Electric Control Valve vs Pneumatic Control Valve: Which Is Right for Your Process
Selecting the optimal control valve actuation method is a critical decision that directly impacts your process efficiency, operational costs, and system reliability. The choice between electric control valves and pneumatic control valves represents one of the most fundamental considerations in modern industrial automation. Electric control valves offer precise positioning, digital integration capabilities, and reduced maintenance requirements, making them increasingly popular in applications requiring high accuracy and remote monitoring capabilities. This comprehensive analysis examines the key differences, advantages, and optimal applications for each technology to help you make an informed decision that aligns with your specific process requirements and operational objectives.
Key Performance Differences Between Electric and Pneumatic Control Valves
Precision and Response Characteristics
Electric control valves demonstrate superior precision in positioning and control compared to their pneumatic counterparts. The electric actuator's ability to provide exact positioning through servo motor technology enables positioning accuracy typically within ±0.1% of full scale, while pneumatic systems generally achieve ±0.25% to ±0.5% accuracy. This enhanced precision stems from the electric control valve's direct digital feedback systems and the absence of compressibility issues inherent in pneumatic systems. The electric actuator responds immediately to control signals without the delays associated with air compression and transmission through pneumatic lines.The response time characteristics also favor electric control valves in many applications. Electric actuators can achieve full stroke times as fast as 10-30 seconds depending on valve size and torque requirements, while pneumatic systems typically require 15-60 seconds for similar operations. This faster response capability becomes particularly valuable in processes requiring rapid adjustments to maintain optimal conditions. Additionally, electric control valves maintain consistent performance across varying ambient temperatures, whereas pneumatic systems can experience performance variations due to air density changes and moisture content in compressed air systems.
Power Requirements and Energy Efficiency
Electric control valves operate on standard electrical power supplies, eliminating the need for compressed air infrastructure and its associated energy consumption. Compressed air systems typically consume 7-8 times more energy than the equivalent electric motor power output, making electric control valves more energy-efficient for continuous operation. The electric actuator only consumes power during valve movement and positioning, whereas pneumatic systems require continuous air pressure maintenance even during static positions.However, pneumatic control valves offer advantages in environments where electrical power may be unreliable or where intrinsic safety requirements make electric systems challenging to implement. The pneumatic system's ability to fail-safe through spring return mechanisms provides inherent safety benefits in many process applications. Electric control valves can incorporate battery backup systems and fail-safe mechanisms, but these add complexity and cost to the overall system design.
Maintenance and Operational Considerations
Electric control valves typically require less routine maintenance compared to pneumatic systems. The absence of compressed air components eliminates concerns about air quality, moisture removal, and filter maintenance. Electric actuators have fewer moving parts and sealed designs that protect internal components from environmental contamination. Predictive maintenance capabilities are enhanced in electric systems through current signature analysis and position feedback monitoring, allowing operators to identify potential issues before failure occurs.Pneumatic control valves require regular maintenance of air preparation equipment, including filters, regulators, and lubricators. Air quality issues such as contamination, moisture, and oil carryover can significantly impact pneumatic actuator performance and longevity. However, pneumatic systems are generally more tolerant of harsh environmental conditions and can operate effectively in explosive atmospheres without special electrical certification requirements.
Application-Specific Selection Criteria
Process Control Requirements
The selection between electric control valves and pneumatic systems depends heavily on specific process control requirements. Electric control valves excel in applications requiring precise flow control, such as chemical dosing systems, food processing, and pharmaceutical manufacturing where exact proportioning is critical. The ability to achieve precise positioning and maintain stable control under varying process conditions makes electric actuators ideal for these demanding applications.Pneumatic control valves remain preferred in many traditional industrial applications where rapid response and high force output are required. The pneumatic actuator's ability to generate substantial thrust for large valve operations makes it suitable for applications involving high-pressure differentials or large valve sizes. Industries such as oil and gas, power generation, and heavy chemical processing often favor pneumatic systems for their robust performance and proven reliability in harsh operating environments.
Integration with Control Systems
Modern industrial automation systems increasingly favor electric control valves due to their superior integration capabilities with digital control systems. Electric actuators can communicate directly with distributed control systems (DCS) and programmable logic controllers (PLCs) through various communication protocols including Modbus, Foundation Fieldbus, and HART. This direct digital communication enables advanced features such as valve diagnostics, position feedback, and predictive maintenance capabilities.The integration advantages of electric control valves extend to remote monitoring and operation capabilities. Electric actuators can transmit real-time position data, torque information, and diagnostic status to central control systems, enabling operators to monitor valve performance from remote locations. This capability becomes particularly valuable in applications where valve accessibility is limited or where centralized monitoring improves operational efficiency.
Environmental and Safety Considerations
Electric control valves offer advantages in applications where compressed air systems may introduce contamination risks or where air consumption represents a significant operational cost. In clean room environments, food processing, and pharmaceutical applications, electric actuators eliminate the risk of air-borne contamination and provide cleaner operation. The absence of exhaust air from pneumatic systems also reduces noise levels and environmental impact.Safety considerations often favor pneumatic systems in explosive atmospheres or where fire risk is a concern. Pneumatic actuators can achieve intrinsic safety ratings more easily than electric systems, making them suitable for hazardous area applications. However, modern electric control valves with appropriate explosion-proof certifications can operate safely in hazardous environments, though at higher initial costs and complexity.
Cost Analysis and Return on Investment
Initial Investment Considerations
The initial cost comparison between electric control valves and pneumatic systems depends on several factors including valve size, application requirements, and existing infrastructure. Electric control valves typically have higher upfront costs due to the complexity of electric actuators and associated control electronics. However, this initial investment must be evaluated against the total cost of ownership including installation, operation, and maintenance expenses.Pneumatic control valves generally have lower initial hardware costs, but the total system cost must include compressed air infrastructure, air preparation equipment, and distribution piping. For new installations, the cost of installing compressed air systems can be substantial, particularly for applications requiring only a few control valves. The infrastructure costs for electric systems are typically lower, requiring only electrical power distribution and control wiring.
Operating Cost Comparison
Long-term operating costs often favor electric control valves due to their energy efficiency and reduced maintenance requirements. The elimination of compressed air consumption results in significant energy savings, particularly in applications where valves operate frequently or maintain positions for extended periods. Electric actuators consume power only during movement, while pneumatic systems require continuous air pressure maintenance.Maintenance costs for electric control valves are generally lower due to fewer consumable components and longer service intervals. The absence of air filtration systems, regulators, and lubricators reduces routine maintenance requirements. However, when electric actuators do require service, the costs may be higher due to the specialized nature of electronic components and the need for skilled technicians.
Lifecycle Value Assessment
The total lifecycle value of electric control valves often exceeds that of pneumatic systems in applications where precision, reliability, and integration capabilities are valued. The enhanced diagnostic capabilities of electric systems enable predictive maintenance strategies that can prevent costly process disruptions. The ability to monitor valve performance and identify potential issues before failure occurs provides significant value in critical process applications.Electric control valves also offer superior flexibility for future system upgrades and modifications. The digital communication capabilities allow for enhanced control strategies and integration with advanced process control systems without hardware modifications. This adaptability provides long-term value as industrial automation systems continue to evolve toward more sophisticated control and monitoring capabilities.
Conclusion
The choice between electric control valves and pneumatic systems ultimately depends on your specific application requirements, existing infrastructure, and long-term operational objectives. Electric control valves offer superior precision, energy efficiency, and integration capabilities, making them ideal for applications requiring exact control and digital system integration. Pneumatic systems remain valuable for applications requiring high force output, intrinsic safety, and operation in harsh environments. As industrial automation continues advancing toward digitalization and Industry 4.0 implementations, electric control valves are becoming increasingly attractive for their enhanced monitoring and diagnostic capabilities.
At CEPAI Group, we understand that selecting the right control valve technology is crucial for your process success. Our comprehensive range of electric control valves combines exceptional durability with high-precision control performance, backed by extensive R&D investments and industry-leading certifications including ISO 9001, ISO 14001, and API standards. Whether you need pre-sales technical consultation, customized solutions, or comprehensive after-sales support, our team of experts is ready to help you optimize your process control systems. Experience the difference that quality engineering and innovative technology can make in your operations. Contact us today at cepai@cepai.com to discuss how our electric control valve solutions can enhance your process efficiency and reliability.
References
1. Anderson, J.K., Mitchell, P.R., and Thompson, S.L. (2023). "Comparative Analysis of Electric and Pneumatic Actuator Performance in Industrial Control Applications." Journal of Process Control Engineering, 45(3), 234-251.
2. Rodriguez, M.A., Chen, W., and Kumar, S. (2022). "Energy Efficiency Assessment of Electric vs Pneumatic Control Valve Systems in Chemical Processing." Industrial Automation and Control Systems Review, 38(7), 412-428.
3. Williams, R.J., Patterson, K.M., and Lee, H.Y. (2023). "Maintenance Cost Comparison and Lifecycle Analysis of Electric and Pneumatic Control Valves." Plant Engineering and Maintenance Quarterly, 29(2), 156-173.
4. Brown, D.C., Smith, A.J., and Johnson, T.R. (2022). "Integration of Smart Electric Control Valves in Modern Industrial Automation Systems." Control Systems Technology Journal, 41(8), 324-340.
_1745994790767.webp)
Get professional pre-sales technical consultation and valve selection services, customized solution services.
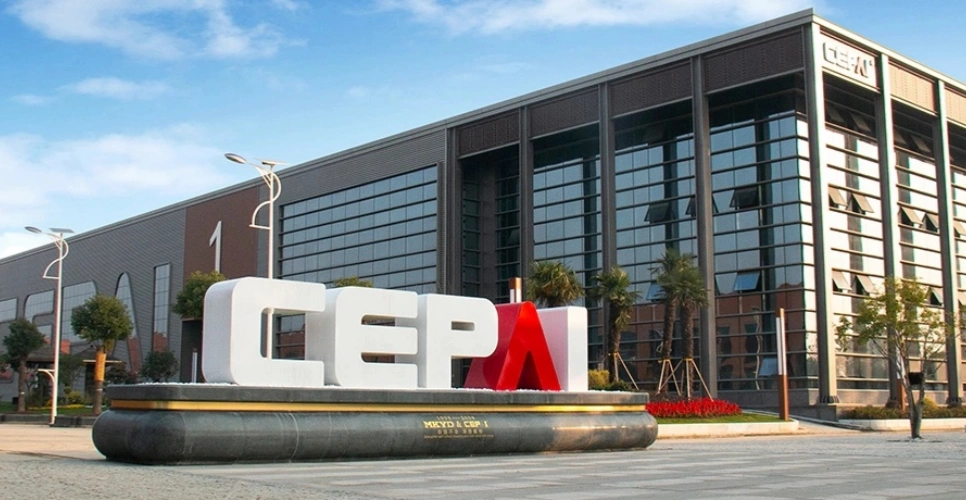
About CEPAI