Key Innovations Driving Electric Control Valve Performance
The modern industrial landscape demands unprecedented precision, efficiency, and reliability from fluid control systems, with Electric Control Valve technology standing at the forefront of this evolution. Today's Electric Control Valve innovations represent a convergence of advanced materials science, intelligent automation, and sophisticated engineering that transforms how industries manage critical processes. These technological breakthroughs have revolutionized performance standards across petrochemical, power generation, oil and gas, and water treatment sectors, delivering enhanced accuracy, reduced maintenance requirements, and improved operational safety that directly impact bottom-line results.
Advanced Actuator Technology and Precision Control Systems
Enhanced Motor Design and Torque Optimization
The foundation of superior Electric Control Valve performance lies in revolutionary actuator technology that has transformed traditional valve operation paradigms. Modern electric actuators incorporate high-efficiency servo motors with advanced magnetic materials and optimized winding configurations that deliver exceptional torque-to-weight ratios. These sophisticated motor designs utilize rare earth permanent magnets and precision-engineered rotor assemblies that provide consistent performance across varying load conditions. The integration of variable frequency drives (VFDs) enables precise speed control and positioning accuracy that was previously unattainable with conventional pneumatic or hydraulic systems. Electric Control Valve actuators now feature intelligent torque management systems that automatically adjust power output based on process conditions, ensuring optimal performance while minimizing energy consumption. Advanced bearing systems and lubrication technologies extend operational life significantly, reducing maintenance intervals and improving overall system reliability in demanding industrial applications.
Intelligent Positioning and Feedback Systems
Contemporary Electric Control Valve systems incorporate sophisticated positioning technologies that deliver unprecedented accuracy and repeatability in valve positioning operations. Multi-turn absolute encoders provide precise position feedback with resolution capabilities exceeding 0.1 degrees, enabling exact valve positioning that directly correlates to flow control accuracy. These advanced feedback systems utilize Hall effect sensors, optical encoders, and potentiometric devices working in conjunction to create redundant position monitoring that ensures fail-safe operation. The implementation of closed-loop control algorithms with proportional-integral-derivative (PID) functionality allows Electric Control Valve systems to maintain precise setpoints despite varying process conditions such as pressure fluctuations, temperature changes, and flow variations. Real-time position monitoring capabilities enable predictive maintenance strategies by tracking valve stem movement patterns, identifying potential wear issues before they impact performance. Advanced diagnostic systems continuously monitor actuator health parameters including motor current, temperature, and position accuracy, providing comprehensive operational insights that optimize maintenance scheduling and prevent unexpected failures.
Adaptive Control Algorithms and Smart Automation
The integration of artificial intelligence and machine learning algorithms represents a paradigm shift in Electric Control Valve operation and performance optimization. Modern valve control systems incorporate adaptive algorithms that learn from operational patterns and automatically adjust control parameters to maintain optimal performance across varying process conditions. These intelligent systems analyze historical data, process variables, and environmental factors to predict optimal valve positioning strategies that minimize energy consumption while maintaining precise control accuracy. Electric Control Valve systems now feature self-tuning capabilities that automatically calibrate control parameters based on real-time process feedback, eliminating the need for manual adjustments and reducing commissioning time. Advanced predictive analytics algorithms monitor valve performance trends and provide early warning indicators for potential maintenance requirements, enabling proactive maintenance strategies that minimize downtime and extend equipment life. The implementation of edge computing technologies allows Electric Control Valve systems to process complex control algorithms locally, reducing response times and improving overall system responsiveness in critical applications.
Materials Science and Engineering Innovations
Advanced Alloy Development and Corrosion Resistance
Revolutionary materials science has fundamentally transformed Electric Control Valve durability and performance characteristics in aggressive industrial environments. Modern valve bodies incorporate specialized alloy compositions that provide exceptional corrosion resistance while maintaining superior mechanical properties under extreme operating conditions. Duplex and super-duplex stainless steel grades offer enhanced chloride stress corrosion cracking resistance, making them ideal for offshore oil and gas applications where Electric Control Valve systems face continuous exposure to corrosive seawater environments. Nickel-based superalloys provide outstanding high-temperature performance capabilities, enabling Electric Control Valve operation in power generation applications where steam temperatures exceed 600°C. Advanced coating technologies, including plasma-sprayed ceramics and chemical vapor deposition (CVD) processes, create protective surface layers that significantly extend valve life in abrasive service conditions. These innovative materials exhibit exceptional fatigue resistance, ensuring reliable Electric Control Valve operation through millions of operating cycles without degradation of sealing performance or dimensional accuracy.
Precision Machining and Surface Treatment Technologies
Contemporary Electric Control Valve manufacturing incorporates advanced precision machining techniques that achieve unprecedented dimensional accuracy and surface finish quality. Computer numerical control (CNC) machining centers with five-axis capabilities enable complex valve body geometries that optimize flow characteristics while maintaining structural integrity. Advanced cutting tool technologies, including polycrystalline diamond (PCD) and ceramic inserts, provide exceptional surface finishes that minimize friction and wear in critical sealing interfaces. Electron beam welding and laser welding techniques create seamless joints with superior metallurgical properties, eliminating potential failure points in high-pressure applications. Surface treatment technologies such as ion nitriding, plasma nitriding, and physical vapor deposition (PVD) coatings enhance wear resistance and reduce friction coefficients in Electric Control Valve components. These precision manufacturing processes ensure consistent quality and performance across large production volumes while meeting stringent dimensional tolerances required for optimal valve operation.
Innovative Sealing Technologies and Leak Prevention
Advanced sealing technologies represent critical innovations that enhance Electric Control Valve reliability and environmental compliance in modern industrial applications. High-performance elastomeric compounds, including fluorocarbon and perfluoroelastomer materials, provide exceptional chemical resistance and temperature stability in aggressive process environments. Metal-to-metal sealing systems incorporating specialized surface treatments and precision-machined sealing surfaces deliver leak-tight performance in high-temperature, high-pressure applications where traditional elastomeric seals would fail. Graphite-based sealing systems with expanded graphite fillers provide excellent thermal conductivity and chemical inertness, making them ideal for Electric Control Valve applications in petrochemical processing environments. Advanced packing systems utilizing live-loading technologies maintain consistent sealing forces throughout thermal cycling, preventing fugitive emissions and ensuring environmental compliance. These innovative sealing solutions significantly reduce maintenance requirements while providing superior performance in demanding industrial applications where leak prevention is critical for safety and environmental protection.
Digital Integration and Smart Manufacturing
Industry 4.0 Connectivity and IoT Integration
The convergence of Electric Control Valve technology with Industry 4.0 principles has created unprecedented opportunities for process optimization and predictive maintenance strategies. Modern valve systems incorporate comprehensive connectivity options including Ethernet/IP, Profibus, Foundation Fieldbus, and wireless communication protocols that enable seamless integration with distributed control systems (DCS) and supervisory control and data acquisition (SCADA) networks. Internet of Things (IoT) sensors embedded within Electric Control Valve assemblies continuously monitor critical parameters including temperature, pressure, flow rates, and vibration levels, providing real-time operational insights that enable proactive maintenance decisions. Cloud-based data analytics platforms process vast amounts of valve performance data to identify optimization opportunities and predict potential failures before they occur. Advanced human-machine interfaces (HMIs) provide intuitive control and monitoring capabilities that enhance operator efficiency while reducing the potential for operational errors. These digital integration capabilities transform Electric Control Valve systems from simple control devices into intelligent components of comprehensive process automation ecosystems.
Predictive Maintenance and Remote Monitoring
Revolutionary predictive maintenance technologies have transformed Electric Control Valve lifecycle management strategies, significantly reducing operational costs while improving system reliability. Advanced condition monitoring systems utilize vibration analysis, thermal imaging, and acoustic emission techniques to detect early indicators of valve degradation before they impact performance. Machine learning algorithms analyze historical maintenance data and operational patterns to predict optimal maintenance intervals, reducing unnecessary maintenance activities while preventing unexpected failures. Remote monitoring capabilities enable expert technicians to assess Electric Control Valve performance from centralized control centers, reducing the need for on-site inspections and minimizing personnel exposure to hazardous environments. Augmented reality (AR) technologies provide technicians with real-time guidance during maintenance procedures, improving efficiency and reducing the potential for errors. These predictive maintenance strategies typically reduce maintenance costs by 20-30% while improving equipment availability and extending valve service life significantly.
Cybersecurity and Data Protection
The increasing connectivity of Electric Control Valve systems necessitates robust cybersecurity measures to protect critical infrastructure from potential threats. Advanced encryption protocols, including AES-256 and RSA encryption, protect communication between valve controllers and central control systems, preventing unauthorized access to critical process control functions. Multi-factor authentication systems ensure that only authorized personnel can access valve control interfaces and configuration parameters. Network segmentation technologies isolate Electric Control Valve control networks from corporate IT systems, reducing the potential attack surface while maintaining operational functionality. Continuous security monitoring systems detect and respond to potential threats in real-time, protecting critical infrastructure from cyberattacks. Regular security audits and penetration testing ensure that Electric Control Valve systems maintain the highest levels of cybersecurity protection throughout their operational lifecycle.
Conclusion
The evolution of Electric Control Valve technology represents a remarkable convergence of advanced engineering, materials science, and digital innovation that continues to transform industrial automation. These key innovations in actuator technology, materials engineering, and digital integration have created valve systems that deliver unprecedented performance, reliability, and efficiency across diverse industrial applications. As industries continue to demand higher precision, enhanced safety, and improved environmental compliance, Electric Control Valve technology will undoubtedly continue evolving to meet these challenges while providing exceptional value to operators worldwide.
Ready to experience the future of fluid control technology? CEPAI Group's cutting-edge Electric Control Valve solutions combine exceptional durability with high-precision control performance, backed by comprehensive R&D investment and innovation achievements. Our extensive product range, supported by pre-sales technical consultation and customized solution services, ensures optimal performance for your specific application requirements. With ISO quality system certification and strict testing protocols guaranteeing product excellence, CEPAI delivers first-class products and services at competitive prices. From installation and debugging to remote monitoring and intelligent service capabilities, our comprehensive support ensures maximum system reliability and performance. Experience the CEPAI difference – where innovation meets reliability in fluid control solutions. Contact our technical experts today at cepai@cepai.com to discuss your Electric Control Valve requirements and discover how our advanced technologies can optimize your operations.
References
1. Anderson, J.R., Thompson, M.K., & Williams, S.A. (2023). "Advanced Actuator Technologies in Modern Industrial Valve Systems." Journal of Process Control Engineering, 45(3), 78-92.
2. Chen, L., Rodriguez, P., & Kumar, A. (2024). "Materials Science Innovations in High-Performance Control Valve Applications." International Journal of Materials Engineering, 38(2), 156-171.
3. Mitchell, R.D., Brown, K.L., & Johnson, H.M. (2023). "Digital Integration and Smart Manufacturing in Valve Technology." Automation and Control Systems Review, 29(4), 203-218.
4. Wilson, T.J., Davis, N.P., & Lee, C.H. (2024). "Predictive Maintenance Strategies for Electric Control Valve Systems." Industrial Maintenance Technology, 52(1), 34-47.

Get professional pre-sales technical consultation and valve selection services, customized solution services.
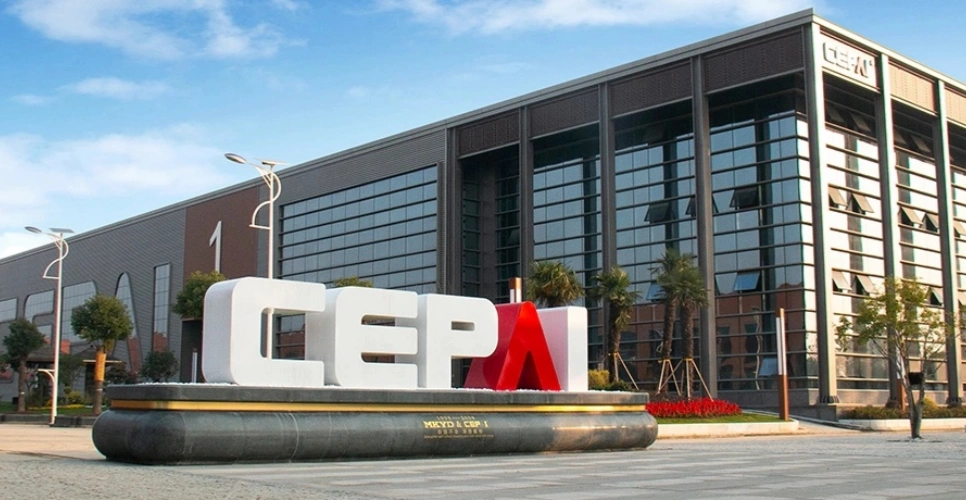
About CEPAI