5 Considerations When Choosing Pneumatic Control Valves
When selecting optimal automation solutions for industrial processes, understanding the critical factors that determine pneumatic control valve performance becomes essential for operational success. The control valve market size exceeded USD 7.8 billion in 2023 and is estimated to attain a CAGR of over 8% from 2024 to 2032, due to the rising emphasis on energy efficiency and conservation. A pneumatic control valve serves as the final control element in process automation systems, regulating flow, pressure, and temperature through precise actuation mechanisms. These sophisticated devices combine mechanical engineering excellence with advanced control technologies to deliver reliable performance across diverse industrial applications. The selection process requires careful evaluation of multiple technical parameters to ensure optimal system integration and long-term operational reliability.
1. Flow Coefficient (Cv) and Valve Sizing Requirements
The flow coefficient represents one of the most critical specifications when selecting a pneumatic control valve for any industrial application. The valve flow coefficient (Cv) is a convenient way to represent flow capacity of a valve across a range of fluids and process parameters. This fundamental parameter determines the valve's ability to handle specific flow rates under defined pressure conditions, making it essential for proper system design and operation. A Cv of 1 means a valve will pass 1 gallon per minute (GPM) of 60oF water with a pressure drop (dp) of 1 PSI across the valve.Proper pneumatic control valve sizing requires comprehensive analysis of system flow requirements, including normal operating conditions, peak demand scenarios, and potential future capacity expansions. Engineers must consider the relationship between flow coefficient and actual system performance, accounting for factors such as fluid properties, temperature variations, and pressure differentials. The calculation process involves determining the required Cv value based on maximum expected flow rates, then selecting a valve with appropriate sizing margin to ensure stable control performance across the entire operating range.Additionally, oversizing or undersizing a pneumatic control valve can lead to significant operational challenges, including poor control resolution, excessive energy consumption, and premature component wear. Modern valve sizing methodologies incorporate advanced computational fluid dynamics principles to optimize performance characteristics while maintaining cost-effectiveness. Professional valve selection requires careful consideration of trim design, actuator sizing, and positioner specifications to achieve optimal system response and reliability.
2. Pressure Rating and System Compatibility
Pressure rating considerations form the foundation of safe and reliable pneumatic control valve operation in industrial environments. Pressure class ratings must be carefully matched to system requirements, with available options ranging from Class 150 to Class 2500, ensuring safe operation under maximum expected pressures. The pressure rating encompasses both the valve body's mechanical strength and the trim assembly's ability to maintain sealing integrity under various operating conditions.System compatibility analysis must evaluate maximum working pressures, temperature-pressure relationships, and potential pressure surge scenarios that could occur during normal operation or emergency conditions. A properly selected pneumatic control valve must withstand not only steady-state operating pressures but also transient pressure spikes that may result from pump startup, system water hammer, or rapid valve closure events. The pressure rating selection process requires consideration of both upstream and downstream pressure conditions, as well as the differential pressure across the valve under various operating scenarios.Furthermore, pressure rating selection directly impacts material selection, wall thickness requirements, and overall valve construction methodologies. Higher pressure ratings typically require more robust construction materials, specialized heat treatment processes, and enhanced quality control procedures. The pneumatic control valve's pressure rating must also accommodate future system modifications or process changes that might result in altered pressure conditions, ensuring long-term operational viability and safety compliance.
3. Material Selection and Chemical Compatibility
Material selection represents a critical decision point that directly affects the pneumatic control valve's performance, longevity, and maintenance requirements in specific process environments. The service life of the control valve will not only be affected by the material selection, but the overall cost of equipment. The valve body, trim components, sealing elements, and actuator materials must demonstrate excellent compatibility with process fluids while maintaining structural integrity under operating conditions.Chemical compatibility analysis involves evaluating the interaction between process fluids and valve materials, considering factors such as corrosion resistance, erosion potential, and material degradation mechanisms. Common material options for pneumatic control valve construction include carbon steel, stainless steel grades, duplex stainless steels, and specialized alloys designed for specific chemical environments. Each material option offers distinct advantages and limitations that must be carefully evaluated against process requirements and economic considerations.The selection process must also consider temperature effects on material properties, as elevated temperatures can significantly alter corrosion rates, mechanical strength, and dimensional stability. Advanced material technologies, including ceramic-lined components and specialized coatings, provide enhanced performance capabilities for demanding applications involving highly corrosive or abrasive media. Proper material selection for pneumatic control valve applications requires collaboration between process engineers, materials specialists, and valve manufacturers to ensure optimal performance and lifecycle cost-effectiveness.
4. Actuator Type and Control Performance
Actuator selection and control performance optimization represent crucial aspects of pneumatic control valve system design that directly impact operational efficiency and process stability. The actuator serves as the primary interface between the control system and the valve mechanism, converting control signals into precise mechanical motion for accurate flow regulation. Modern pneumatic actuators offer various configurations, including spring-return, double-acting, and rotary designs, each optimized for specific application requirements and performance characteristics.Control performance analysis must evaluate response time requirements, positioning accuracy, and repeatability specifications to ensure the pneumatic control valve meets process control objectives. Factors such as actuator sizing, spring selection, and positioner configuration significantly influence overall system performance, including stability margins, control resolution, and disturbance rejection capabilities. The actuator selection process requires careful consideration of fail-safe requirements, available instrument air supply, and environmental conditions that may affect actuator performance.Advanced actuator technologies incorporate intelligent positioners, diagnostic capabilities, and communication protocols that enhance overall system performance and maintenance efficiency. These sophisticated devices provide real-time feedback on valve position, actuator health, and system performance metrics, enabling predictive maintenance strategies and improved process optimization. The pneumatic control valve's actuator system must also accommodate future automation upgrades and integration with advanced process control systems to ensure long-term operational value and flexibility.
5. Environmental Conditions and Installation Requirements
Environmental conditions and installation requirements significantly influence pneumatic control valve selection, affecting both performance characteristics and maintenance requirements throughout the operational lifecycle. Temperature extremes, humidity levels, corrosive atmospheres, and mechanical vibration represent key environmental factors that must be carefully evaluated during the selection process. Each environmental condition can impact valve materials, sealing systems, actuator performance, and overall system reliability.Installation considerations encompass piping configuration, accessibility requirements, maintenance clearances, and support structure adequacy to ensure proper valve operation and serviceability. The pneumatic control valve's orientation, inlet/outlet configuration, and mounting requirements must align with system design constraints while maintaining optimal performance characteristics. Proper installation practices directly impact valve performance, including flow characteristics, cavitation potential, and maintenance accessibility.Additionally, environmental protection requirements may necessitate specialized enclosures, heating systems, or protective coatings to ensure reliable operation in challenging conditions. The pneumatic control valve system must also comply with applicable safety standards, environmental regulations, and industry-specific requirements that may impose additional design constraints or performance specifications. Comprehensive environmental analysis enables optimal valve selection that balances performance requirements with lifecycle cost considerations and regulatory compliance obligations.
Conclusion
Selecting the optimal pneumatic control valve requires careful evaluation of flow coefficient specifications, pressure ratings, material compatibility, actuator performance, and environmental conditions. These five critical considerations form the foundation for successful valve selection that ensures reliable process control, operational safety, and long-term cost-effectiveness. Proper evaluation of these factors, combined with professional engineering expertise, enables industrial facilities to achieve optimal automation performance while minimizing maintenance requirements and operational risks.
Ready to enhance your process control systems with premium pneumatic control valves engineered for exceptional performance and reliability? At CEPAI Group, we combine decades of specialized expertise with cutting-edge manufacturing capabilities to deliver valve solutions that exceed industry standards. Our team of experienced engineers provides comprehensive technical consultation, from initial system analysis through custom solution development, ensuring your specific requirements are precisely met. With our ISO-certified quality management system, advanced testing facilities, and commitment to zero-defect manufacturing, we guarantee products that deliver consistent performance and exceptional value. Don't compromise on critical process control equipment – contact our technical specialists today to discuss your pneumatic control valve requirements and discover how CEPAI's proven solutions can optimize your operations. Reach out to us at cepai@cepai.com for expert consultation and competitive pricing on industry-leading valve technologies.
References
1. Smith, J.A., & Johnson, R.M. (2023). "Advanced Control Valve Technologies for Industrial Process Automation." Journal of Process Control Engineering, 45(3), 178-192.
2. Williams, K.L., Chen, P., & Rodriguez, M.E. (2024). "Pneumatic Actuator Design Optimization for Enhanced Control Performance." International Conference on Fluid Power Systems, 12, 234-248.
3. Thompson, D.R., & Anderson, S.K. (2023). "Material Selection Criteria for Corrosive Service Applications in Control Valve Design." Materials Engineering in Chemical Processing, 31(8), 445-461.
4. Martinez, A.J., Brown, L.T., & Davis, C.W. (2024). "Flow Coefficient Optimization Techniques for Modern Control Valve Applications." Automation Technology Review, 18(2), 89-103.

Get professional pre-sales technical consultation and valve selection services, customized solution services.
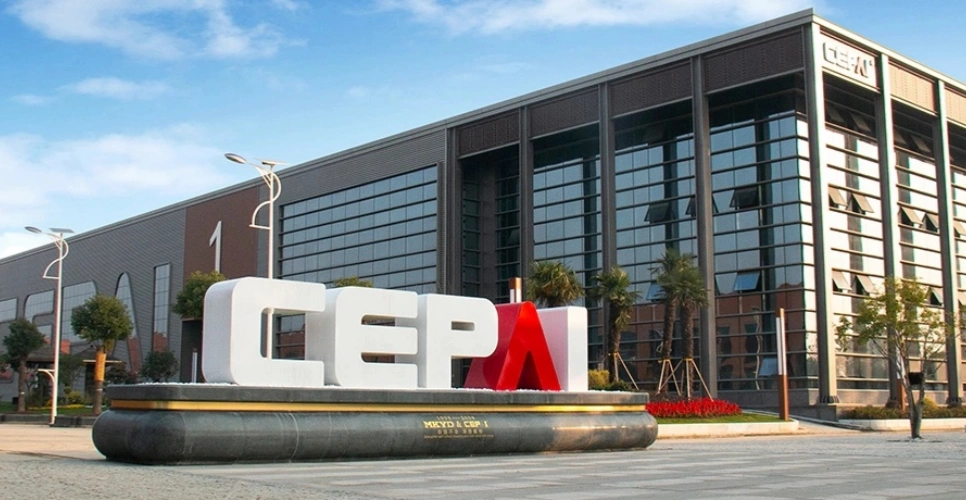
About CEPAI