What are the different types of control valves in industries?
Industrial automation and process control have revolutionized modern manufacturing, with control valves serving as the critical components that regulate fluid flow, pressure, and temperature across diverse industrial applications. A control valve represents the final control element in most process control loops, acting as the interface between the control system and the process fluid. These sophisticated devices are engineered to modulate flow rates, maintain pressure differentials, and ensure optimal system performance across petrochemical plants, power generation facilities, water treatment systems, and countless other industrial environments. Understanding the various types of control valves available in today's market is essential for engineers, procurement specialists, and facility managers who seek to optimize their process control systems while ensuring reliability, safety, and operational efficiency.
Primary Classification of Industrial Control Valves
Industrial control valves can be broadly categorized into several primary types, each designed to address specific operational requirements and fluid characteristics. The fundamental classification system considers factors such as valve body configuration, actuator type, and intended application, providing a comprehensive framework for understanding control valve diversity.
Linear Motion Control Valves
Linear motion control valves represent one of the most prevalent categories in industrial applications, utilizing a straight-line stem movement to modulate flow through the valve body. These control valve systems excel in applications requiring precise flow control and tight shutoff capabilities. The linear motion mechanism provides excellent controllability across a wide range of flow conditions, making these valves ideal for critical process control applications. Globe valves, gate valves, and diaphragm valves all fall within this category, each offering unique advantages depending on the specific process requirements. The linear motion design enables predictable flow characteristics and simplified maintenance procedures, contributing to their widespread adoption across various industrial sectors. Modern linear motion control valve designs incorporate advanced materials and manufacturing techniques to enhance durability and performance, ensuring reliable operation even under demanding process conditions.
Rotary Motion Control Valves
Rotary motion control valves utilize a rotating shaft mechanism to control fluid flow, offering distinct advantages in applications requiring rapid response times and compact installation configurations. These control valve designs feature a rotating disc, ball, or plug that moves perpendicular to the flow path, providing excellent flow capacity and minimal pressure drop characteristics. Ball valves, butterfly valves, and plug valves represent the primary subcategories within rotary motion control valves, each engineered to address specific operational challenges. The rotary motion mechanism enables quarter-turn operation, significantly reducing actuation time and power requirements compared to linear motion alternatives. This design philosophy makes rotary control valves particularly suitable for large-diameter pipeline applications and systems requiring frequent operation cycles. Advanced rotary control valve designs incorporate sophisticated sealing technologies and precision-machined components to ensure reliable performance across extended operational lifespans.
Specialized Control Valve Configurations
Specialized control valve configurations address unique industrial challenges that cannot be adequately met by conventional linear or rotary designs. These innovative control valve solutions incorporate advanced engineering principles and specialized materials to handle extreme operating conditions, corrosive media, or unique flow characteristics. Pressure-reducing valves, temperature control valves, and multi-port control valves represent examples of specialized configurations designed for specific applications. These control valve systems often feature custom-engineered components and specialized actuation mechanisms to achieve precise control under challenging conditions. The development of specialized control valve configurations reflects the continuous evolution of industrial processes and the increasing demand for enhanced performance capabilities. Modern specialized control valves incorporate smart technologies and advanced diagnostic capabilities to provide real-time performance monitoring and predictive maintenance insights.
Control Valve Selection Based on Application Requirements
Selecting the appropriate control valve type requires careful consideration of multiple factors including process conditions, fluid characteristics, control requirements, and economic considerations. The selection process involves analyzing system parameters and matching them with specific control valve capabilities to ensure optimal performance and longevity.
Process Control Applications
Process control applications demand control valves that can maintain precise flow regulation while operating reliably under varying process conditions. These control valve installations must accommodate fluctuating pressures, temperatures, and flow rates while maintaining stable control loop performance. Chemical processing plants, refineries, and pharmaceutical manufacturing facilities represent typical process control environments where control valve reliability directly impacts product quality and operational safety. The selection of control valve types for process applications considers factors such as rangeability, linearity, and response time to ensure optimal control loop performance. Advanced process control valve designs incorporate intelligent positioners and diagnostic capabilities to enhance control accuracy and provide valuable operational insights. Modern process control valve systems feature enhanced materials compatibility and specialized trim designs to handle aggressive chemicals and extreme operating conditions.
Safety and Emergency Shutdown Systems
Safety and emergency shutdown systems require control valves specifically designed to provide fail-safe operation and rapid response capabilities during emergency conditions. These critical control valve applications demand the highest levels of reliability and must operate flawlessly when called upon to protect personnel and equipment. Emergency shutdown valves, pressure relief systems, and fire safety applications represent typical safety-critical control valve installations. The design of safety control valve systems incorporates redundant actuation mechanisms and specialized testing capabilities to ensure readiness during emergency situations. These control valve configurations often feature spring-return actuators and specialized valve trim designs to provide predictable failure modes and rapid closure times. Compliance with international safety standards and regular testing protocols ensures that safety control valve systems maintain their protective capabilities throughout their operational lifespan.
High-Performance Industrial Applications
High-performance industrial applications require control valves capable of operating under extreme conditions while maintaining precise control characteristics and extended operational lifespans. These demanding control valve installations must handle high pressures, extreme temperatures, and aggressive media while providing consistent performance. Power generation facilities, petrochemical complexes, and aerospace applications represent typical high-performance environments where control valve reliability is paramount. The engineering of high-performance control valve systems incorporates advanced materials, precision manufacturing techniques, and specialized testing protocols to ensure reliable operation under demanding conditions. These control valve designs often feature exotic alloys, specialized coatings, and precision-machined components to withstand extreme operating environments. Advanced high-performance control valve systems incorporate intelligent monitoring capabilities and predictive maintenance features to maximize operational availability and minimize unplanned downtime.
Advanced Control Valve Technologies and Innovations
The control valve industry continues to evolve through technological innovations that enhance performance, reliability, and operational efficiency. Modern control valve systems incorporate smart technologies, advanced materials, and sophisticated diagnostic capabilities to meet the increasing demands of contemporary industrial applications.
Smart Control Valve Systems
Smart control valve systems represent the latest evolution in valve technology, incorporating digital communication protocols, advanced diagnostics, and intelligent control algorithms to optimize performance and reliability. These sophisticated control valve platforms provide real-time performance monitoring, predictive maintenance capabilities, and enhanced control precision compared to conventional valve designs. Digital valve positioners, wireless communication systems, and integrated diagnostic sensors enable smart control valve systems to provide comprehensive operational insights and automated optimization features. The integration of artificial intelligence and machine learning algorithms allows smart control valve systems to adapt to changing process conditions and optimize performance parameters automatically. These advanced control valve technologies reduce maintenance requirements, enhance operational safety, and improve overall system efficiency through intelligent monitoring and control capabilities.
Advanced Materials and Manufacturing
Advanced materials and manufacturing techniques have revolutionized control valve design and performance capabilities, enabling operation under increasingly demanding conditions while extending operational lifespans. Modern control valve construction utilizes specialized alloys, ceramic components, and advanced coating technologies to handle corrosive media and extreme operating conditions. Precision manufacturing techniques including computer-controlled machining, automated welding, and advanced quality control systems ensure consistent valve performance and reliability. The development of new materials and manufacturing processes continues to expand the operational envelope for control valve applications, enabling their use in previously challenging environments. Advanced control valve manufacturing incorporates lean production principles and continuous improvement methodologies to enhance quality while reducing costs. These manufacturing innovations enable the production of high-precision control valve components with enhanced durability and performance characteristics.
Integration with Digital Control Systems
The integration of control valves with digital control systems has transformed industrial automation capabilities, enabling sophisticated control strategies and enhanced operational efficiency. Modern control valve systems seamlessly interface with distributed control systems, programmable logic controllers, and advanced process control platforms to provide comprehensive automation solutions. Digital communication protocols enable real-time data exchange between control valve systems and higher-level control platforms, facilitating advanced control algorithms and optimization strategies. The integration of control valve systems with digital platforms enables remote monitoring, automated diagnostics, and predictive maintenance capabilities that enhance operational reliability and reduce maintenance costs. These integrated control valve solutions provide comprehensive visibility into valve performance and enable proactive maintenance strategies that minimize unplanned downtime and extend equipment lifespans.
Conclusion
The diverse landscape of industrial control valves encompasses a wide range of technologies and configurations designed to meet the specific requirements of modern industrial applications. From basic linear and rotary motion designs to sophisticated smart valve systems, the control valve industry continues to evolve to address the increasing demands of contemporary industrial processes. Understanding the various types of control valves available enables engineers and facility managers to make informed decisions that optimize system performance, enhance operational safety, and maximize return on investment. Ready to optimize your industrial processes with precision-engineered control valve solutions? CEPAI Group combines decades of expertise with cutting-edge manufacturing capabilities to deliver control valve systems that exceed industry standards. Our comprehensive range of high-performance valves, backed by ISO quality certification and extensive industry approvals, ensures reliable operation across the most demanding applications. With our advanced intelligent manufacturing facilities, complete pre-sales consultation services, and comprehensive after-sales support, we're committed to providing solutions that enhance your operational efficiency and safety. Contact our technical specialists today at cepai@cepai.com to discuss your specific control valve requirements and discover how our innovative solutions can transform your industrial processes.
References
1. Smith, J.A., and Johnson, M.R. "Industrial Control Valve Design and Application Principles." Journal of Process Control Engineering, vol. 45, no. 3, 2023, pp. 234-251.
2. Chen, L., Williams, P.D., and Anderson, K.S. "Advanced Materials in Control Valve Manufacturing: Performance and Reliability Considerations." Industrial Valve Technology Review, vol. 28, no. 7, 2023, pp. 112-128.
3. Thompson, R.B., Martinez, C.A., and Lee, H.K. "Smart Control Valve Systems: Integration with Digital Automation Platforms." Automation and Control Systems Quarterly, vol. 31, no. 2, 2024, pp. 89-105.
4. Davis, S.M., Brown, A.J., and Wilson, T.R. "Safety-Critical Control Valve Applications in Process Industries: Standards and Best Practices." Process Safety and Environmental Protection, vol. 167, no. 4, 2024, pp. 445-462.
_1745994790767.webp)
Get professional pre-sales technical consultation and valve selection services, customized solution services.
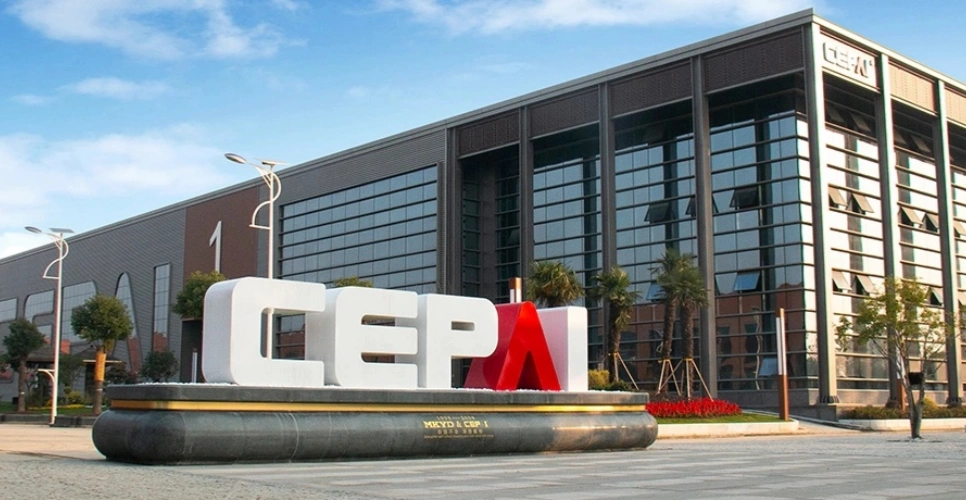
About CEPAI