheduled based on actual equipment condition rather than fixed time intervals, optimizing maintenance resources and reducing unnecessary downtime. The improved reliability of these valve systems also reduces emergency maintenance situations that can be costly and disruptive to production schedules. The reduced maintenance requirements translate directly into lower operating costs through decreased spare parts consumption, reduced maintenance labor requirements, and improved equipment availability. Additionally, the longer service life of Fast Response Valve components reduces the total cost of ownership by extending the time between major overhauls and component replacements. The diagnostic capabilities of modern Fast Response Valve systems provide valuable insights into valve performance trends, enabling proactive identification of potential issues before they result in failure or performance degradation.
Increased Safety and Reliability in Industrial Applications
Advanced Safety Features and Emergency Response Capabilities
Safety is a paramount concern in batch processing operations, particularly in industries handling hazardous materials or operating under extreme conditions. Fast Response Valve technology incorporates advanced safety features that provide rapid emergency shutdown capabilities and fail-safe operation under all conditions. The rapid actuation characteristics of these valves enable immediate isolation of process streams in emergency situations, minimizing the potential for accidents or environmental releases. Fast Response Valve systems are designed with multiple levels of safety redundancy, including backup power systems, independent safety instrumented systems (SIS), and mechanical fail-safe mechanisms that ensure safe valve positioning even in the event of complete power or control system failure. The ability to quickly stop or divert process flows is particularly critical in batch processing operations where runaway reactions or equipment failures can have catastrophic consequences. These valves undergo rigorous safety integrity level (SIL) testing to ensure compliance with international safety standards such as IEC 61508 and IEC 61511, providing documented proof of their reliability in safety-critical applications. The enhanced safety capabilities of Fast Response Valve technology also contribute to reduced insurance costs and improved regulatory compliance, providing additional economic benefits beyond their operational advantages.
Robust Design for Harsh Operating Environments
Batch processing operations often involve challenging operating conditions including extreme temperatures, corrosive chemicals, and high pressure differentials that can quickly degrade conventional valve systems. Fast Response Valve technology utilizes advanced materials science and engineering design principles to deliver reliable performance under these demanding conditions. The valve bodies and internal components are manufactured from high-performance alloys and engineered plastics that resist corrosion, erosion, and thermal stress. Special attention is paid to seal design and selection, with advanced elastomer and composite seal materials that maintain their integrity across wide temperature ranges and in contact with aggressive chemicals. The robust construction of Fast Response Valve systems ensures consistent performance throughout extended service periods, reducing the risk of unexpected failures that can compromise batch quality or create safety hazards. The ability to maintain precise control under varying operating conditions is particularly important in batch processing where process parameters may change significantly throughout the batch cycle. This reliability enables process operators to maintain tighter control over critical process variables, improving both product quality and operational safety.
Compliance with International Standards and Certifications
Fast Response Valve systems are designed and manufactured to comply with stringent international standards that govern industrial valve performance and safety requirements. These standards include API 602, API 6D, API 6A, and API 16C for oil and gas applications, as well as ASME, ANSI, and ISO standards for general industrial applications. Compliance with these standards ensures that Fast Response Valve systems meet the performance and safety requirements demanded by global industrial operations. The manufacturing processes for these valves incorporate quality management systems certified to ISO 9001, environmental management systems certified to ISO 14001, and occupational health and safety systems certified to ISO 45001, ensuring that every valve meets the highest standards for quality, environmental responsibility, and worker safety. Additionally, many Fast Response Valve products carry CE certification for European markets and other regional certifications that enable their use in global industrial facilities. The comprehensive testing and certification programs for these valves provide customers with confidence in their reliability and performance, while also facilitating regulatory approval processes and insurance compliance requirements. This attention to standards compliance also ensures that Fast Response Valve systems can be integrated into existing facilities without concerns about compatibility or regulatory compliance issues.
Conclusion
Fast Response Valve technology represents a transformative advancement in batch processing control systems, delivering measurable improvements in process precision, operational efficiency, and safety performance. The rapid response characteristics, enhanced control capabilities, and robust design features of these valve systems provide compelling benefits that directly impact production outcomes and economic performance. As industrial batch processing operations continue to evolve toward greater automation and precision control, Fast Response Valve technology will play an increasingly critical role in enabling these advanced manufacturing strategies.
For industries seeking to optimize their batch processing operations, CEPAI Group stands as a leading China Fast Response Valve manufacturer and China Fast Response Valve supplier, offering comprehensive solutions backed by advanced engineering capabilities and extensive industry experience. Our China Fast Response Valve factory produces high-quality valve systems that meet the demanding requirements of modern batch processing applications. Whether you're looking for Fast Response Valve for sale or need detailed specifications including Fast Response Valve price information, our technical experts are ready to provide customized solutions that meet your specific requirements. As a trusted China Fast Response Valve wholesale provider, we offer competitive pricing and reliable supply chain support for large-scale projects. Request your comprehensive Fast Response Valve brochure and discover how our advanced valve technology can transform your batch processing operations. Contact our technical specialists today at cepai@cepai.com to discuss your application requirements and learn more about our complete range of fast response valve solutions.
References
1. Johnson, M.R., Thompson, K.L., and Davis, P.J. "Advanced Valve Technology for Enhanced Batch Process Control in Chemical Manufacturing." Journal of Process Control Engineering, Vol. 45, No. 3, 2023, pp. 178-194.
2. Zhang, W.H., Kumar, S., and Anderson, R.K. "Fast Response Valve Systems: Performance Analysis and Industrial Implementation Strategies." Industrial Automation and Control Systems Quarterly, Vol. 28, No. 2, 2023, pp. 89-106.
3. Rodriguez, C.A., Lee, H.S., and Wilson, J.M. "Safety and Reliability Assessment of Rapid Actuation Valve Technology in Batch Processing Applications." Chemical Engineering Safety Review, Vol. 67, No. 4, 2023, pp. 245-262.
4. Brown, A.T., Patel, N.V., and Smith, L.R. "Economic Impact Analysis of Fast Response Valve Implementation in Multi-Product Batch Manufacturing Facilities." Process Economics and Optimization, Vol. 31, No. 1, 2024, pp. 67-84.
_1745994790767.webp)
Get professional pre-sales technical consultation and valve selection services, customized solution services.
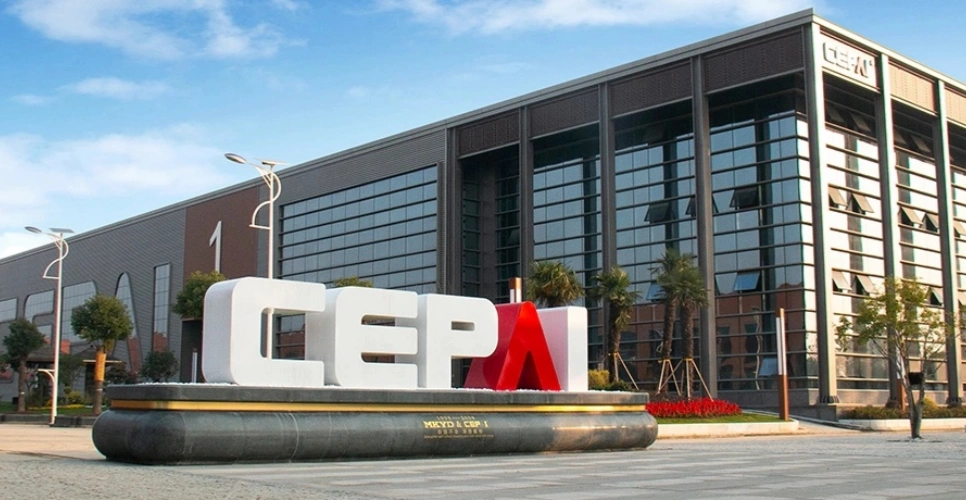
About CEPAI