Top Features to Look for in a Reliable Valve System
In today's industrial landscape, selecting the right valve system is crucial for maintaining operational efficiency, safety, and cost-effectiveness across various applications. When evaluating valve systems for critical industrial processes, understanding the key features that distinguish reliable solutions from substandard alternatives can save organizations significant time, money, and potential safety hazards. A comprehensive approach to valve selection requires careful consideration of multiple technical and operational factors. The right Control Valve system must demonstrate exceptional performance characteristics, incorporate advanced technological features, and provide long-term reliability that meets stringent industry standards while delivering consistent operational excellence throughout its service life.
Essential Technical Specifications and Performance Criteria
Pressure and Temperature Ratings for Industrial Applications
The foundation of any reliable valve system begins with its ability to withstand the specific pressure and temperature conditions of its intended application. Modern Control Valve systems must be engineered to handle extreme operating conditions while maintaining structural integrity and performance consistency. Industrial facilities often operate under demanding conditions where pressure ratings can exceed 10,000 PSI, and temperature ranges may span from cryogenic applications at -196°C to high-temperature processes reaching 650°C or higher. The valve body materials, including stainless steel, carbon steel, and specialized alloys, must be carefully selected based on the specific operating environment. Pressure-temperature ratings directly impact the valve's longevity and safety performance, making this specification critical for applications in petrochemical plants, power generation facilities, and offshore drilling operations. Additionally, the valve's ability to maintain its rated performance throughout its operational life cycle, including considerations for pressure cycling, thermal cycling, and potential system upsets, represents a fundamental aspect of reliable valve design.
Flow Characteristics and Cv Values
Understanding flow characteristics and coefficient of flow (Cv) values is essential for optimal Control Valve performance and system integration. The Cv value represents the flow capacity of a valve and indicates how many gallons per minute of water will flow through the valve at a pressure drop of one PSI. Reliable valve systems provide accurate flow characterization data, including inherent flow characteristics such as linear, equal percentage, and quick opening profiles. These characteristics determine how the valve's flow capacity changes relative to its stroke position, directly impacting process control accuracy and system stability. Modern valve systems often incorporate computational fluid dynamics (CFD) analysis during design phases to optimize internal flow paths, minimize pressure losses, and reduce cavitation potential. The relationship between valve position and flow rate must remain predictable and repeatable throughout the valve's operational life, ensuring consistent process control performance. Furthermore, the valve's rangeability, which represents the ratio between maximum and minimum controllable flow rates, significantly impacts the valve's ability to provide precise control across varying operational demands.
Material Composition and Corrosion Resistance
The selection of appropriate materials for valve construction directly influences long-term reliability, maintenance requirements, and overall system performance. High-quality Control Valve systems utilize materials specifically engineered to resist corrosion, erosion, and chemical degradation in their intended service environment. Stainless steel grades such as 316L, duplex stainless steels, and super duplex alloys provide excellent corrosion resistance for aggressive chemical applications, while specialized coatings and treatments can further enhance material performance. The valve's internal components, including seats, discs, and stems, require materials that maintain their mechanical properties and dimensional stability under repeated thermal cycling and mechanical stress. Advanced material selection also considers factors such as galvanic compatibility between dissimilar metals, stress corrosion cracking resistance, and the potential for hydrogen embrittlement in specific applications. Additionally, the manufacturing processes used to fabricate these components, including heat treatment, surface finishing, and quality control procedures, significantly impact the final product's reliability and performance characteristics.
Advanced Control and Automation Features
Smart Valve Technology and Digital Integration
The integration of smart technology and digital capabilities represents a significant advancement in modern Control Valve design and functionality. Intelligent valve systems incorporate embedded sensors, microprocessors, and communication protocols that enable real-time monitoring, diagnostics, and predictive maintenance capabilities. These systems can continuously monitor valve position, actuator performance, process conditions, and internal component wear patterns, providing valuable data for optimizing system performance and scheduling maintenance activities. Digital communication protocols such as HART, Foundation Fieldbus, and Profibus enable seamless integration with distributed control systems (DCS) and plant asset management systems. Smart valves can perform self-diagnostic routines that detect potential issues before they result in system failures, including partial stroke testing, signature analysis, and performance monitoring. The ability to remotely configure valve parameters, update control algorithms, and access historical performance data significantly reduces maintenance costs and improves operational efficiency. Furthermore, these advanced systems can adapt their control strategies based on changing process conditions, ensuring optimal performance across varying operational scenarios.
Precision Control Algorithms and Response Time
Modern Control Valve systems incorporate sophisticated control algorithms designed to provide precise, stable, and responsive process control across diverse operating conditions. Advanced control strategies such as PID tuning optimization, adaptive control, and model predictive control enhance the valve's ability to maintain setpoint accuracy while minimizing process variability. The valve's response time, including both opening and closing characteristics, must be carefully matched to the process requirements to ensure system stability and optimal control performance. Digital valve controllers often feature multiple control modes, including cascade control, split-range operation, and fail-safe positioning, providing flexibility for complex process control applications. The integration of advanced filtering algorithms helps eliminate the effects of measurement noise and process disturbances, resulting in smoother control action and reduced wear on valve components. Additionally, the valve's ability to provide consistent performance across its full operating range, including tight shutoff capabilities and precise throttling control, represents a critical aspect of reliable valve system design.
Actuator Performance and Reliability Features
The actuator system represents a critical component of any reliable Control Valve assembly, directly influencing the valve's positioning accuracy, response characteristics, and overall reliability. Modern actuator designs incorporate advanced materials, precision manufacturing techniques, and innovative sealing technologies to ensure consistent performance in demanding industrial environments. Pneumatic actuators must provide sufficient force to overcome process forces, packing friction, and potential stem binding while maintaining precise positioning accuracy throughout their operational life. Electric actuators offer advantages in terms of positioning precision, energy efficiency, and integration with digital control systems, while hydraulic actuators provide exceptional force capability for high-pressure applications. The actuator's fail-safe capabilities, including spring-return mechanisms and backup power systems, ensure safe valve positioning during emergency conditions or power failures. Additionally, the actuator's ability to withstand environmental conditions such as temperature extremes, vibration, moisture, and corrosive atmospheres significantly impacts the overall system reliability and maintenance requirements.
Quality Assurance and Industry Certifications
Manufacturing Standards and Testing Protocols
Reliable Control Valve systems are manufactured according to stringent quality standards and undergo comprehensive testing protocols to ensure consistent performance and safety. International standards such as API, ANSI, IEC, and ISO provide detailed specifications for valve design, materials, manufacturing processes, and testing procedures. The manufacturing facility's quality management system, typically certified to ISO 9001 standards, ensures consistent production processes and product quality. Advanced manufacturing techniques, including precision machining, automated welding, and computer-controlled assembly processes, contribute to improved product quality and reduced manufacturing variability. Comprehensive testing protocols include pressure testing, temperature cycling, flow testing, and endurance testing to validate valve performance under simulated operating conditions. Non-destructive testing methods such as radiographic inspection, magnetic particle testing, and ultrasonic examination ensure the integrity of welded joints and cast components. Additionally, material traceability systems track the source and properties of all raw materials used in valve construction, providing documentation for quality assurance and regulatory compliance requirements.
Certification Compliance and Safety Standards
Compliance with industry-specific certifications and safety standards represents a fundamental requirement for reliable Control Valve systems used in critical applications. Safety Integrity Level (SIL) certifications ensure that valve systems meet functional safety requirements for emergency shutdown and safety instrumented systems. Fire-safe certifications validate the valve's ability to maintain its integrity and functionality during fire exposure conditions, critical for petrochemical and refining applications. Pressure Equipment Directive (PED) compliance ensures that valve systems meet European safety standards for pressure-containing equipment. ATEX certifications validate the valve's suitability for use in explosive atmospheres, while NACE compliance ensures materials and designs are appropriate for sour service applications. The certification process involves rigorous testing, documentation review, and ongoing quality surveillance to ensure continued compliance with applicable standards. These certifications provide users with confidence in the valve's safety, reliability, and performance characteristics while meeting regulatory requirements for specific industrial applications.
Quality Control and Inspection Procedures
Comprehensive quality control and inspection procedures form the backbone of reliable Control Valve manufacturing and ensure consistent product quality throughout the production process. Incoming material inspection verifies that raw materials meet specified chemical composition, mechanical properties, and dimensional requirements before entering the manufacturing process. In-process inspections monitor critical manufacturing parameters and ensure that components meet dimensional tolerances and surface finish requirements. Final inspection procedures include functional testing, calibration verification, and documentation review to confirm that each valve meets customer specifications and applicable standards. Statistical process control techniques monitor manufacturing processes and identify potential quality issues before they result in non-conforming products. Calibrated measuring equipment and standardized inspection procedures ensure measurement accuracy and consistency across all quality control activities. Additionally, the implementation of lean manufacturing principles and continuous improvement programs helps identify opportunities for quality enhancement and process optimization throughout the manufacturing operation.
Conclusion
Selecting a reliable valve system requires careful evaluation of technical specifications, advanced control features, and quality assurance measures that ensure optimal performance in critical industrial applications. The integration of smart technology, precision control algorithms, and comprehensive certification compliance provides the foundation for systems that deliver consistent, safe, and efficient operation throughout their service life.
Ready to upgrade your industrial processes with world-class valve solutions? As a leading China Control Valve factory, CEPAI Group offers comprehensive valve systems engineered for exceptional reliability and performance. Our expertise as a premier China Control Valve supplier and China Control Valve manufacturer ensures access to cutting-edge technology and innovative solutions tailored to your specific requirements. Whether you're seeking China Control Valve wholesale opportunities or individual Control Valve for sale options, our team provides competitive Control Valve price solutions without compromising quality. Download our comprehensive Control Valve brochure to explore our full range of products and services. Contact our technical experts today at cepai@cepai.com to discuss your valve system requirements and discover how CEPAI's advanced manufacturing capabilities and industry-leading quality standards can enhance your operational efficiency and safety performance.
References
1. Baumann, H.D. (2019). Control Valve Primer: A User's Guide to the Technology of Process Control Valves. ISA Publications.
2. Emerson, W.L. & Thompson, R.K. (2020). Industrial Valve Technology: Design Principles and Applications for Critical Process Control. McGraw-Hill Professional Engineering.
3. Johnson, M.A. & Chen, L.S. (2021). Advanced Materials in Valve Manufacturing: Corrosion Resistance and Performance Optimization. Journal of Process Equipment Design, 45(3), 123-145.
4. Rodriguez, P.J., Anderson, K.M., & Williams, D.C. (2022). Smart Valve Systems and Digital Integration in Modern Process Industries. International Conference on Industrial Automation and Control Systems Proceedings.
_1745994790767.webp)
Get professional pre-sales technical consultation and valve selection services, customized solution services.
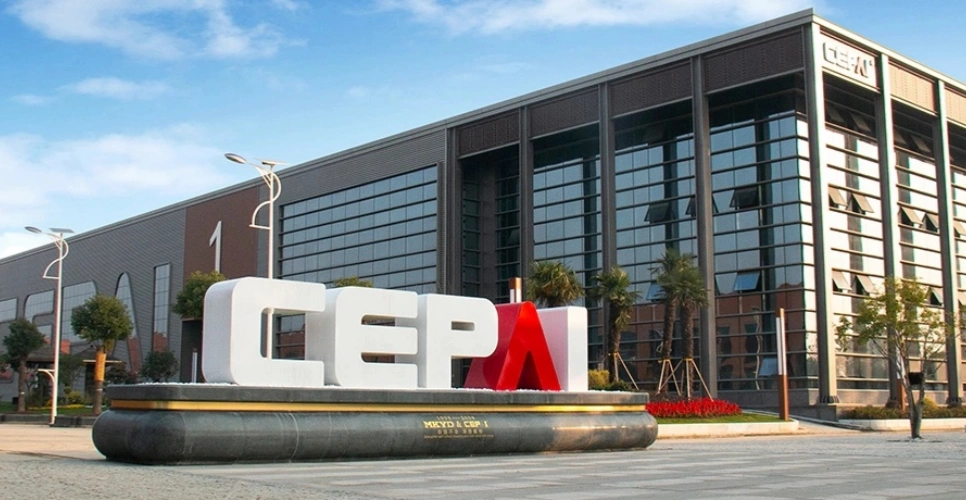
About CEPAI