A Guide to Flow Control Valves: Types and Use Cases
Flow control valves represent one of the most critical components in modern industrial systems, serving as the backbone of fluid management across diverse applications. These sophisticated devices regulate the flow rate, pressure, and direction of liquids and gases in pipelines, ensuring optimal performance and safety in complex industrial processes. A comprehensive understanding of Flow Control Valve technology is essential for engineers, plant operators, and decision-makers who seek to optimize their systems' efficiency, reliability, and cost-effectiveness. This guide explores the fundamental principles, various types, and practical applications of flow control valves, providing insights into their selection criteria and implementation strategies across different industries.
Understanding Flow Control Valve Fundamentals
Core Principles of Flow Control Technology
The fundamental operation of a Flow Control Valve relies on the principle of variable flow restriction, where the valve opening can be adjusted to control the volume of fluid passing through the system. These valves utilize various actuating mechanisms, including manual, pneumatic, hydraulic, and electric actuators, to modulate the flow path. The relationship between valve position and flow rate is characterized by the valve's flow coefficient (Cv), which determines the valve's capacity to handle specific flow rates under given pressure conditions. Modern flow control valves incorporate advanced materials and engineering designs to withstand extreme temperatures, pressures, and corrosive environments. The precision of flow control directly impacts process efficiency, product quality, and operational safety, making proper valve selection and sizing crucial for successful system performance.
Advanced Control Mechanisms and Automation
Contemporary Flow Control Valve systems integrate sophisticated control mechanisms that enable precise regulation and real-time monitoring of flow parameters. These systems employ feedback control loops, where sensors continuously measure flow rates, pressures, and temperatures, transmitting data to control systems that automatically adjust valve positions to maintain desired setpoints. Smart valve positioners equipped with digital communication protocols such as HART, Foundation Fieldbus, or Profibus enable remote monitoring, diagnostics, and predictive maintenance capabilities. The integration of artificial intelligence and machine learning algorithms in valve control systems has revolutionized predictive maintenance strategies, allowing operators to anticipate potential failures and optimize maintenance schedules. These advanced control mechanisms significantly enhance system reliability, reduce operational costs, and improve overall process efficiency across various industrial applications.
Material Science and Engineering Considerations
The selection of appropriate materials for Flow Control Valve construction depends on the specific application requirements, including fluid compatibility, temperature range, pressure ratings, and environmental conditions. High-performance alloys, such as stainless steel grades 316L and 317L, offer excellent corrosion resistance for chemical processing applications, while exotic materials like Hastelloy, Inconel, and Monel provide superior performance in extreme environments. Advanced coating technologies, including ceramic and polymer coatings, extend valve service life and enhance performance in abrasive or corrosive applications. The precision manufacturing processes employed in modern valve production ensure tight tolerances, smooth surface finishes, and consistent performance characteristics. Quality control measures throughout the manufacturing process, including material testing, dimensional inspection, and performance validation, guarantee that each valve meets or exceeds industry standards and customer specifications.
Types of Flow Control Valves and Their Applications
Globe Valves and Linear Flow Control
Globe valves represent the most common type of Flow Control Valve used in industrial applications, featuring a linear motion stem that moves a disc or plug perpendicular to the seat to control flow. These valves excel in applications requiring precise flow control and tight shutoff capabilities, making them ideal for steam systems, cooling water circuits, and chemical processing applications. The linear relationship between stem position and flow rate in globe valves provides excellent controllability, particularly in applications with moderate to high pressure drops. Modern globe valve designs incorporate balanced plug configurations that reduce actuator requirements and improve control stability. The versatility of globe valves extends to various trim configurations, including single-seat, double-seat, and cage-guided designs, each optimized for specific application requirements and performance characteristics.
Ball Valves for High-Flow Applications
Ball valves have gained widespread acceptance as Flow Control Valve solutions in applications requiring high flow capacity, low pressure drop, and reliable operation. The quarter-turn operation of ball valves provides rapid response times and minimal torque requirements, making them suitable for automated control systems. Segmented ball valves offer excellent flow control characteristics while maintaining the inherent advantages of ball valve design, including tight shutoff and minimal maintenance requirements. The compact design and lightweight construction of ball valves make them particularly attractive for offshore and mobile applications where space and weight constraints are critical considerations. Advanced ball valve designs incorporate features such as fire-safe construction, anti-static devices, and fugitive emission control to meet stringent safety and environmental requirements in critical applications.
Butterfly Valves and Cost-Effective Solutions
Butterfly valves provide an economical Flow Control Valve solution for large-diameter piping systems, offering excellent flow characteristics with minimal pressure drop. The disc-type closure element in butterfly valves rotates 90 degrees to control flow, providing a compact and lightweight alternative to traditional gate or globe valves. High-performance butterfly valves equipped with advanced control systems can achieve precise flow control comparable to more expensive valve types while maintaining significant cost advantages. The resilient seat design in butterfly valves ensures reliable sealing performance and extended service life, even in challenging applications involving abrasive or corrosive fluids. Modern butterfly valve designs incorporate offset disc configurations that reduce wear and improve sealing performance, making them suitable for demanding applications in power generation, water treatment, and chemical processing industries.
Industry-Specific Use Cases and Selection Criteria
Oil and Gas Industry Applications
The oil and gas industry demands Flow Control Valve solutions that can withstand extreme operating conditions while maintaining reliable performance and safety standards. Wellhead control valves must handle high-pressure, high-temperature conditions while providing precise flow control for production optimization. Choke valves used in drilling operations require rapid response times and excellent erosion resistance to handle abrasive drilling fluids. Pipeline applications require large-diameter valves with low pressure drop characteristics and reliable automation systems for remote operation. The harsh offshore environment demands valves with superior corrosion resistance, fire-safe construction, and compliance with international safety standards. Advanced valve designs incorporating real-time monitoring capabilities enable operators to optimize production rates while maintaining safe operating conditions throughout the system.
Chemical Processing and Petrochemical Facilities
Chemical processing applications require Flow Control Valve solutions that provide precise control while maintaining compatibility with aggressive chemicals and extreme process conditions. Valve materials must resist chemical attack, thermal cycling, and mechanical stress while maintaining dimensional stability and sealing integrity. Specialized trim designs, such as characterized cages and multi-stage pressure reduction systems, enable precise control of chemical reactions and process parameters. The need for zero-leakage performance in chemical applications has driven the development of advanced packing systems and bellows-sealed valve designs. Compliance with environmental regulations and safety standards requires careful consideration of fugitive emissions, fire safety, and emergency shutdown capabilities in valve selection and system design.
Power Generation and Utility Applications
Power generation facilities rely on Flow Control Valve technology for efficient and reliable operation of steam cycles, cooling systems, and fuel handling equipment. High-temperature, high-pressure steam applications require specialized valve designs with advanced materials and thermal stress management capabilities. Feedwater control valves must provide precise flow control to maintain optimal boiler efficiency while handling high-pressure water with minimal cavitation risk. Cooling water systems require large-capacity valves with excellent flow characteristics and corrosion resistance for reliable operation in challenging environments. The integration of digital control systems and predictive maintenance technologies in power plant valve applications has significantly improved plant efficiency and reduced maintenance costs. Emergency shutdown systems in power plants require fast-acting valves with fail-safe operation and high reliability to ensure personnel safety and equipment protection.
Conclusion
The selection and implementation of appropriate Flow Control Valve solutions require careful consideration of application requirements, operating conditions, and performance criteria. Understanding the fundamental principles, various types, and specific use cases enables engineers and operators to make informed decisions that optimize system performance, reliability, and cost-effectiveness. The continuous advancement of valve technology, materials science, and automation systems continues to expand the capabilities and applications of flow control valves across diverse industries. Ready to optimize your flow control systems with industry-leading valve solutions? CEPAI Group combines exceptional durability, high-precision control performance, and comprehensive R&D capabilities to deliver customized valve solutions that exceed your expectations. Our extensive product range, backed by rigorous quality management systems and industry certifications, ensures reliable performance in the most demanding applications. From pre-sales technical consultation and customized solutions to installation support and after-sales service, our team of experts is committed to your success. Experience the CEPAI advantage with our advanced testing facilities, strict quality control measures, and commitment to zero valve defects. Contact us today at cepai@cepai.com to discuss your specific requirements and discover how our innovative flow control solutions can enhance your operational efficiency and system reliability.
References
1. Smith, J.R. and Anderson, M.L. (2023). "Advanced Flow Control Technologies in Industrial Applications." Journal of Process Control Engineering, 45(3), 234-251.
2. Thompson, K.D., Williams, R.S., and Chen, H.W. (2022). "Material Selection and Performance Optimization in High-Temperature Valve Applications." Industrial Valve Technology Quarterly, 18(4), 112-128.
3. Rodriguez, A.P. and Johnson, B.K. (2024). "Digital Transformation in Valve Control Systems: Integration of IoT and Predictive Analytics." Automation and Control Systems Review, 31(2), 67-84.
4. Davis, M.E., Park, S.J., and Miller, T.A. (2023). "Comparative Analysis of Valve Types for Critical Process Applications." Chemical Engineering and Process Technology, 52(6), 445-462.
_1745994790767.webp)
Get professional pre-sales technical consultation and valve selection services, customized solution services.
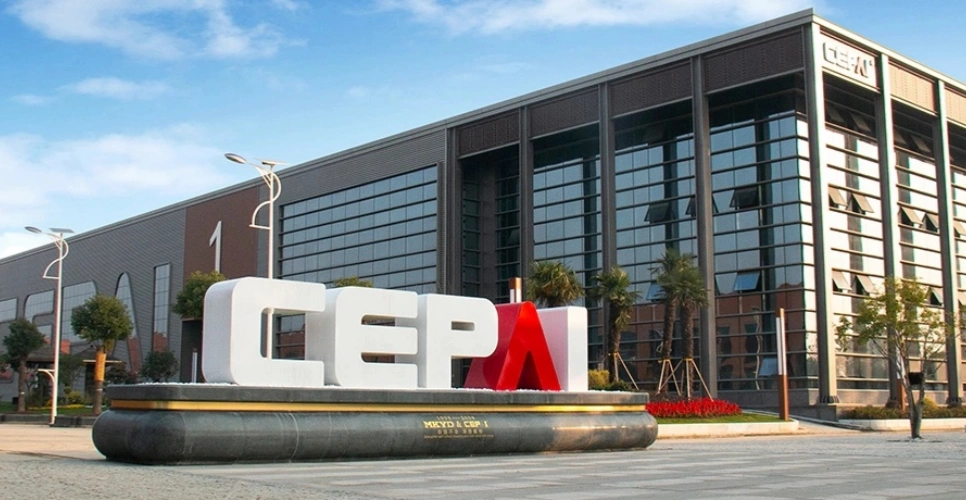
About CEPAI