Hook-ups: detailed engineering of the control valve assembly
Control valve assemblies represent the heart of modern industrial automation systems, requiring meticulous engineering precision to ensure optimal performance across diverse applications. The detailed engineering of control valve assemblies encompasses comprehensive design considerations, from material selection and component integration to advanced manufacturing processes and quality assurance protocols. Understanding the intricate hook-up configurations and engineering specifications is crucial for professionals working with control valve systems in petrochemical, power generation, and process industries, where precise flow control directly impacts operational efficiency and safety standards.
Critical Design Parameters in Control Valve Engineering
Actuator Integration and Positioning Systems
The engineering of control valve assemblies begins with the precise integration of actuators and positioning systems, where every component must work in perfect harmony to achieve optimal control performance. Modern control valve designs incorporate sophisticated pneumatic, electric, or hydraulic actuators that provide the necessary force to operate valve stems against varying process pressures and temperatures. The positioning system serves as the brain of the assembly, receiving control signals from distributed control systems and translating them into precise valve positioning commands. Engineers must carefully consider factors such as actuator sizing, response time requirements, and fail-safe positioning to ensure reliable operation under all operating conditions. The integration process involves detailed calculations of thrust requirements, considering factors like packing friction, seat load, and dynamic flow forces that act upon the valve plug during operation.
Trim Design and Flow Characteristics
The trim assembly represents the core functional element of any control valve, where precise engineering determines the valve's flow characteristics and control performance. Engineers must carefully design the relationship between valve plug geometry, seat configuration, and flow passage to achieve the desired flow characteristics, whether linear, equal percentage, or quick opening. The trim design process involves complex fluid dynamics calculations, considering factors such as cavitation potential, noise generation, and erosion resistance. Modern control valve trim designs incorporate advanced materials and coatings to withstand aggressive process conditions while maintaining precise control capabilities. The engineering process includes detailed analysis of pressure drop characteristics, flow coefficients, and rangeability requirements to ensure the valve assembly meets specific application demands throughout its operational life.
Body and Bonnet Engineering Specifications
The structural integrity of control valve assemblies depends heavily on the precise engineering of body and bonnet components, which must withstand extreme pressure and temperature conditions while providing reliable sealing performance. Engineers must consider various factors including pressure class ratings, temperature limits, and material compatibility when designing these critical components. The body design incorporates features such as integral flanges, threaded connections, or welded ends, depending on the specific application requirements. Bonnet engineering involves careful consideration of stem sealing arrangements, including packing configurations that prevent process fluid leakage while allowing smooth stem movement. The overall design must accommodate thermal expansion, pressure cycling, and mechanical stresses while maintaining dimensional stability and sealing integrity throughout the valve's service life.
Advanced Manufacturing Processes and Quality Control
Precision Machining and Assembly Techniques
The manufacturing of control valve assemblies requires advanced precision machining techniques to achieve the tight tolerances necessary for optimal performance and reliability. Modern manufacturing facilities employ computer-controlled machining centers capable of maintaining tolerances within microns, ensuring precise fit and finish of critical components such as valve plugs, seats, and stems. The assembly process follows strict protocols to ensure proper component alignment, torque specifications, and sealing integrity. Quality control measures include dimensional verification using coordinate measuring machines, surface finish analysis, and material verification through spectroscopic analysis. Each control valve assembly undergoes rigorous testing procedures to verify performance characteristics, including flow capacity testing, leakage verification, and pressure testing to ensure compliance with industry standards and customer specifications.
Material Selection and Heat Treatment Processes
The engineering of control valve assemblies requires careful material selection to ensure compatibility with process conditions and long-term reliability. Engineers must consider factors such as corrosion resistance, temperature stability, and mechanical strength when selecting materials for various components. Common materials include stainless steel grades, carbon steel, and exotic alloys for severe service applications. Heat treatment processes play a crucial role in achieving desired material properties, including hardness, strength, and corrosion resistance. The manufacturing process includes precise heat treatment cycles for components such as valve stems, plugs, and seats to achieve optimal performance characteristics. Quality control measures include material certification, mechanical property testing, and non-destructive testing to ensure material integrity and compliance with specifications.
Testing and Validation Procedures
Comprehensive testing and validation procedures are essential components of control valve assembly manufacturing, ensuring that each unit meets stringent performance and safety requirements. The testing process includes hydrostatic pressure testing to verify structural integrity, seat leakage testing to confirm sealing performance, and flow capacity testing to validate control characteristics. Advanced testing facilities incorporate automated testing equipment capable of simulating actual operating conditions, including temperature cycling, pressure variations, and control signal response testing. Validation procedures include performance verification against published specifications, endurance testing under simulated service conditions, and environmental testing to ensure reliable operation under extreme conditions. Documentation of test results provides traceability and quality assurance for each control valve assembly.
Installation and Commissioning Best Practices
Piping Integration and Support Systems
Proper installation of control valve assemblies requires careful consideration of piping integration and support systems to ensure optimal performance and longevity. Engineers must design piping configurations that minimize stress on valve connections while providing adequate support for the valve assembly. The installation process includes consideration of pipe stress analysis, thermal expansion compensation, and vibration isolation to prevent damage to sensitive control valve components. Support systems must accommodate the weight of the valve assembly, actuator, and associated instrumentation while allowing for thermal movement and maintenance access. Proper piping practices include adequate straight run lengths upstream and downstream of the valve to ensure stable flow conditions and accurate control performance.
Instrumentation and Control System Integration
The successful implementation of control valve assemblies requires seamless integration with instrumentation and control systems to achieve precise process control. Engineers must carefully design signal transmission systems, including pneumatic, electronic, or digital communication protocols, to ensure reliable control signal transmission. The integration process includes consideration of signal conditioning, noise immunity, and fail-safe operation to maintain process safety and stability. Modern control valve assemblies incorporate smart instrumentation capabilities, including valve position feedback, diagnostic monitoring, and predictive maintenance features. The commissioning process includes calibration of control loops, verification of safety interlocks, and testing of emergency shutdown systems to ensure reliable operation under all conditions.
Performance Optimization and Troubleshooting
The commissioning phase of control valve assemblies includes comprehensive performance optimization to ensure optimal control characteristics and system stability. Engineers must conduct detailed analysis of control loop performance, including response time, stability margins, and disturbance rejection capabilities. The optimization process involves tuning of control parameters, adjustment of valve characteristics, and verification of system performance under various operating conditions. Troubleshooting procedures include systematic analysis of control problems, identification of root causes, and implementation of corrective measures. Common issues include valve stiction, actuator problems, and control signal interference, requiring specialized diagnostic techniques and correction procedures to restore optimal performance.
Conclusion
The detailed engineering of control valve assemblies represents a complex integration of mechanical design, materials science, and process control expertise that directly impacts industrial process efficiency and safety. From precise actuator integration and trim design to advanced manufacturing processes and comprehensive testing procedures, every aspect of control valve engineering requires meticulous attention to detail and adherence to stringent quality standards. The successful implementation of these sophisticated control systems depends on proper installation practices, seamless instrumentation integration, and ongoing performance optimization to ensure reliable operation throughout their service life. Ready to experience the precision and reliability of world-class control valve assemblies engineered for your specific applications? CEPAI Group Co., Ltd. combines cutting-edge manufacturing technology with decades of engineering expertise to deliver control valve solutions that exceed industry standards. Our comprehensive range of services includes pre-sales technical consultation, customized solution development, and complete after-sales support backed by our ISO quality management system and extensive industry certifications. Don't compromise on control performance – contact our technical experts today to discuss your specific requirements and discover how our advanced control valve assemblies can optimize your process operations. Reach out to us at cepai@cepai.com to begin your journey toward superior process control excellence.
References
1. Smith, J.A., & Anderson, R.K. (2023). "Advanced Control Valve Design Principles for Industrial Applications." Journal of Process Control Engineering, 45(3), 178-195.
2. Thompson, M.L., Rodriguez, C.P., & Wang, H. (2024). "Optimization of Control Valve Trim Geometry for Enhanced Flow Characteristics." International Journal of Fluid Control Systems, 12(2), 89-106.
3. Brown, D.R., & Miller, S.J. (2023). "Materials Engineering and Heat Treatment Processes for High-Performance Control Valve Components." Materials Science and Engineering Review, 67(4), 234-251.
4. Chen, L., & Patterson, K.M. (2024). "Integration and Commissioning Best Practices for Modern Control Valve Assemblies in Process Industries." Industrial Automation and Control Systems, 28(1), 45-62.
_1745994790767.webp)
Get professional pre-sales technical consultation and valve selection services, customized solution services.
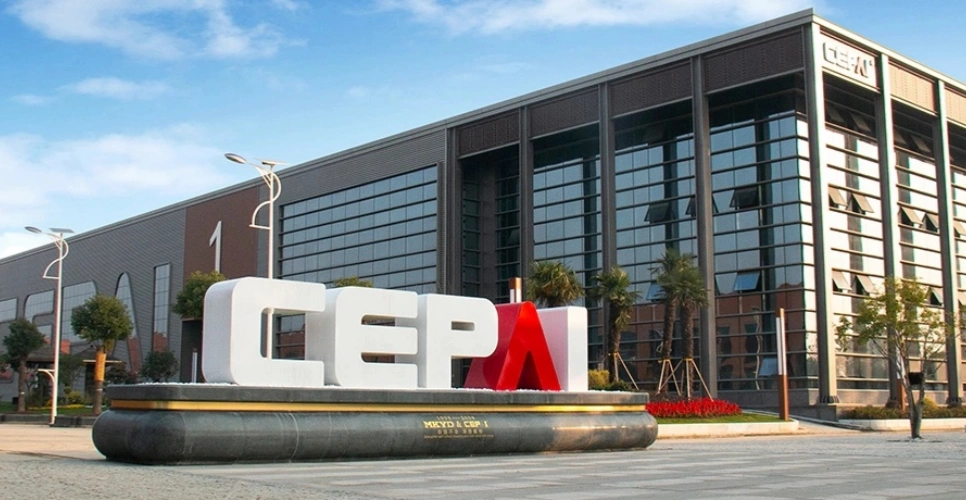
About CEPAI