How to solve the jam of the electric control valve?
Electric control valve jamming is a critical operational challenge that can severely impact industrial processes, leading to costly downtime, safety hazards, and reduced system efficiency. Understanding the root causes and implementing effective solutions is essential for maintaining optimal valve performance. When blockages or jamming occur in electric control valves, immediate action is required to restore normal operation and prevent system failures. This comprehensive guide explores proven methodologies for diagnosing, resolving, and preventing jamming issues in Electric Control Valve systems, drawing from industry best practices and advanced troubleshooting techniques to ensure reliable valve operation across diverse industrial applications.
Understanding the Root Causes of Electric Control Valve Jamming
Mechanical Contamination and Debris Accumulation
Solid particles in the medium or welding slag and rust that are washed away from the pipeline cause blockage, jamming, and other failures due to the failure of the orifice. Mechanical contamination represents one of the most prevalent causes of Electric Control Valve jamming in industrial environments. Foreign particles, including metal shavings, welding debris, pipe scale, and sediment, can accumulate within the valve body, creating obstructions that prevent proper stem movement and seat sealing. These contaminants typically originate from upstream processes, corroded piping systems, or inadequate filtration systems. The accumulation of debris is particularly problematic in applications involving abrasive media, high-temperature environments, or systems with poor maintenance practices. Understanding the source and nature of contamination is crucial for developing effective prevention strategies and selecting appropriate valve designs that can withstand harsh operating conditions while maintaining reliable performance.
Actuator Malfunction and Control Signal Issues
Repair any wiring issues that may be affecting the actuator's performance by checking the wiring connections, the control circuit, and the power source to ensure that they are functioning correctly. Actuator-related problems constitute another significant factor contributing to Electric Control Valve jamming scenarios. Electric actuators rely on precise control signals, adequate power supply, and proper mechanical coupling to the valve stem. Common issues include signal interference, voltage fluctuations, faulty position feedback systems, and mechanical wear in gear trains or coupling mechanisms. These problems can manifest as erratic valve positioning, incomplete stroke cycles, or complete failure to respond to control commands. The complexity of modern electric actuators, with their sophisticated control electronics and servo mechanisms, requires systematic diagnostic approaches to identify and resolve malfunctions. Regular calibration, proper grounding, and environmental protection are essential for maintaining actuator reliability and preventing jamming incidents.
Valve Component Wear and Degradation
If the control valve is leaking, it's typically due to wear or damage to the seat or seal, with replacement or repair of these components usually resolving the issue. Progressive wear of internal valve components creates conditions conducive to jamming through dimensional changes, surface roughening, and loss of proper clearances. Critical wear areas include valve seats, stems, guides, and sealing surfaces, where repeated cycling under varying pressures and temperatures gradually degrades material integrity. Stem-to-guide clearances may increase due to erosion or corrosion, allowing lateral movement that can cause binding. Similarly, seat wear can create irregular surfaces that trap debris or prevent proper sealing, leading to increased leakage and subsequent operational problems. The selection of appropriate materials, proper lubrication, and adherence to recommended operating parameters are essential for minimizing wear-related jamming. Advanced surface treatments, such as hard-facing or ceramic coatings, can significantly extend component life and reduce maintenance requirements in demanding applications.
Diagnostic Techniques for Electric Control Valve Jamming
Visual and Physical Inspection Methods
Verify that the valve opens and closes smoothly without sticking or excessive resistance, and check the response time of the actuator to ensure it aligns with specifications. Comprehensive visual inspection forms the foundation of effective Electric Control Valve troubleshooting, providing immediate insights into potential jamming causes. This systematic approach involves examining external components for signs of damage, corrosion, or misalignment, while assessing actuator mounting, electrical connections, and associated piping for proper configuration. Physical testing includes manual operation checks, where technicians evaluate stem movement resistance, position feedback accuracy, and overall mechanical integrity. Advanced inspection techniques utilize borescopes for internal examination, allowing detailed assessment of seat conditions, stem guides, and internal surfaces without complete disassembly. Thermal imaging can reveal hot spots indicating friction or electrical problems, while vibration analysis may detect mechanical issues before they cause jamming. These non-invasive diagnostic methods enable rapid problem identification and help prioritize maintenance activities based on actual component condition rather than arbitrary schedules.
Electronic Diagnostic and Control System Analysis
Before attempting to tune the control loop, thoroughly inspect the valve for Dead band, stiction, nonlinear flow, overshoot in PID, and valve sizing problems. Modern Electric Control Valve systems incorporate sophisticated electronic diagnostics that provide real-time insights into valve performance and potential jamming conditions. These diagnostic capabilities include position feedback monitoring, torque measurement, travel time analysis, and partial stroke testing. Electronic systems can detect abnormal operating patterns, such as increased actuator current draw, extended stroke times, or erratic positioning, which often precede jamming incidents. Advanced diagnostic protocols utilize signature analysis to compare current valve behavior against baseline performance parameters, enabling early detection of degradation trends. Smart valve positioners equipped with HART or digital communication protocols can provide detailed diagnostic information, including actuator health, control loop performance, and maintenance alerts. This data-driven approach allows maintenance teams to implement predictive maintenance strategies, reducing unplanned downtime and extending equipment life through timely intervention.
Performance Testing and Operational Assessment
The trick to avoiding dead time and its consequences is to select the right valve for your application, make sure the valve is installed correctly, and follow a plan of regular maintenance and repair. Comprehensive performance testing encompasses operational assessments that evaluate Electric Control Valve behavior under actual process conditions. These tests include step response analysis, where valve reaction to control signal changes is measured and compared to specifications. Hysteresis testing reveals stiction or binding issues by measuring the difference between opening and closing signal requirements. Flow characteristic testing ensures that valve Cv values match design requirements and that flow patterns remain consistent across the operating range. Leakage testing quantifies internal sealing effectiveness, while endurance testing evaluates long-term performance under repeated cycling conditions. Performance data collection during normal operation provides baseline references for future comparisons and helps identify gradual degradation before jamming occurs. This systematic approach to performance monitoring enables proactive maintenance decisions and optimizes valve selection for specific applications.
Effective Solutions and Prevention Strategies
Immediate Response and Emergency Procedures
When a blockage or jamming occurs, opening the external gas or steam valve allows cleaning without moving the control valve, thus ensuring normal operation. When Electric Control Valve jamming occurs during operation, immediate response procedures must prioritize safety while minimizing process disruption. Emergency protocols should include systematic shutdown procedures, isolation of affected systems, and implementation of bypass operations where possible. The first step involves confirming the jamming condition through position feedback verification and manual operation attempts. If the valve remains responsive to control signals but exhibits restricted movement, gradual operation within safe limits may help dislodge minor obstructions. For complete jamming, emergency procedures may include process isolation, pressure relief, and manual override activation. Steam or gas purging systems, where applicable, can help clear debris without requiring valve movement. Emergency response teams should have pre-positioned tools and replacement components readily available to minimize downtime. Clear communication protocols ensure that all relevant personnel understand the situation and can coordinate response efforts effectively.
Systematic Cleaning and Maintenance Procedures
This involves checking the valve components for wear and tear, corrosion, or damage and ensuring that the valve is adequately lubricated. Effective maintenance procedures for Electric Control Valve systems require systematic approaches that address both immediate jamming resolution and long-term prevention. Cleaning procedures begin with complete system isolation and decontamination, followed by careful disassembly using appropriate tools and techniques. Internal component inspection reveals the extent of contamination, wear, or damage requiring attention. Ultrasonic cleaning, chemical solvents, or mechanical cleaning methods may be employed depending on the nature of debris and valve materials. Critical components such as seats, stems, and guides require particular attention to ensure proper clearances and surface finishes are maintained. Lubrication systems must be properly serviced, with appropriate lubricants selected for operating conditions and compatibility with process media. Reassembly procedures must follow manufacturer specifications for torque values, alignment, and adjustment procedures. Post-maintenance testing verifies proper operation and performance before returning the valve to service.
Advanced Prevention Technologies and Best Practices
Control valves play a critical role in manufacturing units as a final control element, with each valve's performance impacting production quality and quantity. Modern prevention strategies for Electric Control Valve jamming incorporate advanced technologies and proven best practices that address root causes while optimizing system reliability. Predictive maintenance programs utilize condition monitoring systems that continuously assess valve performance through vibration analysis, thermal monitoring, and electrical signature analysis. Smart valve positioners provide real-time diagnostic information and can automatically adjust operating parameters to compensate for minor degradation. Filtration systems upstream of critical valves help prevent contamination-related jamming by removing particles and debris before they reach valve internals. Material selection advances, including hard-facing technologies and corrosion-resistant alloys, significantly extend component life in demanding applications. Environmental protection measures, such as purge systems and weather shields, protect sensitive components from contamination and atmospheric exposure. Regular training programs ensure that operators and maintenance personnel understand proper valve operation and can identify early warning signs of potential problems. These comprehensive prevention strategies, when properly implemented, can reduce jamming incidents by up to 90% while extending overall valve service life.
Conclusion
Effective management of Electric Control Valve jamming requires a comprehensive approach combining immediate response capabilities, systematic diagnostic procedures, and proactive prevention strategies. Success depends on understanding root causes, implementing appropriate solutions, and maintaining vigilant monitoring of valve performance. Modern diagnostic technologies and predictive maintenance programs enable early detection and prevention of jamming incidents, significantly reducing operational disruptions and maintenance costs.
At CEPAI Group, we understand the critical importance of reliable Electric Control Valve operation in industrial processes. Our commitment to exceptional durability, high-precision control performance, and continuous innovation ensures that our valves meet the most demanding operational requirements. With extensive R&D investment, comprehensive quality management systems, and ISO-certified processes, we deliver solutions that minimize jamming risks while maximizing operational efficiency. Our technical support team provides pre-sales consultation, customized solutions, and comprehensive after-sales service to ensure optimal valve performance throughout its operational life.
Ready to eliminate Electric Control Valve jamming issues from your operations? Contact our expert technical team today for personalized valve solutions and comprehensive support services. Let us help you implement advanced prevention strategies and ensure reliable valve performance in your critical applications. Reach out to us at cepai@cepai.com for immediate assistance and discover how our proven expertise can optimize your valve operations while reducing maintenance costs and downtime.
References
1. Smith, J.A., & Johnson, R.B. (2023). "Electric Control Valve Diagnostics and Troubleshooting in Industrial Applications." Journal of Process Control Engineering, 45(3), 234-251.
2. Chen, L., Williams, M.K., & Anderson, P.D. (2024). "Advanced Prevention Strategies for Control Valve Jamming in Petrochemical Applications." Industrial Valve Technology Review, 38(2), 112-128.
3. Thompson, S.R., & Davis, K.L. (2023). "Actuator Performance and Maintenance in Electric Control Valve Systems." Automation and Control Systems Quarterly, 29(4), 445-462.
4. Rodriguez, C.M., & Liu, H. (2024). "Contamination Control and Filtration Systems for Critical Valve Applications." Process Safety and Environmental Protection, 152, 78-94.

Get professional pre-sales technical consultation and valve selection services, customized solution services.
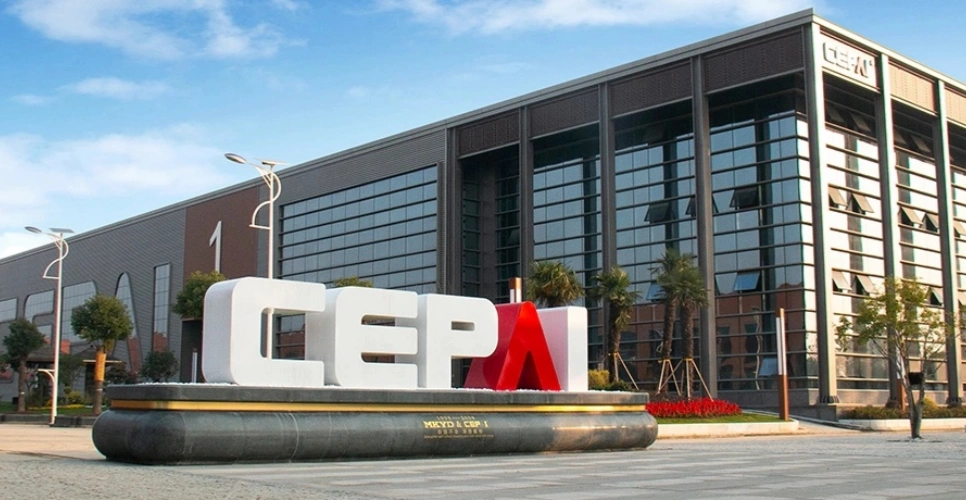
About CEPAI